
книги / Современные подходы к технологии электроэрозионной обработки материалов
..pdf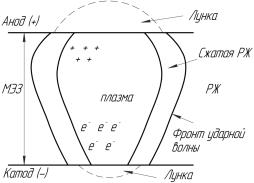
и ионизирует тонкий слой окружающей жидкости, идущей на увеличение массы плазмы. Радиус канала плазмы увеличивается со временем из-за высокого внутреннего давления в канале и преобразования окружающего диэлектрика в плазму. На это преобразование уходит 70–74 % общей энергии.
Рис. 1.2. Плазменный канал
Процесс образования стримера зависит от множества факторов: свойств РЖ, степени загрязнения РЖ продуктами эрозии, материала электродов и др.
После прохождения импульса тока напряжение между электродами отсутствует, происходит деионизация РЖ, т.е. нейтрализация заряженных частиц. Пространство между электродами подготавливается для нового прохождения очередного заряда. Вновь приложенное к электродам напряжение создает предпосылку к образованию следующего разряда электрического импульса, т.е. повторяется процесс образования стримера. Совокупность электрических разрядов проходящих от ЭИ к ЭД с определенной частотой их следования и реализует процесс ЭЭО. Процессы, протекающие в канале разряда, представлены на рис. 1.3 [6].
Количество тепловой энергии, которая выделяется на электродах, неодинаково, так же как и количество снимаемого материала с поверхностей ЭИ и ЭД. Данное неравновесие зависит от множества факторов: теплофизических свойств материалов ЭИ и ЭД, парамет-
11

ров рабочих импульсов, а также полярности рабочих импульсов. Было установлено [7], что при помощи варьирования этими факторами можно увеличивать или уменьшать эрозию электродов.
Эрозия ЭИ является нежелательным явлением в ходе ЭЭ-обра- ботки. Это связано с тем, что искажение формы электрода-инстру- мента будет оказывать негативное влияние на точность ЭЭО и шероховатость обработанной поверхности.
Рис. 1.3. Взаимосвязь физико-химических процессов при ЭЭО
При электроэрозионной обработке стремятся создать условия, при которых износ ЭИ был бы незначителен. Одним из способов уменьшения величины износа ЭИ является применение униполярных импульсов.
Использование униполярных импульсов позволяет осуществлять процесс избирательной электрической эрозии одного из электродов [6]. Если при этом оба электрода изготовлены из одного и того же материала, то при малой продолжительности импульсов преобладает эрозия электрода, имеющего положительную полярность (анода), а при импульсах большой длительности преобладает эрозия электрода, имеющего отрицательную полярность (катода). Разделение им-
12
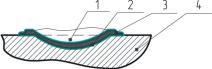
пульсов на импульсы малой и большой длительности является условным. Превышение эрозии одного электрода над другим принято называть в ЭЭО полярным эффектом.
Полярный эффект достигает наибольшего значения при использовании униполярных импульсов значительной длительности и небольшой энергии. Если обрабатываемая заготовка подключена к положительному полюсу ГИ, а ЭИ – к отрицательному, то такое включение электродов называется включением на прямую полярность. Если ЭИ подключен к положительному полюсу ГИ, а обрабатываемая заготовка – к отрицательному, то такое включение электродов называется включением на обратную полярность.
1.3. Сведения о единичной лунке
Под единичной лункой (лунка) понимается след на обрабатываемой поверхности, полученный в результате воздействия одного электрического разряда (рис. 1.4) [9].
Рис. 1.4. Лунка, образовавшаяся на обрабатываемой поверхности под воздействием единичного разряда: 1 – выплавленный металл; 2 – белый слой; 3 – валик вокруг лунки; 4 – обрабатываемая деталь
В работе [10] говорится, что энергия импульса тока, распределяясь между анодом, катодом и столбом разряда, выделяется в течение весьма короткого времени (10–6...10–7 с) при высоких плотностях. В результате этого происходит удаление металла с обрабатываемой поверхности, изменение структуры и свойств поверхностного слоя, образование внутренних напряжений и другие физические явления.
Энергию импульса можно рассчитать по формуле [8]
Wи = ∫0tиU I dtи,
13

где Wи – энергия импульса, Дж; I – сила тока, А; U – напряжение, подаваемое на электроды, В; tи – длительность импульсов (в зару-
бежной литературе обозначается ton), с.
