
книги / Химия и технология полимерных материалов. Технология полимерных материалов
.pdf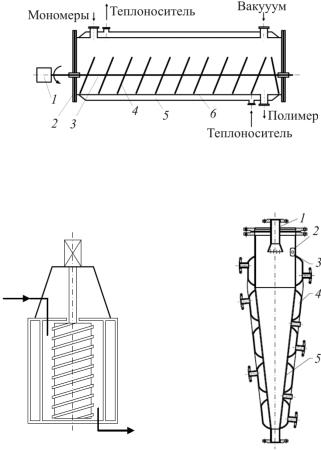
Рис. 1.3. Горизонтальный реактор для синтеза полиэтилентерефталата: 1 – привод мешалки; 2 – крышка; 3 – вал мешалки; 4 – диски;
5 – рубашка; 6 – корпус реактора
а |
б |
Рис. 1.4. Реакторы пленочного типа: а – цилиндр в цилиндре; б – центробежный: 1 – штуцер; 2 – цилиндрическая часть; 3 – сопло; 4 – рубашка; 5 – коническая часть
В реакциях поликонденсации могут применяться пленочные центробежные реакторы (рис. 1.4, б). Центробежный пленочный реактор состоит из двух частей: верхней цилиндрической 2 и нижней конической 5. Снаружи реактор оборудован многосекционной рубашкой 4 для обогрева. Для ввода реагентов реактор
11
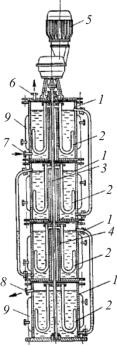
снабжен двухкамерным соплом 3, установленным по касательной к корпусу реактора и штуцером. Таким образом создается высокоразвитая поверхность контакта фаз, когда струя из спирально сужающегося конуса сопла разбивает поток, движущийся по центральному каналу. Диспергированная смесь в виде тонкой пленки движется по спирали вдоль нагретой поверхности конусной части реактора. За счет интенсивного массообмена процесс поликонденсации может протекать в течение нескольких секунд. Образующиеся пары НМП отводятся из реактора через штуцер 1.
|
Полученный полимер через ниж- |
||
|
ний штуцер поступает на даль- |
||
|
нейшую переработку. |
||
|
Колонные аппараты. Ко- |
||
|
лонна |
состоит из |
нескольких |
|
секций, |
расположенных одна |
|
|
над другой (рис. 1.5). Все сек- |
||
|
ции снабжены мешалками с об- |
||
|
щим валом. Вал проходит из |
||
|
одной секции в другую через |
||
|
патрубки, верхние края которых |
||
|
расположены выше уровня ре- |
||
|
акционной смеси. Ввод реаген- |
||
|
тов осуществляется в загрузоч- |
||
|
ный штуцер сверху аппарата, |
||
|
выход готового продукта – че- |
||
|
рез штуцер, расположенный в |
||
|
нижней части колонны. Каждая |
||
|
секция снабжена рубашкой, па- |
||
|
ровые пространства секций со- |
||
Рис. 1.5. Многосекционный аппарат |
общаются между собой. |
||
синтезановолачныхсмол: 1 – секция; |
Процесс поликонденсации |
||
2 – мешалка; 3 – вал мешалки; |
протекает ступенчато, состав ре- |
||
4 – патрубок; 5 – электродвигатель; |
акционной смеси |
меняется от |
|
6–8 – штуцеры; 9 – рубашка |
секции к секции. |
|
|
|
|
12
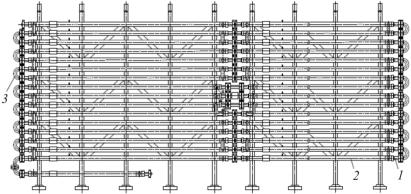
Трубчатые реакторы. В производстве полиэтилена высокого давления (ПЭВД) помимо автоклавного оборудования применяются трубчатые аппараты типа труба в трубе (рис. 1.6). Такой реактор является типичным примером реактора идеального вытеснения. Трубы полимеризатора имеют небольшой диаметр и малую толщину стенок, что в целом позволяет организовать эффективный теплообменный процесс.
Рис. 1.6. Трубчатый реактор получения ПЭВД: 1 – трубчатка; 2 – рубашка; 3 – калач
Шнековые реакторы. Такие аппараты состоят из обогреваемого корпуса, в котором установлены два шнека, вращение которых обеспечивает перемешивание реакционной массы и ее движение вдоль реактора (рис. 1.7).
Реактор работает под глубоким вакуумом для более полного удаления НМП из зоны реакции. Время пребывания реакционной массы в реакторе составляет от 1 до 2,5 ч при средней частоте вращения шнеков 0,15–0,2 с, что позволяет поддерживать производительность реактора на уровне до 400 кг/ч.
Хранение сырья. Жидкие материалы обычно хранят в цилиндрических сосудах вертикальных или горизонтальных объемом до 2000 м3. Низкокипящие жидкости и сжиженные газы хранят в
13

сферических сосудах, выдерживающих давление до 1 МПа. Газообразные реагенты хранят в газгольдерах низкого или высокого (15–16 МПа) давления.
