
книги / Материаловедение. Технология металлов и сварки
.pdfГлава 2 ДЕФОРМАЦИЯ И РЕКРИСТАЛЛИЗАЦИЯ МЕТАЛЛОВ
2.1. Виды деформаций
Деформация – изменение размеров и формы тела под действием внешних сил. Деформация напрямую связана с такой характеристикой, как прочность – это способность материала противостоять деформациям и разрушению. Деформация может быть упругой и пластической.
Упругая – деформация, полностью исчезающая после снятия нагрузки. При упругой деформации происходит незначительное изменение расстояний между атомами в кристаллической решетке. При увеличении межатомных расстояний увеличиваются силы притяжения между атомами. Эти силы и возвращают атомы в исходные позиции, и тело принимает свою первоначальную форму и размеры.
Пластическая (остаточная) – деформация, остающаяся в материале после снятия нагрузки. В этом случае атомы не возвращаются в исходные позиции, а занимают новое положение устойчивого равновесия.
Общая нагрузка складывается из упругой и пластической. После снятия нагрузки остается только пластическая деформация.
Пластическая деформация характеризуется в основном скольжением. Скольжение, или сдвиг, происходит под действием касательных напряжений в плоскостях в направлениях с наиболее плотной упаковкой атомов, где сопротивление сдвигу наименьшее. Металлы, имеющие большое количество линий скольжения, например с ГЦК решеткой, являются наиболее пластичными. А металлы с ГПУ решеткой обладают менее пластическими свойствами.
Для объяснения пластического сдвига учеными был предложен дислокационный механизм, который рассматривает пластический сдвиг как процесс перемещения краевых дислокаций. Согласно этому механизму металл под действием силы Р деформируется вдоль плоскости скольжения А–А сначала упруго, а затем пластиче-
11

ски (рис. 2.1). В момент упругой деформации образуется краевая дислокация. Плоскость, в которой образуется краевая дислокация,
называется экстраплоскостью.
Рис. 2.1. Схема пластического сдвига
За счет движения краевой дислокации от одного ряда атомов к другому происходит частное смещение атомов. Результатом выхода дислокации на поверхность является сдвиг одной части кристалла относительно другой на один параметр решетки.
2.2. Характеристики механических свойств металлов
Механические свойства металлов и их сплавов оценивают при помощи характеристик прочности и пластичности.
Прочность – способность материала противостоять деформациям и разрушению. Характеристики прочности определяют в результате статического испытания специальных образцов на разрывной машине. В результате таких испытаний записывается диаграмма нагрузка – удлинение (деформация).
Для исключения влияния размеров образца испытания проводят на стандартных образцах с определенным соотношением между длиной l0 и площадью поперечного сечения F0. Наиболее часто применяют образцы круглого сечения: длинные l0/d0 = 10 или короткие l0/d0 = 5 (где d0 – исходный диаметр образца).
На рис. 2.2, а приведена диаграмма растяжения низкоуглеродистой отожженной стали. Рассмотрим эту диаграмму растяжения.
До точки a деформация пропорциональна нагрузке и называ-
ется пределом пропорциональности (σпц). Численно предел пропор-
циональности
σпц = Pпц/F0,
где F0 – начальная площадь сечения образца.
12
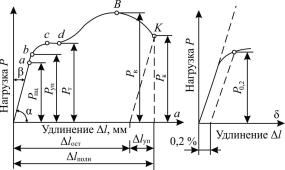
аб
Рис. 2.2. Классическая диаграмма растяжения
Нагрузка, отвечающая точке b, соответствует пределу упругости (σуп), т.е. нагрузке, до которой материал получает только упругую деформацию. Численно предел упругости
σуп = Pуп/F0.
Участок c–d характеризует пластическую деформацию, при которой удлинение образца происходит при постоянной нагрузке и соответствует пределу текучести (σт). Численно предел текучести
σт = Pт/F0.
Большинство технических металлов и сплавов не имеют площадки текучести. Для них определяют условный предел текучести, под которым понимают напряжение, вызывающее остаточную деформацию l = 0,2 % l0, т.е. 0,2 % от начальной длины образца
(рис. 2.2, б) или
σ0,2 = P0,2/F0.
Максимальная нагрузка, соответствующая точке b, определяет
временное сопротивление разрыву, или предел прочности на разрыв:
σв = Pв/F0.
