
книги / Основы сварочных работ при сооружении магистральных трубопроводов
..pdfдолжно состоять из марки, диаметра, группы электродов и обозначения стандарта (ГОСТ 9466–75).
Типы электродов для сварки теплоустойчивых и конструк-
ционных сталей. Согласно ГОСТ 9467–75 электроды подразделяются на следующие типы:
Э38, Э42, Э46 и Э50 − для сварки углеродистых и низколегированных конструкционных сталей с временным сопротивлением разрыву до 50 кгс/мм2;
Э42А, Э46А и Э50А − для сварки углеродистых и низколегированных конструкционных сталей с временным сопротивлением разрыву до 50 кгс/мм2, когда к металлу сварных швов предъявляют повышенные требования пластичности и ударной вязкости;
Э55 и Э60 − для сварки углеродистых и низколегированных конструкционных сталей с временным сопротивлением разрыву от 50 до 60 кгс/мм2;
Э70, Э85, Э100, Э125, Э150 − для сварки легированных конструкционных сталей повышенной и высокой прочности с временным сопротивлением разрыву свыше 60 кгс/мм2;
Э-09М, Э-09МХ, Э-09Х1М, Э-05Х2М, Э-09Х2М1, Э-09Х1МФ,
Э-10Х1М1НФБ, Э-10Х3М1НФБ, Э10Х5МФ − для сварки легированных теплоустойчивых сталей.
Химический состав должен соответствовать:
−для металла, наплавленного электродами для сварки конструкционных сталей, требованиям технических условий или паспортов на электроды конкретных марок;
−для металла, наплавленного электродами для сварки легированных теплоустойчивых сталей, требованиям стандарта.
Механические свойства металла шва, наплавленного металла и сварного соединения, а также содержание серы и фосфора в наплавленном металле регламентированы стандартом.
Условное обозначение электродов для дуговой сварки конст-
рукционных и теплоустойчивых сталей − по ГОСТ 9466–75. При этом во второй строке (знаменателе) группа индексов, указывающих
51
характеристики наплавленного металла и металла шва (поз. 7 на рис. 25), должна быть записана в соответствии с требованиями, приведенными ниже.
Согласно требованиям ГОСТ 9467–75 в условном обозначении электродов для сварки углеродистых и низколегированных сталей с временным сопротивлением разрыву менее 60 кГс/мм2 группа индексов записывается следующим образом: первый индекс (две цифры) указывает минимальное значение величины σВ (кгс/мм2), а второй индекс (одна цифра) одновременно характеризует минимальные значения показателей δ5 и температуры Тх, при которой определяется ударная вязкость (данные следует приводить для металла шва и наплавленного металла в состоянии после сварки, т.е. без термической обработки).
Таким образом, второй индекс (третья цифра) будет означать:
0− δ5 < 20 и Тх не регламентирована;
1− δ5 = 20 и Тх = +20 °С;
2− δ5 = 22 и Тх = +0 °С;
3− δ5 = 24 и Тх = –20 °С;
4− δ5 = 24 и Тх = –30 °С;
5− δ5 = 24 и Тх = –40 °С;
6− δ5 = 24 и Тх = –50 °С;
7− δ5 = 24 и Тх = –60 °С.
Если какой-нибудь показатель (δ5 или Тх) отличается от вышеприведенных, то второй индекс должен соответствовать минимальному значению показателя δ5, и дополнительно, в скобках, указывается третий индекс, характеризующий показатель Тх.
В условном обозначении электродов для сварки сталей с σВ > 60 кгс/мм2 группа индексов, обозначающих характеристики наплавленного металла и металла шва (данные брать для металла в состоянии после термической обработки), указывает среднее содержание основных химических элементов в наплавленном металле и минимальную температуру, при которой ударная вязкость металла составляет не менее 3,5 кгс м/мм2, и должна включать:
52
–первый индекс из двузначного числа, соответствующего среднему содержанию углерода в сотых долях процента;
–последующие индексы, каждый из которых состоит из буквенного обозначения соответствующего химического элемента и стоящего за ним числа, показывающего среднее содержание элемента в наплавленном металле (с погрешностью до 1 %);
–последний индекс, характеризующий Тх:
Тх, °С |
Не регламен- |
+20 |
0 |
–20 |
–30 |
–40 |
–50 |
–60 |
|
тирована |
|
|
|
|
|
|
|
Индекс |
0 |
1 |
2 |
3 |
4 |
5 |
6 |
7 |
Перед последним индексом ставят тире.
К основным химическим элементам, кроме углерода, следует относить только легирующие элементы, определяющие механические свойства наплавленного металла. При этом кремний и марганец считают основными химическими элементами, если их содержание в наплавленном металле превышает 0,8 %.
