
Организация производства
.pdf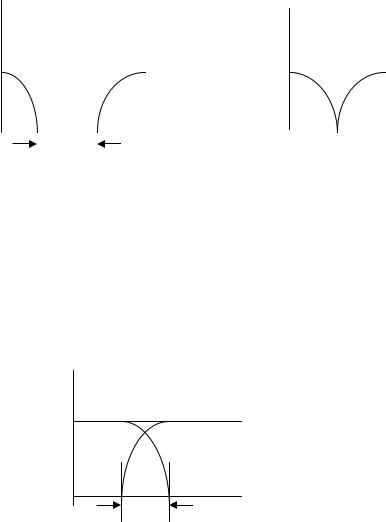
ОСОБЕННОСТИ ОРГАНИЗАЦИИ ПРОИЗВОДСТВА НОВОЙ ПРОДУКЦИИ
Существует 2 формы перехода на выпуск новой продукции : переход с остановкой производства и без остановки производства. В каждой из этих форм выделяется последовательный, параллельный и параллельно последовательный методы перехода. На выбор метода влияют следующие факторы:
1.Техническое отличие новой продукции от снимаемой с производства;
2.Организационнотехнические условия производства;
3.Наличие резервных мощностей и площадей;
4.Возможность использования стандартного решения на этапе проектирования.
Последовательный метод характеризуется тем, что производство новой продукции начинается после полного прекращения производства старой продукции. Метод может быть прерывнопоследовательным и непрерывно – последовательным.
Прерывнопоследовательный Непрерывнопоследовательный
Q
|
Проектн. Выпуск |
|
|
|
проектн. выпуск |
|||
C |
|
|
|
H |
|
|
C |
H |
|
|
|||||||
|
|
|
|
|
T |
|
||
|
|
|
|
|
|
|
|
|
|
|
T |
|
|
|
|
|
|
|
|
|
|
|
|
|
С- старая продукция, Н – новая продукция.
Интервал Т вызван перепланировкой оборудования, монтажом оборудования и транспортных средств. Это самый неэффективный вариант перехода, так как очень большая длительность цикла.
Непрерыно – последовательный метод возможен в том случае, если полностью завершены работы по технологической подготовке производства нового изделия к моменту его выпуска.
При параллельном методе одновременно с сокращением старой продукции происходит наращивание новой.
Q
СН
T
Т
41
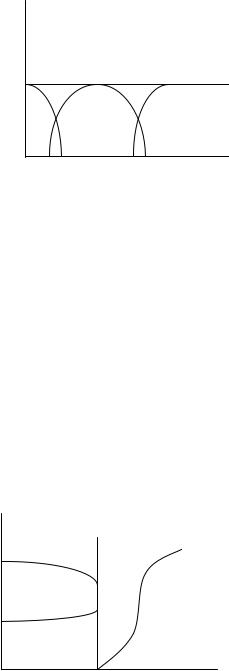
Величина Т зависит от технических возможностей предприятия. Этот метод более выгоден, так как предприятие сохраняет свой выпуск продукции, но он требует дополнительных мощностей и дополнительных производственных рабочих. Применяется в массовом производстве, особенно при реконструкции предприятия.
В условиях массового производства применяется параллельнопоэтапный метод. В этом случае осваивается переходная модель, отличающаяся от старой конструкции. Происходит обновление не конечной продукции, а лишь ее отдельных элементов. Благодаря этому методу удается избежать коренной реконструкции предприятия и снизить затраты на освоение производства.
Q
C П Н
T
Недостаток: большая длительность цикла, что может привести к моральному устареванию нового изделия.
При параллельно – последовательном методе на предприятии создается дополнительные мощности, на которых начинается освоение новой продукции. Пересматривается технология изготовления, проводится переподготовка персонала. Параллельно с подготовкой нового изделия происходит завершение выпуска старого изделия, затем кратковременная остановка производства для перепланировки оборудования с дополнительных участков в цехи основного производства. Метод используется в массовом производстве при освоении продукции существенно отличающейся от снимаемой, когда промежуточная модель невозможна. Подготовка производства на дополнительных участках обеспечивает более высокие темпы нарастания выпуска новой продукции.
