
вариант 7 МТКМ
.pdfМИНИСТЕРСТВО ТРАНСПОРТА РОССИЙСКОЙ ФЕДЕРАЦИИ ФЕДЕРАЛЬНОЕ АГЕНТСТВО ЖЕЛЕЗНОДОРОЖНОГО ТРАНСПОРТА ФЕДЕРАЛЬНОЕ ГОСУДАРСТВЕННОЕ БЮДЖЕТНОЕ ОБРАЗОВАТЕЛЬНОЕ УЧРЕЖДЕНИЕ ВЫСШЕГО ОБРАЗОВАНИЯ
САМАРСКИЙ ГОСУДАРСТВЕННЫЙ УНИВЕРСИТЕТ ПУТЕЙ СООБЩЕНИЯ
Кафедра «Наземные транспортно-технологические средства»
Расчетно-графическая работа №1
По дисциплине «Материаловедения. Технология конструкционных материалов», раздел «Материаловедение»
Вариант №7
Выполнил: ст. гр. ПС-74
Ведышев Роман Александрович
Проверил :к.т.н., доцент
Самохвалова Ж.В.
Самара 2018
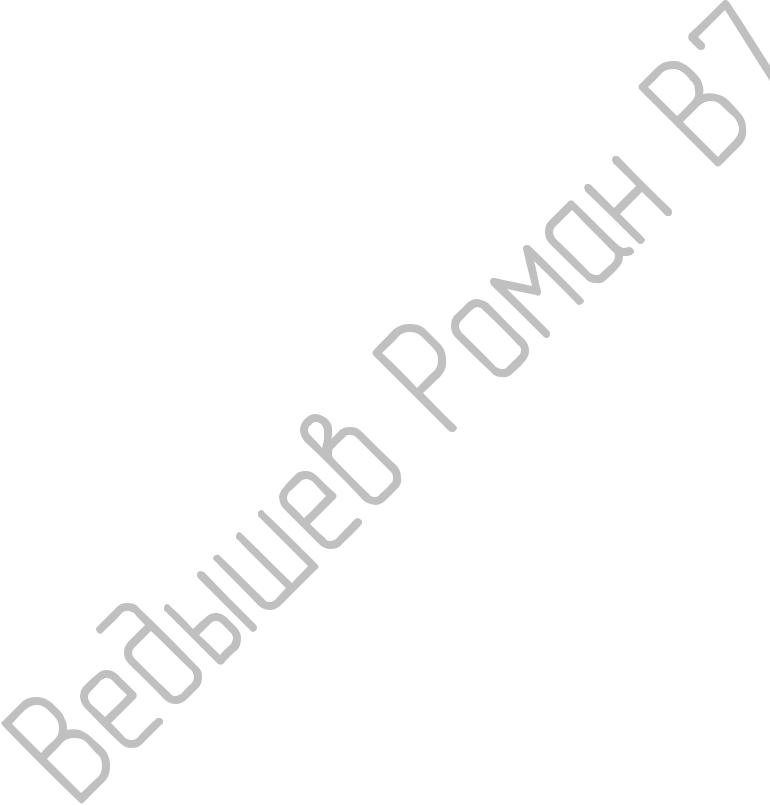
|
СОДЕРЖАНИЕ |
ВВЕДЕНИЕ ..................................................................................................................................................... |
3 |
Задание№1...................................................................................................................................................... |
4 |
Задание№2...................................................................................................................................................... |
8 |
Задание№3.................................................................................................................................................... |
11 |
ЗАКЛЮЧЕНИЕ............................................................................................................................................ |
14 |
БИБЛИОГРАФИЧЕСКИЙ СПИСОК..................................................................................................... |
15 |
2
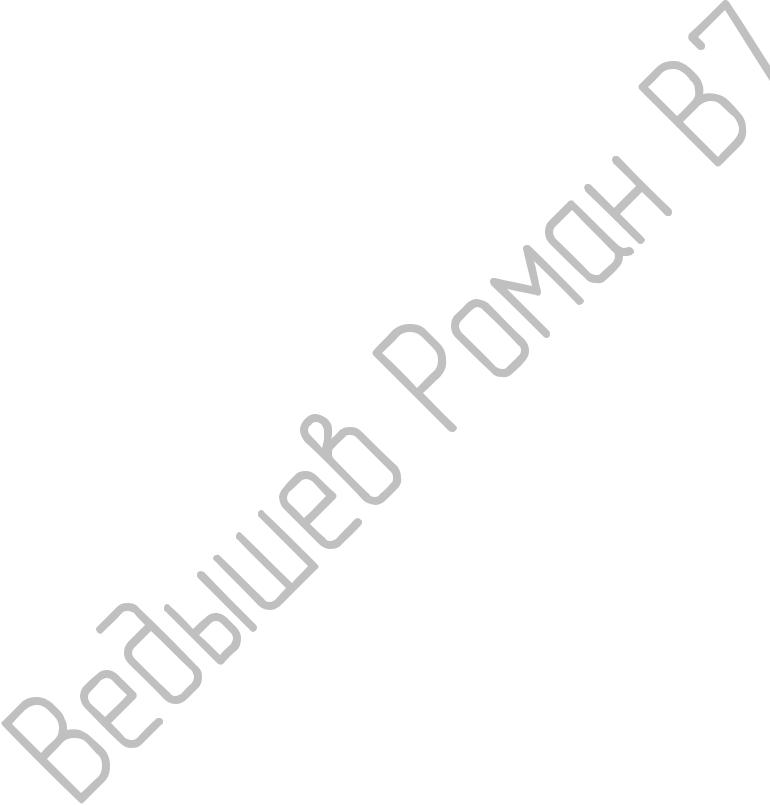
ВВЕДЕНИЕ