Порядок расположения буквенных обозначений химических элементов определяется уменьшением их среднего содержания в наплавленном металле. При среднем содержании элемента менее 0,8 % число за буквенным обозначением не указывают.
Химические элементы, содержащиеся в наплавленном металле, обозначают: А − азот, Б − ниобий, В − вольфрам, Г − марганец, Д − медь, К − кобальт, М − молибден, Н − никель, Р − бор, С − кремний, Е − титан, Ф − ванадий, Х − хром, Ю − алюминий.
В условном обозначении электродов для сварки легированных теплоустойчивых сталей группа индексов, указывающих характеристики наплавленного металла и металла шва (данные брать для метала в состоянии после термической обработки), должна включать два индекса. Первый указывает Тх, а второй – максимальную рабочую температуру, при которой регламентированы показатели длительной прочности наплавленного металла и металла шва
(табл. 4).
53
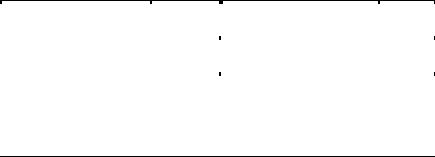
Таблица 4 Соответствие индексов максимальной рабочей температуре, °С
Максимальная рабочая |
Индекс |
|
температура, °С |
|
|
Не регламентирована |
0 |
|
или ниже 450 |
||
|
||
450−465 |
1 |
|
470−80 |
2 |
|
490−505 |
3 |
|
510−525 |
4 |
|
|
|
Максимальная рабочая |
Индекс |
температура, °С |
|
530−545 |
5 |
|
|
550−565 |
6 |
570−585 |
7 |
590−600 |
8 |
Свыше 600 |
9 |
|
|
Примеры составления групп индексов, указывающих характеристики наплавленного металла и металла шва, для условного обозначения электродов, используемых при сварке теплоустойчивых и конструкционных сталей. Группа индексов для электродов марки УОНИ-13/45 (типа Э46А), обеспечивающих следующие механические свойства металла шва и наплавленного металла в состоянии после сварки при нормальной температуре: временное сопротивление разрыву (σВ) не менее 46 кгс/мм2 (43); относительное удлинение (δ5) не менее 22 % (2); выполненный электродами наплавленный металл и металл шва в состоянии после сварки имеет Тх = −40 °С (5): 43 2 (5).
Группа индексов для электродов марки ЦЛ-18 (типа Э85), обеспечивающих получение наплавленного металла со средним содержанием 0,18 % C, 1 % Cr, 1 % Mn, выполненный электродами наплавленный металл и металл шва после термической обработки имеет Тх = −10 °С (2): 18Х1Г-2.
Группа индексов для электродов марки ЦЛ-20 (типа Э-09Х1МФ), обеспечивающих получение наплавленного металла и металла шва после термической обработки с Тх = 0 °С (2); показатели длительной прочности наплавленного металла и металла шва регламентированы до температуры 580 °С (7): 27.
54
Типы покрытых электродов для сварки высоколегированных сталей с особыми свойствами. Электроды для сварки высоко-
легированных сталей с особыми свойствами должны удовлетворять требованиям ГОСТ 10052–75. Разнообразие служебного назначения этих сталей определяет и большой типаж электродов для их сварки. Стандартом предусмотрено 49 типов электродов для сварки хромистых и хромоникелевых сталей, коррозионно-стойких, жаропрочных и жаростойких высоколегированных сталей мартенситно-феррит- ного, ферритного, аустенитно-ферритного и аустенитного классов.
Условное обозначение электродов − по ГОСТ 9466–75. Обозначение типа электрода состоит из индекса Э (электроды
для дуговой сварки) и следующих за ним цифр и букв. Две цифры, следующие за индексом, указывают среднее содержание углерода
внаплавленном металле в сотых долях процента. Химические элементы, содержащиеся в наплавленном металле, обозначены буквами, аналогично обозначению типов электродов для сварки теплоустойчивых и конструкционных сталей. Цифры, следующие за буквенными обозначениями химических элементов, показывают среднее значение элемента в процентах. Если содержание элемента
внаплавленном металле менее 1,5 %, цифры не проставляют. При среднем содержании в наплавленном металле кремния до 0,8 % и марганца до 1,6 % буквы С и Г не ставят (например, тип Э-12Х11НВМФ).
Во второй строке условного обозначения группа индексов, указывающих характеристики наплавленного металла и металла шва (поз. 7 на рис. 25), должна состоять из четырех цифровых индексов для электродов, обеспечивающих аустенитно-ферритную структуру
(А + Ф) наплавленного металла, и из трех цифровых индексов − для остальных электродов.
Первый индекс характеризует стойкость наплавленного металла и металла шва к межкристаллитной коррозии.
