
книги / Разрушение твердых тел
..pdfХарактерной особенностью усталостного разрушения, позво ляющей выделить его из других видов разрушения, является то, что материал под действием повторных нагрузок, значительно меньших номинального предела прочности, определяемого обыч ными испытаниями на растяжение, в конце концов все же разру шается. Число циклов нагружения, которое материал выдержи вает до разрушения, является функцией максимального напря жения цикла и перепада напряжений за цикл. Имеется очень много литературы описательного характера, в которой процесс усталости рассматривается с точки зрения использования в рас четах; однако здесь будут, обсуждаться лишь те современные теоретические и экспериментальные исследования, в которых анализируется механизм зарождения и развития усталостных трещин при действии повторного нагружения.
Деформационное упрочнение при усталости. Деформацион ное упрочнение при усталости может быть установлено путем из мерения усилия, необходимого для получения одной и той же амплитуды деформации. При таких наблюдениях обычно выяв ляется, в противоположность случаю статического нагружения, «насыщение» упрочнения за период, составляющий ~ 1 % от об щей долговечности образца. Дальнейшее циклическое деформи рование металла с постоянной амплитудой деформации происхо дит при неизменной, или почти неизменной, амплитуде напряже ния. Пример упрочнения описанного типа [38] приведен на рис. 11 для поликристаллической меди. Коффин и Тавернелли [39] опубликовали аналогичные результаты для ряда технически чис тых металлов. Монокристаллам меди и алюминия также свойст венно весьма быстрое снижение интенсивности упрочнения и его насыщение после периода нагружения, составляющего ~ 1 % долговечности образца [40, 41]. Уровень напряжения, при кото ром наблюдается насыщение, систематически возрастает с уве личением амплитуды деформации, как это и показано на рис. И.
Авторы исследований [42—44] предположили, что такие изме нения деформационного упрочнения (а следовательно, и весь процесс усталости) могут быть связаны с тенденцией к попереч ному скольжению винтовых дислокаций, более выраженной при циклическом деформировании, чем при статическом. Основой для этого предположения явилось получение типичной структуры волнообразных прерывистых полос скольжения в циклически нагружаемых кристаллах, аналогичной структуре полос сколь жения, характерной для III стадии скольжения в гранецентриро ванных кубических монокристаллах и, в общем случае, связанной с повышенной частотой поперечного скольжения [45]. Сегалл с сотрудниками [46] в результате исследования изменений струк туры в процессе усталости гранецентрированных кубических ме-
22
таллов методом электронной микроскопии «на просвет» также получили прямые доказательства того, что поперечное скольже ние более характерно для циклического нагружения, чем для статического. Их заключение основывается на резко повышенной плотности мелких петель дислокаций в образцах, работающих на усталость, которые, вероятно, образуются в результате возврат но-поступательного перемещения винтовых дислокаций, имею щих пороги (а значит — совершающих поперечное скольже ние) .
Общим, хотя и довольно неопределенным, объяснением на сыщения деформационного упрочнения является то, что при по-
Рис. 11. Деформационное упрочнение поликристаллнческой меди при действии знакопеременного кручения [38]
перечном скольжении винтовых дислокаций они могут аннигили ровать и, таким образом, создавать условия для легкого движе ния новых дислокаций в области аннигиляции. Альден [47] также показал, что цинковые монокристаллы, подвергаемые цикличе скому нагружению при достаточно низких (—52° С) температу рах, чтобы предотвратить возврат в результате диффузионных процессов, упрочняются до необычно высоких значений (по срав нению со статическим пределом текучести). Такое поведение связано с тем, что поперечное скольжение в цинке сильно за труднено. В противоположность цинку в монокристаллах кад мия поперечное скольжение происходит легко и насыщение упрочнения происходит при низких напряжениях [48]. Махлин и Мак Эвили [44] исследовали эффекты, вызываемые циклическим нагружением ионных кристаллов; они наблюдали усталостное разрушение кристаллов AgCl и Т1Вг, в которых поперечное скольжение весьма легко, но не нашли его признаков у кристал лов LiF и NaCl, в которых поперечное скольжение затруднено.