Q
C
H T
42
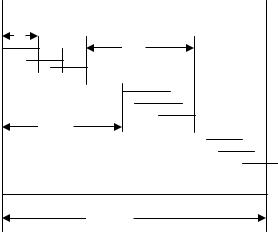
КАЛЕНДАРНО–ПЛАНОВЫЕ НОРМАТИВЫ СЕРИЙНОГО И МАССОВОГО ПРОИЗВОДСТВА
Календарноплановые нормативы (КПН) – это совокупность норм и нормативов по наиболее эффективной организации в краткосрочном периоде. КПН используются в оперативно – календарном планировании.
Основными КПН являются:
-размеры серии выпускаемых изделий;
-размеры партии обрабатываемых изделий;
-периодическая запуска выпуска изделий и деталей;
-длительность производственного цикла серии или партии;
-величина уровня заделов.
Основным КПН является размер партии или серии. Промежуток времени между запуском или выпуском двух серий называется ритмом запуска или выпуска серии.
Рассмотрим график запуска – выпуска серии изделий:
TЦ |
rB |
RB |
r3 |
|
|
|
R З |
|
|
|
Тпл |
Тпл = Тц+ r (n-1)+R (k-1)
n- размер серии;
k- количество серий;
r- ритм запуска или выпуска изделий в серии; R- ритм запуска – выпуска изделий;
Тц – длительность цикла изготовления одного изделия в серии. Средний ритм запуска (выпуска):
rср=Тэфф/Qвып
Темп запуска (выпуска) изделий:
r = Qвып/ Тэфф
Величина r задается планом или определяется при распределении производственной программы по кварталам и месяцам. Между средним ритмом и размером серии имеется зависимость: R= r * n
R= n * Тэфф/Qвып= Тэфф/Qдн (средн)
43
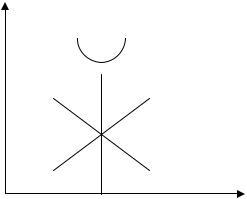
При одинаковых ритмах для различных деталей размер серии будет пропорционален среднедневному выпуску. Размер партии оказывает большое влияние на различные технико – экономические показатели. С ростом размера партии производительность труда растет, так как растет квалификация рабочего и сокращается штучное время на обработку деталей. Также сокращается доля подготовительно – заключительного времени, приходящегося на 1 деталь. Себестоимость детали снижается за счет постоянных расходов, приходящихся на 1 деталь. Длительность цикла обработки и величина незавершенного производства растет с ростом размера партии. Отсюда вытекает задача определения оптимального размера партии:
ПНнезаверш. производство
ПН C
Nопт
РАСЧЕТ ЗАДЕЛОВ В СЕРИЙНОМ ПРОИЗВОДСТВЕ
Незавершенное производство - совокупность заделов, т. е. деталей, изделий, находящихся на различных стадиях производственного процесса: на рабочих местах, участках, цехах, кладовых, межцеховых складах. Излишек или недостаток приводит к увеличению потребности в оборотных средствах и замедлению их оборачиваемости. Различные внутрицеховые или цикловые заделы и межцеховые (оборотные и страховые). Цикловый задел – это количество изделий, находящихся в производственном процессе в цехе на тот или иной момент времени.
Zцикл=Тц * Qср. дн.
ТЦ – длительность цикла изготовления партии; Q – средний дневной выпуск изделий.
Оборотные заделы между цехами возникают из-за различия в поступлении и потреблении изделий.
В серийном производстве поступление деталей в цех происходит не постепенно, а срезу всей партией.
