
книги / Технология керамических материалов
..pdf
Способы подготовки пресс-
порошков. Измельчение матери- алов – важная операция в про- цессе изготовления керамиче- ских изделий. От тонкости по- мола компонентов зависит пол- нота протекания различных реакций в процессе спекания керамики.
В зависимости от вида формуемых изделий (кирпич полусухого прессования, плитки для полов, огнеупорные изделия
Рис. 24. Схема структуры обожженного черепка полусухого прессования: 1 – глинистые агрегаты; 2 – жидкая фаза, цементи- рующая глинистые агрегаты контактным спеканием
итак далее) в настоящее время используют сухой и шликер- ный способ подготовки пресс-порошка.
Сухой способ применяют для однородной по составу одноцветной глины. Он заключается в дроблении комовой глины, ее сушке в сушильном барабане и дальнейшем из- мельчении с последующим рассевом на фракции. После ув- лажнения в смесителях до W = 8–9 % порошок вылеживается
инаправляется на формование. Форма зерен порошка остро- угольная, что способствует лучшему сцеплению частиц и по- вышению прочности прессовок. Однако такой способ подго- товки пресс-порошков имеет ряд существенных недостатков:
–при сушке глины изменяется ее грансостав. Мелкие фракции в сушильном барабане быстро высыхают и истира- ются в пыль, а крупные куски распариваются, слипаются
иокатываются в крупные комья. Глина после сушильного барабана неоднородна по влажности. В сушильных бараба- нах глину часто приходится пересушивать, чтобы избежать
еенеравномерной влажности, а затем вновь увлажнять в по- рошке. Для повышения качества сушки в сушильных бараба- нах иногда устраивают цепные завесы, которые частично разбивают комья глины, создавая условия для равномерной сушки глины;
81

– для помола используют стержневые мельницы, де- зинтеграторы, которые устойчиво работают при влажности глины до 10 %, иначе глина налипает на стержни мельницы или кожух и пальцы дезинтегратора.
Шликерный способ подготовки пресс-порошков приме- няют для глин неоднородных, загрязненных песчаными при- месями. Шликер – глиняная масса с влажностью 45–55 % – это суспензия, в которой хорошо смешиваются различные компо- ненты, в том числе неоднородные глины, тонкомолотые до- бавки и красители. При приготовлении суспензии сначала из- мельчают непластичные компоненты (шамот, кварцевый пе- сок, известняк) в шаровых мельницах мокрого помола с резиновой футеровкой для снижения шума. Если нельзя до- пустить помола металла, используют фарфоровые шары.
Глины, каолины распускают в глиноболтушках или пропеллерных мешалках с бассейном, чтобы поддерживать частицы шликера во взвешенном состоянии (рис. 25).
Рис. 25. Пропеллерная мешалка: а – мешалка в сборе с бассейном; б – устройство мешалки: 1– привод мешалки; 2 – картер;
3 – бассейн; 4 – рама; 5 – трехлопастной винт; 6 – вал
Мешалка – это вертикальный вал с трехлопастным вин- том на нижнем конце. Винт перемещает шликер вниз, масса ударяется о дно бассейна, а затем у стенок поднимается вверх
82
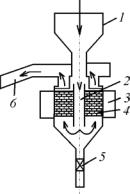
и вновь попадает на лопасти. Такое перемешивание постепенно приводит к измельчению кусков материала.
Готовый шликер перекачивают |
|
|
из пропеллерной мешалки на сито |
|
|
0,25 мм, чтобы удалить включения. |
|
|
Если в шликере присутствуют ме- |
|
|
таллические включения или желези- |
|
|
стые минералы (магнетит), то необ- |
|
|
ходимо пропустить суспензию через |
|
|
электромагнитный фильтр-сепаратор |
Рис. 26. Схема работы |
|
(рис. 26). |
||
электромагнитного |
||
Суспензию пропускают через |
||
фильтра-сепаратора: |
||
решетки с включенным электромаг- |
1 – воронка; 2 – трубка; |
|
нитом, а для очистки решеток его от- |
3 – кольцеобразный |
|
ключают и через открытую пробку |
электромагнит; |
|
4 – пакет решеток; |
||
удаляют включения. |
||
5 – пробка; 6 – отвод- |
||
Если в шликере много раство- |
||
ной лоток |
||
римых солей, тогда его обезвоживают |
|
на фильтр-прессе, получают коржи, которые вновь распус- кают в мешалках. Хранят шликер в емкостях, где проводится барботаж воздухом.
