
книги / Технология производства проводов
..pdf
Рис. 1.1. Форма медных слитков (ГОСТ 193–79):
типа СВ (а), CH и CC (б)
Трапецеидальные слитки отливаются в горизонтально расположенные изложницы, открытые сверху, так что поверхность меди не защищена сверху от окисления и контактирует с воздухом. В результате при кристаллизации поверхность слитка становится морщинистой, «рожистой». Это связано с тем, что насыщенный кислородом слой меди имеет большую усадку при остывании, чем основная масса слитка. Наличие «рожистой» поверхности затрудняет получение при последующих операциях прокатки и волочения медной проволоки с высококачественной поверхностью. Поэтому для получения эмалированных проводов используются строганые слитки, у которых верхний слой снимается на глубину 8–12 мм. По химическому составу медные слитки горизонтальной отливки должны соответствовать меди не ниже марки М1, причем содержание кислорода не должно превышать 0,06 %.
Бескислородная медь, поставляемая в слитках вертикального исполнения, не имеет сильно окисленной поверхности. По химическому составу она должна соответствовать меди не ниже марки М0б. Слитки вертикальной отливки более однородны по содержанию кислорода и пористости, по механическим свойствам.
11
В соответствии с ГОСТ 193–79 для кабельной промышленности выпускаются медные слитки следующих марок:
СВ – вертикальной непрерывной отливки; СН – горизонтальной отливки с неудаленной верхней по-
верхностью; СС – горизонтальной отливки с удаленной верхней по-
верхностью.
Размеры медных слитков приведены в табл. 1.2 [2].
|
|
|
Таблица 1 . 2 |
|
|
Размеры медных слитков, мм |
|
|
|
|
|
|
|
|
Маркаслитка |
ДлинаL |
Ширина В |
|
ВысотаН |
СН |
1372 |
98 |
|
92–102 |
СС |
1360 |
110 |
|
100 |
СВ-I |
1400 |
100 |
|
100 |
СВ |
2800 |
100 |
|
100 |
Вторым по значению металлом в производстве обмоточных и эмалированных проводов является алюминий.
Алюминий – металл серебристо-белого цвета, обладает низким удельным весом, высокой проводимостью. В чистом виде алюминий имеет очень хорошие пластические свойства. Отличительной особенностью алюминия является хорошая коррозионная стойкость. Тонкая окисная пленка защищает металл от дальнейшего окисления. Железо и кремний снижают пластичность и проводимость алюминия (железо делает его хрупким и снижает его химическую стойкость, кремний упрочняет его).
Для производства обмоточных проводов применяется алюминий технической чистоты марок А5Е и А7Е по ГОСТ 11069–74. В нем содержание марганца не более 0,01 %, магния не более 0,02 %, мышьяка не более 0,015 %. В алюминии марки А5Е допускается содержание кремния не более 0,12 % и других примесей (титан, ванадий, марганец, хром) неболее0,01 %.
12
Удельное электрическое сопротивление алюминия в 1,62 раза выше, чем меди. Поэтому сечение алюминиевой проволоки сэлектрическим сопротивлением, равным сопротивлению медной проволоки, должно быть в 1,62 раза больше, а диаметр в 1,27 раза больше, чем сечение и диаметр медной проволоки. При этом алюминиеваяпроволока будет в двараза легчемедной [1].
Алюминий поставляется в слитках с примерными размерами 100×100×2700 мм, весом до 76 кг. Однако в настоящее время для производства проводов в основном используется катанка, получаемая непосредственно из жидкого металла методом непрерывного литья и прокатки. Катанка поставляется в больших бухтах весом до 1500 кг.
Низкое удельное сопротивление меди, ее высокие механические характеристики, хорошая свариваемость, возможность пайки, способность подвергаться лужению, возможность покрытия ее серебром ставят медь на первое место в ряду других материалов. Но содержание меди в земной коре – около 0,1 %, а алюминия – 7,5 %, поэтому в связи с дефицитностью меди широко применяется алюминий.
Мягкие отожженные медь и алюминий идут на изготовление проволоки; полутвердые – на изготовление продукции, для которой необходима определенная механическая прочность; твердотянутые – на изготовление изделий, которым приходится выдерживать высокие механические нагрузки и которые не допускают никаких деформаций.
