
книги / Управление инновационными проектами
..pdfКаждый вид технологических процессов характеризуется следующими признаками:
основным назначением – рабочий и перспективный. Рабочий – для изготовления конкретного изделия в соответствии с требованиями рабочей технической документации. Перспективный – как информационная основа для разработки рабочих технологических процессов при техническом и организационном перевооружении производства. Он рассчитан на применение более совершенных способов обработки, более производительных и экономически эффективных средств технологического оснащения и изменения принципов организации производства;
степенью детализации описания:
1)маршрутное описание технологического процесса –
сокращенное описание всех технологических операций
вмаршрутной карте в последовательности их выполнения без указания переходов и технологических режимов;
2)операционное описание технологического процесса –
полное описание всех технологических операций в последовательности их выполнения с указанием переходов и технологических режимов;
3)маршрутно-операционное описание технологического процесса – сокращенное описание технологических операций
вмаршрутной карте в последовательности их выполнения без указаний переходов и режимов обработки с полным описанием отдельных операций в других технологических документах.
Глубина проработки технологических процессов и степень их детализации зависят от стадии подготовки и организационного типа нового производства. В единичном и опытном производстве при высокой квалификации персонала нередко ограничиваются лишь разработкой межцеховых маршрутных технологий. В серийном и массовом производстве маршрутные технологические карты (расцеховки) со-
121
ставляются лишь на первой стадии технологической подготовки и являются основой для последующей детальной кооперационной проработки.
Основные виды работ технологической подготовки производства следующие:
Выбор или установление типа производства.
Выбор исходных заготовок.
Выбор технологических баз для обработки и составление предварительного маршрута обработки изделия.
Подбор типовых или групповых технологических процессов.
Уточнение предварительного маршрута – плана обра-
ботки.
Определение последовательности выполнения и содержания технологического процесса по всем операциям.
Определение, подбор и заказ новых средств технологического оборудования и оснащения, в том числе средств контроля и испытаний.
Выбор и расчет режимов резания (обработки).
Нормирование технологического процесса по всем операциям.
Определение профессий и квалификации исполни-
телей.
Организация производственных участков, поточных линий, отделений и цехов.
Выбор средств механизации и автоматизации отдельных операций и в целом технологического процесса.
Определение операционного транспорта.
Составление технологических планировок.
Определение технологической рабочей документации. Общий порядок работ по технологической подготовке
производства нового продукта представлен на рис. 24.
122
Схема разработки технологической документации механической обработки деталей на предприятии представлена на рис. 25.
Форма организации технологических процессов изготовления изделия зависит от установленного порядка выполнения операций технологического процесса, расположения технологического оборудования, количества изделий и направления их движения в процессе изготовления.
ГОСТ 14.312–74 устанавливает две формы организации технологических процессов:
групповая;
поточная.
Групповая форма организации технологических процессов характеризуется однородностью конструктивно-техноло- гических признаков изделий, единством средств технологического оснащения одной или нескольких технологических операций и специализации рабочих мест.
Поточная форма организации технологических процессов характеризуется:
специализацией каждого рабочего места на определенной операции, согласованным и ритмичным выполнением всех операций технологического процесса на основе постоянства такта выпуска;
размещением рабочих мест в последовательности, строго соответствующей технологическому процессу.
Факторы, определяющие форму организации технологического процесса, и соответствующие ей характеристики следует выбирать в следующем порядке:
определяют виды изделий;
группируют изделия по общности конструкторскотехнологических признаков;
устанавливают тип производства изделий и их составных частей;
123
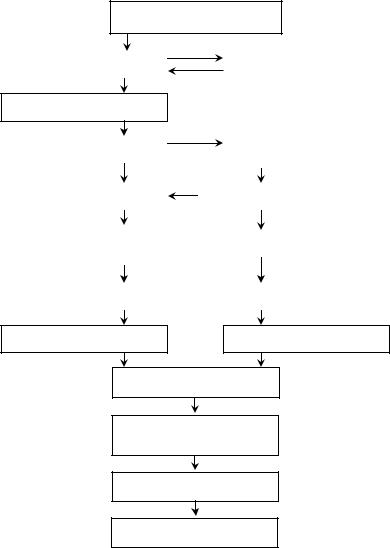
Получение задания на разработку технологической документации
|
|
Проработка конструкторской |
|
Проработка конструкторской |
|||
|
документации на технологичность |
||
документации на технологичность |
|
||
|
для станков с ЧПУ |
||
|
|
Определение маршрута механической обработки
|
|
|
|
Разработка программных операций |
|
Выдача заявок на разработку |
|
|
(выбор оборудования, оснастки, |
||
программ для станков с ЧПУ |
|
|
|
инструмента) |
|
|
|
|
|||
|
|
|
|
|
|
|
|
|
|
|
|
Оформление списков оснащения |
|
|
Разработка программ для станков |
||
|
|
с ЧПУ с помощью ЭВМ |
|||
|
|
|
|
||
|
|
|
|
|
|
Составление карт исходных дан- |
|
|
Разработка КИД и эскизов |
||
ных (КИД) технологических про- |
|
|
|||
|
|
программных операций |
|||
цессов. Оформление эскизов |
|
|
|||
|
|
|
|
||
|
|
|
|
||
|
Ввод оператором КИД в ЭВМ |
|
|||
|
|
|
|
|
|
Контроль введенной исходной информации через распечатку
Контроль введенной исходной информации через дисплей
Вывод готового технологического процесса на формат и его проверка
Согласование технологического процесса со службами и цехами завода
Передача технологического процесса в ОТД
Этап освоения изготовления деталей в производстве
Рис. 25. Схема разработки технологической документации механической обработки деталей на предприятии
124
учитывают программу выпуска каждого изделия и календарные сроки их выпуска;
определяют длительность производственных процессов и наладок технологического оборудования;
определяют потребное количество оборудования и коэффициенты его загрузки;
определяют показатель относительной трудоемкости. Основой при групповой форме организации технологи-
ческих процессов является группирование изделий по конст- руктивно-технологическим признакам.
