
книги / Сооружение и эксплуатация газонефтепроводов и газонефтехранилищ
..pdf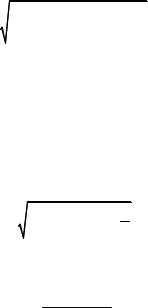
Параметр Re определяется по формуле
Re = 5,172 q ∆ , π d
где q – пропускная способность газопровода, м3/с; d – внутренний диаметр газопровода, м; ∆ – относительная плотность газа по воздуху; µ – динамическая вязкость газа, Па·с.
Соответствующие значения давления в конце газопровода и расстояния между компрессорными станциями определяются по формулам:
|
|
|
|
|
q2 λT |
|
z |
cp |
l ∆ |
|
||||
P |
= |
Р2 |
− |
|
|
cp |
|
|
|
; |
||||
0,1063 10−12 |
d 5 |
|||||||||||||
к |
|
|
н |
|
|
|||||||||
l = |
|
0,1063 10−12 |
d 5 |
(Pн2 − Pк2 ) |
. |
|||||||||
|
|
q2 λT |
|
z |
cp |
∆ |
|
|||||||
|
|
|
|
|
|
|||||||||
|
|
|
|
|
cp |
|
|
|
|
|
При движении газа по трубопроводу давление в нем падает, изменяясь от начального Рн в начале трубы до конечного давления Рк в конце газопровода. Давление в любой произвольной точке, находящейся на расстоянии x от начала газопровода, определяется по формуле
Px = Pн2 − (Pн2 − Pк2 ) xl .
Для определения количества газа в действующем газопроводе используется формула
Q = 293 Vг Рср , |
|
тр |
zср T |
|
где Vг – геометрический объем газопровода, м3; Рср – среднее давление газа в пределах рассматриваемого участка,
Рср = |
2 |
Pн + |
|
Рк2 |
|
. |
|
3 |
P |
+ P |
|||||
|
|
|
|||||
|
|
н |
|
к |
151
20.ДИАГНОСТИКА ТРУБОПРОВОДОВ
20.1.Общие понятия о диагностике трубопроводов
Своевременному обнаружению дефектов, выявлению места
ипричины их возникновения и, наконец, восстановлению нарушенного данными дефектами соответствия трубопровода техническим требованиям служит техническое диагностирование, определение технического состояния объекта диагностирования с заданной точностью. Дефекты трубопроводной системы могут быть вызваны не только условиями эксплуатации, но и ошибками проектирования, представляющими собой особый класс дефектов, которые также подлежат устранению с помощью методов и средств технической диагностики.
Диагностический процесс – это процесс логического мышления, процесс обработки исходной информации для получения вывода о состоянии исследуемой системы трубопровода. Контроль за параметрами процессов перекачки продуктов по трубопроводам для обнаружения дефектов и прогнозирования состояния участков трубопровода базируется на месте параметрической диагностики. Основу метода составляет расчет гидравлических характеристик трубопровода по приведенным значениям измеряемых параметров и последующее сопоставление результатов расчета с первоначальными характеристиками трубопровода, определенными после его сооружения или ремонта. Капитальный ремонт магистральных трубопроводов на основе технологии сплошного ремонта невозможен по чисто экономическим соображениям. Поэтому рекомендуется перейти на метод выборочного ремонта на базе внутритрубной диагностики
идругих современных технологий и технических средств неразрушающего контроля. В связи с важностью этого вопроса в России приняты меры по созданию мощностей для выполнения комплекса диагностических работ. В стране создан Центр тех-
152

нической диагностики в акционерной компании «Транснефть». Центр оснащен необходимыми диагностическими приборами (профилемеры, ультразвуковые и магнитные дефектоскопы на диаметры труб 530/720, 720/820, 1020/1220 мм).
Техническая диагностика – изучение и оценка состояния технической системы и предсказание возможных отклонений в ее работе.
Целью технической диагностики является определение возможности и условий дальнейшей эксплуатации диагностируемого оборудования и в конечном итоге повышение промышленной и экологической безопасности.
