
книги / Металлургия черных и цветных металлов
..pdf9
8
Рис. VI.3. Футеровка 100-т дуговой электропечи: |
|
|
|
|||||
/ — металлический кожух; 2 — листовой асбест; |
3 — слой |
шамотного |
по |
|||||
рошка; 4 — шамотный |
кирпич; |
5 — магнезитовый |
кирпич; |
6 — магнезитовый |
||||
порошок; 7 — кольцевой рельс; |
8 — заслонка; |
9 — рама рабочего окна; |
10 — |
|||||
уплотняющее |
кольцо; |
11 — песочный |
затвор; |
12 — магнезитовая кладка |
стен; |
|||
13 — молотый |
асбест; |
14 — шамотный |
кирпич |
|
|
|
|
Стены укладывают на футеровку откосов. Чтобы предохра нить стык между футеровкой стен и откосами ванны от размыва шлаком, откосы поднимают на 100—200 мм выше уровня порога рабочего окна (или зеркала ванны). Толщина стен в нижней части 300—575 мм. Стойкость стен крупных печей до 100—250 плавок.
Свод основных печей средней и большой вместимости наби рают из магнезитохромитового кирпича, на специальном шаб лоне в сводовом кольце. Благодаря выпуклости шаблона кладка свода получается с необходимой кривизной. При изго товлении свода в кладке оставляют три отверстия для элек тродов и отверстия для отсоса печных газов. Толщина свода больших печей достигает 230—400 мм, стойкость свода 50— 100 плавок. Печь ДСП-100И6 имеет водоохлаждаемый свод. Водоохлаждаемая поверхность его составляет,~80 % поверхно сти. Она выполняется в виде секторов коробчатой конструкции или из трубчатых панелей трапецеидальной формы. Централь ная часть свода, во избежание короткого замыкания между электродами и корпусом через свод выполняется из огнеупор ного кирпича. В кладке имеется три отверстия для электродов, а в металлической периферий,ной части — отверстия для отвода печных газов. Стойкость водоохлаждаемых сводов достигает 3000 плавок и более.
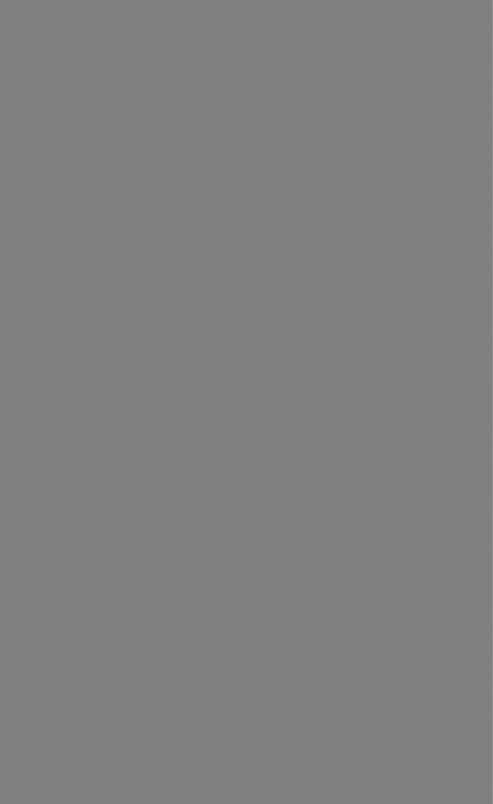
Уплотняющие кольца закрывают промежуток между отвер стием в своде и электродом. Они предохраняют электроды от излишнего окисления и нагрева газами, выходящими из печи, обеспечивают герметичность зазора между электродом и сво дом. На печах малой и средней вместимости применяют так на зываемые экономайзеры — полые водоохлаждаемые кольца, рас полагаемые вокруг электрода на своде или утопленные в кладку свода. Иногда его выполняют в виде змеевика из цельнотянутой трубы, опускаемого в зазор. На печах большой вместимости при меняют газодинамические уплотняющие кольца. Оно состоит из кольца огнеупорного бетона, на которое опирается полое металлическое кольцо. В это кольцо тангенциально подводят сжатый воздух. Воздушный поток препятствует выбиванию га зов из печи. Кольца устанавливают на своде печи.
