
книги / Technologie des Kali - und Steinsalzbergbaus
..pdfBild 7/20. Sklzzo eines handbct&tlgtcn Rolloch-
Ilobolvorscklusscs
von 800 mm auffahren. Entsprechend dem Staßfurter Lagereinfallen von etwa 60° werden diese
Rollöcher |
später auf |
einen Querschnitt von |
|
1,8 X 2 m |
erweitert, |
ohne daß |
Verstopfungen |
auftreten. |
|
|
|
Im Südharzkaliwerk Bleicherode |
arbeitet nach |
einem ähnlichen Prinzip eine Großloch-Kernring- Schrämmaschine. Dieses Aggregat fräst nur einen Ring heraus, der etwa 40 mm breit ist, während der übrige Lochdurchmesser als Kern stehen bleibt und von Zeit zu Zeit durch seine Eigen masse abbricht. Der gesamte Durchmesser be trägt 1 m, nachdem vorher seitlich ein Vorbohi’r loch von unten nach oben hergestellt worden ist. Das Vorbohrloch dient der nachfolgenden Kern bohrung als Führung. Die Maschine arbeitet im Prinzip nach der im Bild 7/19 gezeigten Dar stellung und kann auf Grund ihres relativ großen Bohrlochdurchmessers für mancherlei Zwecke eingesetzt werden.
Das Herstellen der Vorbohrlöcher durch die SBM-3u oder die Kernringmaschine dient der Vorbereitung für das Aufschießen der Rollöcher auf ihren endgültigen Quer schnitt. Vorliegende Betriebsergebnisse beweisen, daß der Maschineneinsatz zur Un terstützung der Hauerarbeit beim Herstellen der Rollöcher nur dann mit wirtschaft lichem Erfolg möglich ist, wenn das Rolloch eine gewisse Mindestlänge erreicht. Beim Vergleich der verschiedenen Auffahrmethoden ergibt sich, daß die Wirtschaftlich keitsgrenze zwischen der Rollochauffahrung im reinen Handbetrieb (Bohren und Schießen) und der Maschinenauffahrung bei der Kernringschrämmaschine bei 34 m Rollochlänge, bei der SBM-3u aber schon bei 12 m Rollochlänge liegt.
Die Rollöcher müssen in der Zwischenförderung bestimmte betriebliche Bedingungen erfüllen. In Hartsalzgruben kann das Rolloch ohne Schwierigkeit als zusätzlicher Bunker benutzt werden, wenn es die entsprechenden Abmessungen erhält. In Carnallitgruben ist diese Bunkerung zu vermeiden. Rollöcher, durch die carnallitisches Rohsalz abgezogen wird, müssen unbedingt zu Schichtschluß leergefahren werden, um ein Zusammenbacken des Salzes zu vermeiden.
Längere Rollöcher sind grundsätzlich vor ihrem Austrag abzuknicken, um Verstop fungen zu verhindern. Von großer Bedeutung ist die störungsfreie Arbeitsweise des Rollochverschlusses, dessen Konstruktion von der Art der nachgeschalteten Haupt streckenfördermittel abhängig ist. Bei Förderwageneinsatz haben sich die in Bild 7/20 dargestellten Hebelverschlüsse bewährt.
Die Leistungen im Rollochbetrieb müssen der Kapazität der vorgeschalteten Abbau förderung angeglichen sein. Sie müssen aber auch ein reibungsloses und möglichst kontinuierliches Beschicken des nachgeschalteten Streckenfördermittels gewährlei sten. Bei guter Arbeitsorganisation kann ein Großrolloch ohne Schwierigkeiten Schichtförderleistungen von 1000 t und darüber erreichen. Bei derartigen Mengen muß allerdings anstelle der handbedienten RollochVerschlüsse eine Druckluftsteuerung eingesetzt werden.
Reine Ladegeräte und reine Fördergeräte haben sich in Salzgruben bisher nicht bewährt. Es muß eine Gerätekombination gefunden werden, die den Ladeund den nachfolgenden AbförderVorgang in möglichst'nur einem Arbeitsgang bewältigt. Das fast ideale Aggregat für diesen Zweck ist seit fast 30 Jahren der Schrapper. Sein schlechter Wirkungsgrad zwingt aber zu neuen Überlegungen, die in der Abbauförderung eine große Betriebskonzen tration mit einer guten Arbeitsproduktivität anstreben müssen. Diese Anforderungen kann der Schrapper nicht mehr erfüllen.