Медная проволока круглого сечения, применяемая для производства обмоточных проводов с бумажной, волокнистой, пленочной и пластмассовой изоляцией, изготавливается по ТУ 16.К71.0887–90. На круглую медную проволоку, предназначенную для последующего эмалирования, распространяется ОСТ 16.0.505.008–73, который регламентирует целый ряд повышенных требований к качеству про- волокипосравнениюсТУ16.К71.087–90.
При производстве круглой проволоки используется медная катанка по ОСТ 13842–80, причем проволоку для эмалиро-
13
ванныхпроводов диаметромменее0,38 ммисвыше1,25 ммрекомендуется изготавливать из скальпированной заготовки или из катанки, полученной методом непрерывного литья и прокатки. Медная круглая проволока может быть мягкой (марка ММ) итвердой (марка МТ). Проволока для обмоточных проводов изготавливается диаметром 0,015–5,20 мм.
Одним из дополнительных требований, обеспечивающих повышенное качество проволоки, предназначенной для эмалирования, является отсутствие дефектов (заусенцы, расслаивание, изменение внешнего вида) на проволоке диаметром 0,375 мм и выше, после навивания на стержень диаметром, равным диаметру испытываемой проволоки. Проволока, применяемая для изготовления эмалированных проводов, должна храниться не более 15 суток в помещении при 5–35 °C и относительной влажности не более 80 %. При этом она должна быть защищена от механических воздействий, действия солнечных лучей, атмосферных осадков и агрессивных сред.
Удельное электрическое сопротивление круглой медной проволоки постоянному току при 20 °C должно соответствовать значениям, приведенным в табл. 1.3.
Таблица 1 . 3 Удельное электрическое сопротивление круглой проволоки
|
Удельноеэлектрическоесопротивле- |
|
Диаметр проволоки, мм |
ние, Ом·м, неболее, длямарок |
|
|
ММ |
МТ |
До 1,0 |
17,24·10–9 |
18,0·10–9 |
Свыше1,0 до2,44 включительно |
17,8·10–9 |
|
2,5 иболее |
|
17,7·10–9 |
Для круглой медной проволоки марки МТ диаметром свыше 1,0 мм фиксируется минимальное число перегибов, которое составляет в зависимости от диаметра 4–7 мм.
Медная проволока прямоугольного сечения марок ПММ (мягкая) и ПМТ (твердая) изготавливается по ГОСТ 434–78.
14
На медную проволоку прямоугольного сечения, предназначенную для последующего эмалирования, распространяются технические условия ТУ 16.501.021–86, в которых требования к качеству проволоки по сравнению с ГОСТ 434–78 повышены.
Для производства алюминиевых эмалированных проводов применяется круглая алюминиевая проволока диаметром от 0,008 до 2,50 мм, для обмоточных проводов с другими видами изоляции – круглая проволока диаметром 1,35–8,0 мм и прямоугольная – сечением от 7,5 до 125 мм2. При производстве эмалированных проводов алюминиевая проволока диаметром менее 0,69 мм предварительно не отжигается, отжиг ее производится непосредственно на агрегатах при эмалировании проволоки. Алюминиевая проволока диаметром выше 0,69 мм должна предварительно отжигаться в отдельных печах, установленных непосредственно на агрегатах.
Круглая алюминиевая проволока, предназначенная для обмоточных проводов, в соответствии с ТУ 16.К71.088–90 изготавливается твердой (марки АТ) и мягкой (марка АМ). Проволока изготавливается из алюминиевой катанки и выпускается в диапазоне диаметров от 0,08 мм и выше.
Удельное электрическое сопротивление мягкой алюминиевой проволоки не должно превышать 28·10–9 Ом·м, твердой и полутвердой – 28,3·10–9 Ом·м. Механические свойства проволоки марок АТ и АМ должны соответствовать указанным в табл. 1.4.
В кабельной промышленности находят применение также сплавы меди с элементами, позволяющими улучшить механические характеристики меди, сохранив удельную проводимость, близкую к проводимости чистой меди.
