
книги / Теория, практика, тенденции развития оперативно-производственного планирования
..pdf
2. Метод расчета размера партии с учетом кратности штучного времени продолжительности смены. Если на произ-
водственном участке применяется оборудование, не требующее значительного времени на наладку, то размер партии определяется по наиболее производительной операции в технологическом процессе и должен быть равен, как минимум, сменной или полусменной выработке деталей:
n |
|
Tсм |
или n |
|
Tсм |
, |
|
tштmin |
2tштmin |
||||||
min |
|
min |
|
|
где Tсм – продолжительность смены, мин; tштmin – минимальное
штучное время.
3. Метод определения размера партии по показателю спе-
циализации рабочих мест. Его используют в случае, когда этот показатель известен. Определение размера партии должно быть по возможности тесно увязано с основными характеристиками планируемого производства: с масштабом выпуска и трудоемкостью. Показатель специализации рабочих мест Kс означает среднее количество различных производственных работ, выполняемых в течение месяца на одном рабочем месте при работе в одну смену. Известно также, что для данной продукции Kс тем меньше, чем больше масштаб выпуска этой продукции, и наоборот. При одном и том же масштабе выпуска более трудоемкая продукция обеспечит более высокую специализацию рабочих мест, а следовательно, и более низкий показатель Kс. Из этого следует, что каждому значению показателя специализации Kс соответствует свое среднее время, в течение которого каждое рабочее место непрерывно занято производством продукции одного вида.
В соответствии с этим размер партии определяется так:
n Fмес Kо ,
min |
Kc T |
|
41
elib.pstu.ru

где Т – суммарная трудоемкость обработки детали во всех операциях технологического процесса (с учетом коэффициента выполнения норм и процента потерь на переналадку),
|
|
t |
штi |
|
Kв.н ; Kо – |
|
|
T tштi |
|
|
|
число операций в технологиче- |
|||
|
|
|
|||||
|
|
|
100 |
|
|
||
ском процессе; |
Fмес |
– месячный фонд рабочего времени одного |
|||||
рабочего места (за одну смену), |
|
||||||
|
|
|
|
|
Fмес Дp Tсм Pсм (1 Kп.п.р ), |
||
где Дp |
– число рабочих дней; |
Pсм – режим сменности; Kп.п.р – |
коэффициент потерь, связанных с простоем в ремонте. Полученный минимальный размер партии корректируется
до нормативной величины партии nн так, чтобы он целое число раз укладывался в месячное задание Nмес. Такой размер партии устанавливается во избежание ненужного скопления незавершенного производства.
Определяется коэффициент
KNмес , nmin
иего значение округляется до целого числа K . Тогда после первой корректировки размер партии
n NKмес .
Вторая корректировка предельных размеров партии деталей заключается в приведении величины периодичности запус- ка-выпуска партии деталей к унифицированным значениям периодичности изготовления деталей. Их величина зависит от количества рабочих дней в месяце: при 22 рабочих днях унифицированные величины периодичности изготовления деталей составляют 22, 11, 2, 1 день; при 21 рабочем дне – 21, 7, 3, 1 день; при 20 рабочих днях – 20, 10, 5, 4, 2, 1 день.
42
elib.pstu.ru
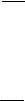
Чтобы привести размеры партии к унифицированной периодичности, определяется расчетная величина периодичности
запуска-выпуска партии
Rрасч n ,
Nдн
где Nдн – средняя потребность сборки в деталях данного наименования,
Nдн Nпр ,
Др
где Nпр – количество деталей, изготовляемых по программе на плановый период; Др – число рабочих дней, дн.
Нормативное значение периодичности Rн выбирается из унифицированного рядакак большаяближайшаякRрасч величина.
Результаты всех указанных расчетов сводятся в таблицу. На основании установленных размеров партий рассчитыва-
ется длительность производственного цикла обработки пар-
тии деталей.