Материаловедением называется комплексная наука, изучающая внутреннее строение и свойства материалов и закономерности их изменения под воздействием внешних факторов: тепловых, механических, химических, электромагнитных радиоактивных.
К числу важнейших свойств материалов относятся: механические (прочность, вязкость, твердость и другие); химические (сопротивление воздействию агрессивной среды); физические (электрические, магнитные, тепловые); технологические (жидкотекучесть, штампуемость, свариваемость, обрабатываемость резанием, прокаливаемость и другие). Непрерывный рост уровня техники предъявляет все более высокие требования к эксплуатационным свойствам материалов различного назначения, а также к методам получения и обработки материалов. Современное материаловедение обобщает и использует результаты исследований отечественных и зарубежных ученых на основе физики и химии твердого тела, что позволяет разрабатывать новые конструкционные материалы и эффективные технологии их получения и обработки.
Условия работы современных изделий машиностроения часто требуют увеличения эксплуатационных характеристик материалов, что во многом определяется крупными достижениями в теории и практике материаловедения. В настоящее время широкое применение нашли новые высокопрочные металлические материалы различного назначения, композиционные материалы, материалы с особыми свойствами (полупроводники и жидкие кристаллы, сверхпроводники, аморфные сплавы), одновременно совершенствовались способы упрочнения деталей термической и химико-термической обработками.
Работы отечественных ученых А.А. Бонвара, А.А. Байкова, Г.В. Курдюмова В.Д. Садовского, В.А. Каргина внесли огромный вклад в развитие современной науки о материалах.
