
книги / Моделирование контактных явлений при абразивном глобоидном зубохонинговании
..pdf
как принято называть, угол давления. Винтовая поверхность детали в системе координат задана уравнениями (3) в соответствии с рис. 2:
Xд = R cos(δд +ϕ); |
|
Yд = R sin (δд +ϕ); |
(3) |
Zд = Pϕ,
где ϕ – угол поворота системы координат, жестко связанной с тор-
цевым профилем ротора; Р – винтовой параметр, Р = 2tπ, t – шаг
винтовой линии.
Профиль инструмента связан с системой координат X гYгZг в соответствии с рис. 3.
Рис. 3. Схема расположения осей координат глобоидного зацепления
11
Переход из системы координат XдYдZд в систему X гYгYг выполняется с помощью следующих уравнений:
Xг = cosϕг (Xд cosϕд −Yд sin ϕд − A) + |
|
+ sin ϕг (Xд cos γsin ϕд +Yд cos γcosϕд − Zд sin γ); |
|
Yг = −sin ϕг (Xд cosϕд −Yд sin ϕд − A) + |
(4) |
+cosϕг (Xд cos γsin ϕд +Yд cos γcosϕд − Zд sin γ); Zг = Xд sin γsin ϕд +Yд sin γcosϕд + Zд cos γ,
где ϕг – угол поворота глобоидного инструмента; ϕд – соответствующий угол поворота ротора; А – межосевое расстояние; γ – угол скрещивания осей ротора и глобоидного инструмента.
Подставляя в формулы (4) значения XдYдZд из уравнений (3),
получим уравнения (5) винтовой поверхности в системе координат
X гYгYг:
Xг = cosϕг (U cos τ+V sin τ− A) + |
|
+ sin ϕг (U sin τcos γ −V cosτcos γ + Pϕsin γ); |
|
Yг =sin ϕг (U cos τ+V sin τ− A) + |
(5) |
+cosϕг (U sin τcos γ −V cos τcos γ + Pϕsin γ); Zг =U sin τsin γ −V cosτsin γ − Pϕcos γ,
где U = Rд cosξд; V = Rд sin ξд; τ = ϕд +δд +ϕ+ξд; τ – угловой па-
раметр торцевого профиля детали.
Полученная система уравнений позволяет описать боковую поверхность витков глобоидного червяка.
1.3. Расчет профиля детали при известном профиле глобоидного инструмента (обратная задача профилирования)
Решение обратной задачи чрезвычайно важно для определения точности формы детали. В нашем случае это позволит установить
12
аналитическую зависимость поверхности глобоидного червяка от поверхности детали.
После преобразования координат из системы X гYгYг в систему XдYдZд , определения линии контакта профиль детали в расчет-
ном торцевом сечении выражается уравнениями (6) в соответствии с рис. 2:
Xд =U cos(τ−ϕд ) +V sin (τ−ϕд ); |
|
Yд =U sin (τ−ϕд ) −V cos(τ−ϕд ); |
(6) |
Zд = −Pϕ.
1.4.Математическое описание взаимного пересечения профилей детали и глобоидного инструмента
в зависимости от параметров установки инструмента
Положение глобоидного инструмента относительно выбранных осей координат обрабатываемой детали полностью определяется тремя параметрами: А – межосевым расстоянием, γ – углом скрещивания осей и осевым расположением глобоидного инструмента Z.
Отклонения установки и взаимной ориентации инструмента относительно детали можно свести к отклонениям от принятых параметров установки глобоидного инструмента ±∆A, ±∆γ, ±∆Z
(см. рис. 3).
Отклонение параметров установки глобоидного инструмента изменяет взаимное расположение профилей детали и инструмента, а так как процесс связан со снятием стружки, то изменение характера зацепления профилей приводит к изменению профиля обрабатываемой детали.
Направление и величину отклонений профиля зубчатой детали определяют по отклонениям расчетного профиля от теоретического. Определение расчетного профиля в зависимости от параметров установки глобоидного инструмента выполняют на основе аналитиче-
13

ских зависимостей, полученных при решении обратной задачи с учетом выбранных отклонений.
