
Пожарная безопасность технологических процессов / Shvyrkov - PB tekhnologicheskikh processov 2012
.pdf
16.3.1.Особенности пожарной опасности установок ВОТ
1.Пожарная опасность установок ВОТ (без привязки их к конкретным производствам) характеризуется пожароопасными свойствами применяемых теплоносителей, их количеством, температурой нагрева, возможностью взрывов и пожаров.
2.Все применяемые в промышленности ВОТ являются ГЖ (табл. 16.1).
Таблица 16.1
Пожароопасные свойства наиболее распространенных ВОТ
|
|
|
|
|
|
|
|
|
Вид ВОТ |
|
|
Температура, оС |
|
|
|||
плавле- |
кипения |
рабочая |
вспышки |
самовоспла- |
НПРП |
ВПРП |
||
|
ния |
менения |
||||||
Дифенильная смесь |
12 |
258 |
370 |
115 |
695 |
115 |
130 |
|
(даутерм) |
||||||||
|
|
|
|
|
|
|
||
Ароматизированное |
–30 |
345 |
300 |
176 |
330 |
170 |
229 |
|
масло АМТ-300 |
||||||||
|
|
|
|
|
|
|
||
Мобильтерм-600 |
–30 |
350 |
300 |
173 |
340 |
165 |
225 |
|
Дитомилметан |
–30 |
293 |
300 |
136 |
500 |
107 |
138 |
|
Дикумилметан |
–22 |
336 |
300 |
151 |
425 |
126 |
193 |
|
Тетрахлордифенил |
–7 |
340 |
300 |
223 |
704 |
– |
– |
|
Тетрафеноксилсилан |
48 |
436 |
350 |
250 |
– |
– |
– |
3.Как видно из табл. 16.1, все ВОТ в условиях эксплуатации нагреты
выше tвсп, но ниже tсв. Весь внутренний объем системы полностью заполнен жидкостью или ее парами, рабочее давление всегда выше атмосферного, поэтому горючие концентрации могут образоваться только в расширительных бачках, емкостях для подпитки системы теплоносителем и сборниках отработанного теплоносителя.
4.Основная опасность при работе установок обогрева ВОТ создается
при образовании неплотностей и повреждений, приводящих к выходу в печь или наружу нагретого ВОТ, разливу его на большой площади и образованию местных зон ВОК. Причинами повреждений обычно являются образование повышенных давлений в системе и прогары труб в огневых печах. Повышенные давления образуются в случае перегрева ВОТ, уменьшения сечения трубопроводов и при попадании воды в ВОТ во время пуска или в периоды подпитки системы. Перегрев ВОТ вызывает образование большого количества газообразных и твердых продуктов термического разложения. Наличие твердых продуктов разложения приводит к образованию пробок в линиях, их ококсованию и прогару.
5. Даутерм, дифениловый эфир и дифенил обладают хорошей термической стойкостью. Из них самым изученным и распространенным является даутерм, который до температуры 400 °С не разлагается, но обладает
221

высокой текучестью, поэтому легко может проникать наружу даже через малейшие неплотности в прокладочных и уплотняющих сальники материалах.
6. Масло АМТ-300 и Мобильтерм-600 имеют значительно меньшую термическую стойкость. Практика эксплуатации установок с этими ВОТ показала, что длительный их нагрев до температуры выше 180 °С (их рабочая температура может достигать 300 °С), приводит к термическому разложению с образованием значительного количества газов (метана, этана, пропана, этилена, пропилена, водорода и др.), ЛВЖ (бензола, толуола, фенола и др.), а также смолистых продуктов и кокса. Следствием этого является снижение (непрерывное) tвсп и tсв теплоносителя и повышение его вязкости (масло утяжеляется), приводящее к образованию газовых и твердых пробок в линиях. При длительной эксплуатации без удаления продуктов разложения tвсп масел АМТ-300 и Мобильтерм-600 может снизиться со
176 °С до 40–60 °С, а tсв с 330 °С до 230–250 °С, т. е. масла из разряда ГЖ переходят в разряд ЛВЖ, а их tсв становится ниже рабочей температуры
всистеме обогрева.
