
книги / Обогащение полезных ископаемых
..pdf
|
|
|
|
|
|
|
|
|
|
|
|
|
|
Таблица 6 |
|
Поправочные коэффициенты на условия грохочения |
|
|
|
|
|||||||||||
|
|
|
|
|
|
|
|
|
|
|
|
|
|
|
|
Показатель |
|
|
|
|
|
|
|
|
Значения |
|
|
|
|
|
|
Содержание в исходном материале |
|
|
|
|
|
|
|
|
|
|
|
|
|
|
|
зерен размером меньше половины |
0 |
|
10 |
20 |
|
30 |
40 |
50 |
60 |
70 |
|
80 |
90 |
||
размера отверстий сита, % |
|
|
|
|
|
|
|
|
|
|
|
|
|
|
|
|
|
|
|
|
|
|
|
|
|
|
|
|
|
|
|
Коэффициент k |
0,4 |
|
0,5 |
0,6 |
|
0,8 |
1,0 |
1,2 |
1,4 |
1,6 |
|
1,8 |
2,0 |
||
Содержание в исходном материале |
|
|
|
|
|
|
|
|
|
|
|
|
|
|
|
зерен размером больше размера |
10 |
|
20 |
25 |
|
30 |
40 |
50 |
60 |
70 |
|
80 |
90 |
||
отверстий сита, % |
|
|
|
|
|
|
|
|
|
|
|
|
|
|
|
|
|
|
|
|
|
|
|
|
|
|
|
|
|
|
|
Коэффициент l |
0,94 |
0,97 |
1,00 |
|
1,03 |
1,09 |
1,18 |
1,32 |
1,55 |
|
2,00 |
3,36 |
|||
Эффективность грохочения, % |
40 |
|
50 |
60 |
|
70 |
80 |
90 |
92 |
94 |
|
– |
– |
||
Коэффициент m |
2,3 |
|
2,1 |
1,9 |
|
1,65 |
1,35 |
1,0 |
0,9 |
0,8 |
|
– |
– |
||
Форма зерен |
Дробленый материал разный (кроме угля) |
Округленная (напри- |
Уголь |
||||||||||||
мер, морская галька) |
(любая) |
||||||||||||||
|
|
|
|
|
|
|
|
|
|
|
|
1,25 |
|
|
|
Коэффициент n |
|
|
|
|
1,0 |
|
|
|
|
|
|
|
|
1,5 |
|
|
|
|
|
|
|
|
|
|
|
|
Для отверстий сита |
|
|||
|
Для отверстий сита меньше 25 мм |
больше |
|||||||||||||
Влажность материала |
|
25 мм |
|
||||||||||||
|
|
|
|
|
|
|
|
|
|
|
|
||||
|
|
|
|
|
|
|
|
||||||||
|
Сухой |
|
|
Влажный |
|
Комкующийся |
В зависимости от влажности |
||||||||
Коэффициент o |
1,0 |
|
|
0,75–0,85 |
|
|
0,2–0,6 |
|
0,9–1,0 |
|
|||||
|
Для отверстий сита меньше 25 мм |
Для отверстий сита больше |
|||||||||||||
Грохочение сухое и мокрое |
|
25 мм |
|
||||||||||||
|
|
|
|
|
|
|
|
|
|
|
|
||||
|
|
|
|
|
|
|
|
||||||||
|
Сухое |
|
|
Мокрое с орошением |
|
Любое |
|
||||||||
Коэффициент p |
1,0 |
|
|
|
|
|
1,25–1,40 |
|
|
|
1,0 |
|
101
101

Для определения поправочных коэффициентов k, l необходимо знать соответственно содержание в исходном материале зерен размером меньше половины размера отверстий сита, содержание в исходном материале зерен размером больше размера отверстий сита. Указанные величины определяются по характеристикам крупности исходного материала.
Для определения поправочного коэффициента m необходимо знать эффективность грохочения. Эффективность E (%) грохочения в первом приближении можно принять в зависимости от содержания
1 d % подрешетного продукта в исходном:
1 d 40 %, E 60...70 %;
1 d 40...70 %, E 70...80 %;1 d 70...80 %, E 80...95 %;
1 d 80 %, E 95 %.
Содержание 1 d % подрешетного продукта в исходном опре-
деляется по характеристике крупности исходного материала. Производительность дробилок определяется обычно по данным
каталогов, паспортов машиностроительных заводов или ГОСТов. Каталожные производительности в какой-то мере усредняют достигнутые в практике результаты. Производительности щековых и конусных дробилок крупного дробления по каталогу приведены в табл. 2 и 3.
