
книги / Наукоемкие химические технологии
..pdfОсновные показатели процесса:
–температура после автотермического риформинга
965 °С,
–температура газа на выходе из трубчатой части KRES
870 °С,
–температура газа на выходе из теплообменного риформера 645 °С,
–степень удаления на криогенной установке компонентов из газа: метана – 100 %, аргона – 60 %, азота – удаляется
избыток (после удаления H/N = 2,9, содержание аргона
0,28 %).
–в реакторе KААР 1-й слой – катализатор на основе железа, 2, 4-й слои – катализатор на основе рутения,
–давление синтеза 94 атм., содержание аммиака после колонны синтеза 20–22 %. Технологическая схема с использованием процессов KААР, KRES представлена на рис. 1.
3. Технология синтеза аммиака под низким давлением
Прошло 20 лет с тех пор, как фирма ICI (Imperial Chemical Industries) представила процесс синтеза аммиака под давлением менеее 10 МПа. В 70-х годах одним из факторов, потребовавших совершенствования синтеза аммиака, стал фактор энергетических затрат. Это пробудило снова интерес к синтезу аммиака под низким давлением.
ICI, учитывая требование снижения энергетических затрат и капитальных затрат на компрессор синтез-газа, разработала свой вариант синтеза низкого давления с использованием катализатора KATALCO-74-1.
Кроме минимизации затрат энергии и уменьшения количества ступеней компрессора синтез-газа до одной в процессе было предусмотрено увеличение на 20 % расхода воздуха, подаваемого на вторичный риформинг, со снижением нагрузки на первичный риформинг. Кроме того, синтез ам-
51
миака в процессе фирмы ICI проводился при соотношении водород : азот, равном 2,2. Это потребовало ввести в схему обработку чистого синтез-газа в криогенной установке для вывода избыточного азота.
Увеличение концентрации азота в циркулирующем газе обеспечило повышение скорости процесса синтеза аммиака, так как стадия адсорбции азота поверхностью катализатора является лимитирующей. Использование нестехиометрической азотоводородной смеси хотя и снижает равновесную концентрацию аммиака, однако это снижение компенсируется применением катализатора с более низкой рабочей темпе-
ратурой – 400–420 °С.
Фирмой ICI разработан еще один вариант синтеза ам-
миака низкого давления – LCA (Leading Concept Ammonia),
который рекомендован для производств малой и средней мощности.
В технологии LCA используется тепло вторичного риформинга для нагревания входного потока парогазовой смеси первичного риформинга. Также используется избыток воздуха для перераспределения тепла между первичным и вторичным риформингами. Технологический газ, охлажденный в специальном аппарате, поступает на одноступенчатую паровую конверсию СО, работающую в изотермическом режиме. Выделение СО, СО2 и избытка азота осуществляется в короткоцикловой адсорбции. Далее син- тез-газ подается в метанатор и осушитель, затем компрессором качается в цикл синтеза. В технологии используется одноступенчатый компрессор синтез-газа с электроприводом.
Первые два производства по этой схеме были построены фирмой ICI в 1988 году в Севернсайде (Великобритания). Колонны синтеза в производствах фирмы ICI используются различной конструкции. В технологии LCA на агрегатах, построенных в Великобритании, использовалась колонна син-
52
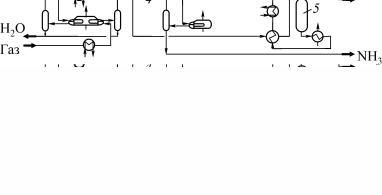
теза с одним слоем катализатора и расположением охлаждающих труб внутри слоя катализатора.
Катализатор синтеза низкого давления KATALCO-74-1 разработан фирмой ICI. Основу катализатора составляет железо, промотированное оксидами алюминия, калия и кальция. В катализатор дополнительно введен как промотор оксид кобальта. Преимущества этого катализатора, по сравнению с традиционным, заключаются в том, что он работает при более низкой температуре, более устойчив к ядам и имеет срок службы до 14 лет. Было показано, что этот катализатор может работать и при давлении 15 МПа и, следовательно, может использоваться в технологии аммиака фирмы Kellog. Концентрация аммиака, достигаемая на выходе из колонны синтеза, составляет свыше 18 %. Мощности, для которых рекомендован синтез аммиака при низком давлении, не более 1500 т/сут.
Для производств аммиака большей мощности фирмой
Uhde разработана технология Dual Pressure Uhde Procces (DPUP) с двумя уровнями давления (рис. 12). Особенность
Рис. 12. Технологическая схема синтеза аммиака фирмы Uhde с двумя уровнями давления: 1, 2 – реакторы синтеза; 3 – компрессор низкого давления; 4 – компрессор высокого давления; 5 – реактор предварительного синтеза; 6 – система очистки газа
53
технологии DPUP в том, что свежий синтез-газ после сжатия в компрессоре до давления 11 МПа поступает в отдельную колонну предварительного синтеза, после которой аммиак (1/3 от всего производимого количества) выделяется из газа. Затем газ компремируется до давления 21 МПа и с этим давлением поступает в цикл синтеза высокого давления. В этом цикле используются две колонны синтеза: одна – с двумя слоями катализатора, другая – с одним. Все слои катализатора в колоннах имеют радиальный ход газа. Мощность такого производства может составлять 3300 т/сут.
