
вариант 10
.pdfМИНИСТЕРСТВО ТРАНСПОРТА РОССИЙСКОЙ ФЕДЕРАЦИИ ФЕДЕРАЛЬНОЕ АГЕНТСТВО ЖЕЛЕЗНОДОРОЖНОГО ТРАНСПОРТА ФЕДЕРАЛЬНОЕ ГОСУДАРСТВЕННОЕ БЮДЖЕТНОЕ ОБРАЗОВАТЕЛЬНОЕ УЧРЕЖДЕНИЕ ВЫСШЕГО ОБРАЗОВАНИЯ
САМАРСКИЙ ГОСУДАРСТВЕННЫЙ УНИВЕРСИТЕТ ПУТЕЙ СООБЩЕНИЯ
Кафедра «Наземные транспортно-технологические средства»
Расчетно-графическая работа №1
По дисциплине «Материаловедения. Технология конструкционных материалов», раздел «Материаловедение»
Вариант №10
Выполнил: студент группы ПС-74
Авдеева Татьяна Александровна
Проверил :к.т.н., доцент
Самохвалова Жанна Владимировна
Самара 2018
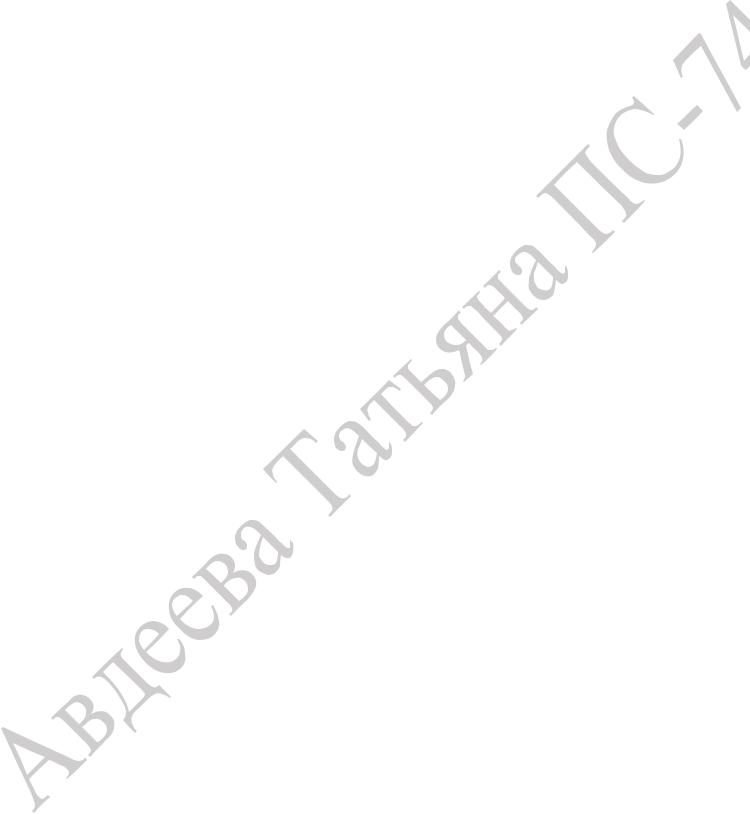
СОДЕРЖАНИЕ
Введение....................................................................................................................... |
3 |
Задание 1..................................................................................................................... |
3 |
Задание 2...................................................................................................................... |
8 |
Задание 3.................................................................................................................... |
10 |
Заключение ................................................................................................................ |
13 |
Библиографический список ..................................................................................... |
14 |
2
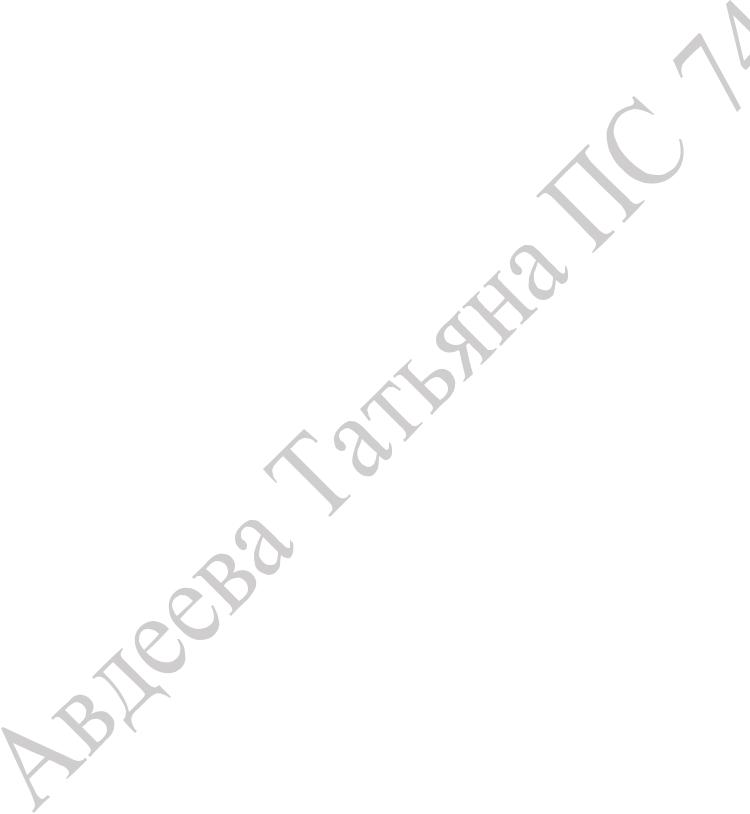
Введение
Материаловедение относится к числу основополагающих дисциплин для технических специальностей. Это связано с тем, что способы обработки материалов являются основой современного производства. Проектирование рациональных, конкурентноспособных изделий, организация их производства невозможны без достаточного уровня знаний в области материаловедения.
Материаловедение является основой для изучения многих специальных дисциплин.