Объемная производительность щековой дробилки QV (м3/ч) для промежуточных размеров выходной щели находят прямолинейной интерполяцией по формуле
QV Qmax Qmax Qmin imax i
imax imin
или
QV Qmin Qmax Qmin i imin ,
imax imin
102
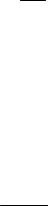
где Qmax и Qmin – максимальная и минимальная производительности дробилки выбранного размера по каталогу, м3/ч; imax и imin – максимальная и минимальная ширина выходной щели дробилки, мм.
Объемная производительность конусной дробилки QV (м3/ч) принимается по данным табл. 3.
Массоваяпроизводительностьдробилкиопределяетсяпоформуле
Qm QV н,
где ρн – насыпная плотность дробимого материала, т/м3.
В каталогах производительность дробилки обычно указывается для пород со средними характеристиками насыпной плотности, крепости и т.д. Поэтому расчетная массовая производительность дробилки Qmp (т/ч) определяется по формуле
Qmр Qm k k f kwkкр,
где Qm – массовая производительность дробилки, т/ч; kρ, kf, kw, kкр – поправочный коэффициент соответственно на насыпную плотность, крепость руды, влажность руды, крупность руды.
Поправочный коэффициент на насыпную плотность определяется по формуле
k н ,
н.ср
где ρн – насыпная плотность дробимого материала, т/м3;н.ср 1,6 т/м3 – насыпная плотность типовой (средней) руды.
Поправочные коэффициенты на условия дробления kf, kw, kкр определяются по табл. 7.
Для определения поправочного коэффициента kкр необходимо знать содержания β30,5B (%) крупных классов (крупнее 0,5B ) в питании:
β 0,5B
β30,5B 1 1β1 d E 100 %,
103
104
|
|
|
|
|
|
|
|
|
|
|
|
|
|
|
|
|
Таблица 7 |
|
|
Поправочные коэффициенты на условия дробления |
|
|
|
|
|
|
|||||||||||
|
|
|
|
|
|
|
|
|
|
|
|
|
|
|
|
|
|
|
|
|
|
|
Руда сред- |
|
|
|
|
|
|
|
|
|
|
|
|
|
|
Коэффициент |
Руда мягкая |
ней твер- |
Руда твердая |
|
Руда весьма твердая (особо крепкая) |
|||||||||||||
(некрепкая) |
дости |
(крепкая) |
|
|||||||||||||||
|
(средней |
|
|
|
|
|
|
|
|
|
|
|
||||||
|
|
|
|
|
|
|
|
|
|
|
|
|
|
|
|
|
|
|
|
|
|
|
крепости) |
|
|
|
|
|
|
|
|
|
|
|
|
|
|
Крепость пород по |
|
|
|
|
|
|
|
|
|
|
|
|
|
|
|
|
|
|
шкале М.М. Прото- |
|
5–10 |
11–15 |
16–18 |
|
|
|
|
|
|
19–20 |
|
|
|
|
|||
дьяконова f |
|
|
|
|
|
|
|
|
|
|
|
|
|
|
|
|
|
|
|
|
|
|
|
|
|
|
|
|
|
|
|
|
|
|
|
|
|
Поправочный |
|
1,2 |
1,0 |
0,95 |
|
|
|
|
|
|
0,90 |
|
|
|
|
|||
на крепость kf |
|
|
|
|
|
|
|
|
|
|
|
|||||||
|
|
|
|
|
|
|
|
|
|
|
|
|
|
|
|
|
|
|
Поправочный |
|
|
|
|
Влажность руды W, % |
|
|
|
|
|
|
|
|
|||||
на влажность kw |
4 |
|
5 |
6 |
7 |
|
8 |
|
|
|
9 |
10 |
|
|
11 |
|||
1 |
|
1 |
0,95 |
0,9 |
|
0,85 |
|
|
0,8 |
0,75 |
|
|
0,65 |
|||||
|
|
|
|
|
|
|
||||||||||||
Поправочный |
|
|
Содержание крупных классов (крупнее 0,5В) в питании β 0,5B , % |
|
|
|||||||||||||
|
|
|
|
|
|
|
|
|
|
|
|
3 |
|
|
|
|
||
|
|
|
|
|
|
|
|
|
|
|
|
|
|
|
|
|
||
на крупность kкр |
5 |
|
10 |
20 |
25 |
30 |
|
40 |
|
50 |
|
60 |
70 |
|
80 |
|||
1,10 |
|
1,08 |
1,05 |
1,04 |
1,03 |
|
1,0 |
|
0,97 |
|
0,95 |
0,92 |
|
0,89 |
||||
|
|
|
|
|
|
104

где β1 0,5 B – содержание класса 0,5B в исходном материале, определяется по характеристике крупности исходного материала, доли ед.; 1 d – содержание класса –d в исходном материале, определяется
по характеристике крупности исходного материала, доли ед.; E – эффективность грохочения, доли ед.; B – ширина приемного отверстия дробилки, мм; d – размер отверстия сита грохота, мм.