3
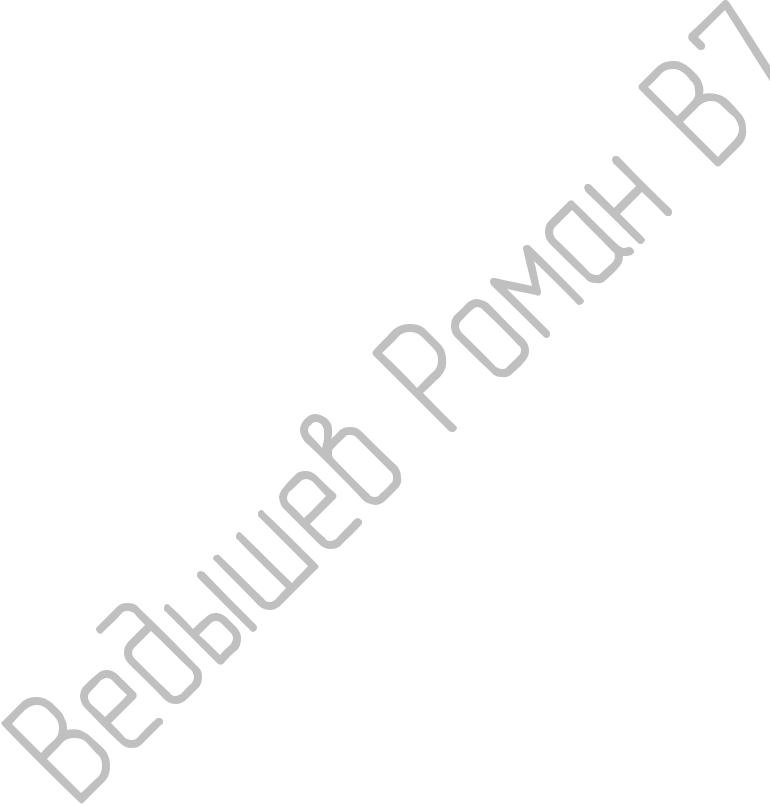
Задание №1
Начертите диаграмму состояний «железо–углерод», укажите структурные составляющие во всех областях диаграммы и дайте им определения. Опишите структурные и фазовые превращения при медленном охлаждении сплава с содержанием углерода С = 5,4 %. Охарактеризуйте этот сплав, определите для него при температуре Т=400 °С (по правилу отрезков) состав фаз и их количество (процентное соотношение). По правилу фаз определите число степени свободы в каждой критической точке сплава и постройте кривую охлаждения сплава.
Решение:
Феррит (Ф) – твердый раствор внедрения углерода в α-железе, магнитен, имеет низкую прочность σв = 250 МПа, σ0,2 = 120 МПа, НВ 80-100, высокую пластичность (δ = 50 %, ψ = 80 %), зернистое строение.
Аустенит (А) – твердый раствор внедрения углерода в γ-железе, немагнитен, НВ 160 при δ = 40…50 %). Микроструктура аустенита имеет зернистое строение.
Аустенит устойчив при высоких температурах. Медленно охлаждаясь, распадается, образуя эвтектоидную смесь феррита с цементитом – перлит. Цементит (Ц) – химическое соединение железа с углеродом Fe3C – магнитен, имеет высокую твердость НВ 800, очень низкую пластичность, сложную кристаллическую решетку.
Перлит (П) – эвтектоидная механическая смесь феррита и цементита, которая образуется при распаде медленно охлаждающегося аустенита. Состоит из пластинок или 12 зерен цементита на ферритной основе. Перлитная структура стали получается при 0,8 % углерода. Механические свойства определяются формой и дисперсностью частиц цементитной фазы: чем мельче смесь, тем выше механические свойства. Пластинчатый перлит имеет НВ 180… 220; σв = 800 МПа, δ = 10 %; зернистый перлит – НВ 160…200; σв = 650 МПа, δ = 20 %.