Для получения порошков из шликера используют рас- пылительные сушилки различных конструкций и производи- тельности (рис. 27).
Сушилка представляет собой цилиндрическую ем- кость с конусообразным днищем, диаметром 4,5–9 м, высо- той 6–16 м (высота конуса 2,7–8,6 м). На емкость сушилки навешивают вибратор и через каждые 15–20 часов его включают, чтобы очистить днище. Предохранительный клапан необходим для выброса пара при его избытке. Шли- кер поступает в сушилку через коллектор под давлени- ем 0,6 МПа. В верхней части сушилки имеется газовый кол- лектор и горелки, где создается температура 400 ° С. В зоне
83
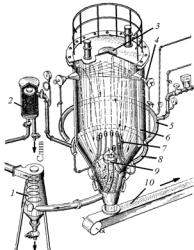
|
горелок из шликера, по- |
||||||
|
ступающего |
в |
верхнюю |
||||
|
часть башни, за счет про- |
||||||
|
гретого пространства и бы- |
||||||
|
строго |
высыхания |
ка- |
||||
|
пель |
суспензии образу- |
|||||
|
ется пресс-порошок в ви- |
||||||
|
де шариков |
влажностью |
|||||
|
6–7 %, который скатыва- |
||||||
|
ется |
по |
стенкам |
вниз |
|||
|
и выдается на |
конвейер. |
|||||
|
Порошок имеет округлую |
||||||
|
форму зерен и почти од- |
||||||
|
нофракционный |
состав, |
|||||
Рис. 27. Распылительная сушилка 525: |
что |
связано |
с |
размером |
|||
1 – циклон-промыватель; 2 – фильтр |
капель, задаваемым |
рас- |
|||||
очистки шликера; 3 – взрывной кла- |
пылительными устройст- |
||||||
пан; 4 – горелка, 5 – газовый коллек- |
|||||||
вами. Более мелкие пы- |
|||||||
тор; 6 – корпус; 7 – форсунка; |
|||||||
леватые |
частицы |
через |
|||||
8 – шликерный коллектор; |
|||||||
9 – вытяжной зонт; 10 – конвейер |
вытяжной зонт удаляют- |
ся в сборник, а затем воз- вращаются в сушилку, где они захватываются нормальными каплями суспензии. Порошок по конвейеру поступает на виб- росито 0,3–0,25 мм и далее в бункер для вылеживания.
К достоинствам данного способа получения порошка следует отнести:
–компактность и высокую производительность уста-
новки;
–быстрый запуск сушилки в работу;
–получение шарообразной формы частиц и оптималь- ного грансостава порошка;
–небольшое количество пыли и хорошая однородность порошка по влажности.
84
Из недостатков данного способа следует отметить:
–необходимость строительства высокого помещения для башни сушилки;
–расположение аварийного клапана неудобное (однако при нормальной работе схемы автоматизации оборудования он остается невостребованным).
Свойства пресс-порошков. Необходимо знать требо-
вания, предъявляемые к техническим свойствам пресс- порошков.
Степень измельчения, или зерновой состав пресс-
порошков, определяется размером и количеством присутст- вующих зерен. В зависимости от степени измельчения мине- ральных компонентов керамические массы делят на грубо-
зернистые и тонкозернистые.
В грубозернистых массах преобладают частицы разме- ром 0,5 мм и более. К тонкозернистым массам относят такие, где имеется значительное содержание частиц менее 0,1 мм. Пресс-порошки промежуточных размеров (0,1–0,5 мм) в тех- нологии керамики применяются крайне редко.
Грубозернистые массы используют в производстве грубой строительной керамики (плитки фасадные, плитки для полов, канализационные трубы, некоторые кислотоупор- ные изделия) и почти всех огнеупорных изделий. Отличи- тельной особенностью этих масс является малая уплотняе- мость при обжиге, низкая линейная огневая усадка – 3–5 %, хотя истинная пористость черепка должна составлять не ме- нее 10–15 %. Для отдельных фракций грубозернистых по- рошков задают допустимые пределы содержания их в массе. Нормируют содержание частиц от нескольких миллиметров до 1мм и от 0,1мм до 0,5 мм. Частицы менее 0,1 мм строго нормируются по содержанию.