Разнообразие свойств материалов является главным фактором, предопределяющим их широкое применение в технике. Материалы обладают отличающимися друг от друга свойствами, причем каждое зависит от особенностей внутреннего строения материала. В связи с этим материаловедение как наука занимается изучением строения материала в тесной связи с их свойствами. Основные свойства материалов можно подразделить на физические, механические, технологические и эксплуатационные.
От физических и механических свойств зависят технологические и эксплуатационные свойства материалов.
Среди механических свойств прочность занимает особое место, так как прежде всего от нее зависит неразрушаемость изделий под воздействием эксплуатационныхнагрузок.Учение о прочности иразрушении являетсяоднойиз важнейших составных частей материаловедения. Оно является теоретической основой для выбора подходящих конструкционных материалов для деталей различного целевого назначения и поиска рациональных способов формирования в них требуемых прочностных свойств для обеспечения надежности и долговечности изделий.
3

Задание 1.
Начертите диаграмму состояний «железо–углерод», укажите структурные составляющие во всех областях диаграммы и дайте им определения. Опишите структурные и фазовые превращения при медленном охлаждении сплава с содержанием углерода С = 4,8 %. Охарактеризуйте этот сплав, определите для него при температуре Т=300 °С (по правилу отрезков) состав фаз и их количество (процентное соотношение). По правилу фаз определите число степени свободы в каждой критической точке сплава и постройте кривую охлаждения сплава.
Феррит (Ф) – твердый раствор внедрения углерода в α-железе, магнитен, имеет низкую прочность σв = 250 МПа, σ0,2 = 120 МПа, НВ 80…100, высокую пластичность (δ = 50 %, ψ = 80 %), зернистое строение. Аустенит (А) – твердый раствор внедрения углерода в γ-железе, немагнитен, НВ 160 при δ = 40…50 %). Микроструктура аустенита имеет
зернистое строение.
Аустенит устойчив при высоких температурах. Медленно охлаждаясь, распадается, образуя эвтектоидную смесь феррита с цементитом – перлит.
