
книги / Основы технологии машиностроения. Методы обработки заготовок и технологические процессы изготовления типовых деталей машин
.pdfопирается на кулачки люнета. В тех случаях, когда следует обеспечить соосность обтачиваемой поверхности с ранее обработанной, кулачки люнета устанавливают впереди рез- ца, то есть на ранее обработанную поверхность. При скоро- стном резании кулачки создают значительное трение. Чтобы уменьшить трение, применяют люнеты с роликовыми опо- рами (см. рис. 3.2, а). При скоростном точении часто воз- никают вибрации, которые увеличивают шероховатость поверхности и снижают точность обработки. Для устране- ния вибраций используют люнеты с виброгасителем (см. рис. 3.2, б). Тарельчатые пружины, помещенные в кор- пусе виброгасителя, поглощают вибрации детали.
При высоких скоростях резания стружка имеет слив- ную форму и сходит из-под резца непрерывной лентой. Та- кая стружка весьма опасна, так как может явиться причи- ной травматизма (порезов и (или) ожогов). Для размельче- ния такой стружки применяют специальные устройства – стружколоматели.
В массовом и крупносерийном производствах обра- ботку валов часто производят на многорезцовых станках, которые имеют два суппорта – передний и задний. Перед- ний суппорт служит для точения. Задний суппорт, совер- шающий поперечное движение, предназначен для подрезки торцов и прорезания канавок. Резцы настраивают так, что- бы обработка всех участков заканчивалась одновременно. Многорезцовое обтачивание выполняют тремя способами.
Первый способ – деление общего припуска по глуби- не. При этом способе припуск на одной из ступеней снима- ется последовательно несколькими резцами, и передний суппорт совершает путь L, равный сумме обрабатываемых ступеней L = l1 + l2 + l3 (рис. 3.3, а).
Второй способ – деление длины заготовки на не- сколько участков (рис. 3.3, б). Применяется, когда макси- мальный припуск может быть удален резцами за один про-
61
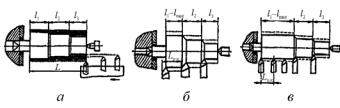
Рис. 3.3. Способы обработки ступенчатого вала на много- резцовом станке: а – способ деления припуска;
б– способ деления длины обработки вала;
в– способ деления длины максимальной ступени
ход. При такой схеме обработки длина хода резца l = L/n, где n – количество ступеней.
Третий способ – деление максимальной ступени вала (рис. 3.3, в). Более длинная ступень l1 протачивается не- сколькими резцами, установленными на одинаковую глу- бину съема.
Установка резцов производится либо по обработан- ной заготовке, либо по специальному эталону.
Многорезцовую обработку применяют, как правило, на предварительных операциях. Чистовое точение можно выполнять на гидрокопировальных станках 1708, 1Н713, 1Б732 и др., имеющих два суппорта, расположенных в вер- тикальной плоскости, что позволяет облегчить сход стружки из зоны резания. Точение по копиру осуществляется одним резцом, расположенным на верхнем суппорте. Подрезка торцов осуществляется резцами, расположенными в ниж- нем суппорте. Точение на многорезцовых станках осущест- вляется со скоростью резания 30–50 м/мин, а чистовое то- чение на гидрокопировальных станках – со скоростью ре- зания 150–200 м/мин. В качестве СОЖ обычно применяют эмульсию.
В серийном и мелкосерийном производствах валы обрабатывают на станках с числовым программным управ- лением или ручным управлением.
62

В единичном производстве обработку валов обычно осуществляют на универсальном оборудовании с ручным управлением.
3.2. Обработка наружных поверхностей вращения абразивным инструментом
К методам обработки наружных поверхностей вра- щения абразивным инструментом относят тонкое алмазное точение (см. раздел 3.1), шлифование, притирку, суперфи- ниш, полирование, алмазное выглаживание, обкатку роли- ками и шариками, хонингование.
3.2.1. Шлифование наружных поверхностей вращения
Шлифование является основным и наиболее распро- страненным методом обработки наружных цилиндрических поверхностей; подразделяется на чистовое и тонкое шли- фование. Тонкое шлифование осуществляется шлифоваль- ными кругами или шлифовальными лентами на кругло- шлифовальных станках с продольной подачей (рис. 3.4) и методом врезания (рис. 3.5), на бесцентрово-шлифоваль- ных станках на проход (рис. 3.6) и методом врезания (рис. 3.7), а также на ленточно-шлифовальных станках.
Рис. 3.4. Схема круглого шлифования с продольной подачей
63
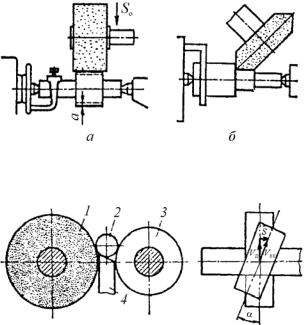
Рис. 3.5. Схема круглого шлифования: а – методом врезания с поперечной подачей; б – методом одновременного шлифования шейки и уступа вала
Рис. 3.6. Схема бесцентрового шлифования на проход
На круглошлифовальном станке заготовка устанавливает- ся в центрах станка. Линейная скорость вращающейся за- готовки составляет 10–15 м/мин, а линейная скорость ин- струмента (шлифовального круга) – порядка 30 м/с.