Основные виды технической диагностики приведены на рис. 20.1.
Техническая
диагностика
С разборкой объекта диагностирования
Без разборки объекта диагностирования
Диагностика |
|
Диагностика |
|
|
|
|
применением |
|
применением |
|
Функциональная |
|
Тестовая |
методов |
|
визуально- |
|
диагностика |
|
диагностика |
разрушающего |
|
измерительного |
|
|
|
|
контроля |
|
контроля |
|
|
|
|
Параметрическая( ) Вибрационная оперативная диагностика диагностика
Рис. 20.1. Виды технической диагностики
153
Задачами технической диагностики, которые необходимо решить для достижения поставленной цели, являются:
•обнаружение дефектов и несоответствий, установление причин их появления и на этой основе определение технического состояния оборудования;
•прогнозирование технического состояния и остаточного ресурса (определение с заданной вероятностью интервала времени, в течение которого сохраняется работоспособное состояние оборудование).
Основной проблемой технической диагностики является распознавание состояния технической системы в условиях ограниченной информации.
Техническое состояние оборудования определяется числом дефектов и степенью их опасности. Дефектом называют каждое отдельное несоответствие детали или технической системы требованиям, установленным технической документацией.
20.2. Внутритрубные инспекционные снаряды
Внутритрубные снаряды – это устройства, предназначенные для пропуска по всей длине трубопровода, движение их осуществляется потоком продукта. Снаряды подразделяются на две категории: пользовательские или обычные, т.е. снаряды, которые исполняют функции очистки, разделения и обезвоживания; и «интеллектуальные» (ВИС), или внутритрубные диагностические снаряды, с помощью которых получают информацию о наличии и местоположении любых дефектов.
Диагностические снаряды можно разделить на профилемеры, используемые для определения отклонений геометрической формы трубопровода от проектной, и дефектоскопы, определяющие наличие дефектов стенок трубопровода.
Дефектоскопы по принципу действия можно разделить на магнитные и ультразвуковые. Магнитные дефектоскопы работают по принципу искажения магнитных линий в местах дефек-
154

тов, а работа ультразвуковых дефектоскопов основана на рассеивании ультразвуковых волн на дефектах (рис. 20.2).
Рис. 20.2. Схема дефектоскопа «Ультраскан»
Техническая характеристика ультразвукового дефектоскопа:
•диапазон диаметров трубопроводов – от 273 до 1220 мм;
•разрешающая способность в продольном направлении –
3,5 – 23,5 мм;
•разрешающая способность в поперечном направлении –
8,5 мм;
•погрешность измерения толщины стенки ±0,2 мм;
•максимальная длина исследуемого участка – 100–400 км.
Техническая характеристика магнитного дефектоскопа:
•диапазон диаметров трубопроводов – от 508 до 762 мм;
•среда эксплуатации – нефть, нефтепродукты, газ;
•толщина обследуемой стенки трубопровода – 6–18 мм;
•погрешность определения местоположения дефекта:
0,5 % от пройденной дистанции, относительно ближайшего кольцевого шва ±0,2 м;
•допустимая овальность трубопровода D – 13 %;
•рабочее давление – 0,5–8,0 МПа.
Ультразвуковой дефектоскоп имеет преимущества перед магнитным. Преимущества заключаются в способности ультразвуковых дефектоскопов измерять толщину стенки трубопрово-
155
да. Зарегистрированные при этом данные об уменьшении толщины стенки считаются решающим фактором при принятии решения о проведении ремонтных работ. Поскольку такие приборы обеспечивают прямое измерение стенки трубопровода, полученные данные могут быть использованы для расчетов его фактической остаточной прочности. Магнитные дефектоскопы определяют лишь изменение толщины стенки относительно проектного значения, что в случае применения сварных труб может привести к значительным ошибкам в расчетах.