Нагрузка, которую выдерживает образец в момент разруше-
ния, называется истинным сопротивлением разрушению:
13
σк = Pк/Fк,
где Fк – конечная площадь сечения образца в месте разрушения. Несмотря на то, что нагрузка Pк < Pв, вследствие образования
шейки на образце Fк < F0, поэтому σк больше, чем σв. Пластичность – способность тела (материала) к пластической
деформации, т.е. получать остаточное изменение формы и размеров без нарушения целостности. Характеристиками пластичности являются относительное удлинение δ (%) и относительное сужение Ψ (%):
|
lк l0 |
100 % |
l |
100 %, |
||||
l |
l |
|||||||
|
|
|
|
|
|
|||
|
|
0 |
|
|
0 |
|
|
|
|
F0 Fк |
100 % |
F |
100 %, |
||||
|
F |
|
||||||
|
|
F |
|
|
|
|
||
|
|
0 |
|
|
0 |
|
|
где l0 и lк – начальная и конечная длины образцов; F0 и Fк – пло-
щади поперечных сечений образцов до и после разрушений.
Кроме того, важной характеристикой механических свойств является ударная вязкость, по которой оценивают склонность стали к хрупкому разрушению, что приобретает большое значение при строительстве газонефтепроводов в северных условиях. Ударной вязкостью называется работа, затраченная при динамическом разрушении надрезанного образца, отнесенная к площади поперечного сечения в месте надреза а = Аn/F0, где An – работа, затраченная на разрушение; F0 – сечение в месте надреза.
Одной из характеристик, через которую оценивают прочность, является твердость. Твердость материала – сопротивление проникновению в его поверхность постороннего тела – индентора.
2.3. Понятие о наклепе и возврате
Наклепом называется изменение свойств металла в результате холодной пластической деформации. При наклепе повышаются прочность и твердость, т.е. происходит упрочнение металла или его нагартовка.
14
Характеристики пластичности (пластичность, вязкость, относительное удлинение и сужение) понижаются, т.е. происходит охрупчивание металла.
При наклепе изменяются все структурно-чувствительные свойства металла. Сама структура также изменяется. Зерна металла вытягиваются в направлении действия деформации, структура становится волокнистой.
Упрочнение объясняется тем, что с увеличением степени деформации на несколько порядков увеличивается число дислокаций. При увеличении числа дислокаций их свободное перемещение ограничивается и прочностные характеристики увеличиваются.
Нагрев может вернуть металлу исходные (до деформации) свойства.
Если температуры нагрева находятся в пределах 0,2–0,3 Тпл, то наступает процесс возврата. Снижается напряжение в материале, улучшается структурноесостояние, уменьшается количество дефектов.
При возврате заметных изменений в структуре металла не наблюдается. Он сохраняет слоистое или волокнистое строение. Механические свойства материала также не изменяются.
2.4. Рекристаллизация наклепанного металла
При нагревании до высоких температур (выше температуры возврата) подвижность атомов возрастает и происходит процесс рекристаллизации.
Рекристаллизация – процесс образования и роста новых равноосных зерен взамен деформированных при наклепе.
Минимальная температура, при которой начинается процесс рекристаллизации, называется температурным порогом рекристал-
лизации и определяется по следующей зависимости: Трек = βТпл (формула Бочвара). Для металлов высокой чистоты β = 0,25…0,35, для технических металлов β = 0,35…0,45, для сплавов и соединений
β = 0,5…0,8.
На практике температуру рекристаллизации выбирают на 100– 150 градусов выше, по сравнению с расчетной, для уверенности прохождения процесса.
15
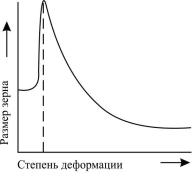
При рекристаллизации происходит существенное изменение свойств металлов, противоположное изменению свойств при наклепе: понижается твердость и прочность металла и возрастают пластические характеристики.
2.5. Понятие критической степени деформации
На свойства металлов большое влияние оказывает размер зерен, образовавшихся в процессе рекристаллизации. В результате образования крупных зерен начинают понижаться прочностные характеристики металлов.
Основными факторами, определяющими величину зерна в процессе рекристаллизации, является температура, время выдержки при этой температуре, степень предварительной деформации.
Наиболее крупные зерна образуются после незначительной предварительной деформации (3–10 %). Такую степень деформации называют критической (рис. 2.3).
Рис. 2.3. Зависимость степени деформации от размера зерна
Критическая степень деформации – такая степень деформа-
ции, при которой образуются наиболее крупные зерна, что обусловливает значительное снижение всех механических свойств в этом металле. Наилучшие физико-химические свойства получаются у металлов, когда обработку давлением проводят при степенях деформа-
16
ции, намного превышающих Екр. В этом случае образуются мелкие зерна в материале, которые обеспечивают высокие механические свойства.
Контрольные вопросы
1.Дайте определение деформации. Какие виды деформации вы знаете?
2.Что такое упругая деформация? Ее краткая характеристика.
3.Что такое пластическая деформация и механизм сдвига при пластической деформации?
4.Что такое прочность и как определяются характеристики прочности?