7.Следует иметь в виду, что при повреждении систем, работающих на маслах АМТ-300 или Мобильтерм-600, ВОК могут образовываться не только за счет смешивания их паров с воздухом, но и в результате образования «масляного тумана» (мелкодисперсного масляного аэрозоля). Аэрозоль образуется за счет распыления масла находящимися в нем газообразными продуктами термического разложения в момент резкого снижения давления при выходе масла наружу.
8.Характерными источниками зажигания в установках являются: пламя, высоконагретые конструкции котлоагрегатов (печей) и открытых спиралей систем электрообогрева, искры при замыкании спиралей на корпус, теплота перегрева подшипников и сальников насосов.
9.Возникшие пожары могут распространяться по поверхности разлившихся теплоносителей, по облакам аэрозоля и паровоздушной смеси, через дверные, оконные и технологические проемы, по системам вентиляции и т. д.
16.3.2. Основные способы обеспечения пожарной безопасности процессов нагревания горючих веществ ВОТ
Пожарную безопасность при нагревании горючих веществ ВОТ обеспечивают следующими способами и техническими решениями или их комбинацией:
масла АМТ-300 и Мобильтерм-600, используемые в качестве теплоносителей, периодически проверяют на температуру вспышки
222

исамовоспламенения. Анализ масел на tвсп (нормально (176±5)°С) следует производить не реже одного раза в два дня, а на tсв (нормально 330–340 °C) – не реже одного раза в месяц;
чтобы уменьшить опасность образования повышенного давления
ипрогара, радиантные трубы размещают так, чтобы факелы пламени горелок не омывали их;
уровень теплоносителя в котлах при обогреве парами ВОТ поддерживают не ниже установленного предела во избежание перегрева жидкости, ее разложения и прогара теплообменной поверхности. Целесообразно автоматическое регулирование температуры ВОТ путем изменения количества сжигаемого топлива, а при электрообогреве – силы тока;
при пуске установок следят за циркуляцией теплоносителя и плавностью нагрева (не более 12–20 °С/ч). При прекращении циркуляции ВОТ в системе прекращают работу горелок и электронагревателей. Подпитку котлов осуществляют теплоносителем, предварительно нагретым для его осушки до температуры 200 °С;
во избежание образования пробок все трубопроводы с ВОТ прокладывают с уклоном в сторону котлов. Если для этого нет условий, устраивают спускные краники. Трубопроводы защищают теплоизоляцией. Теплообменную поверхность котлов и нагревательных электрических труб периодически очищают от коксообразных продуктов разложения;
каждый котлоагрегат защищают предохранительным клапаном, перед которым устанавливают защитную мембрану для предупреждения пригорания тарелок клапанов. Отводные линии от предохранительного клапана на котлах и аппаратах с местным обогревом ВОТ оборудуют устройствами (конденсаторы и т. п.) для улавливания выбрасываемых паров теплоносителя (см. рис. 16.3);
при использовании даутерма соединения труб в системе делают сварными, а там, где это невозможно, применяют плотные и термостойкие прокладочные материалы;
насосы применяют с торцовыми уплотнениями или с гидравлическим уплотнением сальников;
открытые контакты электрообогрева котлов заключают в герметичный кожух, внутри которого создается избыточное давление инертного газа, при падении которого автоматически подается сигнал опасности. Котлоагрегаты размещают в изолированных помещениях (котельных) или на открытых площадках;
вместо горючих и термически нестойких теплоносителей целесообразно применять менее пожароопасные и более термически стойкие (например, кремнийорганические теплоносители);
223

для уменьшения количества выходящего наружу теплоносителя при аварии или пожаре установки обогрева ВОТ оборудуют аварийными сливами из всей системы;
в случае использования в качестве ВОТ масел АМТ-300 или Мо- бильтерм-600 обеспечивают работу расширительного бачка под защитой инертного газа;
расширительные бачки, емкости, оборудование для подпитки котлов свежим ВОТ и циркуляционные насосы размещают в обособленных помещениях. Все это оборудование следует защищать системами пенного
или порошкового тушения, а в топочное пространство котлоагрегатов и к дымовой трубе целесообразно подводить водяной пар.
