
книги / Методы нанесения покрытий
..pdfженного кристаллического строения. Значение этой критической температуры в большинстве случаев соответствует 1/3 от температуры плавления напыляемого материала покрытия.
Температура ведения процесса при промежуточных ее значениях оказывает большое влияние на структуру и свойства формируемых покрытий. Понижение температуры подложки способствует получению мелкозернистых осадков, однако увеличение при этом разницы в температурах подложки и конденсирующегося слоя приводит к росту возникающих термических напряжений, ухудшая сцепление слоя с основой. Повышение же температуры покрываемой поверхности, приводящее к укрупнению зернистого строения покрытия, вызывает увеличение шероховатости поверхностислоя, снижениетвердостииизносостойкости покрытия.
Существенная температурная зависимость качества наносимого слоя покрытия от температурных режимов на покрываемой поверхности требует создания способов расчета этой температуры при нанесении покрытий различными методами вакуумного напыления, а также принятия технологических и конструктивных решений, обеспечивающих поддержание заданной температуры процесса при создании покрытий, особенно при непрерывных (поточных) методах организации производства.
8.2. Способы получения ионно-плазменных покрытий
Теорияитехнологияполученияпокрытийнапылением ввакууме. Нанесение вакуумных покрытий,
их назначение и свойства
Простейшей классической газовой средой, содержащей наносимый на поверхность материал при нанесении покрытий, является паровая среда, получение которой возможно в вакууме, исключающем загрязнение этой среды кислородом.
Паровая среда может быть создана в виде газовой смеси снейтральными газами, не ухудшающими качество пара наносимого вещества и не взаимодействующими с обрабатываемой поверхностью самостоятельно. Создание такой паровой среды может
51
быть выполнено при осуществлении испарения или распыления материала покрытия в вакууме. Интерес к технологиям покрытия ввакууме расширяется в последнее время в связи с разработкой высокоэффективных высокоэкономичных вакуумных систем
иагрегатов, конкурирующих по своей производительности, энергетическим и финансовым затратам с другими видами оборудования итехнологическими процессами. Принципиально новые возможности открываются в связи с развивающимися космическими технологиями. Основные преимущества методов нанесения покрытий в вакууме– это универсальность технологии и высокие скорости нанесения покрытий, в том числе в непрерывном режиме осуществления производственных технологических процессов. Конечно, следует иметь ввиду, что вакуумные покрытия наиболее эффективно могут быть использованы в тех случаях, когда другимиметодами покрытияполучитьневозможноилизатруднительно.
Большим преимуществом методов покрытий в вакууме является полное исключение водородной хрупкости, свойственной всем процессам электрохимического нанесения покрытий из растворов. Методы вакуумного напыления позволяют получить покрытия практически на любом материале. Одна и та же вакуумная установка может быть использована для получения покрытий из различных металлов и сплавов. При этом возможно получать сложнолегированные покрытия различного конструкционного построения, в том числе однородные, послойные или дисперсно-упрочненные. Применение вакуумного напыления позволяет получать односторонние покрытия либо покрытия разной толщины на разные стороны одного и того же изделия (или даже из разных металлов).
Процессы напыления в вакууме позволяют совмещать в едином технологическом процессе непосредственно напыление слоя
ипоследующую его термическую обработку, в ряде случаев обеспечивающую формирование диффузионных зон слоя либо полное расходование напыленного покрытия для диффузионного взаимодействия с основой металла. Это обеспечивает улучшение взаимодействия нанесенного покрытия с материалом основы и достижение принципиально новых качеств поверхности, обусловленных
52

изменением химического состава поверхностных слоев, например повышение коррозионной стойкости, повышение износостойкости идругихкачеств эксплуатационногохарактера.
Существует три разновидности процессов нанесения покрытий в вакууме: катодное распыление, термическое напыление и ионное осаждение.
Катодное распыление – это процесс, в котором мишень, изготовленная из материала покрытия, распыляется при ее бомбардировке положительными ионами. Распыленные частицы осаждаются затем на поверхности подложки (изделия), образуя покрытие. Если распыляется диэлектрик, то он помещается на проводящем электроде (катоде); если распыляется металл, то он может быть либо целиком катодом, либо его частью.
