
книги / Подготовка полуфабрикатов для получения бумаги
..pdf
Скорость вращения ротора выбирается в зависимости от вида волокнистого материала и места установки мельницы в технологическом потоке.
Окружная скорость ротора по его среднему диаметру у мельниц составляет у разных конструкций от 8 до 22 м/с и более. У мельниц, работающих при малой окружной скорости ротора (8–14 м/с), укорачивание волокон происходит в большей степени, чем у мельниц, работающих при более высокой окружной скорости ротора (более
16 м/с).
Мельницы МКН используются в основном для размола, при котором происходит большее или меньшее укорачивание волокон.
Гидрофайнер – коническая мельница с литой гарнитурой (рис. 12). Основное назначение гидрофайнера – гидратация волокон при минимальном их укорачивании. Этим и определяются различия в условиях работы и в конструктивных особенностях указанных конических мельниц.
Рис. 12. Схема гидрофайнера: 1 – ротор; 2 – статор; 3 – присадочное устройство; 4 – муфта сцепления; 5 – крыльчатка
Очевидно, что для уменьшения режущего действия ножи гидрофайнера должны быть толще, чем у мельницы МКН. Они и имеют у гидрофайнера толщину 8–16 мм и не являются съемными, а выфрезерованы в литой ножевой рубашке статора и ротора. Применяемое удельное давление размола при работе гидрофайнера ниже, чем при работе мельницы МКН. Ротор гидрофайнера имеет окружную
41
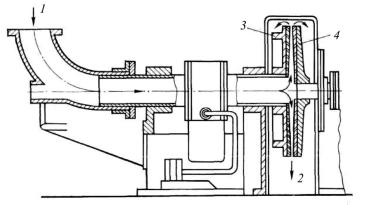
скорость, достигающую до 24 м/с и более. Концентрация массы, поступающей в гидрофайнер, выше, чем при поступлении в мельницу МКН, и составляет 4–6 %. Для обеспечения надлежащего прохода массы повышенной концентрации на валу гидрофайнера имеется крыльчатка.
В мельницах, имеющих наборную гарнитуру, ножи устанавливаются в выфрезерованные пазы и расклиниваются деревянными планками.
Мельницы МКБ имеют чугунный статор с набором базальтовых ножей и ротор из монолитного базальта. Применяются для получения массы очень высокой степени помола.
Дисковые мельницы. По конструктивным особенностям мельницы делятся на однодисковые (имеют два диска, один из которых вращается, другой неподвижен) (рис. 13), двухдисковые (оба диска вращаются в противоположных направлениях) (рис. 14), сдвоенные или трехдисковые (вращается средний диск, два крайних неподвижны) (рис. 15), многодисковые (две или три пары дисков, один в паре не вращается). Последние используются очень редко из-за сложности конструкции. В производстве бумаги обычно используют однодисковые и сдвоенные мельницы (схемы работы – рис. 16).
Рис. 13. Схема дисковой мельницы: 1 – вход массы; 2 – выход массы; 3 – статор; 4 – вращающийся диск
42
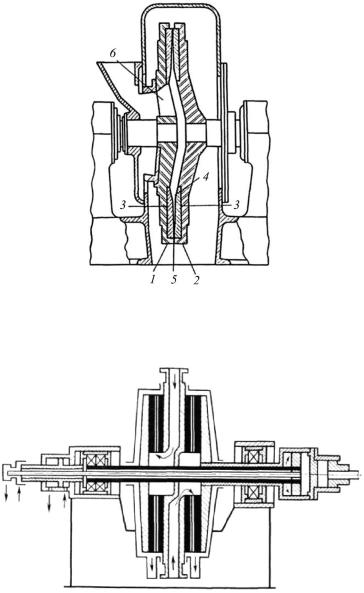
Рис. 14. Двухдисковый рафинер Бауера: 1 и 2 – вращающиеся диски; 3 – рабочая часть дисков; 4 – вход массы; 5 – выход массы;
6 – поступление массы в рафинер
Рис. 15. Схема одной из конструкций сдвоенных дисковых мельниц
43

Рис. 16. Схемы работы однодисковой и сдвоенной мельниц: 1 – вход массы; 2 – корпус; 3 – неподвижный диск; 4 – вращающийся диск; 5 – электродвигатель; 6 – выход массы
Однодисковые мельницы выпускают в трех исполнениях: с камерой, работающей под давлением до 0,6 МПа; с усиленной камерой, работающей под давлением 2,4 МПа и при температуре массы до 190 °С; с камерой, в которую масса подается шнековым питателем. Последний тип мельниц применяется для размола массы при высокой концентрации (рис. 17).
Рис. 17. Дисковая мельница серии МД с винтовой подачей массы: ВП – винтовой питатель; ПМ – поступление массы; ВМ – выход массы
44
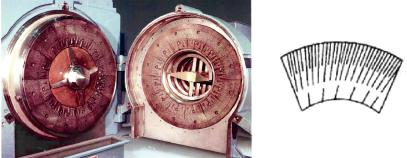
Размольные диски выполняются в виде цельного размольного кольца или в виде отдельных сегментов, изготовленных из стали
(рис. 18).