4
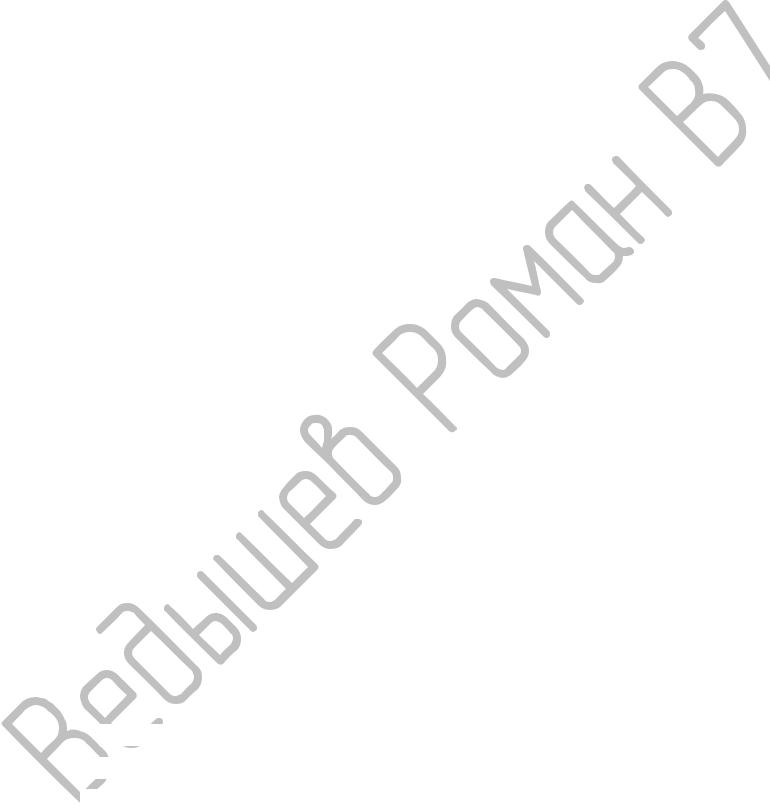
Ледебурит (Л) – механическая смесь (эвтектика) аустенита и цементита (цементита и перлита). Ледебурит – твердая и хрупкая составляющая, НВ
600…700.
В сплаве с содержанием углерода 5,6 % в соответствии с диаграммой «железо–цементит» (рис. 1) имеются 4 точки, характеризующие фазовые превращения при понижении температуры.
Выше точки 1 сплав находится в жидком состоянии, сплав однофазный. Структура: жидкий раствор. Точка 1 находится на линии ACD – ликвидус, следовательно, в этой точке начинается процесс кристаллизации сплава.
На участке 1-2 из жидкого раствора выделяются кристаллы цементита, сплав двухфазный. Структура: жидкий раствор + цементит. Определяем по правилу фаз степень свободы для критической точки. С=К-Ф+2, где С – степень свободы, К – количество компонентов сплава, Ф – количество фаз, находящихся в равновесии данной критической точки, 2 – количество изменяемых параметров. Если С = 0, то процесс происходит с выделением тепла на линии охлаждения наблюдается горизонтальный участок в данной критической точке. Если С не равно 0, то на линии охлаждения наблюдается перегиб в данной критической точке.
С1-2=2+1-2=1 ,следовательно, наблюдается перегиб (т.1-т.2, рис.2).
Точка 2 находится на линии АECF - солидус. В точке 2 заканчивается процесс кристаллизации сплава. Также, она находится на линии ECF – это линия эвтектических превращений, линия ледебуритного превращения. На ней образуется механическая смесь ледебурит Ледебурит = Аустенит + Цементит 1. ( Л(А+Ц1) ). Степень свободы:
С2=2+1-3=0, значит, наблюдается горизонтальный участок т.2-т.2´.