Распыление материала катода может происходить по двум механизмам: 1) выбивание частицы в результате прямой передачи импульса от ударяющего иона поверхностному атому на распыляемом катоде; 2) энергия, выделяющаяся в зоне удара, обеспечивая локальный нагрев, может создавать условия, сходные с термическим испарением материала в вакууме. Характер распыления материала катода описывается некоторыми количественными характеристиками.
Во-первых, процесс катодного распыления характеризуется эффективностью распыления S, под которой понимается количество распыленных атомов мишени, приходящихся на один бомбардирующий ион.
При бомбардировке, кроме распыляемых атомов мишени, выбиваются и вторичные электроны, создающие в ионном пространстве вторичный ионный ток i, который во внешней электрической цепи измеряется как добавочный ток, обусловленный ионами. Эффективностьраспыления, такимобразом, определяется как
S = iNt ,
гдеN – числораспыленныхатомов; t – времябомбардировки; i = i(+) + i(–) – измеренныйсуммарныйтоквовнешнейэлектрическойцепи.
53
Эффективность распыления зависит от природы иона, его массы, энергии и направления движения, а также от материала мишени, температуры и давления в камере. Для каждой пары ион–мишень существует пороговая энергия распыления, выше которой скорость распыления резко возрастает с увеличением энергии бомбардирующего иона.
Ниже приведены некоторые значения пороговой энергии в расчете на 1 ион, Дж:
Серебро |
Золото |
Тантал |
Вольфрам |
Кобальт |
6,4–24 10–19 |
32 10–19 |
20,8–41,6 10–19 |
20,8–52,8 10–19 |
9,6–40 10–19 |
С увеличением энергии иона эффективность распыления увеличивается. Однако если энергия иона становится более 10– 20 кэВ (1 кэВ = 1...6–10–16 Дж), наблюдается снижение эффективности распыления, поскольку ионы большую часть своей энергии затрачивают на рассеивание внутри изделия (образца).
Различают три схемы катодного распыления положительными ионами распыляемого материала: диодная, триодная (распыление при низком давлении) и ионно-лучевая.
В диодной схеме катодного распыления положительные ионы образуются в тлеющем разряде постоянного напряжения, в котором распыляемая мишень является катодом. При пропускании электрического тока в возникающем разряде газ в межэлектродном пространстве ионизируется. Положительные ионы газа бомбардируют катод, выбивая ионы распыляемого металла. Вторичные электроны, вылетающие также из мишени, ускоряются в катодном темном пространстве и, сталкиваясь с молекулами газа, образуют дополнительное число положительных ионов, которые также бомбардируют мишень – катод (рис. 8.3, а).
При использовании двух различных катодов можно получать комплексно легированные слои либо при поочередном включении катодовформироватьмногослойныекомпозиционныепокрытия.
При катодном распылении по диодной схеме давление в вакуумной камере должно быть 1–10 Па (0,01–0,1 мм рт. ст.), ускоряю- щеенапряжение1–15 кВ, катоднаяплотностьтока0,1–5,0 мА/см2.
54
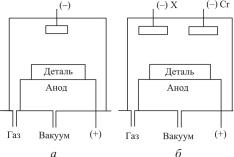
Разновидностью катодного распыления является так называемое химическое распыление, при котором остаточные или специально вводимые газы реагируют с материалом катода и образуют с ним летучие соединения, с помощью которых наносимый материал транспортируется к поверхности и, легко разлагаясь на ней, образует покрытие.
Рис. 8.3. Схемы катодного распыления по диодной схеме при нанесении покрытий: а – одним металлом (с одним катодом);
б – поочередно или параллельно двумя металлами (по двухкатодной схеме)
Другой вариант катодного распыления с использованием химических реакций с вводимой газовой средой – реактивное распыление, при котором происходит распыление в атмосфере кислорода или азота с образованием на защищаемой поверхности слоя окислов или нитридов.
Диодная схема катодного распыления очень проста, однако важнейшим недостатком ее осуществления является низкая скорость распыления и высокая степень загрязненности осадка (слоя), поскольку осаждение покрытия происходит при высоком остаточном давлении газов.