Контрольные вопросы
1.Кожухотрубные теплообменники: устройство, причины образования повышенных напряжений, температурные компенсаторы.
2.Назовите причины повреждения кожухотрубных теплообменников
имеры профилактики.
3.Трубчатые печи: устройство, горелки и форсунки печей, виды трубчатых печей.
4.Укажите причины взрывов в топочном пространстве и в боровах трубчатых печей и мероприятия по защите от разрушений при взрыве.
5.Назовите причины повреждения и прогара змеевиков трубчатых печей и меры профилактики.
6.Трубчатая печь как источник зажигания. Для чего предназначена паровая завеса?
7.Нагревание высокотемпературными органическими теплоносителями: виды ВОТ, их пожароопасные свойства.
8.В чем заключается пожарная опасность установок ВОТ, теплоносителями в которых являются масла АМТ-300 и Мобильтерм-600?
9.Назовите причины образования отложений в трубопроводах установок ВОТ и мероприятия по их предотвращению.
10.Какие меры пожарной профилактики, направленные на предотвращение образования повышенного давления в системах обогрева ВОТ, вы знаете?
11.Какие меры пожарной профилактики, направленные на предотвращение образования отложений в системах обогрева ВОТ и прогара труб печей и котлов для нагрева ВОТ, вы знаете?
224

Глава 17
ПОЖАРНАЯ ОПАСНОСТЬ И ПРОТИВОПОЖАРНАЯ ЗАЩИТА ПРОЦЕССОВ РЕКТИФИКАЦИИ ПОЖАРООПАСНЫХ ЖИДКОСТЕЙ
17.1. Процессы ректификации и оборудование для их проведения
Процессы ректификации смесей жидкостей на составляющие их компоненты или отдельные фракции широко распространены в современной технологии. В качестве примеров достаточно указать на перегонку нефти в целях получения моторных топлив и смазочных масел, на выделение индивидуальных газов из их предварительно сжиженных смесей. Подавляющее большинство ЛВЖ и ГЖ (этиловый спирт, ацетон, уксусная кислота, бензол и многие другие продукты) получаются с использованием процессов ректификации.
В природе существуют жидкости взаимно растворимые друг в друге, ограниченно растворимые и нерастворимые. Процессы перегонки и ректификации используются для разделения смесей жидкостей (часто называемых растворами) взаимно растворимых друг в друге.
Рассмотрим поведение бинарной (состоящей из двух компонентов А и В) идеальной смеси, нагретой до кипения в условиях постоянной температуры и давления. Через определенное время система, состоящая из жидкости и пара, придет в состояние равновесия. Потоки компонентов А и В из жидкой фазы в паровую фазу и обратно будут одинаковы. Но при этом состав пара будет отличаться от состава жидкости. Причина этого явления кроется в том, что компоненты этого раствора имеют различную температуру кипения и, следовательно, интенсивность их испарения и упругость насыщенных паров у них будет разная. Это важное свойство растворов положено в основу их разделения в процессе ректификации.
Чтобы подтвердить это, приведем следующие аргументы. Для этого введем обозначения:
компонент А имеет меньшую температуру кипения tкА и называется низкокипящим (НК), или легколетучим компонентом;
компонент В имеет большую температуру кипения tкВ и называется высококипящим (ВК), или труднолетучим компонентом.
Давление насыщенных паров чистых компонентов А и В при данной
температуре кипения смеси tкип соответственно обозначим PА и PВ. Таким образом, tкА < tкВ, а PА > PВ. Воспользуемся законами Рауля и Дальтона, которым подчиняются идеальные растворы в равновесном состоянии.
Согласно закону Рауля:
pА PАxА , откуда xА pА / PА.
225

Согласно закону Дальтона:
pА Pобщ yА , откуда yА pА / Pобщ,
где Pобщ pА pВ; pА и рВ – парциальные давления компонентов А и В, соответственно; хА и уА – молярные доли (доли моля) компонента А в растворе и в паровой фазе, соответственно.