При дальнейшем охлаждении участок 2 - 3 из аустенита выделяется избыточный углерод в виде вторичного цементита. Аустенит при этом обедняется углеродом и при температуре 727°С приобретает состав, соответствующий эвтектоидному. При дальнейшем охлаждении на линии SK,
5
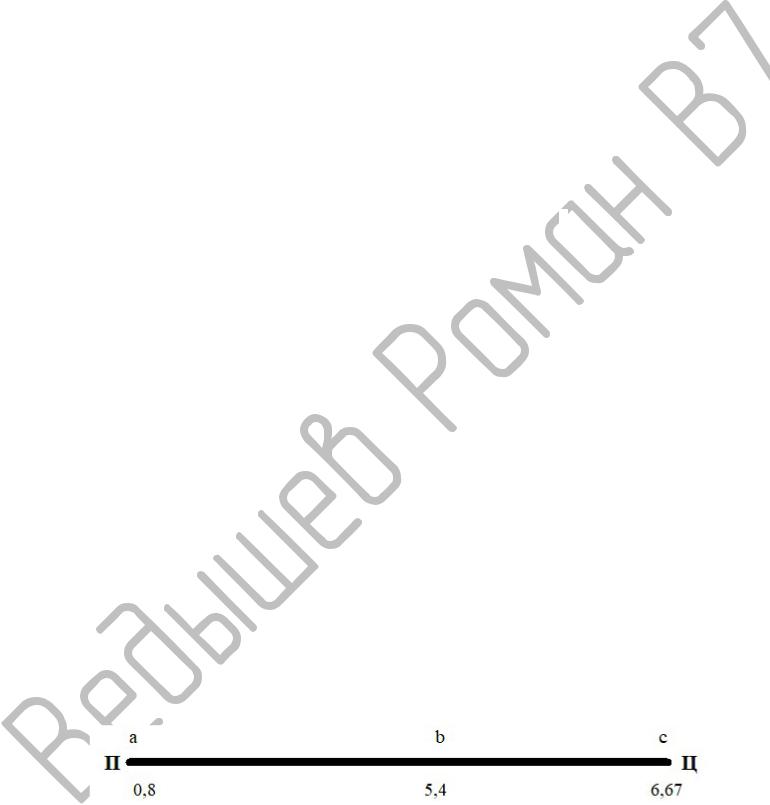
как и в точке S, происходит А→П превращение, поэтому ледебурит ниже температуры 727 ºС является смесью перлита и цементита..
С2´-3=2+1-2=1 ,следовательно, наблюдается перегиб т.2´-т.3.
Точка 3 лежит на линии PSK – это линия эвтектоидных превращений и на ней образуется механическая смесь перлит, состоящий из смеси феррита и цементита вторичного П(Ф+Ц2) . Степень свободы:
С3=2+1-3=0, значит, наблюдается горизонтальный участок т.3-т.3´.
При дальнейшем охлаждении участок 3´ - 4 происходит выделение избыточного углерода из феррита, входящего в перлит и видоизмененный ледебурит. Конечный состав заэвтектического чугуна Л+ЦII.
С3´-4=2+1-2=1, следовательно, наблюдается перегиб т.3´-т.4.
При дальнейшем охлаждении фазовый состав и структура сплавов не меняется до комнтаной температуры.
Так как в заданном сплаве С=5,4 % ,а это больше 2,14%, значит, данный сплав является чугуном. И так как больше 4,3%, значит, чугун заэвтектический.
Применение правила рычага сводится к определению массовой концентрации какой-либо фазы при заданной температуре в двухфазной области диаграммы состояния. Для этого нужно через эту точку провести горизонтальную линию (коноду) до пересечения с линиями, ограничивающими область на диаграмме. Чтобы найти массовую концентрацию фазы, нужно разделить длину отрезка коноды, противолежащего данной фазе, на общую длину коноды.
Используя правило отрезков, определим химический состав и количество фаз для сплава системы «железо–цементит» в точке В (С = 5,4 % при температуре 400 °С) (рис. 3). При температуре 400°С структура Л+Ц, ледебурит состоит из аустенита и перлита , следовательно фазовый состав П+Ц.