По полученной производительности дробилки выбранного типоразмера определяется требуемое количество дробилок Nдр (шт.):
Nдр Q3 , Qmр
где Q3 – количество верхнего продукта грохота, т/ч; Qmр – массовая
производительность дробилки, т/ч.
Количество верхнего продукта определяется по формуле
Q3 Q1 1 1 d E ,
где Q1 – количество исходного материала, т/ч; 1 d – содержание
класса –d в исходном материале, определяется по характеристике крупности исходного материала, доли ед.; E – эффективность грохочения, доли ед.; d – размер отверстия сита грохота, мм.
Коэффициент загрузки дробилки определяется по формуле
kз |
Q3 |
, |
|
NдрQmр |
|||
|
|
где Q3 – количество верхнего продукта грохота, т/ч; Nдр – требуемое количество дробилок, шт.; Qmр – массовая производительность
дробилки, т/ч.
Результаты выполненных расчетов необходимо свести в табл. 8. По данным табл. 8 произвести окончательный выбор дробилки и грохота. При этом необходимо учесть, что при отсутствии явного преимущества щековых дробилок относительно конусных в рас-
105
сматриваемом варианте, при прочих равных условиях, выбор рекомендуется делать в пользу конусных дробилок ввиду более благоприятных условий их эксплуатации.
|
|
|
|
|
|
|
Таблица 8 |
|
|
Результаты расчета стадии дробления |
|||||||
|
|
с предварительным грохочением |
||||||
|
|
|
|
|
|
|
|
|
Номер |
d, мм |
E, % |
F, |
Тип |
i, мм |
Qmp, т/ч |
Nдр, шт. |
kз |
варианта |
м2 |
дробилки |
||||||
1 |
|
|
|
|
|
|
|
|
2 |
|
|
|
|
|
|
|
|
… |
|
|
|
|
|
|
|
|
n |
|
|
|
|
|
|
|
|
Определение гранулометрического состава дробленого про-
дукта 5 выполняется на основе гранулометрического состава (характеристик крупности) исходного материала и гранулометрического состава (характеристик крупности) продукта дробления 4.
Спомощью типовых характеристик крупности (рис. 33) необходимо построить характеристики крупности продукта дробления 4. На рис. 33 по оси абсцисс отложена крупность кусков в долях максимальной ширины разгрузочного отверстия, а по оси ординат – суммарный выход классов по «плюсу».
Спомощью характеристики крупности исходного материала 1
ихарактеристики крупности продукта дробления 4 строится характеристика крупности дробленого продукта 5. Для этого необходимо
наметить не менее 5–7 значений крупности di (мм), по которым будет рассчитан состав продукта 5.
Искомое содержание 5 di (%) принятых классов крупности di
(мм) в конечном дробленом продукте 5 определяется по формулам: если di i , то
d |
|
d |
i |
d |
i 100 %; |
5 |
i |
1 |
i 1 |
4 |
106

если di i, то
5 di 1 di 1 di 4 di 100 %,
где 1 di , 1 di , 1 i – содержание классов крупности di , di и i в исходном материале 1, определяются по характеристике крупности исходного материала, доли ед.; 4 di – содержание класса крупностиdi в продукте дробления 4, определяется по характеристике крупности продукта дробления 4, доли ед.
а |
б |
Рис. 33. Типовые характеристики крупности продукта дробления: а – для щековых дробилок; б – для конусных дробилок; 1 – для твердых руд; 2 – для руд средней твердости; 3 – для мягких руд
По намеченным значениям di (мм) и соответствующим значениям 5 di (%) строится суммарная характеристика крупности по
«минусу» дробленого продукта 5.