Zоб=nmax- nmin/2
.Для уменьшения оборотного задела нужно либо уменьшить максимальный, либо увеличить минимальный размер.
Но увеличение минимального размера партии ведет к увеличению длительности производственного цикла обработки и, следовательно, к увеличению циклового задела.
44
Чтобы этого избежать создаются резервные заделы 2 способами6
1)увеличением размера первых партий в каждом цехе;
2)увеличением сменности работы за счет временного перераспределения рабочих между цехами и участками.
Вмассовом производстве присутствуют заделы: технологический, транспортный, резервный, оборотный. Технологический задел обеспечивает одновременное начало работы на всех рабочих местах при запуске поточной линии.
m
Zтехн=Σ ci * qi
I=1
ci – число рабочих мест на i- ой операции;
qi – число деталей или изделий, обработанных на 1-ом рабочем месте; m- число операций;
Транспортный задел – количество изделий, находящихся в данный момент на конвейере.
Zтран=Lраб/ lтр.п. *nтр.п.
Lраб- рабочая дина конвейера;
lтр.п. – расстояние между транспортными пачками или партиями изделий; nтр.п- размер транспортной пачки.
Резервный задел – создается для обеспечения непрерывной работы поточной линии в случае каких – либо сбоев. Резервный задел создается за счет уплотнения труда рабочих и результаты в нерабочее время или на внепоточных участках.
Межоперационный задел – возникает на прерывных поточных линиях, в следствие различия норм времени в сметных операциях, а также при резервном времени начала работы не полностью загруженных рабочих мест.
РАСЧЕТ ОПЕРЕЖЕНИЙ ЗАПУСКА И ВЫПУСКА ПАРТИЙ ДЕТАЛЕЙ
Под отражением запуска понимается отрезок времени от момента запуска в обработку партии изделий в цехе, до момента выпуска всех тех изделий, для которых были запущены в обработку партии деталей в цехе. Опережение выпуска (Ов) отличается от опережения запуска (Оз) на величину длительности цикла изготовления партии деталей (или серии). Опережения необходимы для расчета и соблюдения сроков запуска и выпуска партии деталей по цехам в котором происходит их обработка.