Скольжение при циклическом нагружении. Многие характер ные особенности процесса циклической деформации, ведущие к образованию усталостных трещин, были впервые описаны Эвингом и Хэмфри [50] еще в 1903 г. Эти исследователи установили, что при циклическом нагружении, как и при статическом, появ ляются линии скольжения, но по мере продолжения циклическо го нагружения они расширяются в более резко выраженные полосы скольжения; в дальнейшем в наиболее интенсивных поло сах скольжения образуются трещины. Далее, с повышением уров ня напряжения плотность полос скольжения повышается, и при более высоком напряжении трещины появляются раньше. Гаф [51] с сотрудниками также исследовал процессы скольжения при циклическом нагружении и показал справедливость закона кри тических касательных напряжений для скольжения, а также уста новил существование напряжения, ниже которого скольжение уже не приводит к развитию трещин. Он показал, кроме того, значение величины перепада напряжений за цикл: при действии двух систем скольжения трещины всегда раньше появятся в той системе, в которой перепад напряжений был больше, даже если максимальное приведенное напряжение во второй системе выше.
Хотя кристаллографическую картину скольжения при устало сти и при статическом нагружении можно считать одинаковой, в этих случаях имеются существенные различия в видимой на по верхности и во внутренней структуре полос скольжения. Прежде всего при усталости скольжение менее однородно; с возраста нием пластической деформации число полос скольжения не уве личивается настолько, чтобы вся поверхность образца оказалась покрытой ими; скорее, наоборот, интенсифицируются лишь от дельные полосы скольжения, о чем можно судить по потемнению и расширению их изображений при микроскопическом наблю дении [41, 52, 53]. Типичные примеры такого эффекта показаны на рис. 12 [54]. Это различие в скольжении при статическом и циклическом нагружении становится более ярко выраженным с уменьшением амплитуды деформации [55]. Альден и Бэкофен [41} нашли, что начало увеличения интенсивности линий скольжения при усталости, видимо, совпадает со стадией затухания быстрого упрочнения. Вуд [55] также установил, что интенсивные полосы скольжения, во рсяком случае — в меди и а-латуни, могут быть выявлены травлением после полирования, в то время как нор мальные полосы (т. е. полученные после статического нагруже ния) выявить не удается. Многие исследователи [53, 56] исполь зовали метод сполировывания поверхностных следов скольжения и последующего нового циклического нагружения, чтобы пока зать, что скольжение имеет тенденцию развиваться в уже суще ствующих (устойчивых) полосах скольжения. Все эти наблюде-
24

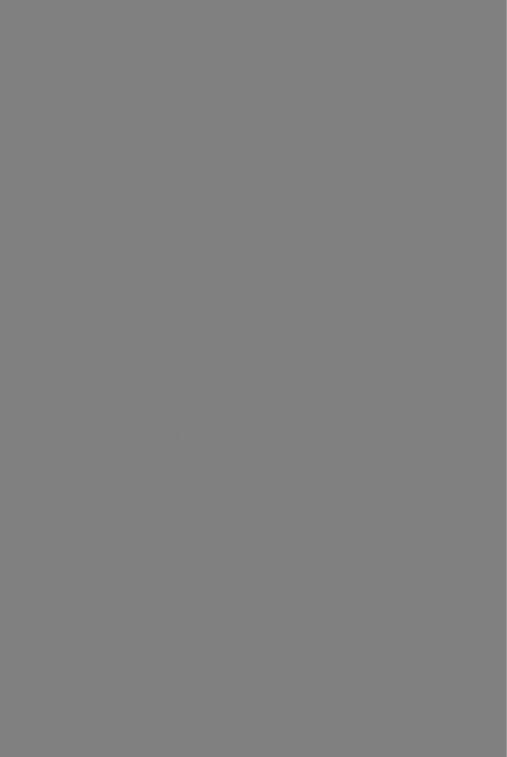
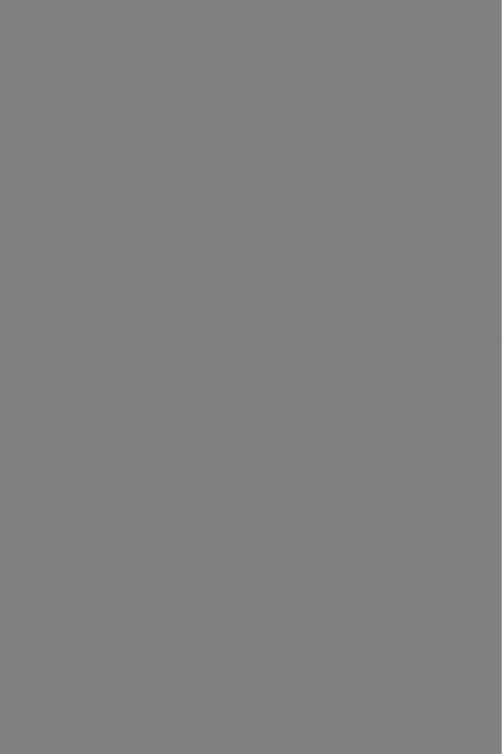
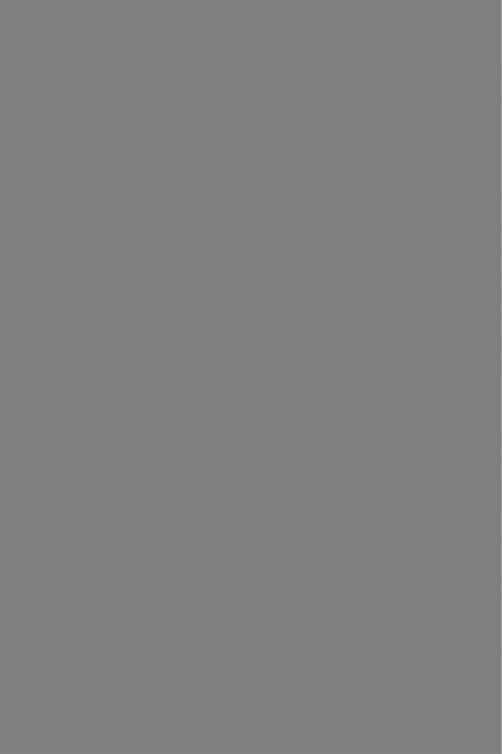