Рисунок 3. Состав фаз
П=ВС/АС=((6,67-5,4) / (6,67-0,8))·100%= 21% Ц=100 - 21 =79%
6
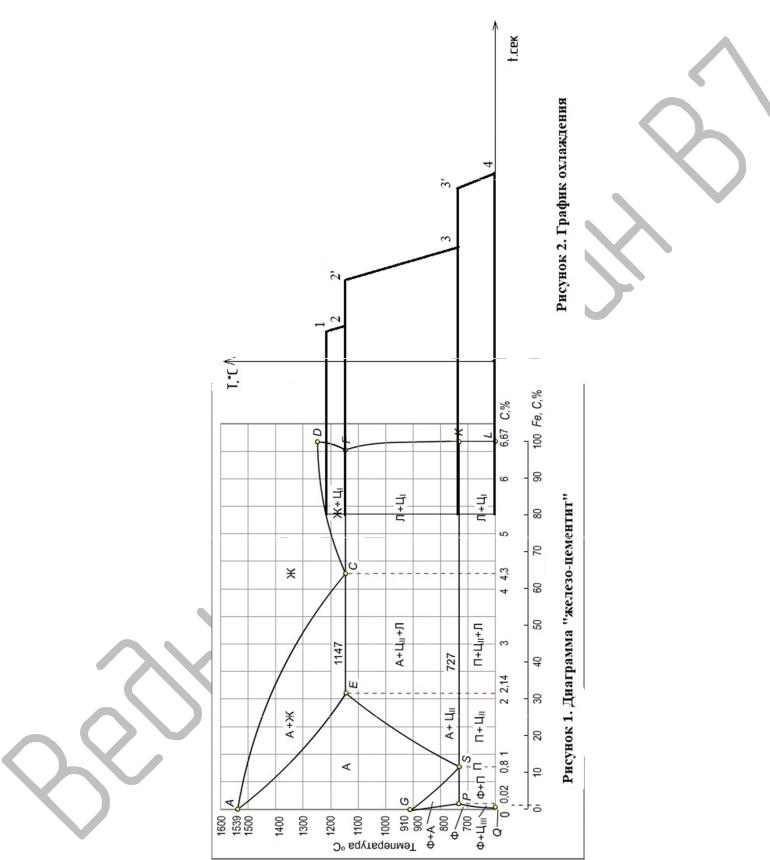
7
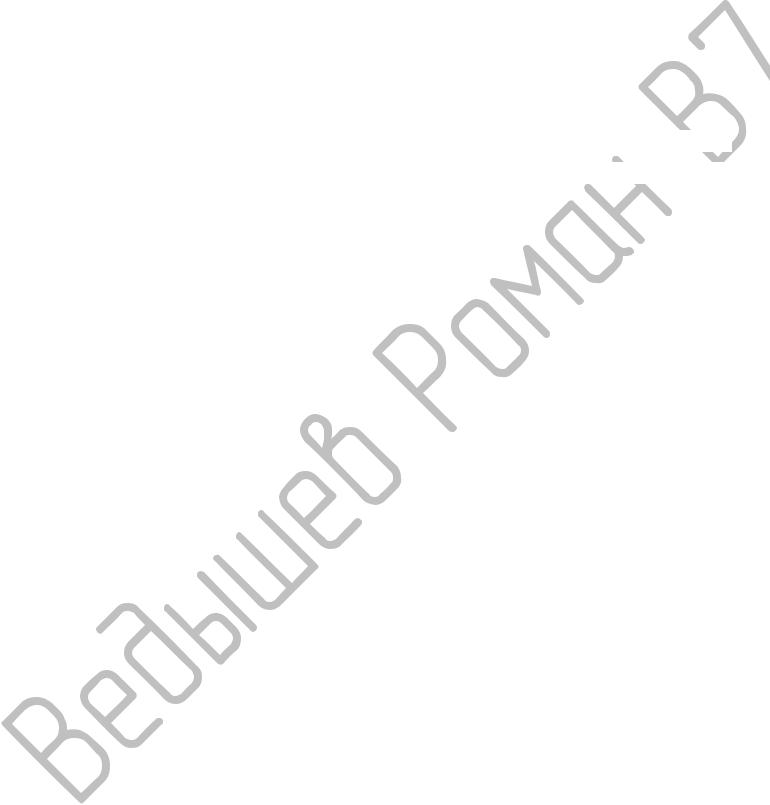
Задание №2
Для изготовления спиральных пружин предлагаются сплавы: 55СГ; Ст.1; ШХ15. Изделия после термической обработки должны обладать конечными свойствами: σупр. = 880…1000 МПа
По марке материала определим назначение и состав сплавов.
