
книги / Основные новые разработки в технологии аммиака
..pdf
|
|
|
|
Таблица 5 |
Характеристики катализаторов KM1 и KM1R |
||||
|
|
|
|
|
Показатели |
|
|
Катализатор |
|
|
KM1 |
|
KM1R |
|
Содержание, мас.%: |
|
|
|
|
Fe, FeO |
– |
|
89–93 |
|
Fe3O4 |
91–95 |
|
– |
|
K2O, Al2O3, CaO, SiO2 |
5–9 |
|
7–11 |
|
Рабочая температура, °С |
340–550 |
|
340–550 |
|
Рабочее давление, атм |
90–600 |
|
90–600 |
|
Максимальный срок безопасной эксплуатации катализатора |
||||
зависит от содержания кислорода в газе: |
|
|
||
|
|
|||
ЭквивалентноесодержаниеO2, 10–6 об. % |
Срокбезопаснойэксплуатации, дни |
|||
<2 |
|
|
|
Не ограничен |
2–4 |
|
|
180 |
|
4–6 |
|
|
30 |
5.3. Катализатор фирмы KBR
Фирмой KBR был разработан новый рутениевый катализатор, обладающий намного более высокой активностью, нежели традиционные железные катализаторы. Этот катализатор представляет собой металлический рутений, нанесенный на углеродную основу, с различным содержанием промотирующих добавок.
Новый катализатор позволил проводить процесс в существенно более мягких условиях (при более низких температуре и давлении), для чего в KBR разработали совершенно новый агрегат синтеза аммиака KAAP [1, 5] (см. подразд. 4.1).
Ниже приведены некоторые особенности работы реактора
вагрегате KAAP:
–низкое рабочее давление синтеза (90 атм);
–концентрация аммиака на выходе из реактора до 20 %;
–температура синтеза 350–400 °С;
–отсутствие стадии разделения воздуха;
51
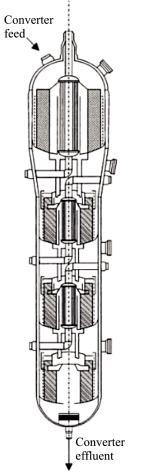
– использование одноступенчатого компрессора вместо трехступенчатого.
Вышеперечисленные особенности процесса KAAP в сумме дают 3–8 % экономии капитальных и эксплуатационных затрат по сравнению с работой других современных агрегатов. Однако высокая стоимость катализатора несколько уменьшает этот эффект.
Реактор синтеза аммиака, используемый в этой схеме, представляет собой четырехслойную колонну синтеза (рис. 20) иимеет следующиеособенности:
– имеет четыре полки с радиальным направлением потока синтез-газа
вслоях катализатора;
–первая по ходу газа полка загружена традиционным железным катализатором, обеспечивающим высокую скорость реакции синтеза при низких концентрациях аммиака;
–три остальные полки загружены новым рутениевым катализатором, который можно использовать и при более высоких концентрациях аммиака;
–применяется межступенчатое
охлаждение газа во встроенных теплообменниках встречным потоком свежего газа.
Катализатор на основе рутения имеет более высокую активность, чем магнетитовый, а также меньшее время восстановления (19 ч в сравнении с 30–40 ч для обычных железных катализаторов).
52

6. ОПЫТ РАЗРАБОТКИ ТЕХНОЛОГИИ МЕГААММИАКА
6.1. Разработка фирм
Ammonia Casale и Linde
Вначале XXI в. фирмы Ammonia Casale и Linde приняли ре-
шение об объединении своих усилий в области разработки технологии аммиака большой единичной мощности. Современные наилучшие технологии достигли уровня мощности 2000 т/сут. Дальнейшее наращивание мощности, в частности до 4000 т/сут, требует разработки новых технологических решений [9].
Врезультате анализа всех вариантов традиционной и усовершенствованных технологий аммиака разработчики пришли к варианту технологии мегааммиака, представленной на рис. 21.
Рис. 21. Блок-схема технологии MEGAMMONIA process
Технология включает в себя пять основных стадий: стадию разделения воздуха, стадию каталитического парциального окисления метана, стадию паровой конверсии СО, стадию очистки газа от СО2 и примесей метана, СО и аргона, стадию синтеза аммиака.
Криогенное разделение воздуха является широко известным процессом, одним из разработчиков которого является фирма Linde. Для рассматриваемого производства необходим кислород чистотой 97,0 % и азот чистотой 99,99 %.