Поверхностные повреждения при усталости. Многие из только что рассмотренных металлографических данных, относящихся к ранним стадиям усталостного разрушения, позволяют предполо жить, что разрушения можно избежать, если удастся предупре дить образование тонких нарушений поверхности при цикличе ском нагружении. Многие исследователи показали возможность увеличения долговечности при усталости, притом, видимо, неог раниченного, путем периодического удаления поврежденного по верхностного слоя. Зибель и Штали [76] в опытах на усталость при изгибе образцов из стали смогли увеличить нормальную дол говечность на 660% путем периодического удаления слоев толщи ной 0,05 мм с поверхности образца. Аналогичные результаты, полученные на железе и стали, указаны в работах Моллера и Хемпеля [77], а также Лисснера [78]. Так как эти опыты проводи лись в условиях циклического изгиба, когда напряжения были максимальными лишь на поверхностности образца, можно было предполагать, что благоприятный эффект от удаления поверх ностных слоев не будет проявляться при испытании образцов в условиях равномерно распределенных (по сечению) напряжений. Однако Томпсон с сотрудниками [53] показал, что долговечность образцов из меди, испытываемых на циклическое растяжение — сжатие, может быть неограниченно увеличена в результате пе риодического электрополирования со снятие^ с поверхности слоев толщиной ^ 2 0 —30 мкм.
Описанные выше результаты были получены в основном для малых амплитуд напряжений (номинальная долговечность со ставляла около 106 циклов), но Раймонд и Коффин показали так же справедливость установленного принципа и при испытаниях алюминия на растяжение — сжатие с амплитудами деформации
в несколько |
процентов; им удалось практически неограничен |
|||
но повысить |
долговечность образцов |
в результате снятия с по |
||
верхности |
после |
каждых 100 |
циклов слоев толщиной |
|
0,12 мм. |
|
|
|
|
Альден и Бэкофен [41] установили, что у алюминиевых моно |
||||
кристаллов возможно увеличение числа циклов нагружения |
(от |
|||
104 до 3- 105 циклов) |
до возникновения трещин в результате |
по |
крытия поверхности тонкой окисной пленкой, предупреждающей развитие поверхностных нарушений. Эти же исследователи так же показали, в отличие от более ранних результатов, что перио дический отжиг тоже может задержать усталостное разрушение, но обязательным условием является проведение отжига до того, как будет достигнуто насыщение деформационного упрочнения. Проведением отжига после каждых 25—30 циклов нагружения им Удалось предупредить образование интенсивных полос сколь жения, характерных для циклического нагружения. В более ран них работах отжиг для устранения повреждений, возникших в результате усталости, обычно проводили слишком поздно для
29
того, чтобы можно было предупредить образование повреждений на поверхности.