В триодной схеме распыления наносимого материала (рис. 8.4) инертный газ ионизируется потоком электронов из горячего эмиттера (катода). Возникающая при этом плазма разряда фокусируется магнитным полем и может существовать при достаточно низких давлениях (порядка 0,1 Па). Деталь помещают против мишени (катода). Мишень заряжена отрицательно и бомбардиру-
55

ется положительными ионами аргона, распыляющими ее. Распыленные частицы осаждаются на поверхности детали, которую не-
обходимовращатьдляравномерногоеепокрытия. |
|
Экспериментами показано, что при нанесении |
тантала |
с давлением аргона 0,1 Па, напряжением 0,7–1,0 кВ, |
катодной |
плотности тока 3 мА/см2 слой наносимого покрытия нарастает с очень малой скоростью конденсации слоя (20 нм/мин).
Рис. 8.4. Схема катодного распыления при низком давлении (триодная схема): А – анод; К – катод; Д – деталь; П – покрытие; Э – горячий катод (эмиттер электронов); Г – газ; М – магнитная отклоняющая система
Ионно-лучевая схема отличается тем, что в камере с мишенью (деталью) поддерживается низкое давление, высокая степень вакуума.
При включении источника ионов поддерживается низкое давление. Для нанесения покрытия с использованием радиочастотного излучения образец загружают в вакуумную камеру и откачивают воздух до давления порядка 0,00001 Па, после чего в камеру вводят аргон. Высокочастотный источник напряжения создает в атмосфере аргона плазменно-дуговой разряд. Ионы аргона бомбардируют мишень, распыляют ее, и частицы мишени осаждаются на подложке, образуя покрытие на детали.
Если к детали подведен отрицательный заряд, то ионы напыляемого металла будут осаждаться в условиях ускоряющего электрического поля. Это способствует увеличению скорости наращи-
56
вания слоя и улучшению прочности сцепления его с основой. Большим преимуществом методов нанесения покрытий с использованием катодного распыления является возможность ионной очистки поверхности детали непосредственно перед осаждением покрытия. Это повышает качество покрытия и позволяет получать покрытия на любой основе с одновременным обеспечением качественногосцеплениянаносимогослоясизделием.
Методы катодного распыления применяют при нанесении специальных покрытий для оптических и электронно-оптических приборов, для нанесения контактных пленок золота, серебра, платины в электронике. Напыление нитрида тантала и тонких прослоек металлических сплавов используют для создания высокоемких конденсаторов. Тончайшие слои хрома и хромо-платинового покрытия используют для создания износостойких покрытий на лезвия безопасных бритв. Износостойкие покрытия могут быть получены напылением вольфрама, хрома, нержавеющей стали нитрида титана, дисульфида молибдена. Используется этот метод и для создания декоративных покрытий, в том числе и на непроводящую основу. С этой целью используют медь, хром, титан и др. Особенно эффективен этот метод в тех случаях, когда применение метода термического напыления затруднено. Например, он может широко использоваться для получения покрытий тугоплавкими металлами исоединениями наихоснове.
8.3. Магнетронное напыление
Ограничения в применении диодных и триодных систем для промышленных целей были обусловлены низкими скоростями осаждения (0,2–2 нмс–1), высоким рабочим давлением (1–10 Па) ибольшим напряжением, подаваемым на разрядное устройство (2–5 кВ), что снижало производительность процесса и препятствовало получению пленок с минимальным уровнем загрязнений ирадиационных дефектов. Положение коренным образом изменилось после появления распылительных систем магнетронного типа. У этих распылительных систем, работающих при низком напряжении на разрядном промежутке (< 700 В), плазма с помощью магнитного поля локализуется в области разряда, что вызывает осцил-
57

ляцию электронов и значительно увеличивает степень ионизации,
врезультате улучшаются параметры распылительной системы (РС) иувеличивается скорость осаждения. Распыление является низкотемпературным процессом и может применяться для полученияпленокпрактически любыхметаллов.