Umfangreiche Betriebsversuche mit Frässcheibenladern und Pendelwagen haben bewie sen, daß bei Gewährleistung bestimmter Betriebsverhältnisse der Einsatz derartiger lei stungsfähiger Gerätetypen die technisch-ökonomischen Kennziffern in der Ablauförderung verbessern kann.
In der Zwischenförderung ist der Rollochbetrieb zu automatisieren. Für das Auffahren der Rollöcher sind Spezialmaschinen einzusetzen.
Zur Wiederholung und Vertiefung
1.Wie arbeiten "Überkopflader? Welche Betriebspunkte können auch im Salzberg bau mit Überkopfladern ausgerüstet werden?
2.Erklären Sie das Arbeitsprinzip von Frässcheibenladern und ihre Vorund Nach teile !
3.Warum sind Wagenförderungen im Abbau unwirtschaftlich?
4.Nennen Sie die Hauptkenngrößen von Pendelwagen!
5.Zeichnen und begründen Sie ein Einsatzschema für Scheibenlader, Pendelwagen und Kratzförderer im Abbau und in der Zwischenförderung!
6.Zählen Sie die Hauptbestandteile einer kompletten Schrapperanlage auf und er läutern Sie das Arbeitsprinzip der Gesamtanlage!
7.Welche Faktoren beeinflussen die Leistungsfähigkeit einer Schrapperanlage? Be gründen Sie Ihre Aussage!
8.Erklären Sie die Arbeitsweise eines Planetengetriebes!
9.Nennen Sie die wichtigsten Sicherheitsvorschriften in der Schrapperförderung!
10.Wie werden Signale mit der Lampe gegeben?
11.Zeichnen Sie eine Förderwagen-Ladestelle bei der Schrapperförderung mit Lade bühne und Seilbahnantrieb!
12.Was versteht man unter einem „Karussellbetrieb“ ?
13.Welche Fördermenge muß ein guter Rollochbetrieb je Schicht bewältigen?
14.Auf 1000 t eff Förderung werden 73,14 m Schrapperseil verbraucht.
Wieviel m Schrapperseil sind erforderlich, wenn im Monat 394741 eff gefördert werden ?
15.Gut gefüllte Förderwagen sind Voraussetzung für einen ökonomischen Wagen einsatz.
Wie hoch ist der Förderverlust, wenn ein Schrapperfahrer 117 Wagen, die richtig gefüllt je 0,951 fassen, nur zu 4/5 ihres Wageninhalts vollschrappt?
16.Ein kompletter Schrapperhaspel in schlagwetter-geschützter Ausführung kostet 48500 DM. Durch die Abschreibung wird die durch den ständigen Einsatz hervor gerufene Wertminderung der einzelnen Maschinen verbucht. Die jährliche A b schreibung eines Schrappers beträgt 12% des Anschaffungswertes.
Welcher Betrag ist in 4 Jahren abzuschreiben?
17. Ein guter Schrapperfahrer hat durch sorgfältige Behandlung des Materials 132 m Schrapperseil eingespart. Ein laufender Meter Schrapperseil kostet 1,57 DM. Vom Gesamtbetrag der Einsparung werden dem Schrapperfahrer 13 % gutgeschrieben. Wie hoch ist demnach seine Materialeinsparungsprämie?
8, Die Streckenförderang
Die Hauptstreckenförderung hat die Aufgabe, das gewonnene Rohsalz in den dafür äufgefahrenen Strecken von den Abbaubetriebspunkten bis zum Füllort in die un mittelbare Nähe der Schachtröhre zu transportieren.
Die Art der Ausund Vorrichtung und die beim Auffahren gewählten Streckenquer schnitte entscheiden deshalb schon frühzeitig über das Förderverfahren in den Haupt strecken.
Der Werra-Kalibergbau mit seinem nur wenig wechselnden Einfallen hat schon in der Ausund Vorrichtung die zukünftigen Hauptstrecken in dasJNiveau des Kalilagers gelegt. Im stärker welligen Südharzbezirk mußten in manchen Salzgruben ganze För derstrecken oder Streckenteile in das liegende Steinsalz verlegt werden, um zu starke Betriebsstörungen in der Hauptstreckenförderung zu vermeiden. Der steile oder halb steile Abbaubetrieb im Staßfurter Revier erfordert eine spezielle Auffahrung der Hauptstrecken im Steinsalz, so daß in diesem Bezirk fast überall ein söhliger Strecken verlauf anzutreffen ist.