Электрододержатели предназначены для подвода тока к элек тродам и удержания их на определенной высоте в печи. Электрододержатель состоит из головки, охватывающей электрод, пружинно-пневматического зажима, рукава, телескопической стойки и жесткой части вторичного токоподвода.
Головки электрододержателей изготавливают из стали, бронзы или латуни и делают водоохлаждаемыми. Зажим элект рода производят пружинным механизмом, а отжим — с помо щью пневматического цилиндра, в который подается сжатый воздух. Шток поршня пневмоцилиндра сжимает пружину и освобождает электрод. Каждый из электродов имеет свой неза висимый механизм зажима и перемещения в вертикальном на правлении. В механизме перемещения электродов с телескопи ческой стойкой рукав электрододержателя закреплен на под вижной стойке, перемещающейся внутри полой вертикальной неподвижной стойки. Подвижная часть механизма снабжена противовесом, что позволяет уменьшить мощность привода. Привод может быть гидравлический или электромеханический. Скорость перемещения при подъеме до 6,0 м/мин, при спуске
1,0—1,5 м/мин.
Электрооборудование печи. Дуговая электропечь является сложным агрегатом, оснащенным рядом устройств и приборов, обеспечивающих снижение высокого напряжения (6—110 кВ), до рабочего (110—600 В) и подвод тока к электродам. Электри ческая схема трехфазной дуговой печи представлена на рис. VI.4. Она включает высоковольтный кабель КВН, ток от кото рого при помощи воздушного разъединителя Р и главного мас ляного выключателя ГВ подается через дроссель Др и пере ключатель ступеней напряжения ПСН к первичной обмотке печного трансформатора ПТ. Со вторичной обмотки трансфор матора ток поступает через так называемую короткую сеть к электродам. Кроме того, имеются выключатель, шунтирую щий дроссель, трансформатор1! тока ТТ и напряжения ТН,
а также защита, измерительные прибо ры и автоматика.
Воздушный разъединитель Р служит для отключения электропечи от высоко вольтного кабеля. Главный выключа тель предназначен для разрыва высо ковольтной цепи, находящейся под на грузкой. Он состоит из железного, изо лированного внутри бака, заполненного до определенного уровня трансформа торным маслом, в который погружен вы ключающий механизм. Масло гасит электрические дуги, возникающие при отключении масляного выключателя под нагрузкой, и является изоляцией между отдельными токоведущими частями.
Дроссель Др служит для увеличения устойчивости горения электрических дуг и ограничения толчков тока при корот ких замыканиях, возможных при обва лах шихты, когда электрод соприкаса ется с металлом. На печах большой мощности (>10 МВ-А) дроссель не устанавливают, так как индуктивное сопротивление трансформатора и корот кой сети достаточно для стабилизации горения дуг и ограничения токов корот кого замыкания. Печной трансформатор ПТ служит для преобразования элек троэнергии высокого напряжения и ма лой силы в ток низкого напряжения и
большой силы. Тяжелые условия его работы, связанные с пере грузкой, с частыми короткими замыканиями, имеющими место при зажигании дуг и обвалах шихты при плавлении, предъяв ляют высокие требования к его конструкции и качеству изго товления. Первичные и вторичные обмотки должны иметь на дежную изоляцию, высокую механическую прочность и интен сивное охлаждение.
Сердечник с обмотками находится в баке, заполненном трансформаторным маслом. Трансформаторы печей средней и большой вместимости имеют принудительное водо-масляное ох лаждение. Трансформаторы обычно устанавливают в отдельном помещении рядом с печью. Мощность трансформатора является определяющим фактором продолжительности плавки и произ водительности печи. Наибольшая мощность потребляется печью
впериод плавления, поэтому продолжительность этого периода
иопределяет мощность трансформатора:
Печь ДСП-100И6, относящаяся к сверхмощным, оснащена трансформатором мощностью 75 МВ*А со ступенями вторич ного напряжения. На первых четырех ступенях напряжения (761, 722, 686, 654 В) кажущаяся мощность трансформатора остается постоянной и равной 75 МВ • А при соответствующем изменении силы рабочего тока (56,9; 60,0; 63,1; 66,2 А), коэффициента мощности (cos ср: 0,75; 0,73; 0,69; 0,65) и активной мощности Ра (56,2; 54,7; 52,0; 49,0 МВт), на остальных ступенях напряжения мощность трансформатора понижается. Наличие ступеней по стоянной мощности расширяет возможности выбора рациональ ных режимов плавки. Особенно это относится к периоду рас плавления, когда проплавление колодцев следует вести при максимальном боковом излучении дуг, плавление основной массы шихты при максимальной суммарной мощности дуг, доплавление металла открытыми дугами. Использование ступеней постоянной, мощности позволяет также увеличить средний за период расплавления коэффициент мощности при работе на высших ступенях напряжения и уменьшить токовые нагрузки, на электроды, что способствует снижению их расхода. При этом сохраняется возможность работы в период открытого горения с низким коэффициентом мощности, на укороченных загублен ных в расплав дугах.
