
книги / Термическая обработка и волочение высокопрочной проволоки
..pdfобласти. Для получения высоких свойств тянутой проволоки сле дует «избегать грубых выделений феррита, и, следовательно, в данном случае следует повышать температуру охлаждающей среды.
На большинстве заводов «понижают температуру охлаждаю щей среды с уменьшением содержания углерода и увеличением диаметра проволоки.
Такой принцип выбора температуры охлаждающей среды (патентировочной ванны) более правилен, так как охлаждение металла тонких и толстых сечений в расплаве протекает различ-
Рис. 5. Средние значения рекомендуемых температур охлаждающей среды — соли при патентировании прово локи, рассчитанные по фор
муле (6)
OJ Of 0,5 0,6 0,7 0,6 0,9 1,0
Содержание углерода,%
но. По мере уменьшения диаметра патентируемой проволоки про цесс превращения переохлажденного аустенита приближается к истинно изотермическому. Для того чтобы при толстых сечени ях проволоки температуру реакции у-+а приблизить к темпера турам реакции для тонких сечений, по мере утолщения диаметра патентируемой .проволоки следует понижать температуру охлаж дающей среды.
Среднюю температуру охлаждающей среды можно опреде лить по эмпирической формуле
tn= 490 + 60С — 15D. |
(6) |
Отклонение температуры ванны от значений, рассчитанных по формуле (6), на величину, не превышающую ±10°С, следует считать допустимым. Температуры ванны, рассчитанные по этой формуле, представлены в виде графика на рис. 5.
При патентировании проволоки из стали, выплавленной на машиностроительной шихте с повышенным содержанием оста-
точных элементов (марганец, хром, никель и др.), температуру соляной ванны следует поддерживать на верхнем пределе или даже несколько превышать его, особенно для пр,оволоки тонких диаметров.
5. ВЛИЯНИЕ РАЗЛИЧНЫХ ФАКТОРОВ НА ПРОДОЛЖИТЕЛЬНОСТЬ ПРЕВРАЩЕНИЯ ПЕРЕОХЛАЖДЕННОГО АУСТЕНИТА
|При патентировании продолжительность пребывания прово локи в охлаждающей среде должна быть более того времени, которое необходимо для завершения процесса превращения пе реохлажденного аустенита.
-Продолжительность изотермического превращения аустенита зависит от температуры охлаждающей среды. Каждой темпера туре ореды для данной стали соответствует определенная дли тельность изотермического превращения. По мере снижения тем пературы среды, начиная от Аги для углеродистых сталей вре- М1Я, необходимое для завершения распада аустенита, уменьшает ся и достигает минимума около 550—600 °С. Ниже 550 °С, вплоть до.точки М, время распада аустенита будет тем больше, чем ни же температура.
Все элементы, растворенные в аустените, за исключением ко бальта, в большей или меньшей степени способствуют увеличе нию продолжительности изотермического превращения аустени та. Кобальт уменьшает устойчивость аустенита при всех темпе ратурах переохлаждения.
Элементы, не образующие в стали карбидов (никель, медь, кремний, кобальт, алюминий), не меняют формы кривой инку бационного периода и конца распада аустенита, создавая мини мум его устойчивости в области 600—500 °С. Этот минимум сдвигается в область высоких температур элементами, повы шающими критические точки (кремний, алюминий, кобальт), или в область более низких температур элементами, снижающи ми эти точки (никель).
Карбидообразующие элементы (хром, вольфрам, молибден, ванадий, марганец) дают на кривой изотермического превраще ния аустенита два минимума с промежуточным максимумом устойчивости аустенита в области 600—:500°С.
Влияние легирующих элементов на кинетику распада пере охлажденного аустенита изучено Р. И. Энтиным [35], который указывает, что «малая скорость диффузии молибдена в аусте ните и пониженная вероятность перемещений атомов молибдена и углерода в определенном соотношении и являются, очевидно, причиной понижения скорости распада аустенита в этом случае и смещения температуры максимума скорости распада к мень шей величине переохлаждения. В промежуточной области тем ператур при распаде аустенита образуется цементит; диффузия молибдена и образование специальных карбидов исключается.