Рис. 18. Поверхности дисков рафинера
Количество таких сегментов чаще 6. Они крепятся к диску с помощью болтов. Канавки в дисках располагаются кольцевыми рядами с разным углом наклона, разной ширины. При сильном износе кромок ножей осуществляется проточка дисков. Срок службы гарнитуры от двух недель до 1,5 лет.
Сдвоенные мельницы работают при давлении не более 0,6 МПа. Размалывающая поверхность такой мельницы вдвое больше, чем однодисковой. Присадка осуществляется за счет диска, не связанного с электродвигателем. Средний диск – «плавающий», он свободно скользит по валу и занимает всегда среднее положение между крайними дисками.
Преимущества использования дисковых мельниц по сравнению
сконическими заключаются в следующем:
–расход энергии на размол ниже на 15–25 %;
–лучше осуществляется гидратация и фибриллирование волокон, что увеличивает прочность бумаги;
–легче проводится ремонт и смена дисков;
–возможна организация размола при высокой концентрации
массы;
–дисковые мельницы более долговечны и надежны в работе.
45
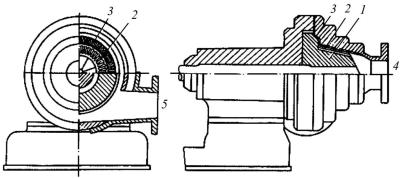
Другие типы размалывающих устройств. Имеется ряд уст-
ройств, занимающих промежуточное положение между гидроразбивателями и мельницами. Они применяются в основном для роспуска брака, макулатуры, легкого размола волокнистых полуфабрикатов с целью активации поверхности волокон.
В этих аппаратах используется принцип высокочастотных механических колебаний. При этом эффективно разделяются пучки волокон, волокно частично фибриллируется и гидратируется. Укорачивающее действие практически отсутствует. Примерами таких аппаратов могут служить: энтштиппер (см. рис. 8), супратонатор
(рис. 19) и др.
Супратонатор по своей конструкций напоминает комбинацию конической мельницы и дискового рафинера. Он состоит из короткого конического ротора с большой конусностью, который у широкого конца переходит в плоский диск, и статора такой же формы. На конической части ротора и статора имеются продольно выфрезерованные ножи толщиной 1,5 мм и высотой 3 мм, как у гидрофайнера, на внутренней же поверхности дисков имеется 300 очень узких радиальных канавок, более широких и прямых на статоре и сходящих на нет на роторе. Ротор приводится во вращение от двигателя со скоростью 3000 и 4000 об/мин и работает с постоянным зазором между дисками 0,5 мм, который устанавливается при помощи винта.
Рис. 19. Супратонатор: 1 – ротор; 2 – статор; 3 – дисковая часть аппарата; 4 – поступление массы; 5 – выход размолотой массы
46
Волокнистая масса поступает в супратонатор с узкого конца по трубе, проходит через коническую часть и далее выбрасывается в дисковую часть аппарата, где, попадая в канавки, испытывает быстро сменяющиеся воздействия сжатия и разрежения с частотой 15 кГц, т.е. близкой к частоте ультразвука, в результате которых волокно фибриллируется, а пучки волокон разделяются на волокна.
Для подачи массы на супратонатор не требуется насоса, так как вследствие большой высоты всасывания (до 6 м) и нагнетания (до 12 м) аппарат может забирать массу из бассейна самостоятельно
иподавать обработанную массу в другой бассейн на значительную высоту.
Аппарат компактен и высокопроизводителен. Оптимальная концентрация массы при размоле 4–5 %, однако он может работать
ипри концентрации в пределах 2–8 %. Предназначается супратонатор главным образом для размола макулатуры. При двух-, трехкратном пропуске через аппарат масса целиком освобождается от узелков и пучков. Расход энергии примерно в 2–3 раза ниже, чем других аппаратов непрерывного и периодического действия. Супратонатор нашел применение также и для размола целлюлозы при выработке впитывающей и пухлой бумаги (салфеточной, туалетной и др.).
6.3. Размол целлюлозы в воздушной среде
Размол волокон целлюлозы в воздушной среде, в отличие от обычного широкораспространенного размола в водной среде, получил также название сухого размола. Вода способствует набуханию растительных волокон, их последующему фибриллированию и получению готовой бумаги с достаточно высокими показателями сомкнутости структуры и механической прочности. Все факторы, благоприятствующие набуханию волокон: понижение температуры производственной воды, создание щелочной среды, наличие в волокнах повышенного содержания гемицеллюлоз (легко набухающей фракции технической целлюлозы), их расположение в волокнах, доступное к действию воды, и др. – все это обеспечивает условия для получения сомкнутой и прочной бумаги.
47
Однако у фильтрующих и впитывающих видов бумаги структура бумажного полотна не должна быть сомкнутой. Более того, для создания необходимых потребительских свойств эти виды бумаги должны обладать нужной степенью пористости. Жесткость для некоторых из них, например салфеточной бумаги, нежелательна, и межволоконные силы связи в такой бумаге должны быть ограничены.