Для производства обмоточных проводов, кроме меди
иалюминия, довольно широко применяются также сплавы высокого электрического сопротивления – манганин, константам
инихром. Провода из сплавов сопротивления необходимы для электроизмерительных и электронагревательных приборов, образцовых резисторов реостатов. Во всех этих случаях при-
15
меняемый сплав должен иметь высокое электрическое сопротивление, а в некоторых случаях и минимальный температурный коэффициент электрического сопротивления. Специфическим требованием, предъявляемым к сплавам сопротивления, является малая термоЭДС по отношению к меди. Манганин относится к группе медно-никелевых сплавов (ГОСТ 492–73) и содержит кроме меди и никеля марганец. Примерный состав манганина марки МНМц 3-12: марганец 11,5–13,5 %; никель (с кобальтом) 2,5–3,5 %; остальное – медь. Содержание примесей, среди которых главной является железо, не должно превышать 0,72 %.
Таблица 1 . 4
Механические свойства проволоки марок АТ и АМ
|
АТ |
|
АМ |
||
Диаметр |
Временное |
|
Относи- |
Временное |
Относи- |
сопротивление |
|
сопротивление |
|||
проволоки, |
|
тельное |
тельное |
||
мм |
разрыву, МПа |
|
удлинение, |
разрыву, МПа |
удлинение, |
2 |
|
2 |
|||
|
(кгс/мм ), |
|
%, не менее |
(кгс/мм ), |
%, не менее |
|
неменее |
|
|
неменее |
|
От0,08 до0,10 |
98 (10) |
|
0,5 |
|
|
0,10–0,30 |
117 (12) |
|
– |
– |
|
|
|
||||
0,30–0,50 |
157 (16) |
|
0,7 |
|
|
0,50–0,60 |
176 (18) |
|
|
|
10 |
0,60–1,00 |
|
|
1,0 |
|
|
1,00–1,50 |
|
|
|
73,5–98 |
15 |
1,50–2,50 |
167 (16,5) |
|
1,3 |
(7,5–10) |
18 |
2,50–4,0 |
|
|
1,5 |
|
20 |
4,0–5,0 |
|
|
2,0 |
|
25 |
5,0–10,0 |
147 (15) |
|
|
||
|
|
|
|
Константан имеет те же компоненты, что и манганин, только содержатся они в других соотношениях (константан марки МНМц 40-1,5): никель (с кобальтом) – 39–41 %; марга-
16

нец – 1,0–2,0 %; остальное – медь. Допустимое содержание примесей, как и для манганина, 0,77 %.
Сплавы, имеющие общее название нихромы, состоят из никеля, хрома и железа (ГОСТ 10994–74). В производстве обмоточных проводов, как правило, используются двойные сплавы никеля и хрома.
Основные параметры манганина, константана и нихрома приведены в табл. 1.5.
Таблица 1 . 5
Основные параметры манганина, константана и нихрома
Параметр |
Манганин |
Константан |
Нихром |
|
МНМц 3-12 |
МНМц 40-1,5 |
Х20Н80 |
||
|
||||
Плотность при20 °С, |
8400 |
8900 |
8400 |
|
кг/м3 |
||||
Температураплавле- |
960 |
1250 |
1380–1420 |
|
ния, °С |
||||
|
|
|
||
Удельноеэлектриче- |
(0,47–0,48)·10–6 |
(0,45–0,52)·10–6 |
(1,04–1,15)·10–6 |
|
ское сопротивление |
||||
при 20 °С, Ом·м |
|
|
|
|
Температурныйкоэф- |
|
|
|
|
фициентудельного |
10·10–6 |
(–20–+60)·10–6 |
(100–104)·10–6 |
|
электрического сопро- |
|
|
|
|
тивления, °С–1 |
|
|
|
|
Разрушающеенапря- |
|
|
|
|
жениеприрастяжении, |
450–550 |
450–650 |
620–680 |
|
МПа |
|
|
|
|
Относительное удли- |
25 |
15–20 |
20 |
|
нение приразрыве, % |
||||
|
|
|
||
ТермоЭДС впаре |
1,0 |
40–50 |
– |
|
смедью, мкВ/°С |
||||
|
|
|
Кабельные заводы обычно получают заготовку из манганина и константана в виде проволоки диаметром 0,8–2,4 мм, а затем подвергают ее волочению до требуемого размера. Нихромовая проволока поступает на кабельные заводы в готовом
17
виде. После волочения проволока из сплавов сопротивления может подвергаться вакуумному отжигу. Отжиг манганиновой проволоки, в частности, производится при 450–650 °С и вакууме приблизительно 0,5 кПа в течение 2 ч.