22
Влияние молибдена на скорость раапада аустенита .при этих ус ловиях не .наблюдается. Имеется основание (полагать, что выде ление доэвтектоиднопо феррита не связано с диффузионным пе рераспределением молибдена». И далее: «Легирование хромом «резко замедляет скорость полиморфного превращения железа, особенно при значительном переохлаждении. Вместе с тем в хромистых сталях так же, как и в молибденовых, в определенном интервале температур, на начальной стадии раапада аустенита, образуются специальные карбиды. Оба этих фактора — скорость диффузии xipoMa и образования специальных карбидов, а также скорость полиморфного превращения у-железа в а-железо — мо гут лимитировать общую скорость раапада аустенита».
Механизм влияния других карбидообразующих элементов (вольфрам, ванадий, марганец) на кинетику раапада аустенита в основных чертах подобен влиянию добавок молибдена. Леги рование никелем, как полагает Р. И. Энтин, понижает скорость раапада аустенита главным образом вследствие изменения ско рости полиморфного превращения, в частности работы образова ния центров кристаллизации a-фазы. Легирование кобальтом ускоряет превращение в основном вследствие повышения кри тических точек. Известную роль может играть и повышение ско рости полиморфного превращения.
С точки зрения практики патентирования углеродистых ста лей представляет интерес рассмотрение влияния на продолжи тельность превращения аустенита таких элементов, как углерод, марганец, хром.
Изменение содержания этих элементов в пределах, допу скаемых условиями поставки катанки, предназначенной для изготовления проволоки, .оказывает ощутимое влияние на про должительность превращения аустенита.
По мере увеличения содержания углерода до значения, рав ного эвтектоидному составу, продолжительность превращения аустенита увеличивается [36, 37]. Исследование Э. Г Горн [10] показало, что повышенное содержание марганца в значительной мере увеличивает продолжительность превращения переохлаж денного аустенита. При содержании марганца до 0,’о0% увели чение времени распада аустенита незначительно.
Влияние хрома на скорость превращения переохлажденного аустенита применительно к проволоке изучалось в ЦНИИЧМ и рядом исследователей [24, 38]. Из исследований следует, что даже незначительное изменение содержания хрома оказывает существенное влияние на продолжительность превращения пе реохлажденного аустенита. При повышении содержания хрома
с0,02 до 0,15% продолжительность распада аустенита возрастает
в10 раз — с 3 до 30 сек. [38] (эксперименты проводились на про волоке диам. 1,2 мм из стали 70).
Кроме химического состава стали, -на продолжительность раапада аустенита оказывают влияние и другие факторы.
В работах К. П. Колчина [38] и ЦНИИЧМ показано, что «при равных температурах охлаждающей среды продолжительность превращения переохлажденного аустенита увеличив1аетоя «по мере уменьшения диаметра проволоки, так как в этом случае
истинная температура превращения приближается к температу ре ванны.
С. С. Штейнберг впервые еще в 1926 г. высказал мысль о том, что зародышевые центры при «превращении аустенита в фер ритоцементную структуру образуются в первую очередь по границам зерен аустенита, поэтому естественно ожидать, что скорость превращения аустенита зависит от величины зерна [3*9].
В одной из своих работ И. Л. Миркин экспериментально по казал, что аустенит крупнозернистой стали более устойчив, чем аустенит той же стали, но с мелким зерном [40].
В. Я. Зубов [10] пришел к выводу, что продолжительность превращения переохлажденного аустенита у крупнозернистой стали в 2—2,5 раза больше, чем у мелкозернистой, Перегрев стали особенно увеличивает продолжительность превращения переохлажденного аустенита за очет инкубационного периода
вкрупнозернистой стали.
И.Л. Миркин [41] установил, что по мере увеличения тем пературы нагрева уменьшается скорость зарождения эвтектоидных зерен и скорость их роста. Он указывает, что обнаруженное явление можно объяснить ростом величины аустенитного зерна, увеличением однородности концентрации углерода в различных точках и участках, а также растворением инородных-включений.
Признавая влияние каждого из перечисленных, факторов, И. Л. Миркин придает первостепенное значение второму факто ру, указывая, что энергия твердого раствора понижается с уве личением статической однородности его концентрации, и поэто му реакции в нем должны происходить с уменьшенной ско ростью, что в действительности и наблюдается в отношении ско рости роста эвтектоидньих зерен.
