
книги / Технологические остаточные напряжения и их влияние на долговечность и надёжность металлоизделий
..pdf
При деформации в несколько переходов степень деформации суммируется по переходам, тогда для многопереходного деформирования после преобразований находим предельную вытяжку из условий опасности последеформационного разрушения прутка от остаточных напряжений.
|
1 |
|
|
п |
|
4 |
|
|
|
|
|
λ = exp |
|
|
− |
|
|
|
tg α |
, |
(3.9) |
||
* |
* |
|
|
3 |
|||||||
|
6ψ µ |
3 |
|
|
|
|
|
||||
где п – количество переходов; |
* |
|
(1−µ−µ2 ) |
|
|
||||||
µ = |
|
1−µ2 |
|
|
– параметр, опреде- |
ляющий влияние коэффициента Пуассона.
а
б
Рис. 3.5. Расчетные зависимости суммарной вытяжки:
µ = 0,5, ψ* = 0,15 (а); µ = 0,3, ψ* = 0,25 (б)
121
Таким образом, соотношение (3.9) позволяет найти в зависимости от геометрии инструмента и физико-механических свойств материала предельно допустимую вытяжку из условия сохранения прочности от остаточных напряжений. На рис. 3.5 приведены расчетные зависимости допустимой вытяжки от угла α технологического во-
лочильного инструмента для различных ψ* и п [14, 15].
Из рис. 3.5 следует, что с увеличением α суммарная допустимая вытяжка уменьшается. Увеличение ψ* также приводит к снижению λ , что объясняется зависимостью комплексного параметра от механических свойств материала.
Предложенная методика позволяет подбирать технологические параметры с целью минимизации остаточных напряжений и недопущении разрушения прутковых заготовок при деформировании.
3.3. Технологическая прочность при деформировании труб
Определение предельных режимов деформирования труб из условий предотвращения последеформационного разрушения от остаточных напряжений также представляет интерес. При этом опасными с точки зрения разрушения принимаются остаточные напряжения, действующие в поверхностных – наружном (r = R1 ) и внутреннем
(r = R2 ) – слоях трубы, где радиальные напряжения – нулевые, а ок-
ружные и осевые остаточные напряжения являются растягивающими и принимают максимальные значения.
Согласно выражениям (2.44)–(2.46) соотношения для определения остаточных напряжений принимают вид:
для внешней поверхности при r = R1
σr |
= 0, |
|
|
|
|
|
|
|
|
|
|
|
|
σθ = а0R1 (R1 − R2 ), |
(3.10) |
|||||
σ |
z |
= а |
µR |
(R |
− R ) |
|
|
0 |
1 |
1 |
2 |
|
122
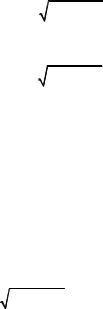
и внутренней поверхности трубы при r = R2
|
|
= 0, |
|
|
|
|
|
|
|
σr |
|
|
|
|
|
|
|
||
|
|
|
|
(R 2 − R1 ), |
(3.11) |
||||
σθ = а0R 2 |
|||||||||
|
|
= а |
µR |
2 ( |
|
|
− R |
1 ) |
|
σ |
z |
R |
2 |
. |
|||||
|
0 |
|
|
|
|
Используя выражения (3.10) и (3.11) с учетом формулы (3.2), определяем интенсивность напряжений в поверхностных слоях тру-
бы [16]:
для наружной поверхности
σi = а0R1 (R1 − R 2 ) 1−µ+µ2 |
(3.12) |
и внутренней поверхности
σi = а0 R 2 (R1 − R 2 ) 1−µ+µ2 . |
(3.13) |
Из соотношений (3.12) и (3.13) следует, что интенсивность остаточных напряжений растет с увеличением толщины стенки трубы, определяемой разностью R1 − R2 , т.е. для толстостенных труб веро-
ятность разрушения от остаточных напряжений более высокая. При этом максимальная интенсивность напряжений соответствует наружной поверхности.
Для оценки опасности разрушения трубной заготовки от остаточных напряжений используем условие прочности по удельной энергии формоизменения (3.1) с учетом равенства σs = σв.