Рассмотрим расчет опережений для различных сочетаний ритмов и размеров партий в 2-х смежных цехах.
ОЗ1=ТЦ1+ТЦ2+(R1- R2)
R1/R2 –целое число;
R1- ритм запуска или выпуска партии в 1-ом цехе;
R2- ритм запуска или выпуска партии во 2-ом цехе.
45
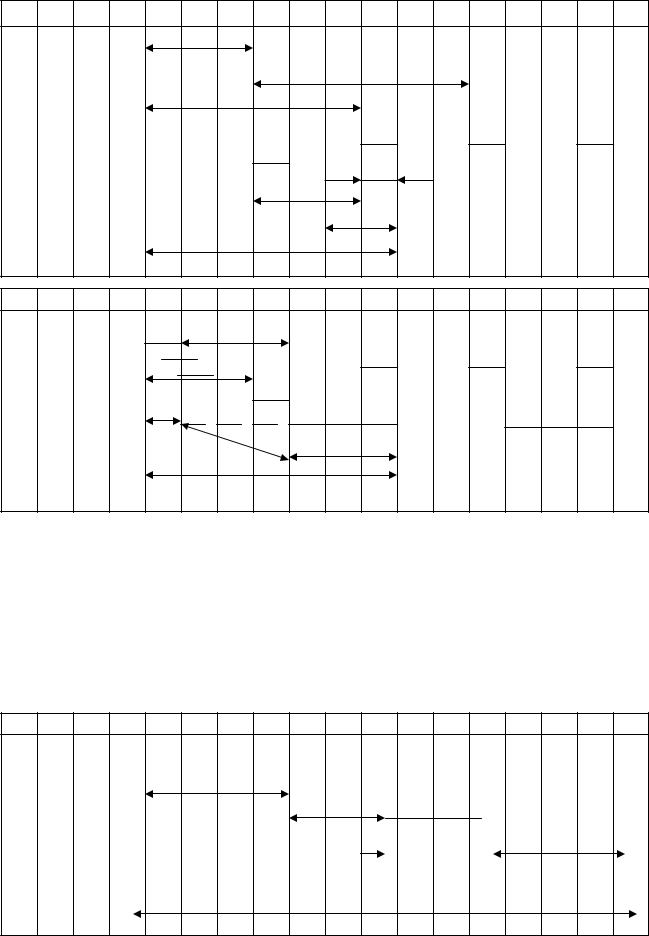
N |
R |
n TЦ 1 |
2 |
3 |
4 |
5 |
6 |
7 |
8 |
9 10 11 12 |
13 14 |
1 |
6 |
20 |
3 |
|
ТЦ1 |
|
|
20 |
|
|
|
|
|
|
20 деталей |
|
|
|
|
|
|
|
|
|
|
|
|
|
|
|
||
2 |
3 |
10 |
1 |
|
от конца до конца |
R1 |
|
|||
|
|
|||||||||
от начала до начала |
R1 |
|
|
|
||||||
|
|
|
|
|
|
10 |
10 |
10 |
10
ТЦ
R2
R2
N |
R |
n TЦ |
1 |
2 |
3 |
4 |
5 |
6 |
7 |
8 |
9 |
10 |
11 12 |
13 14 |
|
1 |
3 |
10 |
1 |
10 |
|
R2 |
|
|
|
10 |
|
|
10 |
|
10 |
2 |
6 |
20 |
3 |
|
R1 |
|
|
|
|
|
|
|
|||
|
|
10 |
|
|
|
|
|
|
|
|
|||||
|
|
|
|
ТЦ |
|
Тедв |
|
20 |
|
|
|
|
20 |
|
|
|
|
|
|
|
|
|
|
|
|
|
|
||||
|
|
|
|
|
|
Q32 |
|
|
ТЦ2 |
|
|
|
|
|
|
|
|
|
|
|
|
|
|
|
|
|
|
|
|
|
Разность между ритмами R1 и R2 можно рассматривать как сдвиг между длительностями циклов обработки партии.
Тсдв2 – это сдвиг момента запуска первой партии деталей во 2-ом цехе по отношению к ее выпуску в 1-ом цехе.
В общем виде формула выглядит так:
ОЗ1=ТЦ1+ТЦ2+ Тсдв2 +(]R1- R2[-1)* R2
]R1- R2[ - округление до ближайшего целого.
N |
R |
n TЦ 1 |
2 |
3 |
4 |
5 |
6 |
7 |
8 |
9 10 11 12 |
13 14 |
1 |
12,5 |
100 |
4 |
100 деталей |
|
|
|
|
40 |
|
|
|
|
|
ТЦ1 |
|
|
|
|
|
|
2 |
5 |
40 |
2 |
|
Т едв2 |
|
40 дет |
|
|
|
|
|
|
|
|
|
|
ТЦ2 |
|
R2 |
|
|
|
|
|
|
|
Q31 |
|
|
|
46

ОЗ1=ТЦ1+ТЦ2+ Тсдв2 + 2R2
2R22=(]R1/ R2[-1)*R2=(]12,5/ 5[-1)*R2
ОЗ1=ТЦ1+ТЦ2+ Тсдв2 +(]R1/ R2[-1)* R2
Сдвиги необходимы для того, чтобы сократить ритмичность запуска партии во 2-ом цехе на весь период обработки до полного окончания обработки всех деталей.
Если такой сдвиг не предусмотреть в самом начале запуска деталей во 2-ом цехе, то в некоторый момент времени он произойдет сам и нарушит ритмичность процесса.