53
Каталитическое парциальное окисление метана разработано и реализовано фирмой Lurgi и является основным процессом производства метанола большой мощности. Эта стадия включает процессы предварительного нагревания природного газа, очистки от соединений серы, насыщения газа водяным паром с использованием конденсата, предварительный риформинг высших углеводородов
собразованием метана и, наконец, парциальное окисление метана
собразованием водорода, СО и СО2 [9].
На стадии очистки газа используются две колонны: одна для удаления из газа СО2 путем абсорбции метанолом, другая для удаления из газа метана, СО и аргона с помощью жидкого азота.
В цикле синтеза аммиака, который осуществляется при давлении 200 атм, используется трехполочная колонна конструкции фирмы Ammonia Casale с магнетитовым катализатором.
Разработчики провели оценку капитальных затрат на строительство производства аммиака мощностью 4000 т/сут. Оказалось, что капитальные затраты составляют 70 % от капитальных затрат на два современных производства аммиака мощностью 2000 т/сут каждое. Структура затрат такова: 61 % на основное оборудование, 15 % на теплообменное оборудование, 7 % на хранилище аммиака, 17 % на блок разделения воздуха. Эксплуатационные затраты снижаются на 40 % [10].
Основные аппараты, используемые в данной технологии, имеют следующие размеры (диаметр): реактор парциального окисления 4,1 м, реактор конверсии СО 3,8 м, реактор синтеза 3,8 м, трубопроводы на стадииполучениясинтез-газа800 мм, вцикле синтеза500 мм.
Мощность компрессора синтез-газа 31 МВт, мощность компрессора для холодильной установки 16 МВт.
6.2. Технология аммиака Dual Pressure
Uhde Procces фирмы Uhde
Фирма Uhde также занимается разработкой производства аммиака повышенной единичной мощности. При этом возникают различные проблемы, рассмотренные в статье [11].
54
В связи с этим авторами статьи были проанализированы как проблемы конструирования, так и проблемы масштабирования основных секций и агрегатов производства.
Сточки зрения конструкций аппаратов, машин и трубопроводов наиболее проблемными в плане увеличения мощности являются секция риформинга и компрессор синтез-газа, а также теплообменники для охлаждения газа, оборудование цикла синтеза и компрессор холодильной системы. В меньшей степени критичны трубопроводы синтеза, секция удаления СО2, реакторы конверсии СО.
Сточки зрения масштабирования наибольшие проблемы при увеличении мощности возникают с компрессором синтез-газа и с трубопроводами в цикле синтеза. Определенные трудности имеются при разработке теплообменного оборудования для охлаждения газа и оборудования цикла синтеза. Меньше проблем возникает в секциях риформингов и конверсии СО и компрессоре холодильной системы.
Сточки зрения пригодности для использования при увеличении мощности был проведен сравнительный анализ традиционной технологии и трех вариантов усовершенствованных технологий (технологий с применением модифицированного первичного риформинга с процессом Purifier, автотермического риформинга без трубчатой печи и с печью и теплообменного риформинга с кислородным и воздушным дутьем). Качественную оценку пригодности этих технологий для создания производства большой мощности можно сделать по результатам проведенного анализа, представленным в табл. 6.
Как видно из данных, приведенных в табл. 6, наилучшие перспективы с точки зрения применения при увеличении мощности имеет технология с модифицированным первичным риформингом и процессом Purifier, а также технология ATR с кислородным дутьем, разделением воздуха и промывкой синтез-газа жидким азотом. Именно эти технологии достаточно проверены в промышленном масштабе и имеют положительные показатели на основных стадиях производства. На стадиях компрессии синтез-газа и синтеза аммиака хорошие перспективы имеет двойное давление.