Уравнения (7) позволяют определить координаты измененного профиля детали как при изменении одного из параметров установки, так и при изменении нескольких параметров, действующих одновременно:
Xд′ = cos(ϕд ± ∆ϕд ) (U cos τ+V sin τ) +
+ cos(±∆γ)sin (ϕд ± ∆ϕд ) (U sin τ−V cos τ) ± |
|
|
± ∆Zг sin(±∆γ)sin (ϕд ± ∆ϕд ) ± |
|
|
± ∆Acos(ϕд ± ∆ϕд ) + Pϕsin(±∆γ)sin (ϕд ± ∆ϕд ); |
|
|
Yд′ = −sin (ϕд ± ∆ϕд ) (U cos τ+V sin τ) + |
(7) |
|
+ cos(±∆γ)cos(ϕд ± ∆ϕд ) (U sin τ−V cos τ) ± |
||
|
||
± ∆Zг sin(±∆γ)sin (ϕд ± ∆ϕд ) − |
|
|
−(±∆A)sin (ϕд ± ∆ϕд ) + Pϕsin(±∆γ)cos(ϕд ± ∆ϕд ); |
|
|
Zд′ = −Pϕcos(±∆γ) +U sin τsin (±∆γ) −V cos τsin (±∆γ) + |
|
|
+(±∆Zг )cos(γ ± ∆γ). |
|
Дать количественную оценку отклонений действительного профиля от теоретического по нормали к теоретическому профилю можно в соответствии с рис. 4, где сплошная линия соответствует смещенному профилю глобоидного инструмента, а штриховая линия – теоретическому профилю.
Отклонения профиля ротора определяются по нормали, проведенной из расчетных точек к теоретическому профилю с помощью уравнения
Xд′ − Xд |
|
∆n = sin(ξд −δд ), |
(8) |
где ∆n – отклонение профиля; Хд – абсцисса точки измененного профиля; Хд′ – абсцисса точки теоретического профиля; ∆n > 0, ес-
14
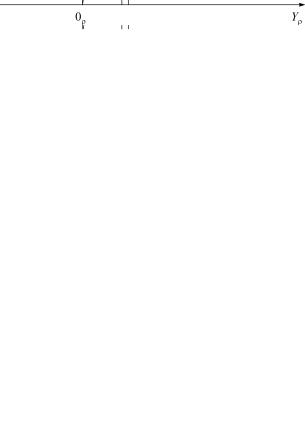
ли отклонения вне «тела» детали, и ∆n < 0, если отклонения в «тело» детали.
Рис. 4. Схема к расчету отклонений профиля ротора винтового забойного двигателя при изменении параметров установки глобоидного инструмента
Координаты Xд и Yд теоретического профиля, выраженные в функции ξд, находят с помощью трансцендентного уравнения нормали, опущенной из соответствующей известной точки фактического профиля на искомую точку теоретического профиля:
15

F∆ = X д − X д′ −(Yд′ −Yд )tg ξд, |
(9) |
где F∆ – величина, характеризующая сходимость трансцендентного уравнения; Xд′, Yд′ – декартовы координаты точек фактического
профиля.
Совместное решение систем уравнений (7–9) позволяет определить количественную оценку отклонений профиля детали при изменении параметров установки инструмента.
При заданных направлениях вращения детали и глобоидного червячного инструмента (рис. 5) и правом направлении винтовой линии глобоидного червяка каждый зуб детали вступает в зацепление с глобоидным червячным инструментом в положении 1 и выходит из зацепления в положении 7.
Рис. 5. Схема определения последовательности расчета профиля ротора винтового забойного двигателя
Взаимодействие профилей в зоне зацепления может быть определено в любом промежуточном сечении, которое может быть задано углом поворота зуба относительно расчетного положения ϕд.
Для примера построим профилограмму, показывающую максимальную величину отклонения расчетного профиля от теоретического при прохождении зуба через все сечения, определяемые углом поворота детали:
16
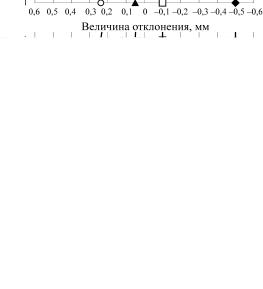
ϕд = –0,698 132; –0,523 599; –0,261 799; 0; 0,261 799; 0,523 599;
0,698 132.
На рис. 6 показана профилограмма, отражающая следующий вариант установки глобоидного хона относительно заготовки:
∆А= −0,5; −0,1; 0,1; 0,5; ∆Z = 0; ∆γ = 0.
Рис. 6. Профилограмма расчетных отклонений левой стороны профиля ротора (dZ = 0; dG = 0): ♦ – dA = –0,5; □ – dA = –0,1; ▲ – dA = 0,1; | – dA = 0,5
Анализируя профилограмму, можно увидеть, что при изменении межосевого расстояния ∆A в минус (в тело детали) происходит отклонение расчетного профиля от теоретического в тело ротора, что характеризуется снятием стружки. При изменении межосевого расстояния ∆A в плюс наблюдается отклонение снятия материала детали.