Величина сдвига рассчитывается как:
Тсдв=Rmin –ДR
Rmin- это наименьший ритм в 2-х смежных цехах;
ДRнаибольший общий делитель в 2-х смежных цехах;
ОЗ1=ТЦ1+ТЦ2+ R2- ДR1,2+(]R1/ R2[-1)* R2
Формула дает величину максимального опережения для 1-го цеха.
При расче5те опережений необходимо учитывать также резервные опережения между выпуском деталей в 1-м цехе и запуском во 2-м, если сдвиг необходим для ритмичности запуска партии, то резервное опережение учитывают возможную задержку выпуска из 1-го цеха или преждевременный запуск во 2-ом цехе.
В резервное время включается так же время оформления документов и транспортировки партии в следующий цех, выбирается в пределах меньшего ритма. Величина опережений может рассчитываться как в днях, так и в натуральных единицах:
Оз ит=Оз дн*Одн (шт/дет)
Пример: для резервного опережения: пусть Трезерв=3 дня, Тц обработки в заготовительном цехе 1 день, Тц в механическом цехе – 4 дня, В сборочном
цехе 5 дней.
Оз общ= 1+3+4+3+5=16 дней
3
5
сбор
3 дн
4
мех
1
заточ
Qз
47
ОПЕРАТИВНОЕ УПРАВЛЕНИЕ ПРОИЗВОДСТВОМ
Оперативнопроизводственное планирование(ОПП) – это комплекс работ по организации оперативнокалендарных планов производства, разработке сменносуточных заданий для рабочих мест, его участков и рабочих мест. Если планирование представляет из себя распределение годовой производственной программы между цехами и участками по месяцам, то опытноконструкторские работы заключаются в распределении на короткий период, вплоть до смены. Плановоучетными единицами являются отдельные изделия, сборочные единицы, детали, операции. Регулирование хода производства осуществляется путем диспетчирования.
Порядок оперативного планирования заключается в составлении местного плана, уточняются сведения по сырью, материалам, энергетике, технологическим режимам, труду и заработной плате. Группа ОПП сообщает производственным подразделениям задание на выпуск продукции, выдает задание отделам (техническому, отделу главного механика, отделу главного технолога, отделу главного энергетика) на подготовку производства по основным позициям: по внедрению новых режимов с указанием сроков по изготовлению норм выработки, по срокам ремонтного оборудования, сообщает лимиты по тепло и электроэнергии.
При планировании определяется вся сумма работ, которая должна быть выполнена в определенный отрезок времени. Она складывается из недовыполненной работы независимо от причин ее невыполнения и новой работы по текущим заданиям. Эта сумма работ является планом работы.
Планы выдаются каждому цеху, участку, с условием учета конкретных цеховых условий и ожидаемых изменений.
1)В первую очередь корректируются задания по основному производству, учитывается фактическое выполнение программы за предшествующий период по количеству ассортиментов комплектности, учитывается уровень заделов, на основании планов работ составляется разнарядка на декаду или неделю. В соответствии с планом работ при необходимости корректируется материальный баланс, учитывается наличие сырья, полуфабрикатов, ожидаемые поступления, количество отказов, подлежащих исполнению, возможность исполнения заменителей, разрешенных технологических регламентов и т. д.
2)После уточнения плана работ на основе материального баланса корректируют, учитывается режим работы и график ремонта, выясняется на каких агрегатах и в каких цехах должны быть отключены производственные мощности в связи с графиком нагрузок по электроэнергии. Рассчитывается уровень производительности оборудования, выявляются узкие места. Процесс контроля и регулирования хода производства в краткосрочном периоде называется диспетчированием. Процесс диспетчирования зависит от типа производства. В серийном производстве объектами диспетчерского контроля являются являются сроки запуска и выпуска партии деталей, состояние складских заделов
48
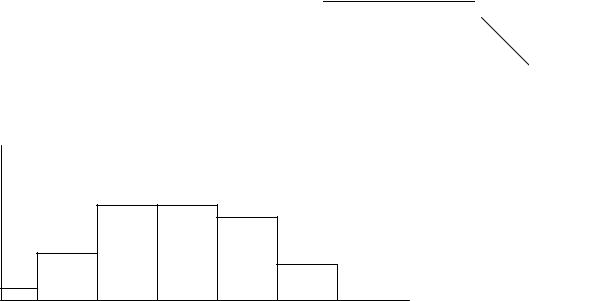
деталей, комплектность сборочных работ. В массовом производстве объектами контроля являются соблюдение ритмов поточных линий, уровень заделов на всех стадиях производственного процесса. В единичном производстве – это сроки выполнения работ по отдельным заказам. Важнейшим условием выполнения календарных планов является полная техническая подготовка производства.