Зерновой состав порошков подбирается из условия по-
лучения максимальной плотности прессовок. Соотношение крупной и мелкой фракций примерно 70:30, если мелкой
85
фракции меньше, то часть пустот крупной фракции не запол- нится. Если мелкой фракции больше, то «скелет» крупной фракции раздвинется, тем самым увеличится пустотность.
Крупные фракции (частицы размером более 0,75 мм) обладают большим сопротивлением, медленнее текут, хуже заполняют форму. Частицы размером 0,1–0,2 мм текут бы- стрее, частицы менее 0,1 мм – легкие, собираются в круп- ные (более 0,75 мм) агрегаты, комкуются, что уменьшает их текучесть.
Пыль – это частицы менее 0,06 мм – затрудняет прес- сование, но не всегда, так как при 10 % – ном добавлении к крупным фракциям (0,5–0,75 мм) увеличивают их теку- честь, поскольку пыль обволакивает крупные частицы, уменьшает трение, ведет себя как смазка.
Форма зерен частиц и характер их поверхности также имеет существенное значение. Остроугольные зерна снижа- ют сыпучесть (текучесть), но повышают силы внутреннего сцепления в прессованном полуфабрикате. Округлые зерна имеют гладкую поверхность, обеспечивают лучшее уплотне- ние и повышенную сыпучесть, но уменьшают силы внутрен- него сцепления.
Сыпучесть (текучесть, подвижность) – способность порошков заполнять форму под действием сил гравитации. Сыпучесть порошка можно определить по времени высыпа- ния порции порошка под действием собственной массы через отверстие диаметром 10 мм или косвенно, по углу естествен- ного откоса. Угол естественного откоса керамических по- рошков находится в пределах от 25 до 45о, с уменьшением угла естественного откоса сыпучесть резко возрастает. От сыпучести пресс-порошков зависит время и качество за- полнения пресс-формы, а также равномерность уплотнения порошка в форме. Если материал из-за плохой сыпучести «зависает» в форме при прессовании, то в прессовках появ- ляется неодинаковая плотность, что требует повышения дав-
86
ления прессования или увеличения времени прессования. В производственных условиях время заполнения форм со- ставляет около 1 с. От сыпучести порошка зависит также равномерность удаления воздуха из прессовок. Запрессо- ванный воздух приводит к появлению трещин в изделиях после обжига.
Сыпучесть зависит от зернового состава порошка, от формы зерен и шероховатости их поверхности, от влаж- ности, от содержания пыли и поверхностно-активных ве- ществ в пресс-порошке, от сил сцепления между частицами.
На сыпучесть (текучесть) влияет средняя плотность частиц. При повышенной плотности порошков (кварц, ша- мот) сыпучесть увеличивается, тяжелый порошок опускается быстрее, легче преодолевает сопротивление воздуха.
Влажность пресс-порошков меняется в широких преде-
лах и составляет обычно от 2–3 % до 10–14 %. Для увлажняе- мых водой пресс-порошков на основе глинистых материалов влажность составляет 6–14 %. Вода, как связка, обеспечивает проявление глинами пластических свойств, снижает давление прессования, уменьшает силы трения между частицами.
Глина в порошке увлажняется водой, что вызывает на- бухание глинистых частиц. Если порошки имеют частицы разных фракций, то они набухают неодновременно, что при- водит к неравномерности увлажнения, появляется рыхлая структура, а после сушки на поверхности прессовок возни- кают трещины.
При прессовании наблюдается отделение воды, кон- центрация влаги неравномерна, отсюда разноплотность прессовок.
При пониженной влажности пресс-порошка (5–8 %) на- блюдается неоднородность уплотнения изделий (для пластич- ных глин – больше, для тощих – меньше). При высокой влаж- ности пресс-порошка (13–16 %) наблюдается большая осадка порошка в форме.