Впоследствии И. Л. Миркин [42] из результатов эксперимен тов и расчетов пришел к выводу, что время изотермического распада аустенита при температурах ванны ниже 500 °С практи чески не зависит от предварительного нагрева. Расчетным путем получено, что время изотермического распада в стали, подвергав шейся высокому нагреву, отличается от времени распада аусте нита в стали с незначительным нагревом только на 10—25%, если температура ванны ниже 500 °С, тогда как при темпера турах ванны выше 550 °С у перегретой стали процесс превраще ния в 2—3,5 раза продолжительнее -по сравнению с низкотем пературным нагревом.
Данные табл. 3 [43] иллюстрируют влияние температуры на грева на продолжительность распада переохлажденного аустени та при различных температурах охлаждающей среды.
|
|
|
|
Т а б л и ц а |
3 |
|
Продолжительность превращения переохлажденного аустенита крупнозернистой |
||||||
|
стали |
[43] |
|
|
|
|
|
Продолжительность превращения |
аустенита |
Увеличение продолжи |
|||
Температура |
в секундах при нагреве, |
®С |
тельности |
превраще |
||
свинцо |
|
|
ния аустенита при |
на |
||
вой ванны, °С |
|
|
греве на |
950 сС |
по |
|
|
810 |
950 |
отношению к нагреву |
|||
|
на 810 °С. % |
|
||||
540 |
2,0 |
з,о |
50,0 |
|
||
510 |
3.0 |
3,5 |
16,5 |
|
||
480 |
5,0 |
5,0 |
0,0 |
|
||
450 |
7,0 |
7,5 |
7,0 |
|
||
420 |
10,0 |
12,5 |
20,0 |
|
т
|
|
|
/40 |
|
|
|
г |
|
|
|
|
|
|
|
|
|
|
|
|
|
|
|
|
|
|
|
120 |
|
|
|
1 |
|
|
|
|
|
|
|
|
|
|
1 |
|
|
|
|
|
|
|
|
|
|
|
|
|
|
|
|
|
|
|
|
100 |
|
|
|
1 |
|
|
|
|
|
|
|
|
|
|
1 |
|
|
|
|
|
Рис. 6. |
Время пребывания |
про |
|
|
|
) |
|
|
|
|
|
О? 80 |
|
|
|
|
|
|
|
||||
волоки в патентировочной |
ван |
|
|
|
/ |
|
|
|
|
||
|
|
у |
/ |
|
|
|
|
||||
|
не: |
|
«I 60 |
|
|
|
|
|
|
|
|
1 — принятое на различных |
заво |
|
|
|
|
/ |
/ |
|
|
||
дах: 2 |
— рекомендуемое по |
Фор |
|
|
|
|
|
|
|
|
|
40 |
|
|
|
V • s |
|
|
|
||||
|
муле (7) |
|
|
/ |
|
|
|
|
|
|
|
|
|
20 |
|
|
|
|
|
|
|
|
|
|
|
|
/ |
|
|
|
|
2 |
|
|
|
|
|
|
|
|
|
|
|
|
|
||
|
|
|
— |
" |
|
|
|
|
|
|
|
|
|
|
О |
|
|
|
Î |
|
|
|
|
|
|
|
1 |
2 |
3 |
4 |
5 |
6 |
7 |
0 |
9 |
|
|
|
|
|
|
Диаметр, мм |
|
|
|
На действующих патентировачных агрегатах отношения дли ны 'печи к длине ванны и скорости патентирования приняты та кими, что врейя пребывания проволоки в охлаждающей среде увеличивается при увеличении диаметра проволоки (рис. 6).
Данные исследований, проведенных в ЦНИИЧМ, показыва ют, что при рекомендуемых температурах охлаждающей среды — соли (рис. 5) — превращение переохлажденного аустенита за капчивается в течение 4—S сек. (табл. 4).
На основании исследований и практики работы заводов ми нимально необходимое время пребывания проволоки в ванне, обеспечивающее превращение переохлажденного аустенита для углеродистых сталей может быть принято равным 15 сек., т. е.