Контроль за ходом производства осуществляется по направлениям:
-по номенклатуре выпуска изделий
-контроль комплектности деталей и покупных изделий
-по выпускающим цехам контроль заделов, а также межцеховых
передач заготовок, деталей, сборочных изделий, контроль оперативной подготовки производства.
Информация о ходе производства поступает из разных источников. Это карточки табельного учета, где отражаются трудозатраты, заказы на поставки, отчетность с места выполнения работ.
Для контроля выполнения календарных планов используется различные методы и модели, например ленточные графики, они строятся на основе допущения линейной зависимости объёма выполненных работ от времени.
1. ленточные графики
Фактич.выполнение
|
|
|
март |
|
|
|
|
Контр. |
|
январь |
|
февраль |
||
|
|
|||
|
|
|
|
точка |
2. S-кривые (применяются часто в строительстве)
В результате контроля анализа выявляются узкие места в текущем и предстоящем ходе работ и подготавливаются предложения по их устранению. Принимаемое решение является программой работ на предстоящий период.
49

СИСТЕМЫ ОКП
Применение той или иной системы ОКП обусловлено типом и объёмом производства, видом выпускаемой продукции. В массовом производстве используется партионно-периодическая система и система планирования по ритму запуска.
При партионно-периодической системе устанавливаются партии деталей, которые и являются планом-графиком работы цеха. При системе планирования по ритму запуска осуществляется выравнивание производительности всех звеньев производственного участка. Составление оперативных программ ведется в последовательности, обратной технологическому процессу.
технологический процесс
заготовительная |
обрабатываю- |
сборочная |
Заготов |
щая стадия |
стадия |
стадия |
составление оперативных программ
В серийном производстве используется системы планирования по групповым комплектам, по опережениям, по заделам и другим нормативам.
При планировании по групповым комплектам детали объединяются в группы в зависимости от периодичности их изготовления, деятельности производственного цикла, маршрута движения.
При использовании системы планирования по опережениям для каждой партии рассчитывается опережение запуска продукции, Эта система наиболее распространена в серийном производстве.
Система планирования по заделам основывается на поддержании определённого уровня заделов.. Используется при непрерывном выпуске и сборке изделий. В единичном и мелкосерийном производстве используется позаказная система планирования, строится график работы для каждого заказа, который увязывается с графиками выполнения других заказов.
ТЕХНИЧЕСКОЕ И ПРОГРАМНОЕ ОБЕСПЕЧЕНИЕ СИСТЕМЫ УПРАВЛЕНИЯ ПРОИЗВОДСТВОМ
Для обмена информацией на предприятии применяются сети ЭВМ необходимой конфигурации и протяженности. Они могут объединять различные типы вычислительной техники. Сети включают автоматизированные рабочие места – комплекс аппаратурных, программных и информационных средств для решения задач пользователя на его ПК, решение диалога с ЭВМ. Внедрение АРМ позволяет повысить оперативность информации, обеспечить управление производством в реальном масштабе времени.
Создан6ие АРМ освобождает персонал от различной работы по оформлению документов и проведению расчетов. Для создания АРМ требуется 1 ЭВМ, к корой подключаются различные устройства:
50