17
Глава 2. РАСЧЕТ НАПРЯЖЕННО-ДЕФОРМИРОВАННОГО СОСТОЯНИЯ В ЗОНЕ КОНТАКТА ГЛОБОИДНОГО ИНСТРУМЕНТА И РОТОРА ВИНТОВОГО ЗАБОЙНОГО ДВИГАТЕЛЯ
2.1. Математическая зависимость изменения напряженнодеформированного состояния профиля глобоидного червяка от изменения параметров технологических наладок
и физико-механических характеристик глобоидного хона
При взаимодействии абразивного инструмента и ротора винтового забойного двигателя происходит передача усилий от инструмента к заготовке путем непосредственного их контакта. При этом
вконтактирующих деталях возникают местные деформации и напряжения, называемые контактными. Несмотря на то, что в большинстве случаев контактные напряжения, возникающие в деталях машин, весьма высоки (зачастую значительно выше предела текучести материала детали), они не влияют на общую прочность деталей. Это объясняется тем, что контактные напряжения и деформации имеют резко выраженный местный характер, быстро уменьшаясь по мере удаления от зоны контакта.
При решении задачи определения контактных напряжений и деформаций пользуются некоторыми допущениями. При теоретическом решении этой задачи рассматривают два тела, ограниченных криволинейными поверхностями и нагруженных силами, прижимающими эти тела друг к другу. При отсутствии нагрузки соприкосновение тел происходит по линии. Нагрузка, нормальная к поверхности контакта, вызывает местные деформации контактирующих тел, в результате которых начальный линейный контакт переходит
вконтакт по некоторой малой площадке, имеющей сложную форму. Давление, передаваемое от одной детали к другой, распределено по контактной площадке неравномерно.
18
Вдоль линии контакта напряжения и деформации зависят от параметров установки инструмента и угла поворота детали. Они влияют на величину внедрения материала, а как следствие, и на величину контактной площадки, которая определяет величину напряжений и деформаций для данных тел в зависимости от их физикомеханических свойств. Перпендикулярно линии контакта напряжения распределяются в виде параболы, и свое максимальное значение имеют в середине контактной площадки.
Решение задачи базируется на следующих предпосылках:
–материалы контактирующих тел однородны и изотропны;
–величины сил, приложенных к соприкасающимся телам, таковы, что процесс деформации протекает в пределах справедливости закона Гука;
–поверхность контакта весьма мала по сравнению с общей поверхностью каждого из соприкасающихся тел;
–силы давления, передаваемые через поверхность контакта от одного тела к другому, нормальны к этой поверхности.
Для оценки напряженного состояния деталей необходимо определить величины трех главных напряжений. Это объясняется двумя положениями теории напряженного состояния. Первое положение сформулировано следующим образом: напряженное состояние в точке тела задано, если известны напряжения на любых трех проходящих через нее взаимно перпендикулярных площадках. При этом среди бесчисленного множества площадок, которые можно провести через исследуемую точку, имеются три взаимно перпендикулярные площадки, касательные напряжения на которых отсутствуют, а нормальные напряжения максимальны. Эти площадки и возникающие на них нормальные напряжения называются главными (рис. 7).
Для исследования напряженного состояния профиля ротора необходимо рассматривать бесконечно малый параллелепипед в окрестности некоторой точки поверхности, как показано на рис. 7. Давление, действующее на верхнюю грань параллелепипеда, должно вызвать деформации не только в направлении оси OY, но и в направлении осей OZ и OX. Этим деформациям препятствует материал
19
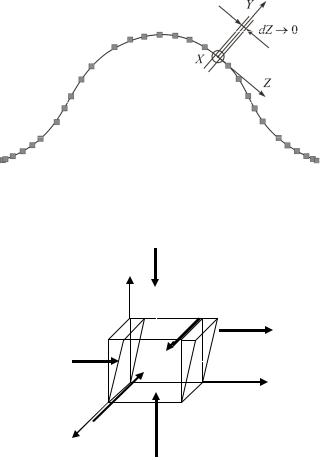
ротора, окружающий мысленно выделенный параллелепипед, и, следовательно, на его гранях, перпендикулярных осям OZ и OX, возникают напряжения сжатия. В процессе вращения глобоидного хона относительно детали за счет трения между поверхностями возникает сила, порождающая напряжения сдвига. Все эти напряжения представлены на рис. 8.
Рис. 7. Схема главных напряжений
N
Y
σy
σz
σx σx
X
Z
σz
σy
Рис. 8. Схема напряжений сдвига
20