Видно, что полученные отношения хА и уА отличаются только знаменателями. Сравнивая знаменатели, можно сделать вывод о том, что в этих уравнениях хА < уА. Следовательно, в паровой фазе содержится больше НК, чем в жидкой фазе, так как всегда сумма парциальных давлений компонентов А и В меньше давления насыщенных паров чистого НК компонента А при одинаковых условиях.
Это положение сформулировано в первом законе Коновалова: пар обогащается тем компонентом, прибавление которого к жидкости повышает
давление пара над ней или понижает температуру ее кипения. |
|
|
|||||||
t, оС |
|
|
|
Нагреем |
жидкость |
ис- |
|||
tкВ |
|
|
|
|
ходного состава xА1 по НК |
||||
|
|
|
|
||||||
|
|
|
|
компоненту до температуры |
|||||
|
|
|
|
|
кипения t1 (рис. 17.1). Обра- |
||||
t2 |
yА2 |
|
|
|
зующийся при этом пар бу- |
||||
|
yА1 |
|
|
дет содержать yА1 долей НК |
|||||
t1 |
|
|
|
компонента. |
Отведем |
этот |
|||
|
|
|
|
|
пар и проведем полную его |
||||
tк |
|
|
|
|
конденсацию |
при |
темпера- |
||
|
|
|
|
туре tк. В получившейся |
|||||
|
|
|
|
tкА |
жидкости будет содержать- |
||||
|
|
|
|
ся xА2 долей НК компонента |
|||||
|
|
|
|
|
(xА2 = yА1). Из графика хо- |
||||
|
|
|
|
|
рошо видно, что xА2 > xА1, |
||||
|
|
|
|
|
т. е. полученный конденсат |
||||
|
xА3 xА1 xА4 |
xА2 |
xА, yА |
||||||
|
обогатился низкокипящим |
||||||||
Рис. 17.1. Изображение процесса простой |
|||||||||
компонентом. |
В |
кипящем |
|||||||
|
перегонки на диаграмме t – x – y |
остатке содержание |
НК |
||||||
|
|
|
|
|
компонента уменьшилось, так как он обогатился высококипящим компонентом (ВК), а температура кипения остатка повысилась, например, до температуры t2. При этой температуре содержание НК компонента в остатке будет равно xА3, а в паровой фазе – yА2. Собрав полученный конденсат, получим жидкость – дистиллят, выкипающий в интервале температур t1 – t2, содержание НК компонента в котором больше, чем в исходной смеси (фракция t1 – t2).
226

Процесс частичного испарения исходной смеси и полной конденсации |
||||||||||
образующихся паров называется простой перегонкой. |
|
|
||||||||
Как и в предыдущем случае, нагреем жидкость исходного состава xА1 |
||||||||||
по НК компоненту до температуры кипения t1 (рис. 17.2). |
|
|
||||||||
Образующийся пар, со- |
t, оС |
|
|
|
|
|||||
держащий yА1 долей НК ком- |
|
|
|
|
|
|||||
понента, будем охлаждать, но |
tкВ |
|
|
|
|
|||||
не до температуры tк, когда |
|
|
|
|
|
|||||
происходит его полная кон- |
t3 |
|
yА3 |
|
|
|||||
денсация, а до температуры t2 |
|
|
|
|
||||||
(точка a). При этом образуется |
t1 |
|
|
yА1 |
|
|||||
двухфазная система: дистиллят |
|
|
yА2 |
|
||||||
t2 |
|
|
|
|||||||
состава xА2 и несконденсиро- |
|
а2 |
а1 |
|
||||||
|
|
|
||||||||
вавшийся пар состава yА2. Со- |
tк |
|
|
|
|
|||||
держание |
НК |
компонента |
в |
|
|
|
|
|
||
них будет |
различно, причем |
|
|
|
|
tкА |
||||
yА2 > xА2 > xА1. По мере выки- |
|
|
|
|
|
|||||
пания исходной смеси содер- |
|
|
|
|
|
|||||
жание НК |
компонента в ней |
xА4 |
xА1 |
xА2 |
xА3 |
xА, yА |
||||
уменьшается, |