В настоящее время как за рубежом, так и в СССР харак терна тенденция к увеличению мощности трансформаторов, т. е. применению электропечей сверхвысокой мощности. Вместо обычной удельной мощности трансформаторов 200—300 кВ*А/т используют трансформаторы, удельная мощность которых со ставляет 500—700 кВ*А/т и даже 1000 кВ*А/т. Переключатель ступеней ПСН напряжений трансформатора позволяет в про цессе плавки изменять напряжение, а следовательно, и подво димую мощность к печи.
Короткая сеть — токоподвод от выводов вторичного напря жения трансформатора до электродов — должна быть выпол нена как можно короче. Короткая сеть состоит из медных шин — выводов От трансформатора за стену трансформаторного поме щения, гибкого кабеля и медных шин или водоохлаждаемой трубы над рукавом электрододержателя.
Автоматическое регулирование положения электродов необ ходимо для изменения мощности, подаваемой в печь. Для этой цели применяют регуляторы, управляющиедвигателями при вода электрододержателя. Регулятор может работать совместно со специальным вычислительным устройством, регулирующим количество вводимой в печь электроэнергии.
Система отвода и очистки газов. В процессе плавки из печи выделяется большое количество газов и дыма. Удельный объем выделяющихся газов в зависимости от количества вдуваемого кислорода составляет 180—800 м3/т стали в час. Запыленность
Рис. V I.5. |
С х ем а газо о ч и стк и «м окрого» |
ти п а (------- |
водовод осветленной в о д ы ; --------- водовод |
шламовой |
|
воды) |
|
|
газов в различных |
периодах плавки составляет от 2 до 18 г/м3, |
что в десятки раз превышает норму (150 мг/м3). В связи с же сткими требованиями, предъявляемыми к металлургическим агрегатам в части охраны окружающей среды, современные электропечи оборудуют системой улавливания и очистки отхо дящих газов. Наиболее распространенным способом является
отвод газов через четвертое отверстие |
(три для электродов) |
|
в своде. |
|
|
Принципиальная схема газоочистки мокрого типа, которой |
оборудованы |
|
отечественные электропечи средней .вместимости, |
представлена |
на рис. VI.5. |
Дымовые газы под действием дымососа отводятся из рабочего пространства печи 1 через водоохлаждаемый патрубок 2 , встроенный в четвертое отверстие. Затем газы поступают в стационарный газоход 3. В зазор между сводом и газозаборным патрубком подсасывается воздух, необходимый для дожигания горючих компонентов газа (СО, Нг) в самом патрубке. Окончательное дожига ние, а также охлаждение газов происходят в стационарном газоходе в резуль
тате поступления воздуха в зазор между фланцами газозаборного патрубка |
и |
||||
стационарного газохода. По газоходу запыленные газы поступают в |
коллек |
||||
тор щелевидных труб Вентури 4. Далее проходят |
каплеуловитель 5 |
и с |
по |
||
мощью вентилятора 7 удаляются через дымовую |
трубу 8 |
в |
атмосферу. Со |
||
противление труб Вентури и газовая нагрузка вентилятора |
устанавливаются |
||||
дроссель-клапаном 6. Количество газов, отбираемых от |
печи по периодам |
||||
плавки, регулируеюя спаренными дроссель-клапанами 9 |
(10 — гидрозатвор). |
Подобная система очистки с некоторыми конструктивными особенностями применяется и на 100-т печах. Эти системы обеспечивают улавливание 70— 80 % дымовых газов, но они не позволяют улавливать газы, выделяющиеся
при загрузке шихты и выпуске металла, а также через рабочее окно и неплот ности между сводом и корпусом и др. В связи с этим электропечи стали по мещать в герметичные камеры, снабженные дверями для въезда тележек со шлаковыми и сталеразливочными ковшами и крана для загрузки шихты. Ка мера оборудована системой отсоса газов, которые затем поступают в газо очистку. Кроме того, камера существенно снижает уровень шума в цехе, особенно сильного в период расплавления при горении электрических дуг.