г' = 15 сек. |
(7) |
Это «время предусматривает некоторый избыток пребывания проволоки в ванне с тем, чтобы при ликвации элементов в стали и специфических особенностях отдельных плавок процесс превра щения переохлажденного аустенита заканчивался в пределах
Т а б л и ц а 4
бремя распада переохлажденного аустенита в стальной проволоке в расплаве селитры, имеющем температуру, рекомендуемую для патентирования
прово |
|
Диаметр |
локи. мм |
1.0
2.0
3,0
4,0
5,0
6,0
7.0
Продолжительность превращения переохлажденного аусте нита, сек., для сталей различных номеров плавок при со держании элементов, %
Температура селитры,°С |
1732б|2 1499 3409 |
6616 |
46225 |
17332 36019 47081 |
46017 |
|||||
0,40 С; 0.09 Сг |
0,48 С; |
0,04 Сг |
0,4 8 С; 0,04 Сг |
0,62 С; 0,04 Сг |
0,63 С: 0,05 Сг |
0,65 С; 0,13 Сг |
0 70 С; 0,02 Сг |
0,77 С; 0,1 0 Сг |
0,83 С; 0,04 Сг |
|
5254-500 |
СО 1 |
О) |
1 00 |
оо 1 со |
6 |
|
8 |
4 - 6 |
4—6 |
6 - 8 |
500 |
8 |
|
4 |
___ |
4 |
— |
4—6 |
6 |
4 - 6 |
|
475 |
6 |
|
4 |
4 |
4 |
6 |
8 |
— |
— |
— |
сл + СЛ О |
6 |
|
СО 1 |
4 |
— |
— |
— |
— |
— |
— |
450 |
8 |
|
4 |
4 |
6 |
4 |
— |
4 |
4 |
4 |
450-4-425 |
___ |
|
4 |
4 |
4 |
— |
8 |
4 |
— |
4 |
•425 |
— |
|
— |
— |
— |
— |
— |
со 1 |
6 |
— |
| Среднее значен
6,0
5,6
5,3
5,0
4,8
4,7
5,3
Среднее |
— |
6,3 5,0 5,0 4,7 4,7 7,0 |
4.7 5,0 |
5,2 |
^ 5 ,3 |
|
начение |
||||||
|
|
|
|
|
||
П р и м е ч а н и я : |
1. Плавка № 21499 Макеевского завода . плавки № 3409 |
и 6616 |
||||
Магнитогорского комбината, остальные плавки завода, сСерп и |
молот*. 2. |
Содержание |
||||
марганца во всех плавках не более 0,60%. |
|
|
|
ванны. На рис. 6 минимально -необходимое время пребывания проволоки в охлаждающей среде показано сплошной линией.
Если аустенит даже частично не успеет превратиться в ванне в сорбит, нераспавшийся .переохлажденный аустенит будет рас падаться на мартенсит или троостит. Получение той или иной из указанных структур будет обусловливаться скоростью охлаж дения проволоки по выходе ее из ванны. Наличие в структуре проволоки участков мартенсита и троостита не допустимо.
Увеличивать время пребывания проволоки в ванне сверх 15 сек. нет необходимости даже при патентировании высокоугле родистой стали, так как при -повышении содержания углерода приходится снижать температуру нагрева -проволоки и повышать температуру охлаждающей среды в соответствии с формулами
(1) и (6). Таким образом, в обоих случаях создаются предпо сылки для сокращения продолжительности превращения переох лажденного аустенита. Из данных табл. 4 следует, что при реко мендованных температурных режимах патентирования повыше ние содержания углерода практически не оказывает влияния на продолжительность превращения аустенита.
Данные табл. 3 показывают, что при крупнозернистой стали даже при .повышенных температурах нагрева время. 15 сек. до статочно для того, чтобы превращение аустенита завершилось в пределах ванны -с охлаждающей средой.