1)55СГ - конструкционная рессорно-пружинная сталь, с=0,55%, легированная с содержанием кремния 1%, марганца 1%. Применяют для изготовления рессор и пружин.
2)Ст.1 - сталь конструкционная углеродистая обыкновенного качества, применение: детали высокой вязкости и низкой твердости, анкерные болты, связывающие обшивки, неответственная арматура, заклепки и котельные связи, балки двутавровые, швеллеры, угловая сталь.
3)ШХ15 - Сталь конструкционная подшипниковая,применение: шарики диаметром до 150 мм, ролики диаметром до 23 мм, кольца подшипников с толщиной стенки до 14 мм, втулки плунжеров, плунжеры, нагнетательные клапаны, корпуса распылителей, ролики толкателей и другие детали, от которых требуется высокая твердость, износостойкость и контактная прочность.
Спиральные пружины изготавливают из рессорнопружинных сталей, следовательно для изгоовления деталей возьмем сталь 55СГ.
Основное требование к материалам используемым для изготовления пружин, рессор, и т.д. – сохранение в течение длительного времени упругих свойств.
Высокая упругость рессорно-пружинных сталей достигается лишь в результате их правильной термической обработки. Термическая обработка пружин состоит из нормализации, закалки и отпуска.
Нормализация производится для измельчения зерна стали с целью получения более благоприятной структуры при дальнейшей закалке.
8
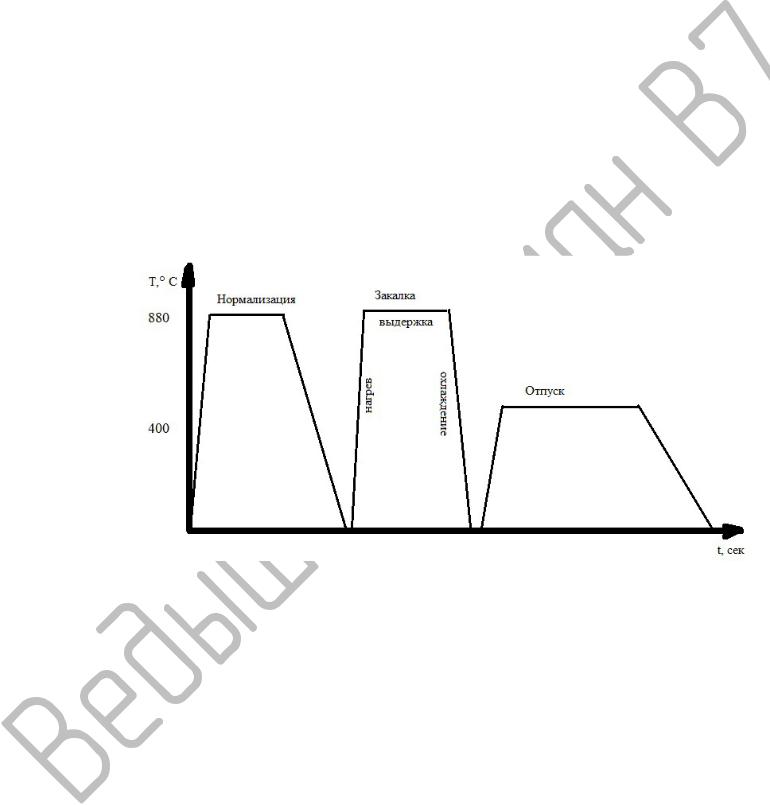
Температура закалки и нормализации: Т= 880°С.
Охлаждение после нормализации производим на воздухе.
Затем производим закалку. Целью закалки является получение неравновесных структур и более высоких механических свойств - твердости, прочности, упругости, износостойкости. Для охлаждения используют масло.