8.1.Seilund Kettenbahnförderung
Die auch heute noch in fast allen Kali -und Steinsalzgruben vorherrschende Förder methode in den Strecken ist die Seilbahn- oder Kettenbahnförderung. Es handelt sich um eine Wagenförderung, d. h. um einen diskontinuierlichen Betrieb.
Jede Wagenförderung in den Hauptstrecken ist an eine Gleisanlage gebunden. Sie muß sorgfältig verlegt und ständig überprüft und gewartet werden. Störungen in der Hauptstreckenförderung können schnell zu Stillständen in der Schachtförderung und damit zu Produktionseinbußen führen. - Die wichtige Arbeit des Gleisverlegens und der Instandhaltung der gesamten Gleisanlagen ist im Lehrbuch „Allgemeine Berg
baukunde“ |
ausführlich beschrieben worden. Auf |
diese' Ausführungen wird ver |
wiesen. |
» |
|
Art und Größe der in den Salzgruben umlaufenden Förderwagen sind durch die ge schichtliche Entwicklung des deutschen Salzbergbaues bedingt. Die Spurweiten der Gleisanlagen sind nicht in allen Gruben gleich. Sie betragen z. B. 540, 560, 600, 660 und 900 mm. Es ist daher nicht möglich, Förderwagen von einer Grube ohne weiteres in eine andere umzusetzen. Darin offenbaren sich die frühere Zerrissenheit des deut schen Salzbergbaues und der Konkurrenzkampf der einzelnen Konzerne unterein ander. Seine Auswirkungen erschweren auch heute noch Standardisierungsbestrebun gen bei den hauptsächlichsten Maschinen und Aggregaten.
Von Bedeutung für die Festlegung der Förderwagengrößen ist die nachgeschaltete Schachtförderung.
Bei Gestellförderung, d. h. Wagenförderung in der Schachtröhre, muß die ge wählte Größe der Wagen auf dir Größe des Förderkorbes abgestimmt sein.
Der heute noch am meisten verbreitete Förderwagen hat einen Inhalt von 800 1und damit eine Nutzlast von ungefähr 1000 kg bei Hartsalz. Er ist in den Gruben der DD R
I
Inhalt |
l |
b |
d |
e |
h |
l |
s |
1000 |
|
QUO |
350 |
630 |
1180 |
1800 |
600 |
lilld 8/1. Klolnfördenvagcn noch TGL 4489
seit 1959 standardisiert (TGL 4489). Die Einzelheiten dieses Wagentyps und seine Hauptabmessungen sind aus der dem obigen DDR-Standard entnommenen Zeich nung in Bild 8/1 ersichtlich.
Durch die Erhöhung der Fördermengen in fast allen Kali-und Steinsalzgruben der DDR ergab sich die Forderung nach größeren Wagen und damit nach einer Verminderung der umlaufenden Totlast. In mehreren Gruben wurde deshalb ein Mittelförderwagen mit einem Nenninhalt von 2000 1eingeführt, der ebenfalls seit 1959 bei Neuanschaf fungen grundsätzlich der TGL 4490 entsprechen muß. Die Maße sind dem Bild 8/2 zu entnehmen.
Der Einsatz noch größerer Förderwagen blieb bisher auf Ausnahmefälle beschränkt. Ihre Einführung macht Schwierigkeiten, weil ihre größere Kastenform bei Beibehal tung der Standsicherheit eine größere Spurweite voraussetzt. Das Umnageln der Gleis anlage und die Veränderung des Schwellenabstandes sind aber in den Gruben nicht ohne weiteres möglich. Die Umstellung auf große Wagen bei in Betrieb befindlichen Salzgruben bereitet also große Schwierigkeiten.
Bei Neuanlagen wird man im Zuge der Mechanisierung und Betriebskonzentration zweifellos auf größere Förderwagen übergehen.
Für die Arbeitsorganisation innerhalb der Streckenförderung ist die Größe des För derwagenparkes ein ausschlaggebender Faktor. Früher war<man allgemein der Auf fassung, daß ein Grubenbetrieb um so besser arbeitet, je weniger Förderwagen sich in Umlauf befinden. In den vergangenen Jahren haben jedoch eingehende Betriebs untersuchungen bewiesen, daß diese Theorie falsch ist. Die Neuanschaffung von För derwagen in einigen Kaligruben hat die Möglichkeiten der Arbeitsorganisation in der Streckenförderung schlagartig verbessert und damit einen störungsfreien Förderab lauf ergeben.