Цементит (Ц) – химическое соединение железа с углеродом Fe3C – магнитен, имеет высокую твердость НВ 800, очень низкую пластичность, сложную кристаллическую решетку.
Перлит (П) – эвтектоидная механическая смесь феррита и цементита, которая образуется при распаде медленно охлаждающегося аустенита. Состоит из пластинок или 12 зерен цементита на ферритной основе. Перлитная структура стали получается при 0,8 % углерода. Механические свойства определяются формой и дисперсностью частиц цементитной фазы: чем мельче смесь, тем выше механические свойства. Пластинчатый перлит имеет НВ 180… 220; σв = 800 МПа, δ = 10 %; зернистый перлит – НВ 160…200; σв = 650 МПа, δ = 20 %.
Ледебурит (Л) – механическая смесь (эвтектика) аустенита и цементита (цементита и перлита). Ледебурит – твердая и хрупкая составляющая, НВ
600…700.
4
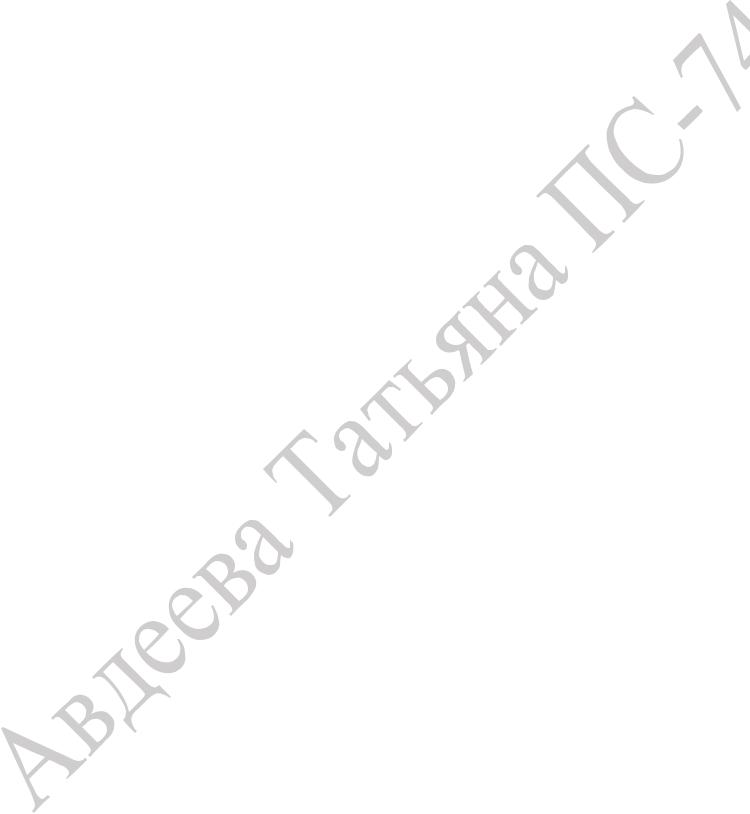
В сплаве с содержанием углерода 4,8 % в соответствии с диаграммой «железо–углерод» (рис. 1) имеются 4 точки, характеризующие фазовые превращения при понижении температуры.
Выше точки 1 сплав находится в жидком состоянии - сплав однофазный. Точка 1 находится на лини ликвидус – ACD, занчит, в этой точке начинается процесс кристаллизации сплава.
На участке 1-2 из жидкого раствора выделяются кристаллы цементита. Сплав двухфазный. Структура: жидкий раствор + цементит 1. Определим по правилу фаз степень свободы для критической точки. С=К-Ф+2, где С – степень свободы, К – количество компонентов сплава, Ф – количество фаз, находящихся в равновесии данной критической точки, 2 – количество изменяемых параметров. Если С не равно 0, то на линии охлаждения наблюдается перегиб в данной критической точке. Если С = 0, то процесс происходит с выделением тепла на линии охлаждения наблюдается горизонтальный участок в данной критической точке. Наданном участке 1-2: С1-2=2+1-2=1– наблюдается перегиб ( участок 1- 2).