Группы изделий для обработки в определенном структурном подразделении (цехе, участке и т.д.) устанавливаются с учетом трудоемкости обработки и объема выпуска. По результатам анализа классификационных групп изделий и показателей относительной трудоемкости следует устанавливать профиль специализации каждого структурного подразделения (цеха, участка и т.д.), отбирать и закреплять изделия за подразделениями.
Завершается технологическая подготовка проектированием, изготовлением и отладкой технологической оснастки для реализации разработанных технологических процессов. Принципиальное значение на этой стадии имеет определение экономически целесообразного уровня технологического оснащения.
Для оценки уровня технологической оснащенности используются показатели общего количества оснастки и различных ее видов по изделию, относительное количество оснастки в расчете на одну деталь, затраты на оснастку, производительность оборудования, удельный вес прогрессивных видов оснастки и др.
По формам организации различают внутризаводскую и внезаводскую технологическую подготовку производства. На предприятии технологическое обеспечение производства осуществляют службы главного технолога. К ним относится
125
отдел главного технолога, конструкторское бюро по оснастке, инструментальные производства, нормативно-плановые службы. Планирование и координацию всех работ по подготовке производства новых продуктов осуществляет, как правило,
специальная служба – Бюро планирования подготовки и про-
изводства (БППП), находящаяся в подчинении главного инженера предприятия.
5.6.3. Организационно-производственная подготовка
Организационно-производственная подготовка вклю-
чает календарное планирование производственного процесса изготовления изделия в установленные сроки, в заданном объеме выпуска и затратах.
Контрольные вопросы
1.Что такое жизненный цикл и из каких этапов он состоит?
2.В чем состоят особенности менеджмента на каждом этапе жизненного цикла?
3.Как вы понимаете исследовательскую и конструкторскую составляющие инновационного проекта? Какую роль вы могли бы им отвести, что принципиально их отличает от остальных этапов инновационного проекта?
4.Что включает в себя этап производства, какое влияние оказывает технология производства на инновационный проект в целом?
126

Глава 6 ПЛАНИРОВАНИЕ ПРОИЗВОДСТВЕННЫХ РЕСУРСОВ
6.1. Методы управления предприятиями
Развитие методов управления промышленными предприятиями в начале ХХ в. связывают прежде всего с именами
Фредерика Тейлора и Генри Гантта. Ф. Тейлор (Frederick W. Taylor) является создателем производственного планирования как дисциплины. Он исследовал факторы, влияющие на производительность, и методы рациональной организации рабочего времени. На основе анализа тысяч экспериментов были сформулированы рекомендации по организации промышленного производства и по обучению кадров. Фредерик Тейлор выдвинул идею узкой специализации, выделил планирование как важнейший элемент организации производства и считал, что производственным планированием должны заниматься профессиональные менеджеры.
Генри Гантт (Henry L. Gantt) работал вместе с Ф. Тейлором над количественными методами организации производства. Один из методов наглядного упорядочения работ – диаграммы Гантта (Gantt Charts) – и сегодня считается одним из стандартов де-факто. Идея Гантта состояла в том, что главным ресурсом планирования является время, а основой принятия управленческих решений – сравнение запланированного и фактического состояния работ. На диаграммах Гантта по горизонтали обычно показывают интервалы времени, а по вертикали – работы, операции, оборудование. Горизонтальные отрезки отражают длительность выполнения работ. Выбрав по горизонтальной оси текущий момент времени и получив оперативную информацию о ходе производства, можно сопоставить фактическое и планировавшееся состояние дел.