55
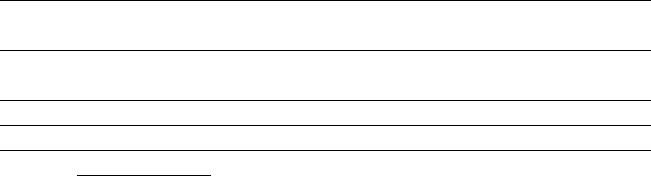
56
Таблица 6 Сравнение различных технологий аммиака с точки зрения возможностей увеличения мощности
|
|
Модифицирован- |
Автотермическийриформинг |
Теплообменныйриформинг |
|||
Состояние, |
|
|
|
|
|
||
|
ныйпервичный |
|
|
|
|
||
объекты |
Традиционная |
|
|
|
|
||
риформинг |
Безтрубчатой |
|
ATR с |
ATR своздуш- |
|||
истадии |
технология |
Струбчатойпечью |
кислородным |
||||
спроцессом |
|||||||
производства |
|
печи |
|
дутьем |
нымдутьем |
||
|
Purifier |
|
|
|
|||
|
|
Сразделением |
Сразделениемвоз- |
Сразделением |
Безразделения |
||
|
|
|
|||||
|
|
|
воздухаипромыв- |
||||
|
|
|
воздуха |
духа |
койазотом |
воздухасPurifier |
|
Состояниепро- |
|
|
|
Проверено |
|
||
|
|
|
Проверенодля |
Проверенодля |
|||
веренностив |
Проверенныйпроцесс |
Проверенный |
Проверенодля |
длясинтеза. |
|||
небольшоймощ- |
небольшоймощ- |
||||||
промышленно- |
процесс |
синтеза |
Проверенныйпро- |
||||
сти |
|
|
|
цесс |
ности |
ности |
|
|
|
|
|
|
|||
Трубопроводы |
Базовыйразмер |
Больше |
Больше |
Больше |
Меньше |
Больше |
|
|
|
|
Оченькритичноза |
Критичнозаисклю- |
|
|
|
КонверсияСО |
Базовыйразмерреактора |
Некритично |
исключением |
чениемнизкого |
Некритично |
Некритично |
|
|
Базоваявеличинастепени |
|
низкогодавления |
давления |
|
|
|
ОчисткаотСО |
Больше |
Значительно |
Больше |
Значительно |
Больше |
||
2 |
очистки |
|
больше |
|
больше |
|
|
Газсинтеза |
Базовоесодержаниеинертов |
Почтисвободен |
Базовоесодержа- |
Базовоесодержание |
Свободенотинер- |
Почтисвободен |
|
|
Увеличениеразмеров |
отинертов |
ниеинертов |
инертов |
тов |
отинертов |
|
|
|
|
|
|
|
||
Компрессия |
критично |
Проверено |
Критично |
Критично |
Проверено |
Проверено |
|
|
Двойноедавлениепроверено |
|
|
|
|
|
|
|
|
|
|
|
|
|
|
|
Увеличениеразмеров |
|
|
|
|
|
|
Синтез |
критично |
Умеренныйриск |
Критично |
Критично |
Умеренныйриск |
Умеренныйриск |
|
|
|
|
|
|
|
|
|
|
Двойноедавлениепроверено |
|
|
|
|
|
56

Встатье [11] также были рассмотрены особенности реализации основных стадий производства при увеличении мощности.
Всвязи с проведенным анализом для производств аммиака большой мощности фирмой Uhde была разработана технология Dual Pressure Uhde Procces (DPUP) [11] с двумя уровнями давления (рис. 22) (см. подразд. 3.4).
Рис. 22. Технологическая схема синтеза аммиака фирмы Uhde с двумя уровнями давления: 1, 2 – реакторы синтеза; 3 – компрессор низкого давления; 4 – компрессор высокого давления; 5 – прямоточный реактор предварительного синтеза; 6 – система очистки газа
Особенность технологии DPUP заключается в том, что свежий синтез-газ после сжатия в компрессоре до давления 11 МПа поступает в отдельную колонну предварительного синтеза, после которой аммиак (1/3 от всего производимого количества) выделяется из газа. Затем газ компремируется до давления 21 МПа и под этим давлением поступает в цикл синтеза высокого давления. В этом цикле используются две колонны синтеза: одна – с двумя слоями катализатора, другая – с одним. Все слои катализатора в колоннах имеют радиальный ход газа. Мощность такого производства может составлять
3300 т/сут.
57
ЗАДАНИЯ ДЛЯ САМОСТОЯТЕЛЬНОЙ РАБОТЫ
1.Составить балансовое стехиометрическое уравнение получения 1 т аммиака из метана, водяного пара и воздуха. Определить теоретический (минимальный) расход метана на получение 1 т аммиака.
2.Составить балансовое уравнение получения 1 т аммиака из метана, водяного пара и воздуха (избыток по сравнению со стехиометрией 50 %). Определить соотношение водород/азот в синтез-газе.
3.Рассчитать суммарный тепловой эффект процесса получения аммиака из метана с использованием стехиометрического количества воздуха, необходимого для получения 1 т аммиака.
4.Рассчитать суммарный тепловой эффект процесса получения аммиака из метана с использованием 50%-ного избытка воздуха по сравнению со стехиометрическим количеством, необходимого для получения 1 т аммиака.
5.Составить балансовое стехиометрическое уравнение получения 1 т аммиака из метана, водяного пара и воздуха, обогащенного кислородом. Содержание кислорода в обогащенном воздухе 30 %. Определить расход метана на получение 1 т аммиака.