Точка 2 находится на линии солидус - AECF. В ней заканчивается процесс кристаллизации сплава. На линии PSK образуется механическая смесь ледебурит : Л(А+Ц1) , вто время как : Ледебурит = Аустенит + Цементит 1. С2=2+1-3=0 – на линии охлаждения наблюдается горизонтальный участок 2-2’.
На участке 2-3 сплав двухфазный и структура: ледебурит + цементит 1. Степень свободы равна С2-3=2+1-2=1 - на линии наблюдается перегиб участок
2’-3.
Точка 3 лежит на линии PSK – это линия эвтектоидных превращений и на ней образуется механическая смесь перлит, состоящий из смеси феррита и цементита вторичного П(Ф+Ц2) . На данном участке степень свободы: С3=2+1- 3=0 – наблюдается горизонтальный участок 3-3’.
На участке 3-4 сплав двухфазный, структура: ледебурит +цементит 1. Степень свободы: С=2+1-2=1. При дальнейшем охлаждении фазовый состав и структура сплавов не меняется до комнатной температуры.
5
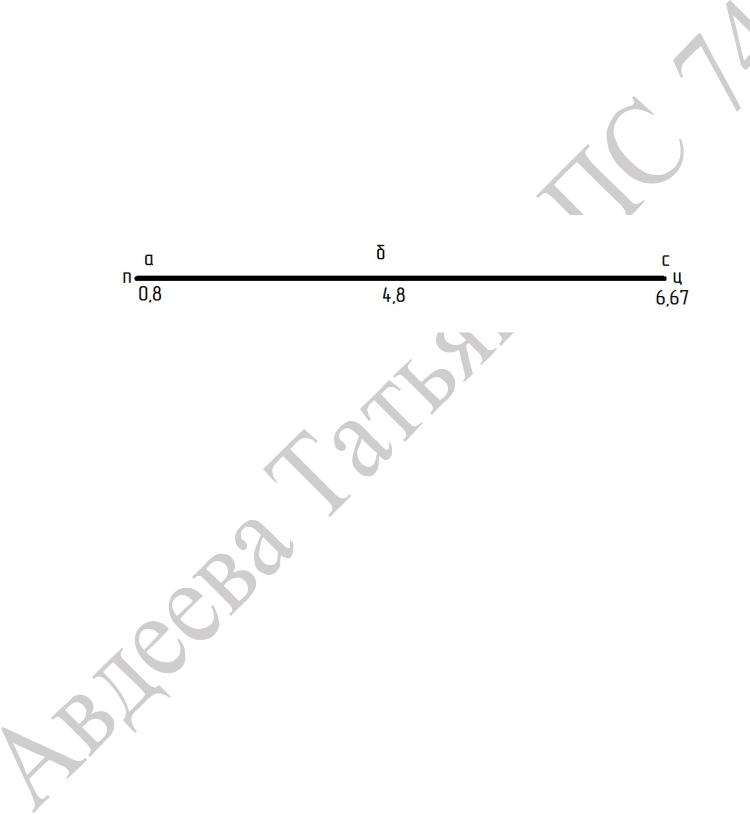
Так как в заданном сплаве С=4,8 % ,а это больше 2,14%, значит, данный сплав является чугуном. И так как больше 4,3%, значит, чугун заэвтектический.
Используя правило отрезков, определим химический состав и количество фаз для сплава системы «железо–углерод» в точке В (С = 4,8 % при температуре 300 °С). Проведем горизонтальную линию через точку б до пересечения с перлитом (точка а) и цементитом (точка с) (рис. 3). В данной точке структура сплава Л+Ц, при температуре 300°С ледебурит является смесью перлита и цементита, следовательно, определим количество фаз перлита и цементита.