Константановая неизолированная проволока предназначена для эксплуатации при температуре не выше 500 °С.
Нихромовая проволока (ГОСТ 8803–89) изготавливается в диапазоне диаметров 0,09–0,40 мм. Как правило, нихромовая проволока поставляется в мягком состоянии со стабильными свойствами по электрическому сопротивлению.
Медь с серебром (до 0,14 % Ag) используется при изготовлении коллекторных полос, медь с кадмием (0,7–1 %) – при изготовлении контактных проводов железных дорог, троллейбусных линий и т.д. [2].
1.2. ИЗГОТОВЛЕНИЕ МЕДНОЙ И АЛЮМИНИЕВОЙ КАТАНКИ
Существуют два метода получения медной катанки:
1)традиционный – горячей прокатки;
2)прогрессивный – непрерывного литья и прокатки.
Сущность процесса прокатки заключается в последова-
тельном уменьшении поперечного сечения и увеличении длины прокатываемой заготовки при ее прохождении между несколькими парами валков, вращающихся в разные стороны. Валки имеют специальные углубления, называемые ручьями. Валки установлены один над другим, и ручьи образуют калибр, через который и проходит нагретая заготовка. Устройства, в которых смонтированы валки и механизмы для их регулирования, назы-
ваются клетями.
Основные технологические параметры, характеризующие процесс прокатки, указаны на рис. 1.2.
18
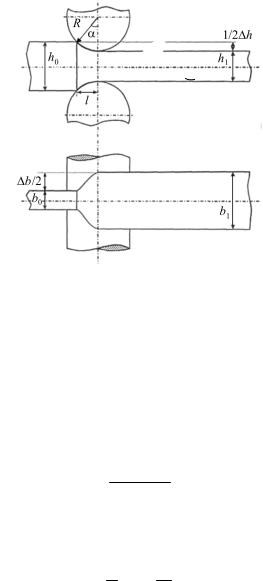
Рис. 1.2. Схема прокатки
Процесс прокатки характеризуют следующие величины:
– абсолютное обжатие по высоте ∆h – разность между высотой прокатываемой полосы до прокатки h0 и высотой полосы после прокатки h1:
∆h = h0 – h1;
– относительное обжатие по высоте ε – отношение абсолютного обжатия по высоте к высоте полосы до прокатки, %:
ε = h 100 % ; h0
– вытяжка по длине μ – отношение длины полосы после прокатки l1 к начальной длине l0:
μ= l1 ; μ = S0 , l0 S1
где S1 и S0 – сечение полосы до и после прокатки;
19

– уширение ∆b – разность между шириной полосы после прокатки b1 и шириной полосы до прокатки b0:
∆b = b1 – b0;
– угол захвата α – угол, образованный радиусами, проведенными из центра валка в точки начала и конца дуги захвата, по которой валок соприкасается с прокатываемым металлом:
cos α = 1− h ,
D
где D – диаметр валка;
– длина очага деформации l – проекция дуги захвата на продольную ось полосы:
l = R h ,
где R – радиус валка;
– опережение – разность скорости выхода полосы из валков и окружной скорости валков [2].
Все эти величины учитываются при расчете калибровки прокатного стана, заключающейся в разработке системы калибров необходимой формы и размера для всех клетей стана. При прокатке меди предельный угол захвата равен 26–30°. По мере уменьшения сечения прокатываемого металла скорость прокатки увеличивается.
При расчете калибровки прокатных станов принимаются во внимание следующие факторы:
–пластические свойства прокатываемого металла;
–захват металла валками;
–энергосиловые возможности стана;
–необходимостьполногоисключенияпереполнениякалибра;
–получение наибольшей возможной вытяжки;
–соблюдение постоянства секундного объема металла при непрерывной прокатке FnVn = const, где Fn – площадь попереч-
20