а R2 |
(1− |
|
) |
1−µ+µ2 ≤ σ |
|
. |
(3.14) |
R |
s |
||||||
0 1 |
|
|
|
|
|
|
Подставляя значение параметра a0 в соответствии с соотношением (2.51) в неравенство (3.14), получим
123

|
|
|
|
|
|
|
|
|
|
|
n |
|
|
|
|
|
|
|
|
|
60ε |
1 |
+ |
|
mεср |
|
|
|
|
|
|
|
|
|
|
|
|
|||||||
|
|
|
|
|
|
|
ср |
|
|
|
(n +1) |
|
|
|
|
|
|
* |
|
* |
|
|
|
|
|
|
|
|
|
(1− R) ψ |
µ |
|
|
|
|
≤1. |
(3.15) |
|||||||
|
|
|
|
|
|
|
|
|
||||||
|
|
|
|
B |
|
|
||||||||
|
|
|
|
|
|
|
|
|
|
|
|
После преобразований с учетом выражения (1.39) определяем соотношения ddд для случаев жесткопластической среды без упрочнения (m = 0) и с линейным упрочнением (n = 1), соответственно:
|
|
B |
|
|
2(1− R3 )tgα |
|
|
|
|
||||||||
d dд = exp |
|
− |
|
|
|
|
|
|
|
|
, |
|
(3.16) |
||||
|
|
|
|
|
|
|
|
||||||||||
|
120ψ* (1− R)2 µ* |
|
|
|
3 3 (1− R |
2 |
|
|
|
|
|
|
|||||
|
|
|
|
|
|
|
) |
|
|
|
|
||||||
|
−1+ 1+ |
mB |
|
|
|
|
|
|
|
|
|
|
|
|
|
|
|
|
|
|
|
|
|
|
|
|
|
|
|
|
|
|
|
|
|
30ψ* (1− R) |
2 |
µ* |
|
|
|
|
|
|
|
|
|
|
|||||
|
|
|
|
|
|
|
|
|
|
||||||||
|
|
|
|
|
|
2(1− R3 )tgα |
|
||||||||||
d dд = exp |
|
|
|
|
|
|
− |
|
|
|
|
|
|
|
|
. |
(3.17) |
|
|
|
|
|
|
|
|
|
|
|
|
|
|
||||
|
|
2m |
|
|
|
|
|
3 3 (1 |
− |
R |
2 ) |
|
|||||
|
|
|
|
|
|
|
|
|
|
|
|
|
|
|
|
|
|
|
|
|
|
|
|
|
|
|
|
|
|
|
|
|
|
|
|
|
|
|
|
|
|
|
|
|
|
|
|
|
|
|
|
|
|
На рис. 3.6 представлены расчетные значения предельных обжатий в зависимости от энергетического безразмерного параметра ψ* , относительно толщины стенки трубы R = R2 / R1 и угла наклона об-
разующей канала волоки с учетом деформационного упрочнения материала при µ = 0,5 для случая среды с линейным упрочнением.
Согласно рис. 3.6 для реальных величин и заданных значений относительной толщины стенки трубы можно определять предельные из условий прочности трубы от остаточных напряжений отношения ddд , характеризующих деформацию.
124
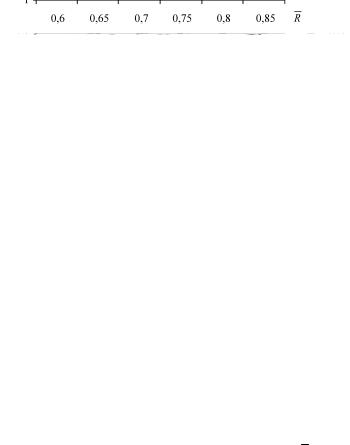
а
б
Рис. 3.6. Расчетные зависимости отношения d/dд: а – от параметра ψ* при
α = 6; 11; 16°; б – от относительной толщины стенки трубы R при ψ* = 0,02; 0,03; 0,04
3.4. Остаточные напряжения и технологическая прочность трубной заготовки при волочении
Опыт применения волочильного производства показывает, что для качественной продукции необходим оптимальный выбор технологических параметров для исключения брака и разрушения заготовок в процессе изготовления. Анализ полученных распределений остаточных напряжений в прутках и трубах показывает, что значения
125
растягивающих напряжений в заготовках после выхода из матрицы могут быть значительными из-за неравномерности распределения пластических деформаций. Складываясь по принципу суперпозиции с напряжениями волочения, остаточные напряжения могут превысить предел прочности материала, что приведет преждевременному разрушению переднего конца заготовки на стадии производства.