Рисунок 3. Состав фаз
Определим процентное содержание фаз:
Перлит: Qп=ВС/АС=((6,67-4,8) / (6,67-0,8))*100%= 31% Цементит: Qц=100 - 21 =69%
6
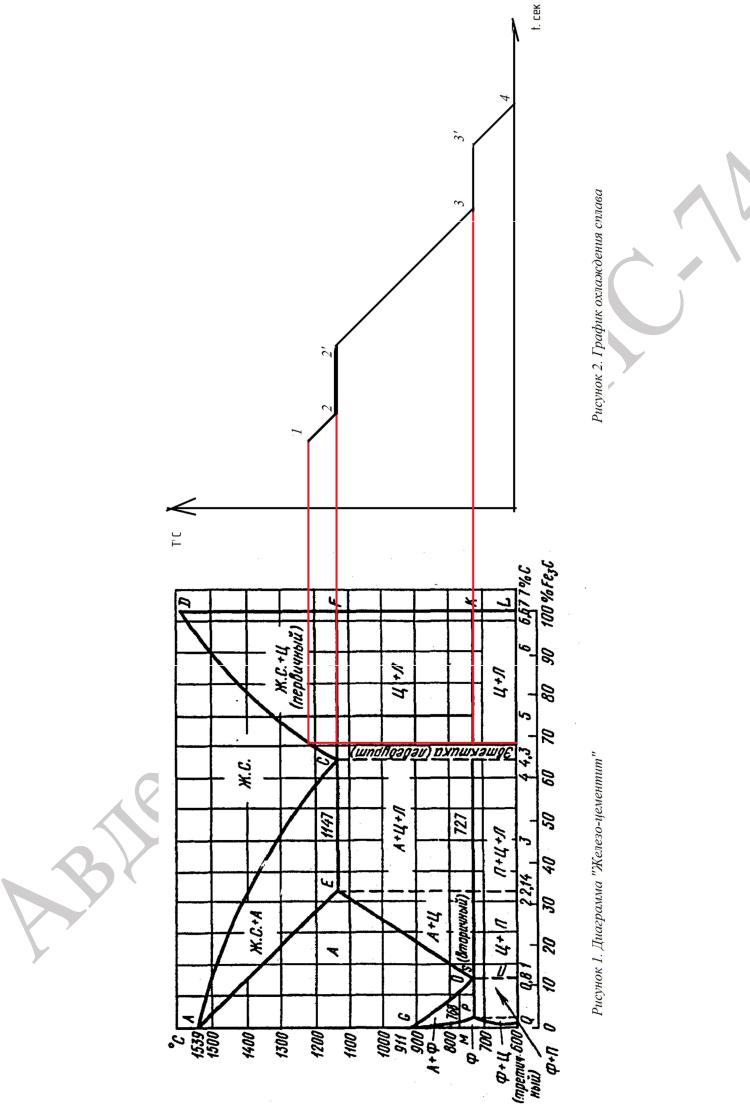
7
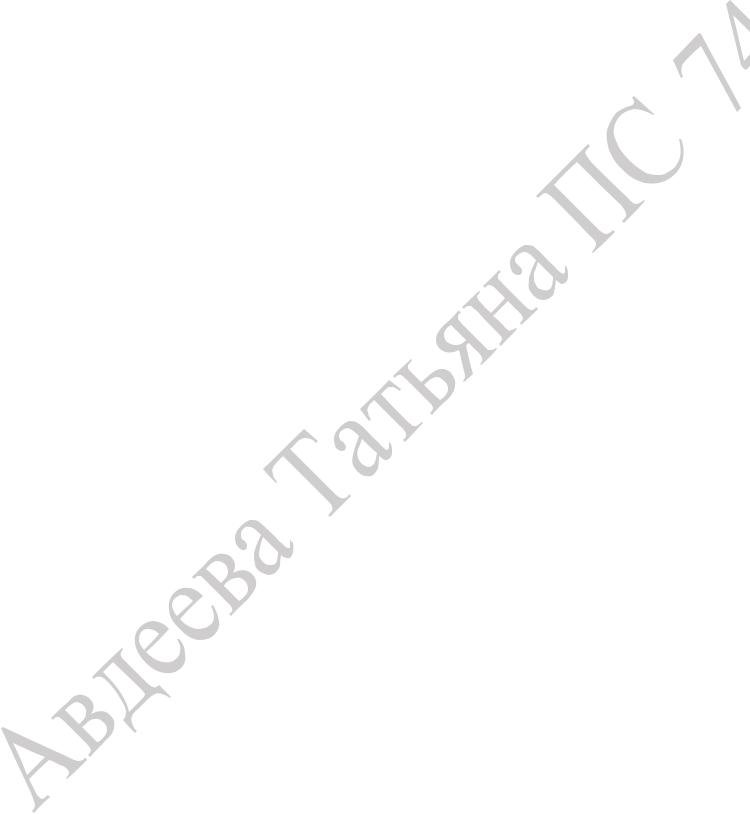
Задание 2.