III. НОВЫЕ ТЕХНОЛОГИИ ПРИМЕНЕНИЯ КАТАЛИЗАТОРОВ
1. Основы применения нестационарного катализа
Традиционным для технологов считается проведение промышленных процессов в стационарных условиях. В производствах стремятся поддерживать неизменными технологические параметры путем стабилизации в основном входных параметров. Однако возможен и другой подход к обеспечению оптимальных условий проведения процессов – нестационарный, при котором входные параметры меняются со временем, например периодически.
В последнее время появилось значительное число теоретических и экспериментальных исследований, в которых показано, что для большого класса технологических процессов можно использовать нестационарные режимы, которые по своей эффективности будут превосходить стационарные.
Ктаким процессам относятся массо-, теплообмен, адсорбция,
вчастности короткоцикловая, ректификация, разделение газожидкостных смесей и др.
Впроцессах массо- и теплообмена нестационарные условия могут индуцироваться, например, пульсацией скорости
54
потоков. В этом случае интенсификация процессов связана с повышением степени турбулентности, с изменением движущих сил процессов.
В работах, связанных с созданием пульсационной аппаратуры для процессов экстракции, сорбции, растворения и выщелачивания, показана высокая эффективность искусственно создаваемых нестационарных режимов для процессов с участием жидкой фазы.
Химический реактор с неподвижным слоем твердого катализатора является динамической системой, в которой
впространстве и во времени объедены сложные физикохимические процессы, происходящие на поверхности зерен катализатора, внутри пор зерна и в пространстве между зернами катализатора. В стационарном режиме достаточно трудно организовать каталитический процесс так, чтобы все его элементарные стадии работали в режиме, который соответствует оптимальному режиму.
Внестационарном режиме можно так периодически изменять входные параметры или таким образом активизировать катализатор, чтобы в целом повысить эффективность процесса.
Например, при обратимом экзотермическом процессе
вреакторе с неподвижным слоем катализатора температура монотонно возрастает с ростом степени превращения исходных реагентов. Однако оптимальный с точки зрения скорости процесса режим требует понижения температуры с увеличением степени превращения.
Вискусственно создаваемых нестационарных условиях возможна такая организация процесса, при которой температура будет понижаться с ростом степени превращения, что позволит приблизиться к оптимальным условиям в одном слое катализатора.
Применение нестационарного катализа основано на таких известных фактах, которые говорят о воздействии реак-
55
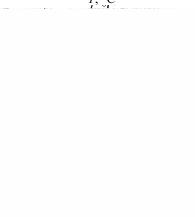
ционной среды на катализатор. Поэтому необходимо рассмотреть, хотя бы кратко, этот вопрос.
2. Воздействие реакционной среды на катализатор
Реакционная среда воздействует на катализатор, изменяя его состояние: химический состав и структуру поверхности, каталитические свойства. Многочисленные экспериментальные исследования свидетельствуют о влиянии концентрации компонентов реакционной среды и температуры на перечисленные свойства катализаторов.
Такие экспериментальные данные получены, в частности, для ванадиевых катализаторов, которые используются в процессе окисления диоксида серы кислородом.
На рис. 13 показаны изменения состава ванадиевого катализатора в зависимости от состава реакционной смеси
Рис. 13. Зависимость степени восстановления ванадиевых катализа-
торов от состава и температуры: – отношение содержания четырехвалентного ванадия в активной форме (1), неактивной (2) и общее (3, 4) к общему содержанию ванадия в катализаторе. Химический состав катализатора: отношение K/V = 2,5; носитель – силикагель; содержание V2O5 8 вес. %. Состав газа, %: 1–3 – 0,3–04 SО2;
7,4–7,5 SО3; 7,7 О2; 84,5 N2; 4 – 2,6 SО2; 5,2 SО3; 8,4 О2; 83,8 N2
56
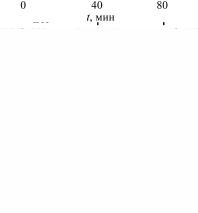
(содержания SO2, SO3, O2 и N2) и температуры. Рассмотрено влияние этих факторов на степень восстановления катализатора (относительные содержания четырехвалентного ванадия к общему содержанию ванадия). Причем рассмотрены состояния четырехвалентного ванадия в активной и неактивной формах.
Сравнение кривых 3 и 4 показывает, что при увеличении содержания в газе SO2 и снижении температуры увеличивается общая степень восстановления ванадия. Однако эти изменения могут быть обратимыми.
Наряду с этим при длительном воздействии богатой SO2 реакционной смеси и низкой температуры в катализаторе появляется неактивный четырехвалентный ванадий в виде кристаллической фазы. Увеличение содержания в катализаторе ванадия в такой форме приводит к снижению каталитической активности (см. кривые 2, 3 рис. 1 и кривую 1 рис. 14).
