
книги / Технология ковки и объёмной штамповки
..pdfМинистерство образования и науки Российской Федерации
Федеральное государственное бюджетное образовательное учреждение высшего профессионального образования «Пермский национальный исследовательский политехнический университет»
Г.Л. Колмогоров, Т.Е. Мельникова
ТЕХНОЛОГИЯ КОВКИ И ОБЪЕМНОЙ ШТАМПОВКИ
Рекомендовано Редакционно-издательским советом университета
в качестве учебного пособия
Издательство Пермского национального исследовательского
политехнического университета
2014
1
УДК 621.73.043 (075.8) К60
Рецензенты:
канд. физ.-мат. наук, проф. А.А. Лежнева (Пермский национальный исследовательский политехнический университет)
Колмогоров, Г.Л.
К60 Технология ковки и объемной штамповки: учеб. пособие / Г.Л. Колмогоров, Т.Е. Мельникова. – Пермь: Изд-во Перм. нац. исслед. политехн. ун-та, 2014. – 34 с.
ISBN 978-5-398-01273-6
Изложены основные понятия дисциплины «Технология ковки и объемной штамповки».
Предназначено для студентов заочного обучения направления 651400 – «Машиностроительные технологии и оборудование» специальности 120400 – «Машины и технология обработки металлов давлением».
УДК 621.73.043 (075.8)
ISBN 978-5-398-01273-6 |
© ПНИПУ, 2014 |
2
|
ОГЛАВЛЕНИЕ |
|
Введение................................................................................................ |
4 |
|
1. |
Характеристика исходных материалов и основные |
|
технологические операции.................................................................. |
7 |
|
2. |
Ковка. Основные технологические операции.............................. |
10 |
3. |
Объемная штамповка..................................................................... |
16 |
4. |
Холодная объемная штамповка..................................................... |
26 |
Вопросы для самоконтроля студентов............................................. |
33 |
|
Список литературы............................................................................. |
33 |
3
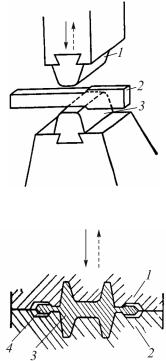
ВВЕДЕНИЕ
Способность металла принимать значительную пластическую деформацию в горячем и холодном состоянии широко используется в технике. При этом изменение формы осуществляется преимущественно с помощью давящего на металл инструмента.
Пластическая обработка металлов прерывистым воздействием универсального инструмента или соответствующей рабочей частью специального инструмента (штампа) для придания телу заданной формы и размеров называется в первом случае ковкой, а во втором – штамповкой.
Рис. 1. Схема процесса ковки
Рис. 2. Схема штамповки: 1 – верхняя часть штампа; 2 – нижняя часть штампа; 3 – изделие; 4 – облой (заусенец)
4
При ковке (рис. 1) деформирование заготовки 2 осуществляется с помощью универсального подкладного инструмента или бойков 1 и 3. Бойки чаще всего бывают плоскими, однако применяют вырезные и закругленные бойки. Нижний боек обычно неподвижен, верхний совершает возвратно-поступа- тельное движение. В результате многократного и непрерывного воздействия инструмента заготовка принимает необходимую форму и размеры.
При объемной штамповке придание заготовке заданной формы и размеров осуществляется путем заполнения металлом рабочей полости штампа (рис. 2).
Данными способами обработки давлением получают весьма разнообразные по форме и размерам изделия из металлов, полимеров и других материалов с различной степенью точности размеров, разными механическими и другими характеристиками и качеством поверхности. Поэтому ковочно-штамповочное производство находит широкое применение в машиностроении и приборостроении, в производстве предметов народного потребления и в других отраслях промышленности. Получение изделий ковкой и штамповкой позволяет максимально приблизить исходную форму заготовки к форме и размерам готовой детали и тем самым уменьшить или полностью исключить дорогостоящие операции резания с потерей металла в стружку. При изготовлении деталей из прокатных заготовок на машиностроительных заводах с использованием металлорежущих станков теряется в виде стружки до 30…40 % металла. Предварительная обработка этих заготовок методами ковочноштамповочного производства снижает эти отходы в 4…5 раз, уменьшает парк металлорежущих станков и дает значительную экономию средств. Кроме того, ковка и штамповка улучшают свойства металла, вследствие чего наиболее ответственные детали многих машин и приборов часто изготовляют только из поковок.