При деформации трубной заготовки в конической волоке напряжение волочения определяется по формуле И.Л. Перлина [3]
σ |
= ln Dсн 1,15σ + f ctg α (σ −σ |
) |
+ σ |
, |
(3.18) |
||||
вол |
|
s |
n |
s |
пр |
|
пр |
|
|
|
Dск |
|
|
|
|
|
|
|
|
где σвол – напряжение волочения; Dсн, |
Dск |
– диаметры на входе и на |
|||||||
выходе из матрицы соответственно; f |
– коэффициент трения в зоне |
||||||||
деформации; σпр – напряжение противонатяжения; αn |
– приведен- |
||||||||
ный угол волоки, tg αn = 0,65tg α. |
|
|
|
|
|
|
|
Полное напряжение в направлении оси складывается из напряжения нагрузки (волочения) и осевых остаточных напряжений. С учетом этого положения запишем соотношение (3.18) в следующем виде:
σ |
= ln |
Dсн 1,15σ |
+ f ctg α |
(σ −σ |
) |
+ σ |
+σ0 |
, |
(3.19) |
|||
вол |
|
D |
|
s |
n |
s |
пр |
|
пр |
z |
|
|
|
|
ск |
|
|
|
|
|
|
|
|
|
|
где σ0z – осевые остаточные напряжения в поверхностных слоях Осе-
вые остаточные напряжения достигают максимальных значений во внешних поверхностных слоях заготовки.
Исходя из условия прочности σвол ≤ σs , с учетом некоторых преобразований получим следующее соотношение:
|
|
|
ln Dсн |
1,15 + f ctg α |
(1−σ |
) |
≤1−(σ |
+σ0 ) , |
(3.20) |
||
|
|
|
|
Dск |
|
n |
пр |
|
пр |
z |
|
|
|
|
|
|
|
|
|
|
|
|
|
|
|
σпр |
0 |
σ0z |
|
|
|
|
|
|
|
где σ |
= |
|
|
; σ = |
|
. |
|
|
|
|
|
σ |
|
σ |
|
|
|
|
|
||||
пр |
|
|
z |
|
|
|
|
|
|
||
|
|
s |
|
|
s |
|
|
|
|
|
|
126

Из соотношения (3.20) следуют соотношения технологических параметров и свойств материала, соответствующие предельному случаю волочения из условия сохранения прочности переднего конца
D |
|
0 |
) |
|
|
|
|
1−(σпр +σz |
|
|
|||
сн = exp |
|
|
|
|
. |
(3.21) |
|
+ f ctg αn (1 |
|
||||
Dск |
1,15 |
−σпр ) |
|
|||
|
|
|
|
|
|
Формула (3.21) использована для расчета предельных соотношений диаметров заготовок из стали 45 (рис. 3.7, а) и сплава ВТ1-1 (рис. 3.7, б) при калибровке из условий сохранения прочности переднего конца заготовки с учетом тех остаточных напряжений, которые
а
б
Рис. 3.7. Предельные отношения диаметров заготовок в зависимости от коэффициента трения и α = 8; 12; 16°: а – сталь 45, ψ* = 0,02; б – сплав ВТ1-1, ψ* = 0,03; 8, S 12, –×– 16
127
формируются при деформации в данном проходе или в предыдущих проходах. На рис. 3.7 приведены результаты расчета предельных обжатий в зависимости от угла раствора образующей канала волоки,
для различных значений коэффициента трения f и ψ при σпр = 0 ;
µ= 0,5.
3.5.Остаточные напряжения и прочность металлоизделий при наличии трещин
Согласно современным представлениям теории разрушения тело после пластической деформации оказывается пораженным микротрещинами. Остаточные растягивающие напряжения в результате длительного воздействия на микротрещины могут вызвать их увеличение до критических размеров и привести к макроразрушению металла. Кроме того, растягивающие остаточные напряжения способствуют раскрытию микротрещин и проникновению в них агрессивной среды, что приводит к снижению коррозионной стойкости поверхностных слоев металла. В свою очередь, сжимающие напряжения препятствуют коррозионному воздействию агрессивной среды на поверхности микротрещин. При высоком уровне напряжений и развитых микротрещинах иногда достаточно легких ударных нагрузок для наступления хрупкого излома. Понижение предела усталости – также результат воздействия растягивающих остаточных напряжений в сочетании с напряжениями от внешних нагрузок, особенно растягивающих.