По своему варианту задания из предложенных марок сплавов У12А; 30ХГС; Р18 выберите марку сплава для указанного изделия (полуоси). Обоснуйте свой выбор. Опишите технологию обработки и структуру для получения повышенной прочности по всему сечению НВ 230…280. Опишите, как определяются эти
свойства.
Дадим определение каждой марке сплавов. У12А – сталь углеродистая, инструментальная, высококачественная, с содержанием углерода 1,2%. Предназначена для изготовления режущих
инструментов, работающих с низкими скоростями резания.
30ХГС – сталь конструкционная, углеродистая, легированная, с содержанием углерода 0,3%, хрома 1%, марганца 1%, кремния 1%. Данную сталь используют для изготовления изделий, которые работают в условиях повышенных динамических нагрузок.
Р18 – сталь с содержанием вольфрама 18%, инструментальная, быстрорежущая. Предназначена для изготовления режущих инструментов, работающих при высоких скоростях.
Полуось - вал ведущего моста, передающий вращение; полуоси во время работы испытывают динамические нагрузки.
Согласно описанию сталей и определению изделия, из представленных сплавов подходит сталь марки 30ХГС.
Для получения повышенной прочности по всему сечению НВ230…280 применим закалку и отпуск.
Закалку данной стали проводим при температуре Т=880°С (согласно марочнику сталей). Целью закалки является увеличение износостойкости, твердости, прочности, упругости. Охлаждение производим в пресной воде.
Так как изделие работает при динамических нагрузках, то применим высокий отпуск. Целью данного отпуска является снижение напряжений, возникших при закалке. Температура отпуска 550-600°С. Охлаждение после данной операции проводят на воздухе.
8
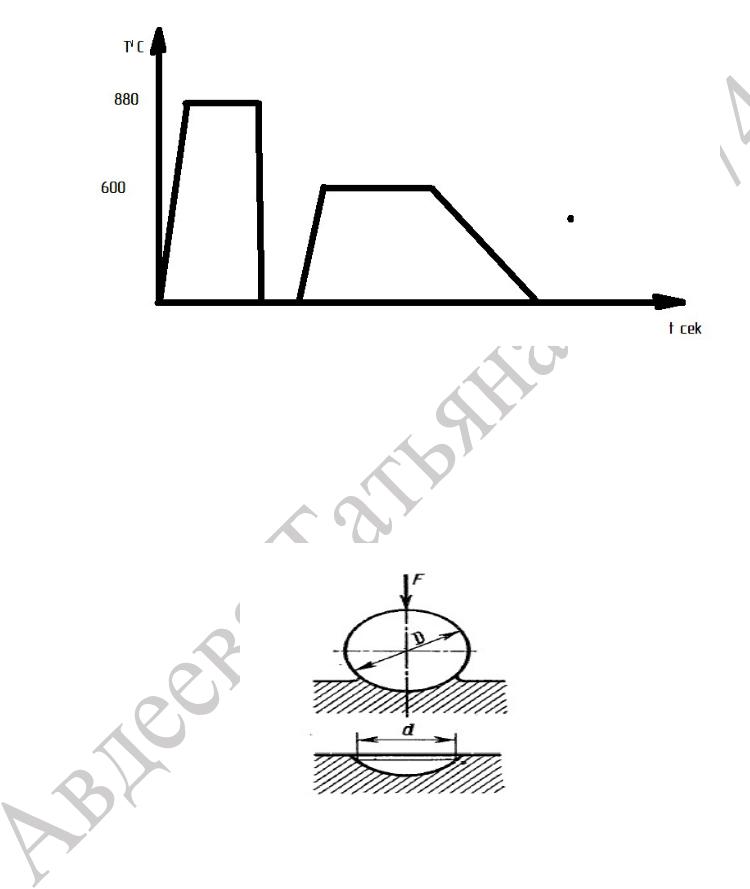
Рисунок 4. График термической обработки изделия
После термической обработки изделие обладает прочностью НВ 230…280. Измерение твердости определяют на приборах – твердомерах. Обозначение HВ показывает, что твердость определяется по методу Бринелля. Индекс В обозначает, что испытание проводится вдавливанием шарика.