Рис. 14. Изменение во времени концентрации диоксида серы CSO2 на выходе из экспериментального реактора перемешивания (1)
и доля четырехвалентного ванадия в неактивной (2) и активной (3) формах от общего количества ванадия, участвующего в катализе после скачкообразного изменения температуры от 485 до 420 °С в момент времени t = 0 для катализатора с отношением K/V = 3
и7 вес. % V2О5. Исходная реакционная смесь: SO2 (4 %) и О2 (10 %)
вгелии. Условное время контакта в реакторе 0,2 с
57
Из рис. 14 видно также, что практически сразу после снижения температуры содержание четырехвалентного ванадия в активной форме увеличивается примерно в два раза и далее изменяется незначительно. В то же время содержание восстановленного ванадия в неактивной форме со временем медленно растет до некоторого стационарного значения. По-видимому, четырехвалентный ванадий в активной форме, непосредственно участвуя в каталитическом процессе, при низкой температуре может переходить в неактивную форму.
3. Время и характер установления стационарного состояния катализатора
Важным фактором при осуществлении реакций гетерогенного катализа является время и характер приближения состояния катализатора к стационарному. Это время Мк или иначе время переходного режима (время релаксации) следует оценивать в сравнении с длительностью каталитического процесса Мр (т.е. со временем воздействия реакционной среды на катализатор). Для процессов, протекающих при изменяющихся параметрах газовой фазы, целесообразно ввести понятие масштаба изменения состояния газовой фазы Мг. Если это изменение периодическое, то Мг – длительность периода. В большинстве случаев Мр >> Мг.
В результате изменения значений параметров реакционной среды нестационарными могут оказаться концентрации промежуточных соединений каталитического цикла и состояния приповерхностного слоя катализатора. Поверхностные концентрации изменяются со скоростью, близкой по порядку к скорости реакции.
Для достаточно быстрых реакций масштаб времени изменения поверхностных концентраций 10–1–10–2 с (Мf).
Изменение приповерхностных слоев катализатора осуществляется значительно медленнее, чем протекает каталитическая реакция. Поэтому в большинстве случаев прибли-
58
жение к стационарному состоянию происходит намного медленнее, чем протекает реакция (Мк > Мf ).
В зависимости от характера изменения состояния катализатора и внешних условий каталитический процесс может протекать стационарно, нестационарно и квазистационарно.
Наблюдаемые скорости химического превращения W в нестационарном режиме зависят от температуры и мгновенных (для определенного времени) концентраций всех участников реакции (в том числе промежуточных соединений на поверхности катализатора).
В стационарных условиях скорости образования и расходования индивидуальных газообразных веществ равны между собой. В нестационарном режиме эти скорости могут оказаться различными.
Масштабы времени переходных процессов для ряда каталитических процессов определены экспериментально. Так, для реакции окисления SО2 в SО3 на ванадиевом катализаторе получены следующие данные:
t = 422 °С; р = 0,1 МПа; Мк = 100 мин;
релаксация неактивной фазы
для ИК-1-1 при t = 380–485 °С, р = 0,1 МПа,
в случае концентрационных и температурных возмуще-
ний Мк = 2–3 мин (435–420 °С), Мк = 20–40 мин (t < 420 °С).
4. Методы создания нестационарного состояния катализатора
Поддержание нестационарного состояния катализатора достигается изменением параметров реакционной среды – состава, температуры, давления, объемной скорости. При колебаниях этих параметров могут возникнуть два типа состояний:
1-й – нестационарные концентрации промежуточных соединений;
2-й – нестационарные состояния приповерхностного слоя катализатора.
59
В первом случае в нестационарном режиме возможно увеличение эффективности из-за того, что при образовании промежуточных соединений колебательный режим может позволить регулировать их концентрацию, а следовательно, производительность и селективность.
Во втором случае увеличение эффективности процесса возможно за счет создания оптимального нестационарного состояния катализатора.
Нестационарного состояния катализатора можно достичь, периодически изменяя состав, температуру, давление и объемную скорость реакционной среды.
Одним из способов создания нестационарного режима является реверс направления подачи реакционной смеси в неподвижный слой катализатора. При этом способе катализатор не только ускоряет реакцию, но и выполняет функцию регенератора тепла. Это позволяет исключить поверхностный теплообмен и упростить конструкцию реактора.
Исследования показали, что если слой катализатора вначале разогреть до достаточно высокой температуры и направить на него реакционную смесь с низкой температурой, при которой реакция практически не идет, то через некоторый промежуток времени в слое установится тепловой фронт, движущийся в том же направлении, что и газ, но со скоростью много меньшей скорости фильтрации.
Одним из способов удержания теплового фронта в слое катализатора является переключение направления подачи реакционной смеси (реверс) в момент, когда фронт подходит к торцу слоя. При таком проведении каталитического процесса в слое катализатора создается зона высоких температур, колеблющаяся внутри слоя в соответствии с циклами переключения газа. Метод реверса оказался эффективным для обратимых экзотермических реакций как окисление диоксида серы, синтез аммиака, каталитической очистки газа от СО.
60