Рис. 1.7. Схема горизонтального двухшнекового реактора:
1 – корпус; 2 – штуцер отвода НМП; 3 – шнеки; 4 – горизонтальный загрузочный шнек; 5 – разгрузочный штуцер
Транспортировку реагентов осуществляют по трубопроводам. Для перекачки жидких продуктов используют насосы, для газообразных – турбокомпрессоры и турбогазодувки.
Подготовка мономеров и вспомогательных веществ. При про-
изводстве полимерных материалов сырьем могут являться твердые, жидкие и газообразные вещества, которые необходимо подготовить и правильно дозировать в промышленном процессе. Например, в условиях Сибири и Крайнего Севера преобладают низкие температуры воздуха, поэтому часто требуется предусматривать подогрев железнодорожных цистерн перед разгрузкой и емкостей для прицеховых складов наоткрытых площадках.
При приеме газообразных мономеров необходимо удалять из них сконденсированные фазы путем фильтрования, осушки или увлажнения (для безопасной работы к ацетилену добавляют водяной пар).
В процессе хранения и транспортировки мономеров к ним могут добавлять ингибиторы для предотвращения преждевре-
14
менной полимеризации. В этом случае перед началом производственного процесса требуется очистка мономеров от ингибиторов и стабилизаторов, а также удаление примесей, которые могут негативно повлиять на процесс получения полимеров.
Технологические схемы производства полимерных материалов делят на два типа: с открытой цепью и циклические.
Через схему с открытой цепью все реагенты проходят один раз. В случае низкой степени превращения в одном аппарате в схему последовательно встраивают несколько однотипных реакторов.
Циклическая схема предусматривает многократное возвращение исходного мономера в реактор. Такие схемы применяются в производстве полиэтилена, где степень превращения мономера невысока (12–15 %).
15
2. ПЕРЕРАБОТКА ПОЛИМЕРОВ
Полимеры в чистом виде, полученные после их выделения и очистки, называются первичными полимерами или первичными смолами.
За редким исключением (полиэтилен, полипропилен, полистирол, полиметилметакрилат), первичные полимеры обычно непригодны для прямой переработки в изделия. Большинство полимеров требуют размягчения с помощью пластификаторов. Каучуки необходимо вулканизировать. Почти все полимеры защищают от термической, окислительной и фотодеструкции введением соответствующих стабилизаторов. Для придания изделиям привлекательного товарного вида широко используются красители и пигменты. Часто для облегчения переработки к полимерам добавляют смазки и антиадгезивы. Иногда в полимеры вводят и другие вещества, обеспечивающие им специальные свойства. Это вспениватели, пламегасители, армирующие наполнители и т.д.
Процесс введения в первичные полимеры всех этих ингредиентов называют компаундированием, а получаемую композицию – компаундом.
Компаундирование различных групп полимеров проводят по-разному.
Пластические полимеры (полистирол, поливинилхлорид, полиметилметакрилат, полиэтилен) обычно поступают на переработку в виде сыпучих порошков или гранул. Необходимые для компаундирования добавки в виде порошков смешивают с первичными полимерами в различных миксерах или смесителях. Если имеются жидкие ингредиенты компаунда, то смешение удобнее проводить с помощью обычных высокоскоростных мешалок. Смешение проводится при комнатной или повышенной температуре, но гораздо ниже температуры размягчения полимера.
Типичным примером изготовления полимерного компаунда является процесс производства поливинилхлоридного пластиката. Поливинилхлоридный пластикат получают компаундированием
16
первичного поливинилхлорида с пластификаторами, стабилизаторами, смазывающими веществами, пигментами и наполнителями.
В качестве пластификаторов чаще всего применяют сложные эфиры фталевой и себациновой кислот. Несколько реже, ввиду высокой токсичности, используют трикрезилфосфаты. Пластифицирующим действием обладают и хлорированные высшие парафины. Кроме того, они придают материалу негорючесть. Иногда поливинилхлорид пластифицируют добавкой эластомеров. Например, бутадиен-нитрильный каучук имеет перед низкомолекулярными пластификаторами то преимущество, что он хорошо совмещается с поливинилхлоридом и не выпотевает со временем.
Стабилизаторы защищают пластикат от термодеструкции. Обычно стабилизаторами являются соединения свинца основного характера: силикат, стеарат, карбонат свинца, которые хорошо поглощают хлористый водород, образующийся в процессе термодеструкции. Содержание стабилизаторов в пластикате колеблется от 3 до 18 %.
Смазывающие вещества облегчают переработку поливинилхлорида вальцеванием, каландрованием или экструзией. В качестве смазки применяют стеариновую кислоту или стеараты кальция и свинца в количестве 1–3 % от массы полимера.
Пигменты улучшают внешний вид изделия и экранируют его от деструктивного воздействия ультрафиолетовых лучей. Часто в поливинилхлоридный пластикат с этой целью вводят 1–2 % сажи.
Наполнители улучшают механические свойства компаунда и снижают стоимость готовых изделий. Широко распространенные наполнители – каолин, аэросил, диоксид титана. Чем выше содержание наполнителей в компаунде, тем он дешевле, но слишком большое количество наполнителей делает пластикат жестким и ломким. Поэтому содержание наполнителей не должно превышать 10 %.