Принцип действия магнетронной распылительной системы показан на рис. 8.5. Основными элементами устройства являются катод-мишень, анод и магнитная система. При подаче постоянного напряжения между мишенью (отрицательный потенциал) и анодом (положительный или нулевой потенциал) возникает неоднородное электрическое поле и возбуждается аномальный тлеющий разряд. Наличие замкнутого магнитного поля у распыляемой поверхности мишени позволяет локализовать плазму разряда непосредственно у мишени. Эмитированные с катода под действием ионной бомбардировки электроны захватываются магнитным полем, им сообщается сложное циклоидальное движение по замкнутым траекториям у поверхности мишени. Электроны оказываются как бы
вловушке, создаваемой с одной стороны магнитным полем, возвращающим электроны на катод, а с другой– поверхностью мишени, отталкивающей электроны.
Рис. 8.5. Магнетронная схема распыления: 1 – распыляемая мишень; 2 – тлеющий разряд; 3 – натекатель; 4 – поток напыляемых частиц; 5 – напыляемое изделие-подложка; 6 – анод; 7 – постоянный магнит
58
Электроны циклируют в этой ловушке до тех пор, пока не произойдет несколько ионизирующих столкновений с атомами рабочего газа, в результате которых электрон потеряет полученную от электрического поля энергию. Таким образом, большая часть энергии электрона, прежде чем он попадет на анод, тратится на ионизацию и возбуждение, что значительно увеличивает эффективность процесса ионизации и приводит к возрастанию концентрации положительных ионов у поверхности мишени. Это, в свою очередь, обуславливает увеличение интенсивности ионной бомбардировки мишени и значительный рост скорости распыления, а следовательно – и скорости осаждения пленки. Средние скорости осаждения различных материалов с помощью магнетронной распылительной системы, имеющей плоскую дисковую мишень диаметром 150 мм, при мощности источника 4 кВт и расположении подложки на расстоянии 60 мм от источника приведены ниже.
Материал: Si Ti Ta W Nb Mo Al Cr Pt Cu Au Ag. Скорость осаждения, нм/с: 7 8 8 8 8,5 12 13 17 21 30 37 44.
Следует отметить, что плазма разряда существует только в области магнитной ловушки, в непосредственной близости от мишени, и ее форма определяется геометрией и величиной магнитного поля.
Создание магнитной ловушки у распыляемой поверхности мишени представляет собой простое, но весьма эффективное решение проблемы увеличения скорости распыления материалов в плазменных распылительных системах. Помимо этого достоинства магнотронная распылительная система (МРС) обладает рядом специфических свойств, основным из которых является отсутствие бомбардировки высокоэнергетическими вторичными электронами.
Магнетронные системы относятся к низковольтным системам распыления. Напряжение питания не превышает 1000 В постоянного тока. Рабочее напряжение составляет 300–700 В, на мишень обычно подается отрицательный потенциал, а анод
59
имеет нулевой потенциал. Однако в магнетронных системах с плоским катодом для более полного улавливания вторичных электронов рекомендуется на анод подавать небольшое положительное смещение (40–50 В). В некоторых системах предусматривается подача отрицательного напряжения смещения на подложку (до 100 В) для реализации распыления со смещением.
Магнетронная распылительная система может работать в диапазоне давлений от 10–2 до 1 Па и выше. Важнейшими параметрами, во многом определяющими характер разряда в ней, являются геометрия и величина магнитного поля, индукция которого у поверхности мишени 0,03–0,1 Т.
8.4. Газотермическое напыление
Методы газотермического нанесения покрытий (газотермического напыления) объединяют широкий класс технологий, при которых на поверхность обрабатываемых изделий наносят слой металлического или неметаллического вещества (в виде распыленной жидкости или порошков) с целью наращивания изношенных при эксплуатации участков поверхности детали, повышения коррозионной стойкости или устойчивости к износу, а также для создания специальных свойств поверхности. Использование недорогих материалов с покрытиями, например, методами газопламенного напыления, позволяет в ряде случаев отказаться от применения высокодефицитных высоколегированных сталей и сплавов. Этими методами оказывается возможным наносить на поверхность обрабатываемых деталей широкий класс напыляемых материалов – от пластических масс до тугоплавких металлов и твердых и износостойких неорганических соединений, в том числе порошковых.
Методы газотермического напыления включают в себя следующие разновидности: газопламенные; электрические и электродуговые; детонационные; плазменные. Наиболее старой схемой газотермического нанесения покрытий являлась технология распыления струи предварительно расплавленного легкоплавкого металла высокоскоростным потоком нагретого воздуха, при
60