Процесс шлифования может осуществляться с продоль- ной подачей (см. рис. 3.4) и методом врезания (см. рис. 3.5). В первом случае заготовка совершает возвратно-поступа- тельное продольное перемещение с продольной подачей Sпр = (0,5 – 0,8)Н, где Н – высота круга, за один оборот за- готовки, а в конце каждого хода производится поперечная подача (глубиной резания) 0,01–0,03 мм.
При выхаживающих проходах продольная подача уменьшается до Sпр = 0,2…0,3Н, глубина резания до 0,005…0,02 мм. Длина продольного хода при шлифовании
64

Рис. 3.7. Схема бесцентрового шлифования методом врезания
должна обеспечивать перебег инструмента на сторону, рав- ный 0,2 – 0,4Н, где Н – высота круга или ширина ленты.
Второй способ заключается в том, что инструменту (шлифовальному кругу или шлифовальной ленте) сообща- ется только поперечная подача за один оборот заготовки.
Чистовое круглое шлифование в центрах станка обес- печивает точность 6–7-го квалитета и шероховатость по- верхности Ra = 0,3…1,25 мкм. Тонкое круглое шлифование в центрах станка обеспечивает точность 5–6-го квалитета и шероховатость поверхности Ra = 0,02…0,08 мкм.
При шлифовании на бесцентрово-шлифовальных станках на проход (см. рис. 3.6) заготовку 2 устанавливают между двумя шлифовальными кругами (ведущим кругом 3 и шлифующим кругом 1, обеспечивающим съем материала) на специальный поддерживающий нож 4, изготовленный из износостойкого материала.
Благодаря скосу, направленному в сторону ведущего круга, деталь прижимается к ведущему кругу, вследствие
65
чего ведущий круг передает крутящий момент детали. Во избежание огранки детали диаметром более 30 мм смещают вверх на 10–15 мм от линии центров шлифо- вальных кругов.
При шлифовании на проход ведущий круг устанав- ливают под углом α = 1…5°.
Величину продольной подачи S при шлифовании на проход назначают в пределах 400–4000 мм/мин. Ли- нейная скорость ведущего круга Vв.к = 15…30 м/мин при черновом шлифовании. При чистовом шлифовании увеличивают до 100 м/мин и более.
Продольная подача определяется по формуле
S =1000 Vв.к sin αη S ;
окружная скорость вращения детали определяется по формуле
Vд = Vв.к cos α(1 + δ ),
где S – продольная подача, мм/мин; Vд – окружная скорость вращения детали, м/мин; Vв.к – окружная скорость ведущего круга, м/мин; ηS – коэффициент осевого проскальзывания (0,90…0,98); δ – коэффициент, учитывающий ускоренное за счет скорости шлифующего круга вращение изделия
(δ = 0,04…0,07).
Возможно шлифование набором шлифующих кругов разной зернистости, ширина такого круга может достигать 800 мм. Шлифование сборным кругом позволяет за один проход обеспечить обработку по 6–8-му квалитету точно- сти и шероховатость поверхности Ra = 0,16…0,32 мкм.
Бесцентровое шлифование может также осуществ- ляться методом врезания (см. рис. 3.7).
Бесцентрово-шлифовальные станки имеют жесткость в 1,5–2,0 раза большую по сравнению с кругло-шлифоваль- ными станками. Поэтому они допускают форсированные
66
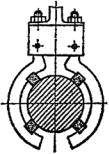
режимы обработки, обеспечивая более высокую произво- дительность. Позволяют осуществлять шлифование валов, имеющих малую жесткость. В качестве СОЖ при шлифо- вании (круглом и бесцентровом) применяют эмульсии или водные содовые растворы.
3.2.2. Хонингование наружных поверхностей вращения
Хонингование валов производится на специальных станках, снабженных приспособлениями с двумя полуколь- цами (рис. 3.8), на внутренней стороне которых закреплены шлифовальные бруски, а также на токарных и токарно- револьверных станках с аналогич- ными приспособлениями, устанавли- ваемыми на суппорте станка. Хонин- гование делят на среднее и тонкое.
Обрабатываемая деталь, охватывае- мая двумя полукольцами, получает вращательное движение.
Скорость резания при наруж- ном хонинговании колеблется от 60 до 200 м/мин, а давление брусков – от 0,3 до 1,35 МПа. Кроме того, брускам сообщают продольное пе-
ремещение вдоль образующей наружной поверхности со скоростью от 15 до 100 м/мин. После двух-трех минут хонингования станок автоматически выключается и де- таль освобождается.
В качестве СОЖ используют смесь из 75–85 % керо- сина и 15–25 % индустриального масла И-20А. Среднее хо-
нингование обеспечивает точность 7–8-го квалитета и ше- роховатость поверхности Ra = 0,32…1,25 мкм.