Развитие трещин при усталости. В свете имеющихся резуль татов микроскопических наблюдений начальных стадий развития усталостных трещин на поверхности циклически нагружаемого образца, представляется мало обоснованным разделение процес са усталости на периоды зарождения и развития трещин. Про цесс усталости в целом заключается в постепенном прохождении через стадии-концентрации скольжения в «бороздках», образо вании поверхностных неровностей и, наконец, образовании тре щин в области интрузий. С другой стороны, если подходить с точки зрения долговечности, то трещины -появляются значитель но раньше достижения 10% от числа циклов, вызывающих разрушение [55], и, таким образом, не менее 90% долговечности при ходится на период роста трещин.
Имеется большое число исследований ранних стадий уста лостного разрушения, но число структурных и микроскопических исследований, посвященных изучению особенностей процесса роста трещин при циклическом нагружении, весьма ограниченно. В большинстве случаев анализ роста усталостных трещин про водился с целью установления методрв предсказания долговеч ности при усталости в зависимости от приложенного напряжения и потому либо но£ит чисто эмпирический характер *, либо осно вывается на гипотетических механических моделях, которые мо гут быть подвергнуты математическому анализу [80—82]. Так как этот анализ роста усталостных трещин достаточно обсуждался в недавних обзорах Томпсона и Водоворта [83] и Паркера.и Фегредо [58], мы не будем на нем останавливаться. Мы ограничимся лишь теми работами, которые касаются микроструктурного ана лиза роста трещин.
Вуд [55] описал самые ранние стадии продвижения трещин* основываясь на наблюдениях по описанному выше методу на клонных сечений. Он наблюдал, что образовавшиеся на поверх ности в области интрузий микротрещины продвигаются вдоль ин тенсивных полос скольжения и перерастают в «разрывы» (см. рис. 14). При дальнейшем циклическом нагружении эти «разры вы» по полосам скольжения, перескакивая от одного разрыва к другому, превращаются в более широко развитые трещины, про ходящие нерегулярно через зерно, а иногда и по границам зерен. Таким образом, развитие усталостной трещины на ранних ста диях можно проследить методом микроскопического изучения по верхности после различного периода испытаний. Томпсон с сотрудниками [53], используя эту методику для поликристаллической меди, нашли большое число мелких трещин, длина которых в основном не превышала диаметра одного зерна и которые могли быть удалены электролитической полировкой на глубину1
1 По данным Христенсена и Денке.
порядка 10 мкм после испытаний продолжительностью ~ 5 % от долговечности. С дальнейшим увеличением продолжительности циклического нагружения число и глубина трещин увеличивают ся и, начиная примерно с 40% от долговечности, уже можно наблюдать проникновение трещин в соседние зерна. Однако боль шие непрерывные трещины, проходящие через несколько зерен, обнаружены не были, вплоть до последних моментов работы об разца. Такие результаты показывают, что фрактографический анализ развития повреждений при усталости дает сведения лишь о весьма коротком последнем периоде службы образца и при том— для гладких образцов. В то же время у образцов с остры ми надрезами или при структуре, имеющей области типа надре зов, эта конечная стадия развития макроскопической трещины может составлять основную долю всего процесса усталостногоразрушения.
Характерные макроскопические признаки усталостного раз рушения хорошо известны и уже давно используются для выяс нения типа разрушения и для нахождения локальных источников усталостного разрушения. Макроскопические, приблизительнополукруговые следы, концентричные точке зарождения разруше ния, не отображают последовательные положения трещины,, занимаемые ею по мере увеличения числа циклов нагруже ния.
Современные электронномикроскопические исследования по верхностей изломов усталостного разрушения [56] показали, чтона этой поверхности имеется весьма тонкая система многочислен ных бороздок, которые, вероятно, и отображают положения фронта трещины, продвигающейся при каждом цикле нагруже ния. Крюссар с сотрудниками [56], а также Христенсен и Денкена большом числе различных материалов показали, что протя женность указанных бороздок определяется приложенным на пряжением и что по мере увеличения длины трещины протяжен ность бороздок закономерно возрастает, отображая, во всяком случае качественно, увеличение скорости роста трещины с увели чением ее длины.
В противоположность разрушению других типов, характер' картины на этих конечных стадиях усталостного разрушения ока зывается мало зависящим от структурных особенностей мате риала, а именно — от границ зерен, через которые продвигается трещина. Крюссар с сотрудниками [56] установил, что границы зерен остаются неразличимыми на поверхности усталостного раз рушения и не выявляются по каким-либо нарушениям непрерыв ности системы бороздок; для выявления положения границ зерен необходимо травление поверхности изломов уста лостного разрушения. Детали процесса разрушения, объясняю щие механизм продвижения фронта трещины в каждое следую щее его положение, пока остаются неясными; при больших уве