Второй индекс указывает максимальную рабочую температуру, при которой регламентированы показатели длительной прочности наплавленного металла и металла шва.
55

Третий индекс указывает максимальную температуру сварных соединений, до которой допускается применение электродов при сварке жаростойких сталей.
Четвертый индекс указывает содержание ферритной фазы в наплавленном металле для электродов, обеспечивающих аустенитноферритную структуру наплавленного металла.
Показатели механических свойств приведены в состоянии после сварки либо после термообработки.
Пример обозначения покрытых электродов для сварки высоколегированных сталей с особыми свойствами. Для электрода типа Э-10Х25Н13Г2Б по ГОСТ 10052–75, марки ЦЛ-9, диаметром 5 мм, для сварки высоколегированных сталей с особыми свойствами В, с толстым покрытием Д, 1-й группы, с установленной по ГОСТ 10052–75 группой индексов, характеризующих наплавленный металл 2075 (2 − стойкость металла против межкристаллитной коррозии при испытании по методу АМ; 0 − требований по максимальной рабочей температуре наплавленного металла и металла шва нет; 7 − максимальная рабочая температура сварных соединений 910−1000 °С, до которой допускается применение электродов при сварке жаростойких сталей; 5 − содержание ферритной фазы в наплавленном металле 2−10 %), с основным покрытием Б, пригодного для сварки в нижнем горизонтальном на вертикальной плоскости и в вертикальном снизу вверх положении (3) на постоянном токе обратной полярности (0), полное обозначение имеет следующий вид:
Э−10Х25Н13Г2Б−ЦЛ-9 −5,0 −ВД1 ГОСТ 9466–75, ГОСТ 10052–75,
Е−2075 −Б30
ав технической документации – электроды ЦЛ-9−5,0−1−ГОСТ
9466–75.
7.3.2. Классификация электродных покрытий
Характеристика электродов. Покрытый электрод представляет собой металлический стержень длиной до 450 мм, на поверхность которого чаще всего методом опрессовывания, реже окунанием, на-
56
несено специальное покрытие, состоящее из смеси измельченных компонентов определенного состава и толщины. Один конец электрода на длине 20–30 мм свободен от покрытия для зажатия его в электрододержателе. В зависимости от назначения к электроду предъявляются различные требования.
Основные требования для всех видов электродов: обеспечение устойчивого горения дуги; хорошее формирование шва; получение металла шва определенного химического состава и свойств без дефектов; спокойное и равномерное плавление электродного стержня и покрытия в процессе сварки; минимальные потери электродного металла на угар и разбрызгивание; высокая производительность процесса сварки; легкая отделимость шлаковой корки с поверхности шва: достаточная прочность покрытия; сохранение физико-химиче- ских свойств электродов в течение длительного хранения; минимальная токсичность в процессе сварки и при изготовлении.
К покрытым электродам предъявляют также ряд специальных требований: получение заданной формы шва (глубокий провар, вогнутый мениск шва в разделке, возможность вести процесс в различных пространственных положениях и т.д.); возможность ведения процесса сварки определенным способом (сварка опиранием, сварка методом сверху вниз и другие); получение металла шва со специальными свойствами (повышенной прочности, пластичности, изностойкости, жаропрочности и т.д.).
Основные составляющие (компоненты) покрытий. Для удовлетворения перечисленных требований в покрытие электрода вводят определенные вещества (компоненты) − шлакообразующие, газообразующие, раскислители, легирующие, стабилизирующие, связующие, а также используют металлические стержни различного состава, обычно близкого к составу свариваемого металла.
Шлакообразующие компоненты составляют основу покрытия. Обычно это руды (марганцовая, титановая), минералы (ильменитовый и рутиловый концентраты, полевой шпат, кремнезем, гранит, мрамор, плавиковый шпат и другие), которые при расплавлении образуют шлак, защищающий капли электродного металла и сва-
57
рочную ванну от непосредственного контакта с окружающей атмосферой.
Газообразующие компоненты находятся в электродном покрытии в виде органических (крахмал, пищевая мука, декстрин и другие) либо неорганических веществ, чаще всего карбонатов (мрамора CaCO3, магнезита MgCO3 и других), которые при нагреве разлагаются и образуют газы, оттесняющие воздух от дугового промежутка.
Легирующие элементы и элементы-раскислители − кремний, марганец, титан и другие, используемые в виде сплавов этих элементов с железом (так называемых ферросплавов) вводят в состав покрытия для получения металла шва с требуемыми химическим составом и механическими свойствами. Алюминий в покрытие вводят в виде порошка-пудры.
Для обеспечения устойчивого горения дуги (стабилизации) в покрытие электродов добавляют стабилизирующие (ионизирующие) компоненты − соединения щелочных и щелочно-земельных металлов, обладающих низким коэффициентом ионизации и малой работой выхода электронов. Обычно это различные соединения, в состав которых входят калий, натрий, кальций, мел, полевой шпат, гранит и другие.