Определение длительности производственного цикла далеко не всегда является необходимым и даже возможным. Значение этого норматива и методы его определения изменяются в зависимости от той или иной совокупности производственных условий.
В условиях серийного, регулярно повторяющегося производства одинаковой продукции принято считать, что длительность производственного цикла определяется по партии тех деталей, которые являются ведущими. Именно на определение партии таких деталей и ориентированы рассмотренные выше методы расчета партии деталей.
Итак, длительность производственного цикла обработки партии деталей определяется следующим образом:
43
elib.pstu.ru
|
1 |
|
K |
t |
штi |
K |
п |
|
|
|
|
Tц |
|
nн i 1о |
|
|
tмо (Kо 1) |
|
, |
||||
Tсм |
Kp Pсм Kв.н |
||||||||||
|
|
|
|
|
|
||||||
|
|
|
|
|
|
|
|
|
|
|
где Kп – коэффициент параллельности; Kр – количество рабочих мест, одновременно занятых на операции; Рсм – режим сменности; Kв.н – коэффициент выполнения норм; Kо – количество операций; tмо – суммарное межоперационное время по всем ( Kо – 1) парам смежных операций, затрачиваемое на кон-
троль и транспортировку предметов к рабочему месту следующей операции, а также время по всем операциям на ожидание обработки или сборки.
Время межоперационного пролеживания tмо = (0,5…1) Тсм.
Расчет длительности и построение производственного цикла имеют в серийном производстве оперативное значение только для периода развертывания производства данного изделия.
График производственного цикла помогает правильно решить вопрос о своевременном развертывании производства данных изделий. Но в установившемся серийном производстве, когда выпуск одной и той же продукции ритмично повторяется в течение планового года (или ряда лет), нет надобности в подобном графике и в особых расчетах календарной длительности производственного цикла. Задача оперативного регулирования серийного производства заключается в том, чтобы обеспечить ритмичное повторение производства и выпуска отдельных групп предметов, заготовок, деталей и т.д.
Следующим этапом расчета календарно-плановых нормативов является определение норм заделов деталей. Заделами называются находящиеся на различных стадиях производственного процесса детали, сборочные единицы или изделия, т.е. незавершенное производство в натуральном выражении. Они являются овеществленным выражением опережений запуска пар-
44
elib.pstu.ru
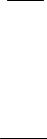
тии деталей, сборочных единиц или изделий. Как без соблюдения установленных размеров запуска и выпуска, так и без необходимых заделов не может быть обеспечен бесперебойный и равномерный выпуск продукции.
Цикловой задел – это количество деталей, находящихся непосредственно в производственном процессе цеха в данный момент времени.
Величина циклового задела Zц определяется отношением длительности цикла к периодичности запуска-выпуска:
Zц TцRнnн .
Оборотные заделы в серийном производстве возникают лишь при различных величинах размеров партий или периодичности запуска-выпуска в смежных цехах. При этом между смежными цехами средняя величина оборотного задела
Zо nб 2nм ,
где nб, nм – больший и меньший размеры партии.
Календарные планы-графики работы участков серийного производства деталей строятся различными способами в зависимости от количества детале-операций, закрепленных в среднем за одним станком, степени устойчивости номенклатуры изготовляемых деталей и периодичности их обработки. Одним из способов является построение подетально-пооперационного стандарт-плана. Он строится на интервале времени, равном максимальной периодичности запуска-выпуска партий деталей, проходящих обработку на участке.
Для построения стандарт-планов дополнительно рассчитывается дата запуска партий деталей исходя из величины циклового задела и среднего ритма деталей в партии:
45
elib.pstu.ru

Д = Zц · rд,
где Zц – величина циклового задела; rд – средний ритм деталей в партии, дни,
rд Rн ,
nн
где Rн – нормативная периодичность запуска партий деталей в производство, дни; nн – нормативный размер партии данного наименования, шт.