Определение эффективности стадии дробления. Эффектив-
ность Eд (%) стадии дробления определяется по формуле
E |
1 dд 1 dд |
||
5 |
1 |
100 %, |
|
|
|
||
д |
|
dд |
|
|
|
1 |
|
107
1 d |
1 d |
|
– содержание класса крупности 1 dд соответст- |
где 1 |
д , 5 |
д |
венно в исходном материале 1 и дробленом продукте 5, определяются по соответствующим характеристикам крупности, %; 1 dд – содержание класса dд в исходном материале 1, определяется по характеристике крупности исходного материала 1, %; dд – заданная
крупность дробленого продукта, мм.
Анализ эффективности стадии дробления может быть выполнен на основе сравнения суммарных выходов заданного класса в исходном материале 1 и дробленом продукте 5. Для этого предлагается
определить и сравнить суммарные выходы класса (dд 20(dд 20)) в исходном материале 1 и дробленом продукте 5.
Анализ результатов. В заключение необходимо отразить и проанализировать результаты основных этапов выполненной работы:
1)параметры грохота: размер отверстия сита грохота d (мм); расчетная рабочая площадь F (м2) сита грохота; эффективность грохочения E (%);
2)параметры дробилки: тип дробилки, расчетная массовая про-
изводительность дробилки Qmp (т/ч); количество дробилок Nдр (шт.); коэффициент загрузки дробилки kз;
3)параметры эффективности стадии дробления: эффективность
стадии дробления Eд (%); суммарные выходы класса (dд 20(dд 20)) в исходном материале 1 и дробленом продукте 5.
По результатам анализа указанных параметров, должны быть предложены пути повышения эффективности использования выбранного оборудования. В отдельных случаях целесообразно рассмотреть альтернативные варианты дробилок и грохотов.
Контрольные вопросы
1.Основные технологические свойства минералов.
2.Механические свойства полезных ископаемых, влияющих на их обогащение.
108
3.Химические свойства полезных ископаемых, влияющих на их обогащение.
4.Влияние текстурных и структурных особенностей строения полезного ископаемого на процесс обогащения.
5.Влияниемагнитных свойствминераловнапроцесс обогащения.
6.Влияние спектроскопических и радиоспектроскопических свойств минералов на процесс обогащения.
7.Показатели обогащения полезных ископаемых и их обогати-
мости.
8.Подготовкаполезныхископаемыхкпереработкеи обогащению.
9.Цели, задачи, способы усреднения сырья и продуктов обога-
щения.
10.Усреднительные бункера и склады.
11.Классификация методов и процессов обогащения.
12.Понятие технологической схемы обогащения.
13.Подготовительные обогатительные процессы.
14.Сущность процесса грохочения.
15.Гранулометрический состав полезных ископаемых.
16.Конструкции грохотов.
17.Принцип действия колосниковых, криволинейных и плоских грохотов.
18.Конструкции просеивающих поверхностей.
19.Классификация грохотов, их назначение и область применения, достоинства и недостатки.
20.Понятия «эффективность» и «производительность» процесса грохочения. От чего зависит производительность, эффективность грохочения?
21.Понятие «класс крупности». Определение гранулометрического состава материала.
22.Характеритсики крупности, способы их построения, свойства. Определение выхода класса по характеристике крупности.
23.Сущность процесса классификации полезных ископаемых.
24.Гидравлическая классификация в восходящем потоке воды,
вгоризонтальном потоке пульпы.
109
25.Принцип действия и область применения гидравлического камерного классификатора.
26.Принцип действия и область применения механического спирального классификатора.
27.Принцип действия и область применения гидроциклона.
28.Сущность процесса дробления.
29.Способы дробления полезных ископаемых.
30.Классификация дробилок, их назначение и область применения, достоинства и недостатки.
31.Принцип действия, достоинства и недостатки щековых дро-
билок.
32.Принцип действия, достоинства и недостатки конусных дробилок.
33.Принцип действия, достоинства и недостатки валковых дробилок.
34.Принцип действия, достоинства и недостатки молотковых дробилок.
35.Принцип действия, достоинства и недостатки роторных дробилок.
36.Схемы дробления: с предварительным грохочением, с поверочным грохочением, с предварительным и поверочным грохочением. Их достоинства и недостатки, область применения.
37.Понятия «эффективность» и «производительность» процесса дробления. От чего зависит производительность, эффективность дробления?
38.Выбор и расчет дробилок и грохотов для обеспечения дробления заданного материала с предварительным грохочением.
39.Построение суммарных характеристик крупности продуктов для различных этапов дробления с предварительным грохочением.
40.Анализ результатов расчета основных параметров дробления с предварительным грохочением.
41.Сущность процесса измельчения.
42.Классификация измельчительных машин.
43.Принцип действия, достоинства и недостатки барабанной мельницы.
110