Внутритрубные инспекционные снаряды имеют одинаковые конструктивные элементы: это манжеты, с помощью которых снаряды перемещаются под действием потока нефти и опираются на стенки трубопровода; демпферы, расположенные спереди и сзади снаряда, для предохранения его от разрушения или столкновения с каким-либо препятствием; одометр, определяющий расстояние, пройденное снарядом с момента запуска. В герметичном корпусе располагается компьютер, источник питания, имеется вывод для считывания данных из памяти компьютера. Для получения информации профилемер имеет датчики, находящиеся в непосредственном соприкосновении со стенкой трубопровода, а дефектоскоп – 160 датчиков, осуществляющих прозвучивание стенок. Снаряд обычно делится на функционально и конструктивно законченные секции.
Имеющееся программное обеспечение позволяет представить информацию, полученную от внутритрубных инспекционных снарядов, в виде диаграмм с графическими изображениями дефектов в трехмерном пространстве, в виде статистических данных, с информацией о количестве дефектов каждого вида.
В публикациях А.Г. Головинского отмечается, что практическая работа с внутритрубными инспекционными снарядами выявила ряд их недостатков. «Ультраскан» позволяет обнаруживать особенности, ориентированные параллельно поверхности трубы и обладающие определенной площадью проекции, в результате чего не регистрируются двойные дефекты, распо-
156
ложенные один над другим по высоте стенки трубы, неточно оцениваются характер и размеры опасных трещиноподобных повреждений, ориентированных под углом к поверхности.
Во время трассовых обследований дополнительно установлено, что в ряде случаев внутритрубный инспекционный снаряд регистрирует только один из близко расположенных дефектов и неточно определяет местоположение небольших по размерам особенностей. Последнее существенно затрудняет обнаружение внутренних повреждений непосредственно на трубопроводе.
Одной из последних отечественных разработок является универсальный снаряд-дефектоскоп, разработанный СКБ «Транснефтеавтоматика», который включает в себя четыре функциональные и конструкционно законченные секции, механически и электрически связанные между собой: магнитную, ультразвуковую, навигационную, энергетическую. Данный дефектоскоп позволяет получить полную картину технического состояния оборудования. При описанных вариантах требуется строительство пусковых и приемных камер.
Под руководством профессора А.А. Дубова на предприятии
ООО «Энергодиагностика» (Москва) [13] разработан метод бесконтактной магнитометрической диагностики, согласно которому основными источниками возникновения повреждений в конструкциях являются зоны концентрации напряжений, в которых коррозионные процессы, развитие усталости и ползучести проходят наиболее интенсивно. При развитии этих процессов изменяется намагниченность металла, отражающая фактическое напряженно-деформированное состояние конструкций. Таким образом, метод магнитной памяти металла – это метод неразрушающего контроля, основанный на регистрации и анализе распределения собственных магнитных полей рассеяния на поверхности изделий с целью определения зон концентрации напряжений, дефектов, неоднородности структуры металла и сварных соединений. Для проведения бесконтактного магнитометрического обследования был изготовлен прибор СКИФ
157

«МБС-04». Он очень удобен в эксплуатации, его габаритные размеры 230×600×130 мм, вес 4,9 кг. Один человек может двигаться вдоль трассы трубопровода и обследовать намечаемый участок.
Рис. 20.3. Диаграмма напряженного состояния участка газопровода
ООО «Западно-Уральский центр сертификации» провел обследование газопровода Чернушка–Пермь на участке в районе 4000–4500 м. Направление обследования – по ходу продукта. В результате обследования была получена диаграмма напряженного состояния участка газопровода (рис. 20.3). Полученная диаграмма позволяет выделить наиболее напряженные участки газопровода т.е. наиболее опасные.