Значение ковочно-штамповочного производства подтверждается огромным разнообразием получаемых изделий, номенклатура выпуска которых превышает 500 000 типов, а всего методами ковкиштамповки обрабатывают 7…8 % выплавляемой в стране стали. Причем выпуск поковок современного цеха серийного производства составляет 150…200 тыс. т в год, крупносерийного производства – 200…300 тыс. т в год, а производительность кузнечных заводов до 400…500 тыс. т в год. Практически каждый машиностроительный завод имеет ковочно-штамповочные цехи, которые в зависимости от степени специализации, производительности, типа основного оборудования можно подразделить на специализированные, универсальные и смешанные. В качестве примера приводятся следующие под- разделенияковочно-штамповочного производства:
1. Кузнечные цехи ковки, изготавливающие единичные и мелкосерийные изделия: чаще всего встречаются на металлургических,
5
судостроительных и других заводах. В таких цехах ковкой на молотах производятся сравнительно небольшие поковки(массойдо 1 т).
2.Кузнечно-прессовые цехи ковки, изготовляющие единичные и мелкосерийные поковки значительной массой (до 250 т и более). Основными машинами таких цехов являются гидравлические и парогидравлические прессы.
3.Ковочно-штамповочные цехи, выпускающие поковки массой до 1000 кг крупносерийного и массового производства, предназначенные для изготовления автомобилей, тракторов, самолетов и других машин; основными агрегатами таких цехов являются штамповочные молоты и прессы, горизонтально-ковочные машины и пр.
4.Холодно-прессовые цехи, изготовляющие изделия холодной штамповкой из листового материала. Такие цехи предназначаются для производства крупносерийных и массовых деталей, которые поступают обычно на сборку без существенной дополнительной обработки.
5.Специализированные цехи, которые определяются типом выпускаемых массовых изделий (пружинные, рессорные, метизные и др.) или типом установленного оборудования (например, цехи холодно-высадочных автоматов и др.).
Прогресс современного машиностроения в значительной мере определяется состоянием ковочно-штамповочного производства, поэтому развитию этих видов обработки давлением уделяется серьезное внимание.
6

1.ХАРАКТЕРИСТИКА ИСХОДНЫХ МАТЕРИАЛОВ
ИОСНОВНЫЕ ТЕХНОЛОГИЧЕСКИЕ ОПЕРАЦИИ
Для процессов ковки исходными материалами являются слитки, масса которых может составлять от нескольких килограммов до 250…350 т, и прокатные заготовки. Для горячей штамповки используют кованую, прокатанную, прессованную заготовки и заготовки, получаемые волочением, а также жидкий металл.
Все основные положения теории обработки металлов давлением, касающиеся механизма пластического деформирования, энергосиловых параметров, термомеханических режимов и прочих, полностью применимы при деформировании металла ковкой и штамповкой.
В условиях ковочно-штамповочного производства характеристикой деформирования при протяжке или осадке является величина укова, которая определяется степенью изменения поперечного сечения изделия или степенью изменения высоты заготовки в процессе осадки. При протяжке слитка участками обеспечивается турбулентность течения деформируемого металла, что способствует разрушению дендритной структуры, а следовательно, интенсивному выравниванию механических свойств в продольном и поперечном направлениях при повышении общего уровня этих характеристик. При ковке слитков из углеродистой стали высокие механические свойства достигаются при размере укова не менее 2,5; при ковке легированной стали уков должен быть 3…4. При дальнейшем увеличении степени деформации наблюдается лишь слабое изменение механических свойств металла. Подобные показатели при прокатке достигаются не менее чем при 7-кратной вытяжке, 10-кратном волочении.
Важной величиной, влияющей на свойства металла поковки, является относительная подача при протяжке, которая определяет-
ся отношением Hl , где l – подача; H – высота обжимаемого тела в данный момент обработки (рис. 3).
7
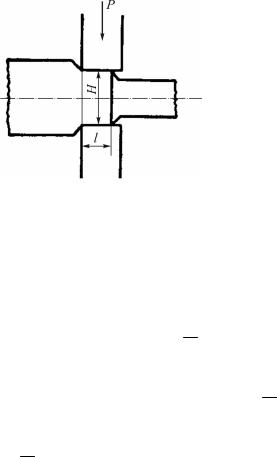
Рис. 3. Очаг деформации при протяжке
Известно, что для устранения пороков слитка (уплотнение металла, заварка внутренних неплотностей, раздробление дендритной структуры и др.) ковку необходимо вести в условиях всестороннего неравномерного сжатия и не допускать появления растягивающих напряжений в отдельных частях поковки.