87
Для порошков с высокой влажностью необходима дли- тельная сушка. Желательно порошок перед прессованием прогреть до температуры 70–90 ° С паром, тогда порошок бы- стрее набухает (в 3–4 раза), повышается его пластичность, снижается износ пресс-формы.
Насыпная плотность пресс-порошка зависит от истин-
ной плотности минерального вещества, от содержания тех- нологической связки (воды). В свободно насыпанных порош- ках объем минеральной части составляет от 30 до 45 %, доля воды – 5–15 %, а доля воздуха – 45–65 %. Поры, заполненные воздухом, при прессовании разрушаются, и за счет этого уменьшается объем материала.
3.2.1.2. Стадии формования изделий
Формование изделий происходит при прессовании и уп- лотнении пресс-порошка. При этом преодолеваются силы внутреннего трения между частицами, удаляется воздух, про- исходит связывание частиц между собой.
Уплотнение порошка можно рассматривать по отдель- ным стадиям.
Начало прессования (первая стадия) отмечается, когда твердые частицы перемещаются в направлении давления прессования, частично удаляется воздух, разрушаются круп- ные поры и мостики из частиц порошка, увеличивается кон- тактная поверхность, но отсутствует существенная деформа- ция зерен.
Следующая (вторая) стадия уплотнения отмечается при повышении давления прессования, когда возникает и увеличивается необратимая деформация частиц. При этом вода выделяется на контактную поверхность между части- цами и склеивает их. Воздух при сжатии частично вытесня- ется из прессовок, проходя между формой и пуансоном. Ос-
88
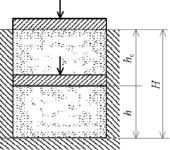
тавшийся в порошке воздух защемляется частицами, за- прессовывается и сжимается.
Третья (последняя) стадия уплотнения характеризуется максимальным уплотнением и хрупким разрушением частиц, которые измельчаются и хорошо сцепляются между собой, образуя большую поверхность соприкосновения. На данном этапе возникает упругая деформация удлиненных частиц в виде игл и пластинок. Упругая деформация таких частиц возникает при защемлении их другими частицами. Такие час- тицы изгибаются по схеме консольной балки или балки на 2 опорах. При прессовании воздух сжимается, а после оконча- ния прессования и освобождения изделия из формы происхо- дит его упругое расширение, достигающее иногда 8 %. За- прессованный воздух может вызвать трещины в прессовках. Желательно обеспечивать ступенчатое прессование для удале- ния воздуха.
Суммарный эффект уплотнения характеризуется ко-
эффициентом сжатия (Ксж):
|
|
Ксж = |
Н |
, |
(14) |
|
|
|
|||
|
|
|
h |
|
|
где Н – |
высота засыпки порошка в форму; |
|
|||
h – |
высота полученной прессовки. |
|
|||
Разница между |
высотой |
|
|||
засыпанного в форму порошка и |
|
||||
высотой полученной прессовки |
|
||||
называют осадкой (рис. 28). |
|
||||
Графическую зависимость |
|
||||
между осадкой и удельным дав- |
|
||||
лением |
прессования |
глиняного |
|
порошка при различной влаж- |
|
ности выражают компрессион- |
Рис.28. Схема к определению |
ными кривыми (рис. 29). |
понятия «осадка» |
89

Рис. 29. Зависимость между осадкой и удельным давлением прессования глиняного порошка при его влажности (в %): 1 – 0,001; 2 – 8,1;
3 – 11,15; 4 – 13,25; 5 – 15,95
Как видно, с увеличением давления и влажности осадка возрастает. Осадка интенсивно развивается в начале прессова- ния, затем начинает затухать и при достижении некоторого давления почти полностью прекращается. Это указывает на то, что для каждого порошка существует определенное давление, за пределами которого дальнейшего уплотнения прессовки не происходит.
Прессовое давление, приложенное к штампу, затухает в направлении толщины изделия. Перепады давления и плот- ности по толщине прессовки могут быть снижены введением пластифицирующих добавок, повышением влажности порош- ка, смазыванием и подогревом стенок пресс-формы. На равно- плотность прессовок большое влияние оказывает режим прес- сования. По направленности прессовых усилий различают прессование одностороннее и двухстороннее, по кратности приложения давления – однократное и многократное прессо- вание, по интенсивности приложения – ударное (механические
90