а |
температура |
||||||||
Рис. 17.2. Изображение процесса перегонки |
||||||||||
кипения смеси растет. Но, как |
||||||||||
видно из диаграммы, при час- |
с дефлегмацией пара на диаграмме t – x – y |
|||||||||
|
|
|
|
|
||||||
тичной конденсации при температуре t2 состав пара не изменяется до тех |
||||||||||
пор, пока температура остатка не превысит значения t3. Это состояние сис- |
||||||||||
темы будет соответствовать составу остатка по НК xА4, а пара – yА3. |
|
|||||||||
Таким образом, процесс неполной конденсации, так же как процесс |
||||||||||
частичного испарения, приводит к обогащению пара низкокипящим ком- |
||||||||||
понентом, причем концентрация НК компонента в отобранном дистилляте |
||||||||||
xА3 = yА2 будет значительно выше, чем при проведении процесса частично- |
||||||||||
го испарения при прочих равных условиях. Такой процесс частичного ис- |
||||||||||
парения исходной смеси и неполной конденсации образующихся паров на- |
||||||||||
зывается процессом перегонки с дефлегмацией пара. Многократно чередуя |
||||||||||
процессы частичного испарения и неполной конденсации, можно получить |
||||||||||
достаточно чистый дистиллят (практически чистый НК компонент) и ку- |
||||||||||
бовый остаток, т. е. разделить смесь на компоненты. В этом и заключается |
||||||||||
сущность процесса ректификации. |
|
|
|
|
||||||
Процесс ректификации осуществляют в ректификационной колонне, |
||||||||||
в которой происходит многократное противоточное взаимодействие пара |
||||||||||
и кипящей жидкости, в результате чего исходная смесь разделяется на со- |
||||||||||
ставляющие компоненты. Принципиальная схема ректификационной ко- |
||||||||||
лонны показана на рис. 17.3. |
|
|
|
|
|
|
227
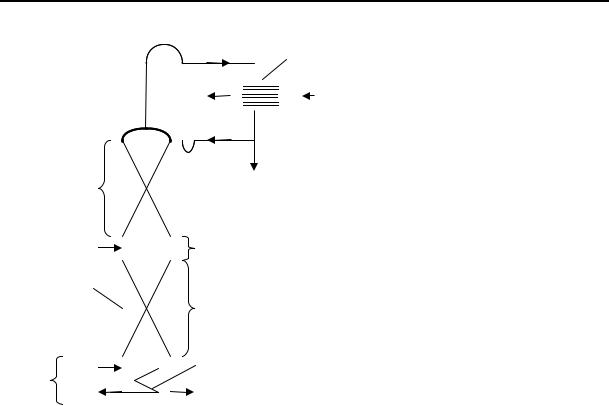
|
|
|
|
|
Пар (Gп) |
2 |
|
|||||
|
|
|
|
|
|
|
|
|
|
|
||
|
|
|
|
|
|
|
|
|
|
|
||
|
|
|
|
|
|
|
|
|
|
|
Вода |
|
|
|
|
|
|
|
|
|
|
|
|
|
|
|
|
|
|
|
|
|
|
|
|
|
|
|
|
|
|
|
|
|
|
|
|
|
|
|
|
|
|
|
Флегма (Gф) |
|
|
|
||||||
|
|
|
|
|
|
|
|
|
|
|
|
Рис. 17.3. Схема ректификационной |
|
|
|
|
|
|
|
|
|
|
|
|
|
I |
|
|
|
Ректификат (Gр) |
колонны: |
|||||||
|
|
|
1 – ректификационная колонна; |
|||||||||
|
|
|
|
|
|
|
|
|
|
|
|
2 – дефлегматор; 3 – кипятильник |
Исходная |
|
|
|
III |
|
|
На схеме обозначены: |
|||||
|
|
|
|
|
||||||||
смесь (Gи.с) |
|
|
|
|
|
|||||||
|
|
|
|
|
|
|
|
|
|
G – расход продукта, кмоль/с; |
||
|
|
|
|
|
|
|
|
|
|
|||
|
|
|
|
|
|
|
|
|
|
|
|
|
1 |
|
|
|
|
|
|
|
|
|
|
|
и.с – исходная смесь; |
|
|
|
|
|
II |
|
|
п – пар; о – остаток; ф – флегма; |
||||
|
|
|
|
|
|
|
р – ректификат (дистиллят) |
|||||
|
|
|
|
|
|
|
|
|
|
|
|
|
Водяной |
|
|
|
|
|
|
|
|
|
|
|
|
пар |
|
|
|
3 |
|
|
|
|
|
|
|
|
|
|
|
|
|
||||||||
IV |
|
|
|
Остаток (Gо) |
|
|
|
|||||
|
|
|
|
|
|
|
|
Простая ректификационная колонна состоит из укрепляющей части (I) и отгонной (исчерпывающей) части (II). Среднюю часть колонны, куда поступает исходная кипящая смесь, называют эвапорационным объемом (III), а нижнюю часть колонны с кипятильником – кубовой частью (IV).