При протяжке с относительной подачей Hl < 0,5 в централь-
ной части поперечного сечения заготовки возникают продольные растягивающие напряжения. При протяжке с подачей Hl > 0,5
действуют только напряжения сжатия, поэтому рекомендуется протяжка с подачей Hl > 0,5.
Выбирая технологические операции производства поковок, необходимо учитывать направление волокна в исходной заготовке, которое получается при предварительном деформировании (например, при прокатке), и в готовом изделии. Металл изделия при волокнистом строении характеризуется анизотропией свойств. Поэтому в процессах ковки и штамповки способ обработки выбирают таким, чтобы обеспечить расположение волокон, отвечающее максимальному повышению механических свойств металла в нужном направлении.
8

Наглядным примером необходимости учета направленности волокон является изготовление коленчатых валов. Если коленчатый вал изготовить механической обработкой на металлорежущих станках, то волокна в элементах вала получаются подрезанными (рис. 4, а), что снижает прочность этих участков. Если при изготовлении коленчатого вала применяют операции гибки или передачи металла, то получают волокнистую структуру, расположенную по контуру вала (рис. 4, б), а следовательно, повышенную его прочность.
Рис. 4. Расположение волокна в поковке коленчатого вала в зависимости от способа его изготовления
Для получения изделий ковкой и штамповкой приходится иметь дело с подготовкой, пластической обработкой и отделкой, поэтому технологические операции подразделяются на три основные группы: подготовительные; собственно ковочно-штамповоч- ные; отделочные.
Подготовка включает такие операции, как сортировка, разрезка на мерные длины, удаление поверхностных дефектов, при необходимости термическую обработку и др.
Если деформирование выполняется в горячем состоянии, возникает необходимость нагрева металла. При ковке часто нагрев выполняется в камерных печах, а нагрев крупных слитков – в печах с выдвижным подом. При горячей штамповке наряду с пламенными печами применяют индукционный нагрев, так как при нем быстро достигается необходимая температура, что сокращает потери металла в окалину по сравнению с нагревом в пламенных печах с 2,5…3 до 0,5…1 % и практически исключается обезуглероживание поверхностного слоя. Для заготовок большой длины при диаметре 60…70 мм используют контактный нагрев.
9
К ковочно-штамповочным операциям относят операции, непосредственно связанные с изменением формы исходной заготовки в пластическом состоянии. Принятый технологический цикл должен обеспечить производство изделий с определенной точностью их геометрической формы и размеров, с механическими свойствами, структурой, отсутствием поверхностных и внутренних дефектов. При проектировании технологического процесса предусматривается периодический контроль качества изделия.
Отделочные операции включают такие виды обработки, как обрезка облоя (заусенца) или других отходов, калибровка для повышения точности размеров и формы изделия и улучшения качества поверхности, термическая обработка, правка, очистка и травление, гальванические и декоративные покрытия, оксидирование, анодирование и пр.
2. КОВКА. ОСНОВНЫЕ ТЕХНОЛОГИЧЕСКИЕ ОПЕРАЦИИ
При получении изделий ковкой исходный продукт обрабатывают многократным прерывистым воздействием универсального инструмента – молота или пресса. Смещаемый объем перемещается по контактной поверхности инструмента. Ковка находит применение при единичном и мелкосерийном производстве и выполнении ремонтных работ. Данным способом изготовляют тяжелые поковки (до 250 т и более – валы гидротурбин, цельнокованые паровые котлы и др.), поковки средней массы (50…400 кг – коленчатые валы крупных машин, маховики, диски и др.) и мелкие поковки массой до 50 кг разнообразного назначения.
Технологическиепроцессы ковки представляют собойразличные сочетания и последовательность основных и вспомогательных операций, таких как биллетировка, осадка, протяжка, разгонка, прошивка, гибка, скручивание, рубка, кузнечная сварка и другие, а также операцииотделкии термической обработкипринеобходимости.
Ковку выполняют с применением кузнечного инструмента, который подразделяется на основной, обеспечивающий деформацию металла (рис. 5), и вспомогательный, используемый для удер-
10