5.Назовите основные характеристики прочности. Как они определяются?
6.Характеристика горизонтального участка на диаграмме растяжения.
7.Назовите характеристики пластичности. Как они определя-
ются?
8.Устройство и принцип работы маятникового копра.
9.Способы определения твердости.
10.Что такое наклеп и как меняются свойства металла при этом явлении?
11.Дайте характеристику явлению возврата.
12.Дайте определение процессу рекристаллизации. Как изменяются свойства металла при этом явлении?
13.Понятие критической степени деформации.
17
Глава 3 ДИАГРАММЫ СОСТОЯНИЯ СПЛАВОВ
3.1. Основные понятия в теории сплавов
Сплавами называются сложные вещества, полученные сплавлением двух и более простых веществ.
Метод получения сплавов: плавление чистых веществ; диффузия, методы порошковой металлургии и др.
Преимущества: обладают более высокими механическими свойствами и эксплуатационными характеристиками по сравнению
счистыми металлами.
Косновным понятиям в теории сплавов относятся: компонент, система, фаза.
Компоненты – вещества (элементы, соединения), которые применяют для получения сплавов. Компонент, преобладающий в сплаве количественно, называется основным.
Совокупность компонентов сплава называется системой. Фазой называется однородная часть сплава, отделенная от
других частей поверхностью раздела, при переходе через которую химический состав и структура материала изменяется скачком.
3.2. Кристаллизация металлов и сплавов
Металлы и металлические сплавы получают чаще всего кристаллизацией из жидкого состояния. Методом термического анализа можно построить кривые нагрева или охлаждения металла.
В огнеупорный тигель, содержащий расплавленный металл, погружают термопару, концы которой подсоединяют к гальванометру, показывающему температуру (рис. 3.1). Температуру фиксируют через равные промежутки времени.
Полученные кривые неодинаковы для аморфного и кристаллического тел. Затвердевание аморфного тела происходит постепенно без явных границ между твердым и жидким состояниями.
18
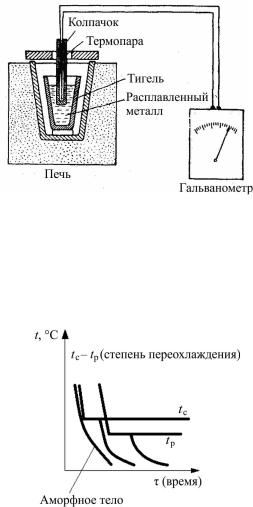
Рис. 3.1. Схема термического анализа
При превращении кристаллического тела из жидкого в твердое состояние при tс появляется горизонтальная площадка, которая объясняется выделяющейся скрытой теплотой кристаллизации, компенсирующей отвод тепла (рис. 3.2).
Рис. 3.2. Превращение аморфного
икристаллического тела из жидкого
втвердое состояние
При очень медленном охлаждении в системе идет равновесный процесс кристаллизации и tс соответствует равновесной температуре. При более быстром охлаждении температура кристаллиза-
19
ции сдвигается до температуры переохлаждения tp. Разность температур tс – tp называется степенью переохлаждения.
Сначала процесс кристаллизации протекает быстро, но при взаимном столкновении рост кристаллов замедляется. Пока кристаллы окружены жидкостью, они имеют правильную форму. Однако при столкновении и срастании их правильная форма нарушается. При затвердевании границы принимают округлую форму, и такие кристаллы называют зернами или кристаллитами.
Процесс кристаллизации металла из жидкости состоит из двух одновременно протекающих стадий: образование зародышей (центров кристаллизации) и роста кристаллов.
Центрами кристаллизации являются либо затвердевшие мельчайшие частицы металла, либо частицы примесей.
При небольших степенях переохлаждения, когда скорость роста зародыша велика, а скорость образования зародышей мала, формируются крупнозернистые структуры.
При увеличении переохлаждения скорость образования зародышей увеличивается более интенсивно, чем скорость их роста, и образуются более мелкие кристаллы в металле.
При быстром росте кристаллов по трем направлениям образуются кристаллы древообразной формы, которые называются дендритами. Такая структура характерна для металлических слитков.
3.3.Взаимодействие компонентов при образовании сплавов
Впроцессе кристаллизации металлов из жидкого состояния могут образоваться следующие сплавы:
1. Механические смеси. Образуются, когда из жидкого расплава выпадают кристаллы составляющих его компонентов. Компоненты не склонны к взаимному растворению и не взаимодействуют друг с другом, кроме того, они имеют различные кристаллические решетки.
2. Твердые растворы. В твердых растворах сохраняется решетка одного из компонентов, а второй компонент, утратив свое кристаллическое строение, распределяется в первом в виде отдель-
20