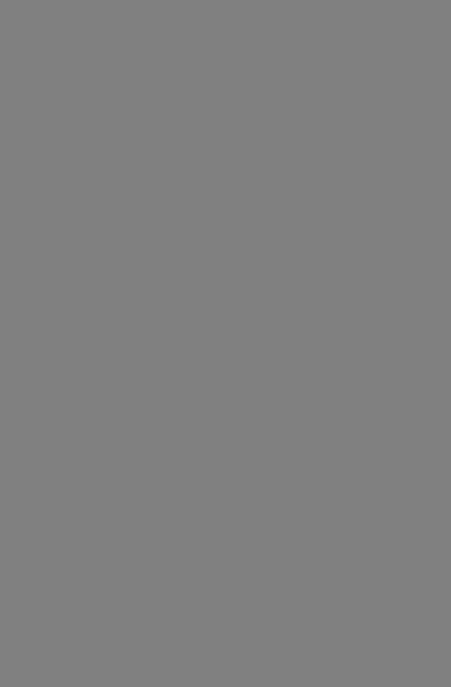
5 > /40 |
|
5,0мм |
^ □ |
|
I т |
|
|||
|
V |
|
||
i'120 |
|
г- |
|
|
s. |
|
> / и |
|
|
I |
wo |
—2,3мм |
|
|
|
|
|
||
! |
90 |
|
|
|
|
600,39 |
0M6 0J52 0,56 |
0,630,65 |
0,630# |
|
|
Содержаниеуглерода,% |
|
Рис. 8. Предел прочности патентированной за готовки диам. 5,0 и 2,3 мм в зависимости от
содержания |
углерода: |
— — — — фактический; |
---------- — по форму |
ле |
(8) |
|
т |
0,63% с |
----------- -- |
|||
|
130 |
|||||
|
|
|
|
|
|
|
|
т |
0,63Я с |
Р |
_____: |
||
|
но |
|||||
|
0.56%С____ |
|
|
|
||
|
too |
|
|
_______ |
||
|
90 |
о,зэ%с |
||||
I |
|
|
|
|||
so |
|
3,9 |
3,0 |
|
2Д |
|
|
S,о |
|
|
|||
|
т |
|
|
|
|
_ —' —ч |
|
O.S5% С |
1 |
__________ - r - J |
|||
[130 |
|
|
|
|
|
|
' |
120 |
|
_ _ |
|
н- — ““ —4 |
|
|
0,65% С |
|
|
|
||
|
110 — — ^ |
|
|
|
|
|
|
100 |
0fi6% C |
|
|
|
|
|
90 |
|
г |
3,0 |
|
|
|
5,0 |
|
3,9 |
2Д |
1.6 |
Диаметр,мн
Рис. 9. Предел прочности патентированной за готовки стали в зависимости от диаметра про волоки:
— — — — фактический; |
--------------- — по Форму |
ле |
(8) |
ванной заготовки, обеспечивающего достаточно высокие свойст ва проволоки после волочения [44, 45],
Cj, = 100С—D -j- 53 кгIмм2. (S)
На рис. 8 и 9 приведены данные (сходимости расчетного зна чения предела прочности с фактическим.
«Предел прочности 'патентированной заготовки, рассчитанный по формуле (8), несколько отличается от значения, рассчитанно го по рекомендованной автором ранее формуле, которая была разработана на основе практики работы завода «Серп и молот» при ,патентиров(ании в свинце [46].
Для подсчета .предела прочности патентиров«анной проволо ки имеются формулы и других авторов [47, 48].
ВЛИЯНИЕ РАЗЛИЧНЫХ ФАКТОРОВ НА СКОРОСТЬ ПАТЕНТИРОВАНИЯ
Для получения необходимой структуры и предела прочности патентароваиной заготовки необходимо также правильно выб рать скорость патентарования, которая определяет производи тельность патентировочных агрегатов и качество готовой про волоки.
Скорость патентарования [49] зависит от многих факторов: от химического состава стали, диаметра патентируемой проволоки, типа и длины печи, способа обогрева металла,
распределения температур по длине печи, заданной температуры нагрева проволоки, длины ванны,
состава и температуры охлаждающей среды и др.
Литературные данные по вопросу выбора скорости патентирования ограничиваются либо описанием последствий непра вильно выбранной скорости патентарования, либо приведением скоростей патентарования, применяемых на тех или иных заво дах, без анализа взаимосвязи между скоростью патентарования и факторами, влияющими на нее. Ряд исследователей (напри мер, [33]) рассматривает этот вопрос только с точки зрения пре вращения .переохлажденного аустенита, не связывая его с технологией нагрева проволоки в печи и производительностью патентировочных агрегатов, а также назначением и целесооб разностью наличия зон в печах.
Вследствие того что некоторые основные положения, связан ные с патентированием проволоки, еще не разработаны или разработы и освещены недостаточно, наблюдается непроизводи тельное использование патентировочных агрегатов. Эти обстоя тельства привели к выводу о необходимости аналитического ис следования взаимосвязи между скоростью патентарования и факторами, лимитирующими ее [49ч-51].