§ 3. Перспективы развития конструкции дуговых электропечей
Современные дуговые электропечи представляют собой высоко мощные крупнотоннажные агрегаты с удельной мощностью 500—700 кВ-А/т. Устойчивая высокая производительность сверх мощных печей обеспечивается минимально возможной продол жительностью плавки, сокращением технологических простоев и выносом операций по доводке металла в установки внепечной обработки. Расчеты показывают, что сокращение цикла плавки в 100-т сверхмощной печи на 1 мин уменьшаются производст венные затраты на 0,06—0,10 руб/т стали. Наиболее перспек тивным является создание рафинирующих комплексов для полу чения широкого сортамента сталей из стандартного полупро дукта, выплавляемого в дуговых печах. Эти комплексы должны обеспечить обработку металла вакуумом, инертными и активными газами, рафинирующими шлаковыми смесями и порошкообразными реагентами, доводку металла по химиче скому составу и температуре. Сочетание высокомощной, дуговой печи с рафинирующим комплексом позволит увеличить произ водство стали на 30—50 %, снизить удельный расход электро энергии на 20—40 кВт*ч/т, сократить потребление легирующих •раскислителей и других материалов. Что касается самих сверх мощных печей, то в них следует применять высококачественные электроды, в том числе водоохлаждаемые. По данным зарубеж ной практики, применение составных водоохлаждаемых элек тродов обеспечивает снижение их расхода на 20—30 %. Учиты вая, что эксплуатационные расходы на электроды составляют 5—15 % себестоимости стали, это должно привести к значи тельной экономии.
Эффективность плавки возрастает также за счет примене ния водоохлаждаемой футеровки и утилизации тепла охлаж дающей воды, применения замкнутого цикла охлаждения. Не менее эффективным является использование тепла отходящих газов для подогрева шихтовых материалов перед завалкой в печь.
Перспективными в конструктивном отношении, по-видимому, будут водо
охлаждаемые пени в стационарном варианте без наклона на слив с выпуском металла через днище. Подобные печи работают в СССР и за рубежом. Такие печи менее металлоемки, имеют ряд упрощенных механических узлов и токо-
Рнс. VI.6. Схема устройства одноэлектродной дуговой электропечи постоянного тока
подводов, что приводит к снижению стоимости агрегатов. Стационарные печи
имеют преимущества в части увеличения площади водоохлаждения стен и увеличения энергетического потенциала охлаждающей воды за счет повыше ния давления в системе охлаждения при подключении печи к системе воды
высокого давления через жесткие трубопроводы. Выпуск через подину позво ляет предотвратить его излишнее окисление и снизить температуру металла, что соответственно приведет к экономии электроэнергии. Одним из перспек тивных направлений Bi развитии электропечей является применение постоян ного тока. Такого рода печи вместимостью до 50-т успешно эксплуатируются
на ряде зарубежных заводов.
На рис. VI.6 представлена схема устройства 12-т дуговой электропечи постоянного тока. Печь имеет один графитовый электрод диаметром 250 мм, установленный в центре свода и включенный в цепь питания в качестве катода. Дуга горит между электродом и шихтой или расплавом, являющихся ано дом. Расплав контактирует с подовым электродом, который вы полнен в виде нескольких металлических штырей, проходящих сквозь набивную магнезитовую футеровку и подсоединенных к токоподводящей шине. Выступающие за пределы кожуха печи контактные штыри и токоподводящая шина охлаждаются воз духом с помощью вентиляторов. По мере износа футеровки пода происходит оплавление штырей, и они всегда располагаются заподлицо с поверхностью подины. При эксплуатации в печи всегда оставляют некоторое количество жидкой стали с тем, чтобы при последующей завалке обеспечить надежный контакт шихты и подового электрода. Печь имеет донное выпускное от верстие, эксцентрично расположенное в подине ближе к рабо-
©
Рис. VI.7. Схема устройства трехэлектродной дуговой электропечи постоянного тока
чему окну. Питание печи обеспечивается от тиристорного пре образователя.