Тонкое хонингование обеспечивает точность 6–7-го квалитета и шероховатость поверхности Ra = 0,08…016 мкм.
67
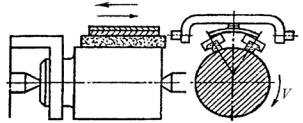
Следует отметить, что хонингование наружных ци- линдрических поверхностей валов применяют крайне редко. Значительно чаще для обработки наружных цилиндриче- ских поверхностей валов применяют суперфиниш.
3.2.3. Суперфиниширование наружных поверхностей вращения
Суперфиниширование наружных поверхностей вра- щения (суперфиниш) очень похоже на хонингование, так как в качестве обрабатывающего инструмента применяют мелкозернистые шлифовальные (абразивные, алмазные или эльборовые) бруски. Отличие суперфиниша от хонингова- ния состоит в том, что при суперфинише наряду с враща- тельным движением заготовки и поступательным продоль- ным движением брусков вдоль образующей заготовки име- ется еще колебательное движение брусков, которое являет- ся главным рабочим движением (рис. 3.9).
Рис. 3.9. Схема суперфиниширования
Суперфиниширование принято подразделять на чис- тое, тонкое и двукратное. Колебательное движение направ- лено вдоль брусков. При чистом суперфинишировании ко- лебательное движение имеет ход от 2 до 6 мм и частоту ко- лебаний от 300 до 1000 ход/мин, при тонком и двукратном суперфинишировании – ход от 0,2 до 2,0 мм и частоту ко- лебаний от 1000 до 10000 ход/мин. Толщина срезаемого
68
слоя изменяется от 0,005 до 0,02 мм, а продолжительность обработки составляет 0,2–0,5 мин. Шероховатость поверх- ности достигает Rа = 0,04 мкм. В качестве СОЖ используют смесь индустриального масла И-20А с керосином в соот- ношении 1 : 10.
В начале процесса микронеровности на поверхности детали разрывают масляную пленку. Выступающие гре- бешки микронеровностей срезаются абразивными бруска- ми. По мере срезания гребешков микронеровность сглажи- вается, и после того, как масляная пленка станет сплошной и не будет иметь разрывов от выступающих зерен, процесс резания прекращается.
При суперфинишировании предъявляются очень же- сткие требования к чистоте СОЖ, потому что наличие мель- чайших металлических или абразивных частичек может вы- звать появление рисок на обрабатываемой поверхности.
Суперфинишу предшествует операция шлифования или тонкого точения, которая обеспечивает шероховатость поверхности Ra ≤ 0,32 мкм.
Чистое суперфиниширование обеспечивает точ- ность 6–7-го квалитета и шероховатость поверхности
Ra = 0,04…0,08 мкм.
Тонкое суперфиниширование обеспечивает точ- ность 5–6-го квалитета и шероховатость поверхности
Ra = 0,02…0,04 мкм.
Двойное суперфиниширование обеспечивает точ- ность 5-го квалитета и шероховатость поверхности
Ra = 0,01…0,02 мкм.
Суперфиниш не исправляет дефекты формы, полу- ченные на предыдущих операциях.
69
3.2.4. Притирка наружных поверхностей вращения
Притирка (доводка) – отделочная операция, которую выполняют инструментами – притирами (бывает двух ви- дов: чистовая и тонкая). Притиры изготавливают из чугуна или бронзы, и на их поверхность наносят абразивную сус- пензию (микропорошок с машинным маслом). Относитель- ное перемещение детали и притира должно обеспечивать движение зерен по новым, не повторяющимся траекториям. Для обеспечения этого условия обрабатываемая деталь по- лучает вращение от шпинделя станка, а возвратно- поступательное продольное перемещение осуществляется вручную. В качестве абразивов достаточно часто исполь- зуют окись хрома (Cr2O3), окись железа (Fe2O3) (порошок окиси железа часто называют крокусом) или венскую из- весть (порошок углекислого кальция с примесью магния
ижелеза). По твердости, режущим свойствам и производи- тельности окись хрома стоит на первом месте. Наиболее чистую поверхность обеспечивает венская известь. В каче- стве смазывающего материала используют смесь машинно- го масла с керосином. При использовании венской извести применяют спирт, а при использовании крокуса – вазелин.
Для доводочных работ широко используют суспензии
ипасты, например пасты, разрабатываемые ГОИ (Государ- ственным оптическим институтом). Пасты ГОИ содержат термически обработанную (прокаленную) окись хрома, жи- ры и органические поверхностно-активные кислоты (олеи- новую или стеариновую). Пасты ГОИ делятся на грубые (40 мкм), средние (16 мкм) и тонкие (7 мкм). Цифры указы- вают толщину снятого слоя со стальной закаленной плитки при 100 возвратно-поступательных движениях притира.
Притирку наружных цилиндрических поверхностей валов в единичном производстве осуществляют на токар- ных станках с использованием разрезных притиров – вту-
70