158
21. ПРОГНОЗИРОВАНИЕ И РЕМОНТ МАГИСТРАЛЬНЫХ ТРУБОПРОВОДОВ
Надежность трубопроводной системы зависит не только от числа отказов, но и от того, как конструктивно и организационно обеспечиваются быстрое отыскание и локализация неисправностей, определение причин их проявления и прогнозирование фактического состояния агрегатов и устройств в период нормальной эксплуатации и аварийных состояний. С применением регулярной диагностики оборудования расход запасных частей на замену и ремонт элементов снижается примерно в пять раз, стоимость текущего ремонта (благодаря более точному знанию объекта и увеличению межремонтного периода) – в два раза, рабочий парк машин – примерно на 10 %, расход топлива и фонда заработной платы – на 10 %.
Методы обнаружения утечек на трубопроводах. Как пока-
зывает отечественная и зарубежная практика эксплуатации трубопроводов, основными причинами аварий и утечек на них являются разрушения труб из-за коррозии, дефектов сварки или некачественного изготовления, стихийных явлений, ошибок управления.
Наиболее простыми системами обнаружения утечек из трубопроводов являются системы, базирующиеся на измерении количества измеряемого продукта в начале и в конце трубопровода. Они позволяют регистрировать утечки по балансу перекачки с чувствительностью системы до 0,75 % расхода жидкости. Факт утечки можно определить по понижению давления в трубопроводе, эта система отличается быстрым реагированием, так как волны давления передаются с высокой акустической скоростью в трубе (приблизительно 1000 м/c). На принципе регистрации кратковременного изменения давления в трубопроводе в результате быстрого возникновения течи основан метод Вэйфалет направленного действия. Эффект защищенности достигается установкой на концах участка чувствительных датчиков и специальной обработки
159
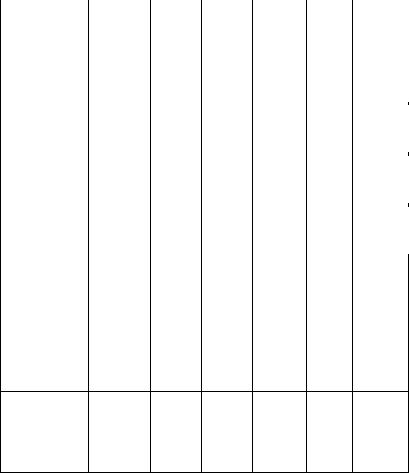
сигналов от них. Существует достаточно много видов зарубежных и отечественных течеискателей. В табл. 21.1 дана сравнительная характеристика методов обнаружения утечек в трубопроводах.
Таблица 21.1
Сравнение эффективности методов обнаружения утечек в трубопроводах
|
ЧувствиОпреОценка Время ДиапаНизкая |
||||||
Метод |
тельность |
деление |
размера |
реаги- |
зон |
степень |
|
|
места |
утечки |
рования |
приме- |
ложных |
||
|
|
||||||
|
|
утечки |
|
|
нения |
сигналов |
|
Визуальное |
– |
+ |
– |
– |
+ |
+ |
|
наблюдение |
|||||||
|
|
|
|
|
|
||
Исследование |
|
|
|
|
|
|
|
окружающего |
+ |
+ |
– |
– |
– |
+ |
|
воздуха |
|
|
|
|
|
|
|
Измерение |
|
|
|
|
|
|
|
акустических |
+ |
+ |
– |
– |
+ |
+ |
|
шумов |
|
|
|
|
|
|
|
Укладка |
|
|
|
|
|
|
|
кабеля вдоль |
+ |
– |
– |
+ |
– |
+ |
|
трубопровода |
|
|
|
|
|
|
|
Метод линей- |
+ |
– |
+ |
– |
– |
+ |
|
ного баланса |
|||||||
|
|
|
|
|
|
||
Контроль за |
|
|
|
|
|
|
|
понижением |
– |
– |
– |
+ |
– |
– |
|
давления в |
|||||||
|
|
|
|
|
|
||
трубопроводе |
|
|
|
|
|
|
|
Система |
+ |
+ |
+ |
+ |
+ |
+ |
|
Вэйфалет |
|||||||
|
|
|
|
|
|
Моделирование нестацио-
нарных про- + + + + + +
цессов перекачки
«+» хорошая или средняя эффективность, «–» низкая эффективность.
160