Bild 8/2. MIttelfördcrwagcn nach TGL 4490
Die erforderliche Größe des Förderwagenparkes richtet sich nach der Förderhöhe der Grube, dem Nutzinhalt der Förderwagen und ihrer notwendigen Umlaufzahl in einem bestimmten Zeitabschnitt.
Zur Berechnung der Förderwagenanzahl ist die Formel auf S. 157 der „Allgemeinen Bergbaukunde“ zu benutzen:
X = Ä 7 + /
Darin bedeuten:
X Anzahl der Förderwagen
F Förderhöhe der Grube [t eff]
I Nutzinhalt eines Förderwagens [t eff]
U tägliche Umlaufzahl
/Anzahl der notwendigen Reservewagen
Die Größe / ist für einen störungslosen Betrieb wichtig. Sie ist von den jeweiligen Ver hältnissen abhängig und daher für jede Grube verschieden. In ihr ist die Anzahl der in Reparatur befindlichen und der für Sonderzwecke notwendigen Wagen (Sprengstofftransport, sonstige Transporte, Wasserwagen) enthalten. Entscheidend für die richtige Benutzung der obigen Formel ist bei Schrapperförderung die Anzahl der an den Schrapperfüllstellen stehenden notwendigen leeren Förderwagen.
Beispiel:
Die notwendige Förderwagenzahl ist entsprechend der obigen Formel nach folgenden ge gebenen Werten zu errechnen:
F Förderhöhe [t eff] = 5500
I |
Förderwageninhalt [t] = 2,2 |
U tägliche Umlaufzahl = 6 |
|
/ |
notwendige Reservewagen = 10-15 % zur errechneten Gesamtsumme |

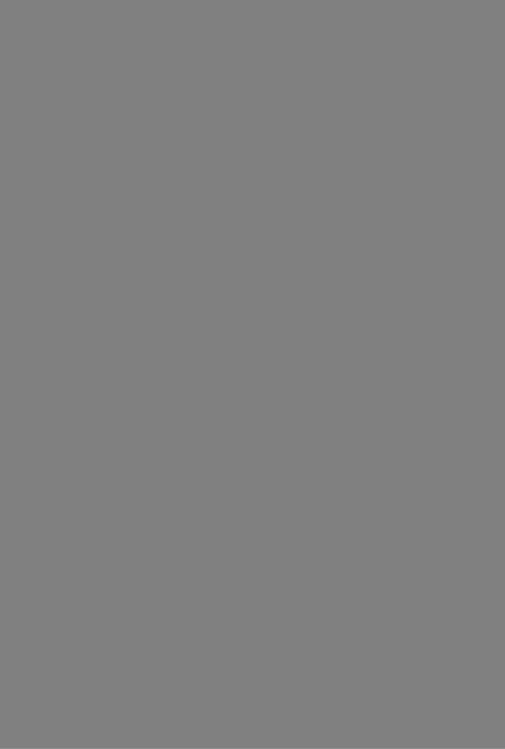

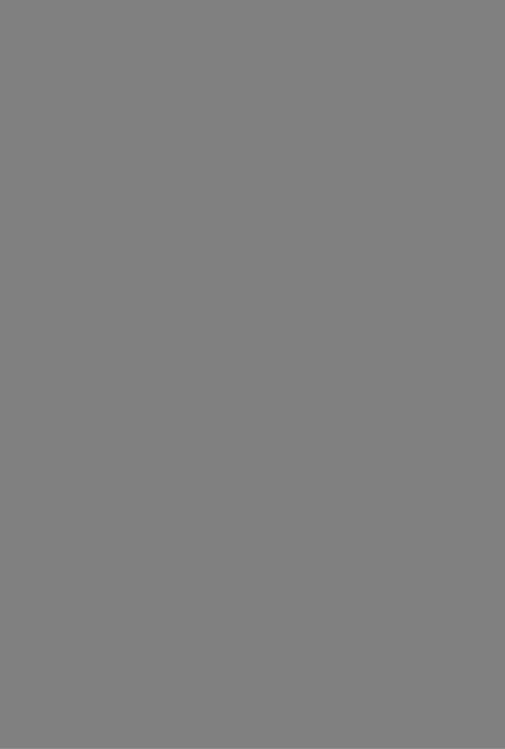