Рисунок 5. Метод определения твердости по Бринеллю
9
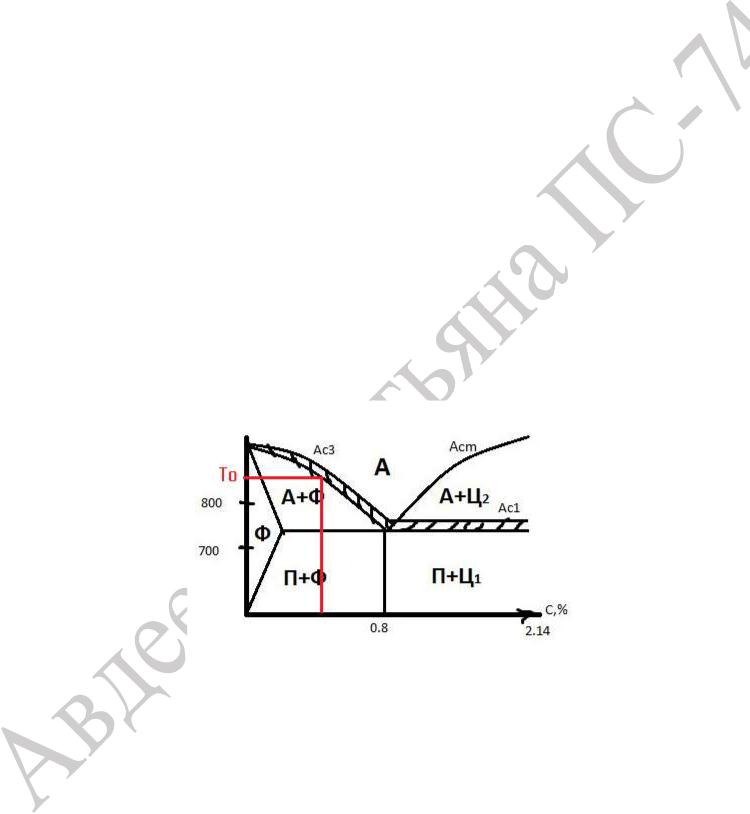
Задание 3.
По своему варианту задания выберите режим термической обработки изделия(ось) из стали 45, для получения заданных свойств = HB2500, обоснуйте свой выбор. Постройте график термической обработки изделия. На основе диаграммы состояний «железо–цементит» и построенного графика термической обработки опишите превращения, происходящие в структуре стали.
Ось – это деталь подвижного состава, воспринимающая на себя вес локомотива или вагона и передающая его через колеса на рельс; работает при повышенных динамических нагрузках.
Сталь 45 – сталь с содержанием углерода 0,45% ,углеродистая конструкционная качественная, доэвтектоидная.
Для получения заданных свойств применим следующую термическую обработку: полную закалку (так как сталь доэвтектоидная) и высокий отпуск. Проведение закалки и высокого отпуска называется улучшением стали.
Рисунок 6. Определение начальной темпертауры термообработки (полная закалка)
Начальная температура термической обработки: То=850°С.
Сначала проводим полную закалку. Её целью является увеличение износостойкости, упругости, прочности и твердости.
10