Отсюда понятно, что при выработке подобных видов бумаги целесообразно исключить факторы, вызывающие гидратацию волокон, и в первую очередь воду – основной фактор гидратации. Сказанное является предпосылкой для применения при выработке пористых видов бумаги размола волокон в воздушной среде.
В то время как при размоле в водной среде увеличение интенсивности размола с сокращением длины размалываемых волокон приводит к увеличению степени помола массы и замедлению процесса ее обезвоживания, при размоле волокон в воздушной среде с их укорочением наблюдается обратное явление: уменьшение степени помола волокон и ускорение процесса их обезвоживания.
При размоле воздушно-сухих волокон целлюлозы в дисковой мельнице уменьшением величины зазора между дисками мельницы можно осуществить регулируемое укорачивание волокон, сопровождаемое соответствующим ростом их удельной поверхности с приданием им повышенной садкости и скорости обезвоживания при одновременном снижении водоудерживающей и связеобразующей способностей волокон.
Установлено, что в процессе размола сухих волокон происходит термомеханическая их деструкция, сопровождаемая комплексом физико-химических изменений в их структуре и свойствах: снижается содержание α-целлюлозы в размалываемых таким образом хлопковых волокнах, повышается их истинная плотность с уменьшением объема пор, наблюдается вследствие перегрева волокон их дегидратация, происходит разрыв химических связей с образованием карбонильных групп, значительно снижается степень полимеризации целлюлозы и увеличивается отрицательное значение ее электрокинетического потенциала, одновременно повышаются адсорбционная и реакционная способности целлюлозы.
48
Применение сухого размола целлюлозы в производственных условиях себя оправдало при изготовлении фильтрующих волокнистых материалов обычного формования из водной среды. Такие материалы из целлюлозы, подвергнутой размолу в воздушной среде, обладают монодисперсной пористой структурой с высокой и стабильной величиной объемов крупных макропор, практически не зависящей от интенсивности процесса размола исходных волокон.
Была установлена возможность совокупного применения волокон, размолотых в воздушной среде, с волокнами, размолотыми в водной среде. При этом волокна сухого размола играют роль активных порообразующих компонентов, а размолотые в водной среде – упрочняющих компонентов полотна, одновременно снижающих его пористость. Подобная технология при необходимом соотношении тех и других волокон позволяет целенаправленно регулировать пористость, структурно-фильтрационные свойства и показатели фи- зико-механических свойств фильтрующих материалов обычного формования из водной среды.
7.ПРОКЛЕЙКА БУМАГИ
7.1.Назначение процесса проклейки и его контроль
Проклейку бумаги осуществляют для придания ей водостойкости. При этом снижается впитывающая способность бумаги и увеличивается пригодность бумаги для письма и печати. Некоторые вещества, введенные в бумажную массу, придают ей водостойкость (гидрофобность), другие – кроме водостойкости – механическую прочность, т.е. обладают связывающей способностью.
К первой группе относятся канифольный клей, дисперсия парафина и другие гидрофобизирующие вещества.
Ко второй группе относятся крахмальный клей, животный клей, натриевая соль карбоксиметилцеллюлозы и др. Они гидрофильны и эффект проклейки достигается за счет образования сомкнутой структуры бумаги, так как эти вещества обладают сродством к цел-
49
люлозе и связывают волокна между собой. Вследствие этого наблюдается увеличение показателей механической прочности бумаги.
Имеются вещества, которые можно отнести к первой и второй группам, так как они обладают и гидрофобизирующими и связывающими способностями, например, латексы.
Различают два способа проклейки:
1.Проклейка в массе, когда проклеивающие вещества вводятся
вбумажную массу.
2.Поверхностная проклейка, когда проклеивающими веществами обрабатывается поверхность готовой бумаги.
При поверхностной проклейке проклеивающие вещества в виде растворов, дисперсий, эмульсий наносят с одной или обеих сторон полотна бумаги. В этом случае бумага подвергается обработке клеящими веществами лишь с поверхности, а в толще листа остается непроклеенной.
Осуществляется поверхностная проклейка в сушильной части машины на клеильном прессе. При этом проклеивающее вещество образует на поверхности бумаги сплошную пленку, препятствующую проникновению воды. Поверхностная проклейка применяется для документной, чертежной, рисовальной бумаги.
Проклейка в массе осуществляется путем введения дисперсий и растворов проклеивающих веществ в волокнистую суспензию перед отливом бумаги на бумагоделательной машине. При этом проклеивающие вещества распределяются по всей толщине бумаги.
Наиболее распространенным веществом для проклейки бумаги
вмассе является канифольный клей.
Эффект проклейки зависит от гидрофобности частиц клея, от равномерности их распределения в бумаге, от степени дисперсности частиц.
Степень проклейки зависит от природы жидкости, так как скорость проникновения жидкости в бумагу, например чернил, зависит от их вязкости и сил поверхностного натяжения.
По степени проклейки различают следующие виды бумаги:
– сильноклееные – расход канифоли 1,5–4,0 % от массы волокна (писчая, тетрадная, фотоподложка, картографическая и др.);
50