6.3. Пример расчета календарно-плановых нормативов в серийном производстве
Рассчитаем календарно-плановые нормативы для серийного производства двух деталей с месячной программой выпуска. Технология их обработки, штучное время, программа выпуска, коэффициент выполнения норм и процент потерь на переналадку приведены в табл. 6.
Подготовительно-заключительное время tпmax.з для зубооб-
рабатывающих, зубошлифовальных операций принимаем равным 60 мин, для токарных – 20 мин, для всех остальных –
30 мин.
Продолжительность смены 8 ч. Месячный эффективный фонд рабочего времени одного рабочего места Fмес рассчитываем с учетом времени простоев в ремонте Kп.п.р, которое составляет 5 % от номинального фонда рабочего времени. Используем
следующие значения: Kс = 4, Kп = 0,7, Рсм = 2, Kр = 1. Трудоемкость изготовления деталей считается средней
и малой, если для них tшт = 3…4 мин.
При расчете оборотных заделов для нечетных деталей принимаем размер партии в подающем цехе вдвое меньшим, чем в потребляющем, а для четных деталей наоборот.
46
elib.pstu.ru
Таблица 6
Исходные данные к расчету нормативов для обрабатывающего цеха
Номер |
Про- |
Коэффи- |
Процент |
|
Норма |
|
дета- |
грамма |
циент |
потерь |
Наименование |
штучного |
|
ли |
выпуска, |
выполне- |
наперена- |
операции |
времени, |
|
|
шт. |
ниянорм |
ладку |
|
мин |
|
|
|
|
|
Токарная |
7,9 |
|
|
|
|
|
Сверлильная |
6,4 |
|
1 |
2100 |
1,15 |
9 |
Фрезерная |
5,6 |
|
Зубообрабаты- |
3,3 |
|||||
|
|
|
|
вающая |
||
|
|
|
|
|
||
|
|
|
|
Шлифовальная |
6,2 |
|
|
|
|
|
Зубошлифовальная |
13,8 |
|
|
|
|
|
Сверлильная |
2,9 |
|
|
|
|
|
Токарная |
5,4 |
|
2 |
2000 |
1,2 |
4 |
Сверлильная |
1,8 |
|
Протяжная |
3,5 |
|||||
|
|
|
|
|||
|
|
|
|
Шлифовальная |
3,9 |
|
|
|
|
|
Полировальная |
8,8 |
Нормативный размер партии nн рассчитываем методом постепенного подбора. Минимально допустимые размеры партий деталей nmin1, nmin2 в данном случае определяем по показателю специализации рабочих мест.
Рассчитываем месячный фонд рабочего времени одного рабочего места:
Fмес Дp Tсм Pсм 60 (1 Kп.п.р )
20 8 2 60 (1 0,05) 18 240 мин.
Далее определяем суммарную трудоемкость T обработки деталей во всех операциях с учетом коэффициента выполнения норм и процента потерь на переналадку (результаты этого расчета отражены в табл. 7).