127
Все современные системы управления проектами и планирования предлагают представление графиков работ в виде диаграмм Гантта. В то же время диаграммы Гантта имеют ряд очевидных недостатков. Например, с помощью диаграмм Гантта неудобно планировать многовариантные взаимосвязанные цепочки работ (в строительных, военных, государственных проектах, производстве). Для таких задач в военном ведомстве США в 50-е гг. были предложены методы сетевого планирования, или методы выбора «критического пути». Кроме того, диаграммы Гантта удобно применять только для одного критического ресурса – времени. При необходимости учета еще нескольких ресурсов, например технологической оснастки, диаграммы Гантта нужно воспринимать как «объемные», приобретающие ряд измерений по числу учитываемых ресурсов. Это удобно для визуальной интерпретации планов, но затрудняет их анализ.
Работы Ф. Тейлора и Г. Гантта легли в основу научных дисциплин, возникших в середине ХХ в.: промышленной ин-
женерии (Industrial Engineering), занимающейся управлением
иорганизацией производства, а также исследования операций (Operations Research). С исследованием операций связаны работы по применению математических методов формализации человеческой деятельности, в том числе в производстве
ипланировании. Разработаны многие статистические и оп-
тимизационные алгоритмы планирования, используемые в современных системах. Например, в SAP R/3 для прогнози-
рования потребностей в продукции (функция Forecast) с уче-
том информации о фактическом спросе за предыдущие периоды используются статистические и эвристические методы (расчеты сезонных колебаний спроса, расчеты по трендам). Еще одним примером являются методы оперативного планирования (функция Scheduling), подсистемы планирования производства (PP) SAP R/3, в которых «зашиты» алгоритмы расчета даты выполнения заказа, сокращения длительности
128
производственного цикла, минимизации переналадок оборудования и др. (Заметим, что SAP R/3 упоминается как пример реализации упоминаемых здесь и далее функций.)
В начале 60-х гг. в США начались работы по автомати-
зации управления запасами (Inventory Control). В результате активного роста крупносерийного и массового производства товаров народного потребления и торговли после Второй мировой войны стало очевидно, что использование математических моделей планирования спроса и управления запасами ведет к существенной экономии средств, замороженных в виде запасов и незавершенного производства. Невозможно разработать «абсолютно оптимальные методы планирования запасов», поэтому следует выбирать и адаптировать алгоритмы к специфике конкретных складских задач в зависимости от цикла производства или поставок хранимой номенклатуры, стоимости, размеров изделий, расфасовки, применяемости и спроса, объемов складов и т.д. Было установлено, что выбор оптимального объема партии заказа – одно из важнейших условий повышения эффективности предприятия, так как их недостаточный объем ведет к росту административных расходов при повторных заказах, а избыточный – к замораживанию средств.
Управление складами (Inventory Control) в современных системах управления основано на математических методах управления запасами. Например, в подсистеме MM управления материальными потоками SAP R/3 может использоваться планирование пополнения склада на основе прогноза или по достижении минимального уровня запаса (по «точке заказа»). Предлагаются более десяти вариантов расчета оптимальной партии заказа, а также возможности включения в систему алгоритмов, разработанных пользователем.
Первые автоматизированные системы управления запасами в промышленном производстве основывались на расчетах по спецификации состава изделия (Bill of Materials). По
129
плану выпуска изделия формировались планы производства и рассчитывался объем закупки материалов и комплектующих изделий [APICS92].
Конец 60-х гг. связан с работами Оливера Уайта (Oliver Wight, который в условиях автоматизации промышленных предприятий предлагал рассматривать в комплексе производственные, снабженческие и сбытовые подразделения. Такой подход и применение вычислительной техники впервые позволили оперативно корректировать плановые задания
впроцессе производства (при изменении потребностей, корректировке заказов, недостатке ресурсов, отказах оборудования).
Впубликациях Оливера Уайта и Американского общества по управлению запасами и управлению производством
[APICS92] были сформулированы алгоритмы планирования,
сегодня известные как MRP (Material Requirements Planning) – планирование потребностей в материалах –
вконце 60-х гг., и MRP II (Manufacturing Resource Planning) – планирование ресурсов производства – в конце
70-х – начале 80-х гг.
Не все современные концепции управления возникали
вСША. Так, метод планирования и управления Just-in-time (JIT – Точно вовремя) появился на предприятиях автомобильного концерна в 50-х гг. Он охватывает проектирование изделий, выбор поставщиков, обеспечение качества, планирование, учет производства и контроль (с использованием специальных бирок-ярлыков Kanban). Одна из важнейших концепций метода «точно вовремя» связана с минимизацией страховых и межоперационных заделов за счет стабилизации поставок, а также обеспечения резерва производственных мощностей. Метод «точно вовремя» не противоречит MRP и MRP II и часто предлагается в современных системах как одна из форм организации производства. Однако до сих пор он не соответствовал традиции отечественной промышлен-
130