Конструкция 6-т дуговой электропечи постоянного тока с тремя электродами представлена на рис. VI.7. Электропечи постоянного тока имеют ряд преимуществ по сравнению с пе чами, работающими на трехфазном переменном токе. Они явля ются более чистыми в экологическом отношении агрегатами, отмечено снижение уровня шума на 5—10 дБ по сравнению с дуговыми печами переменного тока. Достигается снижение удельного расхода электродов до 1,5 кг/т при незначительном повышении расхода электроэнергии за счет увеличения потерь в схеме питания (снижаются потери в короткой цепи). Воз можно использование нерасходуемых электродов с созданием потока плазмы при продувке дуг аргоном. Это позволяет сни зить необходимую мощность на единицу площади пода с 2,1 до 1,6 МВт/м2.
Глав а 2. ТЕХНОЛОГИЯ ВЫПЛАВКИ СТАЛИ
ВОСНОВНЫХ ДУГОВЫХ ПЕЧАХ
§1. Шихтовые материалы электроплавки
Для производства стали в электропечах используют стальной лом, легированные металлоотходы, металлизованные окатыши, губчатое железо, передельный чугун, шлакообразующие, на углероживающие материалы, легирующие добавки и раскислители.
Нелегированный (углеродистый) лом не должен быть за грязнен никелем, медью и мышьяком. Содержание фосфора в ломе не должно быть выше 0,05 %. Он не должен быть сильно
окисленным, замусорен и загрязнен. Желательно |
сортировать |
и хранить отдельно мелкий, средний и крупный |
лом. Жела |
тельно иметь лом тяжеловесный, чтобы обеспечить загрузку шихты в один прием. Отходы легированных сталей сортируются по группам. По степени легковесности и характеру отдельных кусков его разделяют на брикеты, стружку и обсечку. При на личии смешанных и чрезмерно легковесных отходов производят предварительный переплав их на шихтовую болванку опреде ленного химического состава, которая также используется в шихту электропечей. В ряде случаев используют предвари тельно выплавленную заготовку, которая представляет собой низкоуглеродную сталь с ограниченным содержанием углерода, фосфора и серы, полученную из свежей шихты. Ее применение вследствие более высокой цены повышает себестоимость стали.
Металлизованные окатыши и губчатое железо довольно ши роко используют в качестве основного шихтового материала, как заменитель стального лома. Они содержат 85—93 % Fe и очень малое количество серы, фосфора, никеля, меди и других примесей, обычно присутствующих в стальном ломе. Это поз воляет выплавлять высококачественную сталь повышенной ча стоты.
Чугун применяют в качестве науглероживающего материала. Он должен содержать мало фосфора и серы (<0,03 %).
Для формирования шлака необходимого состава и жидкоподвижности применяют шлакообразующие— известняк, свежеобожженную известь, плавиковый шпат, шамотный бой и пе сок. Известняк используют в дробленом и прокаленном виде. Содержание СаСОз в известняке должно быть не менее 97 %, а серы не выше 0,05 % •
Известь применяют только свежеобожженной, она должна содержать >90 % СаО и минимальные количества S1O2, AI2O3, Fe203, MgO и серы (не более 0,10 %). Плавиковый шпат слу жит для регулирования вязкости шлака, он должен содержать 85—95 % CaF2, частично плавиковый шпат заменяют шамотным боем (60 % Si02, 35 % А120 3).
Для ускорения окислительных реакций в печь вводят окис лители— железную руду и газообразный кислород. Железная руда должна быть кусковатой и иметь высокое содержание оксидов железа, низкое кремнезема (<8 %) и фосфора (<0,2 %). Газообразный кислород, применяющийся в послед ние голы во все увеличивающихся масштабах, должен содер жать не менее 99,5 % Ог и не более 1 г на м3 влаги. В качестве окислителей используют также прокатную окалину, сырые ока тыши и агломерат. Раскислители и легирующие добавки вводят