Установлено [3, 5, 10], что в течение импульса металл с электродаинструмента и электрода-детали удаляется в основном в жидком и газообразном состояниях. Как было отмечено в подразд. 1.2, рабочая жидкость, окружающая канал разряда, испаряется, образуя газовую полость. В начальный момент скорость движения границ газовой полости (см. рис. 1.2 – фронт ударной волны) достигает 200 м/с, а давление
вполости – сотен атмосфер. В результате обрабатываемый материал испытывает значительное механическое давление. После окончания импульса тока газовая полость по инерции продолжает расширяться, что наряду с конденсацией паров металла приводит к быстрому падению давления в ней, вплоть до давления ниже атмосферного. В момент, когда размеры газовой полости приближаются к набольшим, а давление
вней к наименьшему, перегретый металл, который находится в образовавшейся лунке, вскипает и выбрасывается из нее. Реактивной струей паров металла оставшийся в лунке жидкий металл выдавливается из нее и, застывая, образует окаймляющийся валик(см. рис. 1.4, 1.5).
Рис. 1.5. Лунка на поверхности ЭД при увеличении ×1000
В результате ЭЭО образуется поверхность, представляющая собой совокупность большого количества лунок. Основными характеристиками лунок являются: радиус rл, глубина hл, их соотношение К = rл / hл, атакже коэффициент перекрытия лунок β (отношение rл к расстоянию между соседними лунками L). В основном данные параметры и определяют основные показатели ЭЭ процесса, такие как производительность, шероховатостьобработанной поверхности иточность обработки.
14
Размеры лунок зависят от многих факторов, одним из которых являются физико-механические свойства обрабатываемого материала. Для оценки влияния этих свойств используется критерий фазового превращения Палатника. Данный критерий определяется как произведение основных физико-механических показателей:
П= с λ ρ Tп2 ,
где с – удельная теплоемкость материала; ρ – плотность материала; λ – коэффициент теплопроводности материала; Тп – температура плавления материала.
По данному критерию также можно судить об эрозионной стойкости того или иного материала. Чем выше значение критерия, тем выше эрозионная стойкость материала.
Физико-механические свойства сталей представлены в табл. 1.1.
|
|
|
|
|
|
|
Таблица 1 . 1 |
|
|
|
|
|
|
|
|
Параметр/ |
ρ, |
λ, |
с, |
Тп, |
о |
С |
П = с λ ρ T 2 , |
марка |
3 |
|
|
|
п |
||
материала |
кг/м |
Вт/м·К |
Дж/кг·К |
|
|
|
Дж·Вт/м4 |
40 |
7850 |
50 |
470 |
1535 |
6,03·1014 |
||
45 |
7826 |
48 |
473 |
1535 |
5,81·1014 |
||
40Х |
7850 |
41 |
466 |
1535 |
4,88·1014 |
||
5ХНВ |
7900 |
41 |
466 |
1500 |
4,78·1014 |
||
35ХГСА |
7850 |
38 |
496 |
1500 |
4,65·1014 |
||
У10 |
7810 |
40 |
469 |
1535 |
4,79·1014 |
||
У8А |
7819 |
42 |
470 |
1535 |
5,05·1014 |
||
Х12М |
7770 |
42 |
462 |
1500 |
4,90·1014 |
||
Х12Ф1 |
7770 |
30 |
482 |
1500 |
8,01·1014 |
||
5ХГСВФ |
7920 |
38 |
461 |
1500 |
4,36·1014 |
||
5ХНСВ |
7920 |
40 |
480 |
1500 |
4,78·1014 |
||
5ХНМ |
7900 |
42 |
475 |
1500 |
4,95·1014 |
||
3Х2В8Ф |
7920 |
36 |
482 |
1500 |
9,40·1014 |
||
4Х2В5ФМ |
7950 |
38 |
492 |
1500 |
4,88·1014 |
||
40ХНВА |
7850 |
20 |
495 |
1527 |
2,51·1014 |
||
Р6М5 |
7859 |
34 |
460 |
1520 |
2,84·1014 |
||
Медь М2 |
8860 |
390 |
450 |
1350 |
2,227·1015 |
||
Латунь |
8200 |
150 |
360 |
1158 |
5,979·1014 |
||
ЛС59-1 |
|
|
|
|
|
|
|
Углеграфит |
8800 |
125 |
400 |
1350 |
6,03·1014 |
||
|
|
|
|
|
|
|
15 |
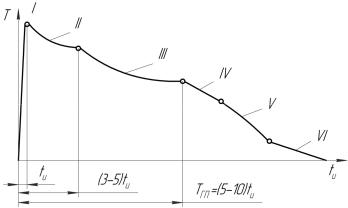
1.4. Стадии нагрева и охлаждения поверхностей электрода при электроэрозионной обработке
Исследования структуры и свойств поверхностного слоя обработанного материала после ЭЭО показали, что они близки к получаемым после термической обработки [5, 10]. Таким образом, для получения качественной поверхности после ЭЭ-обработки необходимо учитывать условиянагрева и охлаждения поверхности единичной лунки.