Изготовление пластиката начинают введением в поливинилхлорид стабилизаторов, чтобы избежать деструкции материала даже на начальных этапах его переработки. Затем в полимер вво-
17
дят пластификаторы, постепенно повышая температуру в смесителе от 80–90 до 110–130 °С. Стабилизированный и пластифицированный полимер из смесителя направляют на вальцы, где в процессе вальцевания в него вводят остальные компоненты, повышая температуру к концу процесса до 155–180 °С.
Первичные эластомеры, такие как каучуки, получают обычно в виде крошки или латекса. К крошке добавляют вулканизаторы, ускорители вулканизации, наполнители, смазывающие вещества и прессуют в толстые пластины, называемые кипами. Кипы являются обычнойформойхранения, транспортировкии продажи каучука.
На переработку каучуки также поступают в виде кип. Поскольку эластомеры – не сыпучие материалы, просто перемешать их с компонентами компаунда невозможно. Поэтому компаундирование проводят на двухвалковой каучуковой мельнице. Содержание каучука в готовом компаунде составляет от 33 до 50 %. Часто это смесь натурального и синтетического каучука в соотношении 1:1. До 65 % компаунда приходится на наполнители. В качестве наполнителей применяют мел, тальк, каолин, сажу.
Эластомеры в виде латекса компаундируют простым перемешиванием всех компонентов с помощью высокоскоростных мешалок.
В случае волокнообразующих полимеров компаундирование не проводят. Все необходимые добавки к полимеру напрямую вводят в полимерный расплав или раствор непосредственно перед прядением нити.
Особое место среди композиций на основе полимерных материалов и изделий из них занимают так называемые полимерные композиционные материалы (ПКМ). В полимерных композиционных материалах полимер выступает в качестве связующего, а другим компонентом является армирующий наполнитель в виде волокон, нитей, лент, жгутов или полотнищ тканей.
При производстве полимерных композиционных материалов в качестве наполнителей широко применяют стекловолокно, стеклянный шпон, стеклоткани, углеродные волокна и углеткани, борные
18
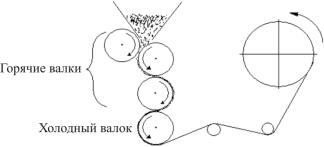
волокна. Однако армирующие наполнители ПКМ могут быть также органическими полимерами. Например, гетинаксы представляют собой листы бумаги, пропитанные полимерным связующим и отвержденныеподдавлением при высокой температуре.
В основе технологии переработки полимеров в изделия лежат процессы, заимствованные из технологии металлообработки и стекольной промышленности. Большинство полимерных изделий получены либо формованием, либо механической обработкой, либо отливкой жидких композиций в формы с последующим отверждением или сшиванием.
Прежде чем рассматривать отдельные приемы и методы изготовления полимерных изделий, вспомним, что полимеры делятся на термопласты и реактопласты. Термопласты, сформованные в изделия при повышенной температуре, необходимо охладить, иначе они потеряют форму. Для реактопластов такой необходимости нет, поскольку после отверждения или сшивки они сохраняют свою форму в любых условиях.
Каучуки, сополимеры бутадиена со стиролом и акрилонитрилом, полиэтилен и поливинилхлорид применяют для производства пленок и листовых материалов методом каландрования (рис. 2.1).
Рис. 2.1. Схема каландра
Каландр представляет собой систему стальных валков с постепенно уменьшающимися зазорами между ними. Верхние вал-
19
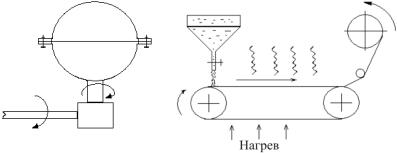
ки каландра обогреваются. Нижние, последние в системе валки остаются холодными.
Полимер в виде крошки или гранул из бункера попадает на горячие валки, размягчается и раскатывается ими в непрерывную ленту. Прокатанная до требуемой толщины лента охлаждается, проходя между холодными валками, и сматывается в рулон.
Полые изделия из термопластов получают методом ротационного литья. На рис. 2.2 представлена схема изготовления методом ротационного литья резиновых мячей.
Термопласт в виде порошка помещают в разъемную форму, которая нагревается и одновременно вращается в двух плоскостях. Полимер внутри формы плавится и равномерно растекается по всей ее внутренней поверхности. После охлаждения форму останавливают, раскрывают и извлекают из нее готовое изделие. Таким же методом производят резиновую обувь, игрушки и т.п.
В методе отливки пленок (рис. 2.3) раствор полимера в легколетучем растворителе непрерывным потоком выливают на движущийся нагретый стальной пояс.
Рис. 2.2. Ротационное литье |
Рис. 2.3. Отливка пленок |
Растворитель при этом испаряется, а на гладкой полированной поверхности металла остается тонкая прозрачная полимерная пленка, которую охлаждают и сматывают в рулон. Таким методом получают пленку из целлофана, а также фото- и кинопленку.
20