После закалки проводим отпуск. Отпуск пружин производится при температурах 370 - 500°С. Целью отпуска является: получение более устойчивого структурного состояния; устранение или уменьшение напряжений; повышение вязкости и пластичности; понижение твердости и уменьшение хрупкости закаленной стали. Охлаждение производят на воздухе.
Рисунок 4.График термической обработки изделия
При нагреве для нормализации и закалки необходимо следить за тем, чтобы не произошло изменения формы и размеров пружин в процессе нагрева. Под печи, где нагреваются пружины, должен быть ровным и гладким. Если на поду имеются неровности, то во избежание искривления мелкие пружины следует укладывать на противень, а длинные — на ровные корытообразные швеллеры. Пружины укладывают в горизонтальном (лежачем) положении, так как пружина, поставленная на торец, при нагреве осядет под действием собственного веса и изменит форму. Плоские пружины и рессоры ставят на ребро, а для пружин сложной формы применяют различные приспособления.
9
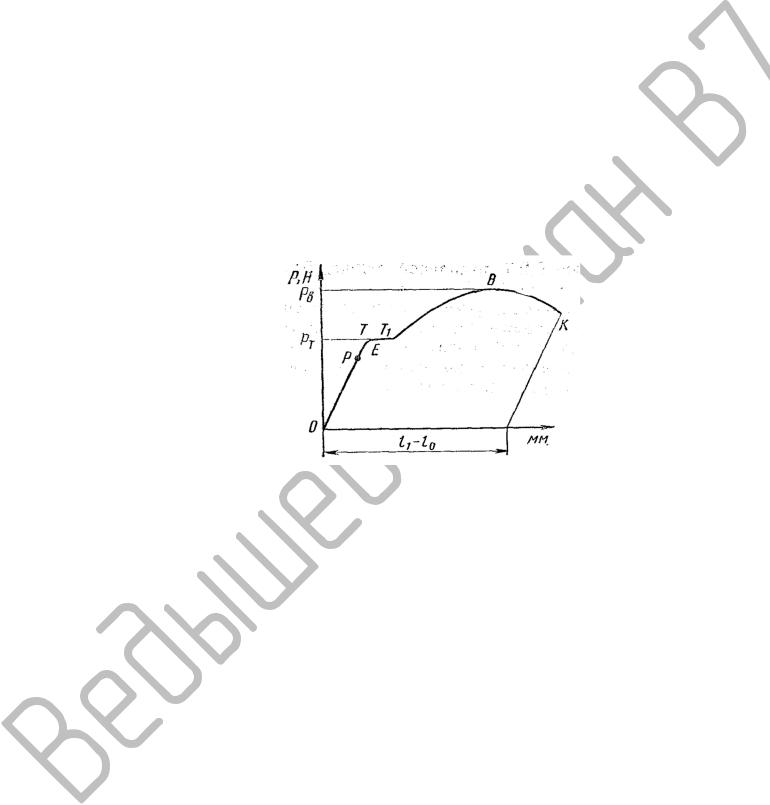
После термической обработки изделие обладает σупр. = 880…1000 Мпа. Под механическими свойствами понимают свойства, обнаруживаемые в
материале при приложении к нему нагрузки. Главными из этих свойств являются прочность, упругость, пластичность, хрупкость, вязкость, твердость.
Прочность, пластичность и упругость определяют испытанием на растяжение металлических стержней. Обычно применяют круглые образцы (прутки) Ø10 и 20 мм. Расчетная длина берется пятикратному или десятикратному диаметру. Испытываемый образец материала с первоначальной площадью F0 постепенно растягивается с возрастающей силой Р, Н. Результаты испытаний изображаются диаграммой растяжения (рис.5).
Рисунок 5. Диаграмма растяжения образца из мягкой стали
Точка Е соответствует пределу упругости σупр, т.е. напряжению при котором появляется первая остаточная деформация.
упр |
Pупр |
|
F |
, |
|
|
0 |
где Рупр – нагрузка, соответствующая пределу упругости, Н; F0 – начальная площадь сечения образца, м2.
10