При нагреве поверхностного слоя в процессе ЭЭО его свойства будут определяться величиной внутренних напряжений, возникающих в результате значительной разности температур. При определенных условиях напряжения могут превышать предел прочности обрабатываемого материала, что приведет к образованию сетки микротрещин.
При охлаждении поверхностного слоя заготовки в процессе ЭЭО существенно меняются его структура и свойства. Возможности воздействия на качество поверхности при этом сравнительно широки и определяются подбором состава рабочей жидкости, а также режимами ЭЭО.
На рис. 1.6 показан характер изменения температуры поверхности лунки при воздействии на поверхность электрического импульса длительностью tи.
Рис. 1.6. Диаграмма изменения температуры поверхности лунки
16
PNRPU
Тепловой режим I (см. рис. 1.6) связан с образованием плоского мгновенного источника тепла, действующего в течение t ≤ tи. За это время происходит интенсивный нагрев поверхностных слоев электродов вплоть до их расплавления и испарения. Тепловой режим II охватывает время tи ≤ t = (3–5) tи, т.е. с момента окончания импульса тока до момента дополнительного выброса металла из лунки. В этот период поверхность лунки покрыта перегретым металлом с температурой, превышающей его температуру плавления [10].
Тепловой режим III начинается после дополнительного выброса металла из лунки и заканчивается, как можно условно считать, при t = TГП = (5–10) tи, т.е. одновременно с началом ликвидации газовой полости (ТГП – время существования газовой полости). Температура поверхности лунки близка к температуре плавления обрабатываемой заготовки. В это время еще сохраняется значительный градиент температур в поверхностном слое заготовки [10].
Ускоренный процесс охлаждения поверхности лунки (тепловой режим IV) начинается с t > ТГП, т.е. после окончания дополнительного выброса металла из лунки, и особенно в момент, когда диаметр газовой полости приближается к минимальному. В это время газовая полость постепенно уменьшается, и ее граница перемещается к центру лунки. Затем наступает момент, когда граница газовой полости, представляющая собой парожидкостную смесь, соприкоснется с периферийной частью поверхности лунки, имеющей высокую температуру. В результате часть рабочей жидкости газовой полости превращается в пар. Появление пузырьков пара приводит к пульсации размеров газовой полости [10].
Как отмечено в работе [11], учитывая специфику условий протекания процесса ЭЭО, сомнительно утверждать, что пленочное кипение жидкости в межэлектродном промежутке переходит в пузырьковое, как это имеет место при охлаждении открытых поверхностей. Также отмечалось, что с понижением температуры поверхности лунки рабочая жидкость все чаще соприкасается с ней и, испаряясь, интенсивно отводит тепло. Эта стадия охлаждения (тепловой режим V) происходит с наибольшей скоростью.
17

По мере охлаждения поверхности лунки до температуры кипения РЖ газовая полость ликвидируется, и жидкость начинает омывать всю поверхность лунки. Наступает последняя стадия охлаждения (тепловой режим VI), которая характеризуется конвективным теплообменом поверхности лунки с рабочей жидкостью, вступивших в непосредственный контакт. Скорость теплообмена в этот момент умеренная (см. рис. 1.6) и определяется в основном свойствами рабочей жидкости, величиной температурного перепада между поверхностью лунки и РЖ, а также скоростью перемещения рабочей жидкости в межэлектродном промежутке.