Проблема установления закономерностей развития трещин приобретает особую актуальность в связи с применением высокопрочных материалов, тенденций к уменьшению массы машин, изысканию резервов прочности материалов, выбору оптимальных технологических процессов изготовления и упрочнения материалов, а также назначению оптимальных сроков службы и повышению надежности работы деталей.
Практически все материалы имеют плоские дефекты типа трещиноподобных разрывов или полостей. В работе [17] перечислены некоторые дефекты и их характерные размеры:
128
–трещины сдвига – дислокации в металлах (10−8 −10 см);
–технологические трещины в металлах (10−3 −10 см). К ним относят: сварочные трещины; трещины, возникающие при термообработке, запрессовке, ковке и других процессах; зоны окисленного металла;
–эксплуатационные трещины (10−3 −10 см). К ним относят: усталостные трещины, коррозионные трещины, диффузионно-водород- ные трещины;
–трещины в металлах, возникающие в металлургическом про-
цессе (10−5 −1 см). К ним относят раковины и пустоты, возникающие при остывании металла в слитках; зоны окисленного металла; зоны охрупченного металла; инородные включения, прочность которых меньше прочности основного металла.
Опыт показывает, что практически во всех готовых металлоизделиях, даже в ненагруженном состоянии, имеются мелкие микротрещины – несплошности и нарушения структуры. Поэтому при расчетах на прочность и долговечность конструкций необходимо учитывать возможность образования в исходном материале и в готовых изделиях от субмикродо макроскопических дефектов типа трещин, возникающих в процессе изготовления и обработки.
В деталях, уже проработавших в течение определенного времени, вероятность наличия трещин резко возрастает. Усталостные трещины, возникающие при циклических нагрузках, постоянно разрастаясь, подготавливают условия для хрупкого разрушения. В связи с этим особое значение приобретает способность материала или конструкции воспринимать нагрузки при наличии трещины.
На рис. 3.8 приведены различные дефекты, которые возникают при прокате металлоизделий [18]. Пустоты различной величины и формы, чаще одиночные, образуются вследствие раскрытия и неполной заварки термических трещин и называются в литературе «скворечниками» (рис. 3.8, а). Они могут не обнаруживаться при внешнем осмотре поверхности заготовки. Данный тип дефекта следует отличать от внутренних разрывов, образующихся при непра-
129
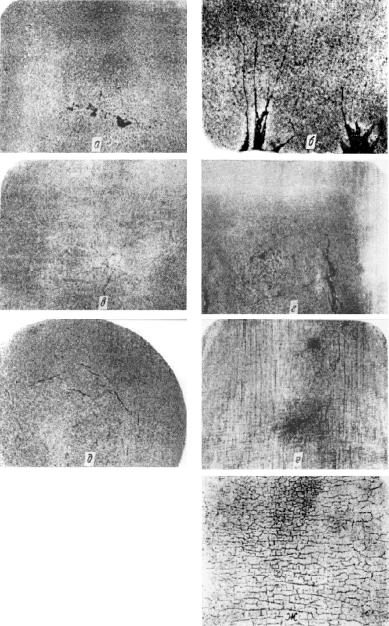
а |
|
б |
|
|
|
в |
|
|
|
г |
|
|
|
|
|
д |
|
|
|
|
|
|
|
|
г |
|
|
|
|
|
|
|
Рис. 3.8. Трещины в прокате: а – |
|
|
|||
скворечники б – трещины от рва- |
|
|
|||
нин; в – осевые интеркристал- |
|
|
|||
литные и межкристаллитные тре- |
|
|
|||
щины; г – трещины от внутрен- |
|
|
|||
него пережога; д – флокены; е |
– |
|
|
||
скворечник от флокена; ж |
– |
|
|
||
шлифовочно-травильные трещины |
|
ж |
|||
|
|
|
|
|
|
|
|
|
|
|
|
130