В качестве связующих компонентов при изготовлении покрытых электродов используют водные растворы силикатов натрия
икалия, называемые натриевым или калиевым жидким стеклом, а также нитриево-калиевым жидким стеклом.
Для улучшения пластичности обмазочной массы электрода используют формовочные добавки (бентонит, каолин, декстрин, слюду
идругие).
Для повышения производительности сварки, увеличения количества дополнительного металла, вводимого в шов, в покрытии электродов может содержаться до 60 % железного порошка.
Многие материалы, входящие в состав покрытия, одновременно выполняют несколько функций. Например, мел (мрамор), разлагаясь при высокой температуре по реакции CaCO3 → CaO + CO2, создает газовую (CO2) и шлаковую (CaO) защиту расплавленного
58
металла, а ионы кальция в атмосфере дуги повышают устойчивость ее горения.
Виды электродных покрытий. Современные промышленные защитные покрытия электродов для дуговой сварки преимущественно сталей по их металлургическому воздействию в сварочной ванне можно классифицировать на следующие основные виды.
Кислое (рудно-кислое) покрытие (А), основу которого состав-
ляют оксиды марганца, железа, кремния. Газовая защита осуществляется органическими компонентами, сгорающими в процессе плавления электрода. В качестве раскислителей в покрытие вводят ферромарганец.
При плавлении кислых покрытий большая часть введенных в них ферросплавов окисляется рудами; легирование металла кремнием и марганцем идет по схеме кремнемарганцевосстановительного процесса; что не позволяет легировать металл элементами с большим сродством к кислороду. Образующиеся шлаки, обычно кислые, не содержат CaO и не очищают металл от фосфора. В наплавленном металле много растворенного кислорода и неметаллических включений. В результате этого швы обладают пониженной стойкостью к образованию горячих трещин, ударная вязкость металла шва обычно не превышает 12 кгс м/мм2. В связи с высоким содержанием ферромарганца и окислов железа покрытия более токсичны, так как аэрозоли в зоне сварки и зоне дыхания сварщика содержат большое количество вредных соединений марганца.
С энергетической же точки зрения электроды с таким покрытием характеризуются достаточно высокой скоростью расплавления и обеспечивают сварку на форсированных режимах. Электроды с кислым покрытием обладают высокой проплавляющей способностью. Они наиболее технологичны при сварке в нижнем положении, но могут быть использованы и для выполнения вертикальных и горизонтальных швов. Однако из-за повышенной токсичности электроды с кислым покрытием почти не применяются.
Рутиловое покрытие (Р) состоит преимущественно из шлакообразующего компонента − рутилового концентрата TiO2 (до 45 %)
59
с добавками алюмосиликатов (слюды, полевого шпата и др.) и карбонатов (мрамора, магнезита). Вместо рутила в покрытии может содержаться 45−50 % ильменита. Газовая защита обеспечивается введением до 5 % органических веществ (целлюлозы, декстрина), а также разложением карбонатов. В качестве легирующего и раскисляющего компонента используют ферромарганец (10−15 %), а для повышения коэффициента наплавки вводят порошок железа.
Электроды с рутиловым покрытием обладают целым рядом преимуществ по сравнению с другими видами электродов, а именно обеспечивают отличное формирование шва с плавным переходом к основному металлу, малые потери металла на разбрызгивание, легкую отделяемость шлаковой корни, стабильное горение дуги при сварке на переменном токе. Металл шва, выполненный электродами с рутиловым покрытием, мало склонен к образованию пор при колебаниях дуги, при сварке влажного и ржавого металла, при сварке по окисленным поверхностям. Стойкость металла шва к образованию трещин несколько ниже, чем у электродов с кислым покрытием.
Покрытия этого вида обеспечивают высокое качество металла шва, малотоксичны и обладают хорошими сварочно-технологиче- скими свойствами.
Целлюлозное покрытие (Ц) содержит преимущественно (до 50 %) органические составляющие для образования большого количества газов. В качестве шлакообразующей основы используют рутилосиликатные компоненты. Иногда в покрытие вводят специальные компоненты, например, асбест. Раскисление сварочной ванны осуществляется с помощью ферромарганца.
Электроды этого вида имеют небольшую толщину покрытия и при сварке образуют сравнительно малое количество шлака.
Электроды с целлюлозным покрытием характеризуются высокой проплавляющей способностью и значительной скоростью расплавления. Они обеспечивают сварку во всех пространственных положениях с высокой скоростью. Сварка корневого шва производится методом опирания с формированием обратной стороны шва, поэтому отпадает необходимость подварки швов изнутри и обеспечивает-
60