47
elib.pstu.ru
Таблица 7 Результаты расчета трудоемкости обработки деталей
Но- |
Коэф- |
|
|
|
Трудоем- |
|
фици- |
Процент |
|
Норма |
|||
мер |
ент |
потерьна |
Наименование |
штучного |
костьоб- |
|
дета- |
выпол- |
перена- |
операции |
времени, |
работки |
|
деталей, |
||||||
ли |
нения |
ладку |
|
мин. |
||
|
мин |
|||||
|
норм |
|
|
|
||
|
|
|
|
|
||
|
|
|
Токарная |
7,9 |
9,90 |
|
|
|
|
Сверлильная |
6,4 |
8,02 |
|
|
|
|
Фрезерная |
5,6 |
7,02 |
|
1 |
1,15 |
9 |
Зубообрабатывающая |
3,3 |
4,14 |
|
Шлифовальная |
6,2 |
7,77 |
||||
|
|
|
||||
|
|
|
Зубошлифовальная |
13,8 |
17,30 |
|
|
|
|
Суммарная трудоем- |
43,2 |
54,15 |
|
|
|
|
кость обработкидетали |
|||
|
|
|
Сверлильная |
2,9 |
3,62 |
|
|
|
|
Токарная |
5,4 |
6,74 |
|
|
|
|
Сверлильная |
1,8 |
2,25 |
|
2 |
1,2 |
4 |
Протяжная |
3,5 |
4,37 |
|
Шлифовальная |
3,9 |
4,87 |
||||
|
|
|
||||
|
|
|
Полировальная |
8,8 |
10,98 |
|
|
|
|
Суммарная трудоем- |
26,3 |
32,82 |
|
|
|
|
костьобработкидетали |
Затем вычисляем размер партии:
n |
|
Fмес Kо |
|
18240 6 506 шт., |
|
|
|
||||
min1 |
|
|
Kc T |
|
4 54,15 |
|
|
|
|
||
n |
|
Fмес Kо |
18240 6 833 шт. |
||
|
|||||
min 2 |
|
|
Kc T |
|
4 32,82 |
|
|
|
|
Полученный минимальный размер партии корректируем до нормативной величины партии nн, чтобы он целое число раз укладывался в месячное задание Nмес (программу выпуска).
48
elib.pstu.ru

Для этого определим коэффициенты:
K1 |
Nмес1 |
|
|
2100 |
4,15; |
K1 4; |
|
|
nmin1 |
506 |
|||||
|
|
|
|
|
|||
K2 |
|
Nмес2 |
|
2000 |
2,4; |
K2 2. |
|
|
nmin 2 |
833 |
|||||
|
|
|
|
|
Тогда после первой корректировки получим:
n1 |
Nмес1 |
|
|
2100 |
525 шт., |
||
K1 |
4 |
||||||
|
|
|
|
|
|||
n2 |
|
Nмес2 |
|
|
2000 |
1000 шт. |
|
|
K2 |
|
2 |
||||
|
|
|
|
|
Затем приводим величины периодичности запуска-выпуска партии деталей к значениям унифицированных величин периодичности изготовления деталей. Их величина зависит от количества рабочих дней в месяце: при 20 рабочих днях унифицированные величины периодичности изготовления деталей равны
20, 10, 5, 4, 2, 1 день.
Определим расчетную величину периодичности запускавыпуска партии первой детали:
Nдн1 Nпр1 2100 105 шт.; Др 20
R |
|
n1 |
525 5 дн. |
|
|||
расч1 |
|
Nдн1 |
105 |
|
|
Нормативное значение периодичности Rн выбирается из унифицированного ряда как большая ближайшая к Rрасч величина. Нормативное значение периодичности первой детали Rн равно 5 дням. Тогда нормативный размер партии деталей
nн1 5 105 525 шт.
49
elib.pstu.ru

И коэффициент кратности
K1 Nмес 2100 4. nн1 525
Определим расчетную величину периодичности запускавыпуска партии второй детали:
Nдн2 Nпр2 2000 100 шт., Др 20
R |
|
n2 |
1000 10 дн. |
|
|||
расч2 |
|
Nдн2 |
100 |
|
|
Нормативное значение периодичности Rн выбирается из унифицированного ряда как большая ближайшая к Rрасч величина. Нормативное значение периодичности второй детали Rн равно 10 дням. Тогда нормативный размер партии деталей
nн2 10 100 1000 шт.
И коэффициент кратности
K2 Nмес 2000 2. nн2 1000
Результаты расчетов заносим в табл. 8.
Таблица 8
Результаты расчета размера и периодичности запуска-выпуска партии деталей
Деталь |
n |
Периодичность |
nн |
K |
||
Rрасч |
Rн |
|||||
|
525 |
|
|
|||
1 |
5 |
5 |
525 |
4 |
||
2 |
1000 |
10 |
10 |
1000 |
2 |
50
elib.pstu.ru