1.5. Шероховатость поверхности при ЭЭО
Шероховатость поверхности оказывает значительное влияние на эксплуатационные свойства деталей.
После электроэрозионной обработки поверхность ЭД имеет некую шероховатость, образованную путем большого количества взаимно пересекающихся лунок. Параметры шероховатости определяются размерами и геометрией двух групп неровностей: полученных в результате взаимного пересечения лунок и образовавшихся в результате искажения профиля лунки. Первая группа неровностей в значительной степени будет определяться размерами лунок: rл, hл, β. С использованием данных факторов становится возможным определение параметров шероховатости. Вторая группа неровностей полностью определяется случайными факторами, определение которых практически невозможно. Таким образом, реальный профиль шероховатости можно разделить на две составляющие: систематическую
ислучайную. Случайная составляющая профиля шероховатости составляет примерно 10–15 % от систематической [8].
Шероховатость зависит в первую очередь от энергии импульса
исвойств обрабатываемого материала [6]:
Rz = β2 k4 3 Wи , 3
где β – коэффициент перекрытия лунок (для максимальной шероховатости β = 1,2); k4 – постоянная величина, не зависящая от длитель-
18
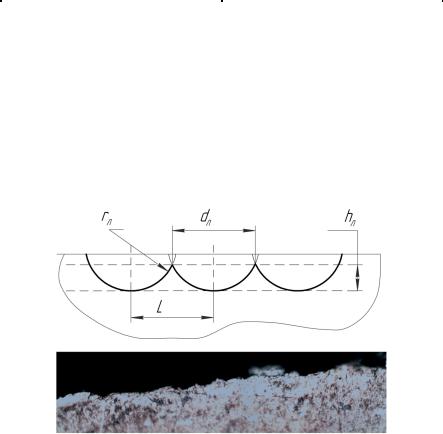
ности и энергии импульса (значения коэффициента k4 для различных материалов приведены в табл. 1.2); Wи – энергия импульса.
Чем выше электроэрозионная обрабатываемость материала, тем большую высоту микронеровностей имеет обработанная поверхность. Стоит отметить, что параметры шероховатости поверхности, обработанной электроэрозионным способом, существенно отличаются от параметров поверхностей, обработанных резанием и виброобкатыванием.
|
Таблица 1 . 2 |
|
|
Материал заготовки |
k·103, см/Дж1/3 |
Al |
12–15 |
Cu |
6–8 |
Fe |
5,5 |
Ni |
67 |
Сталь 45 |
5–6 |
ВК-6 |
1,5–2 |
ВК-15 |
2,5–3 |
На рис. 1.7 представлены общая схема формирования параметров шероховатости поверхности и реальный профиль обработанной поверхности.
Рис. 1.7. Схема формирования параметров шероховатости и реальный профиль обработанной поверхности
19
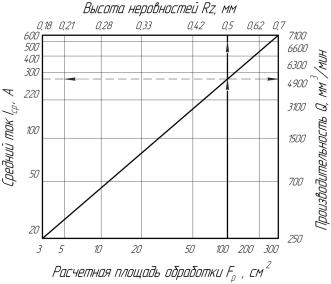
С увеличением энергии импульса Wи шероховатость обработанной поверхности возрастает. Это объясняется тем, что с увеличением Wи будет выделяться большее количество теплоты в течение одного импульса, следовательно, будет наблюдаться большее проплавление металла, что, в свою очередь, приведет к увеличению радиуса лунки rл и, как следствие, коэффициента перекрытия β. Таким образом, для получения меньших значений параметров шероховатости необходимо правильно подбирать режим обработки.
На рис. 1.8 представлена номограмма режимов и технологических характеристик при обработке стали 45 медным ЭИ на чистоте 400 имп/с (режим по току до 600 А). С использованием номограммы режим обработки выбирается следующим образом: при расчетной площади обработки Fр = 100 см2 поднимаются от точки 100 см2 нижней шкалы по вертикали до пересечения с наклонной прямой, затем по горизонтали перемещаются влево до пересечения со шкалой тока и определяют Iср = 270 А. Следуя по горизонтали, по правой шкале находим производительность Q = 4300 мм3/мин. На верхней шкале показана высота неровностей Rz, которая для рассматриваемого примера равна 0,5 мм [3].
Рис. 1.8. Номограмма режимов и технологических характеристик
20