6.Оценить энергозатраты на проведение процесса паровой
конверсии метана. Степень превращения метана 0,7. Исходные данные: расход метана 582 нм3/т, соотношение пар/метан в исходной смеси 3/1, температура на входе 550 °С, на выходе 820 °С, тепловой
эффект процесса 49,38 ккал/моль СН4, теплоемкость парогазовой смеси 8,2 кал/моль·°С.
7.Оценить снижение энергозатрат при использовании предриформинга. Исходные данные: температура парогазовой смеси
на входе в реактор предриформинга 540 °С, на выходе 480 °С, на входе в трубчатую печь 540 °С, на выходе 820 °С. Степень превращения метана на выходе из трубчатой печи 0,7, тепловой эффект процесса 49,38 ккал/моль СН4, теплоемкость парогазовой смеси 8,2 кал/моль·°С.
8. Оценить затраты энергии на сжатие синтез-газа. Исходные данные: расход синтез-газа 2834 нм3/т, давление на входе в компрессор 30 атм, на выходе 200 атм, температура 18 °С.
58
9.Оценить затраты энергии на сжатие циркуляционного газа синтеза. Исходные данные: расход циркуляционного газа 9704 нм3/т, давление на входе в компрессор 185 атм, на выходе 200 атм, температура 18 °С.
10.Оценить затраты энергии на выделение 1 т аммиака из газа синтеза. Исходные данные: расход газа 8407 нм3/т, температура исходного газа 250 °С, конечная температура –4 °С, теплота конденсации аммиака 5,58 ккал/моль.
11.Оценить снижение энергетических затрат на охлаждение
газа синтеза при уменьшении содержания инертов в исходном син- тез-газе с 1,2 до 0,4 %. Исходные данные: расход газа 8407 нм3/т, температура исходного газа 250 °С, конечная температура –4 °С, теплоемкость газа 7,0 кал/моль·°С.
Примеры выполнения заданий для самостоятельной работы
Пример 1 Задание. Оценить энергозатраты на проведение процесса
паровой конверсии метана. Степень превращения метана 0,7. Исходные данные: расход парогазовой смеси 3015 нм3/т, содержание метана в исходной смеси 19,3 об.%, температура на выходе 820 °С, тепловой эффект процесса 49,38 ккал/моль СН4, теплоемкость парогазовой смеси 8,2 кал/моль·°С. Начальная температура газа 25 °С.
Реакция паровой конверсии метана: CH4 + H2O = CO + 3H2 – Q.
При проведении процесса паровой конверсии метана тепло расходуется на нагревание парогазовой смеси Q1 и на протекание эндотермической реакции Q2.
Количество теплоты на нагревание парогазовой смеси находим по формуле
Q1 V cp t,
где V – расход парогазовой смеси, нм3/т; ср – теплоемкость парогазовой смеси, кал/(нм3·°С); ∆t – изменение температуры парогазовой смеси при нагревании, °С.
59

Находим эти величины:
V = 3015 нм3/т;
ср = 8,2·1000/22,4 = 366 кал/(нм3·°С); t = 820 – 25 = 795 °С.
Отсюда Q1 = 3015·366·795 = 877274550 кал/т = 0,877 Гкал/т.
Количество теплоты, расходуемое на протекание эндотермической реакции, находим по формуле
Q2 H VCH4 ,
где |
Н – тепловой эффект |
химического процесса, ккал/нм3СН4, |
|
V |
– количество метана, прореагировавшего по реакции, нм3/т, |
||
CH4 |
|
|
|
|
V |
|
V C x , |
|
CH4 |
100 |
|
|
|
|
где С – содержание метана в исходной смеси, об.%; х – степень превращения метана.
Находим эти величины:
Н = 49,38·1000/22,4 = 2204,5 ккал/нм3СН4;VCH4 = 3015·19,3·0,7/100 = 407,3 нм3/т.
Отсюда Q2 = 2204,5·407,3 = 897892,8 ккал/т = 0,898 Гкал/т.
Таким образом, общие затраты энергии Q = 0,877 + 0,898 = = 1,775 Гкал/т, что равноценно расходу природного газа в количестве 221,8 нм3/т при калорийности 8000 ккал/нм3.
Пример 2 Задание. Оценить затраты энергии на сжатие технологическо-
го воздуха. Исходные данные: расход воздуха 834 нм3/т, давление на входе в компрессор 1 атм, на выходе 38 атм, температура 30 °С. КПД компрессорной установки 0,7.
Определим число ступеней сжатия по формуле:
lg p2 n lgpx1 ,
60