Уравнение материального баланса процесса ректификации для всего количества смеси имеет вид:
Gи.с = Gр + Gо. |
(17.1) |
Для НК компонента: |
|
Gи.с xи.с = Gрxр + Gоxо. |
(17.2) |
Решая совместно уравнения (17.1) и (17.2), можно найти количество и состав веществ, участвующих в процессе ректификации (обычно опреде-
ляют Gр и Gо, задаваясь величинами Gи.с, xи.с, xр, xо).
Составим уравнение материального баланса для дефлегматора:
Gп = Gф + Gр. |
(17.3) |
|||
Разделим обе части уравнения (17.3) на Gр и получим: |
|
|||
G |
п |
Gф |
1. |
(17.4) |
|
Gр |
|||
Gр |
|
|
Отношение количества возвращаемого в колонну продукта (флегмы) к количеству отбираемого ректификата называется флегмовым числом
228

R = Gф / Gр. Тогда количество пара, движущегося по колонне снизу вверх, можно определить из выражения
Gп = Gр(R + 1). |
(17.5) |
Количество стекающей жидкости составит: |
|
в укрепляющей части колонны |
|
Gф = GрR; |
(17.6) |
в отгонной части колонны |
|
G = Gи.с + Gф. |
(17.7) |
В процессе эксплуатации ректификационной колонны флегмовое число меняется от бесконечности (при пуске в работу колонна работает «на себя», так как отбор ректификата отсутствует) до оптимального значения, определяемого из технико-экономических соображений. Обычно принимают:
1,2Rmin ≤ R ≤ 2,5Rmin, |
|
|
|
(17.8) |
|
где Rmin – минимальное флегмовое число, равное Rmin = |
хр yи.с.р |
; уи.с.р – |
|||
у |
и.с.р |
х |
|||
|
|
||||
|
|
и.с |
|
состав пара, который находится в равновесии с жидкостью состава хи.с.
17.1.1. Основные типы ректификационных колонн
Ректификационные колонны, представляющие собой вертикальные цилиндрические аппараты, бывают насадочные и тарельчатые (барботажные). Высота ректификационных колонн составляет 10–100 м и более, диаметр 0,5–6 м и более. В насадочных колоннах трудно добиться достаточно четкого разделения компонентов. Поэтому на практике чаще используются барботажные колонны.
В барботажных ректификационных колоннах в качестве массотеплообменных устройств используются тарелки (горизонтальные диски специальной конструкции) как с организованным, так и с неорганизованным переливом жидкости. Так как скорость пара в колоннах небольшая (в тарельчатых она обычно не превышает 0,5 м/с), то диаметр колонн лимитируется расходом пара: чем больше массовая производительность колонны по пару, тем больше ее диаметр. Высота ректификационных колонн зависит от многих факторов и в первую очередь от чистоты дистиллята (четкости ректификации) и разности температур кипения разделяемых компонентов. Чем выше чистота получаемого дистиллята и меньше разность температур кипения чистых компонентов, тем больше будет высота колонны.
229
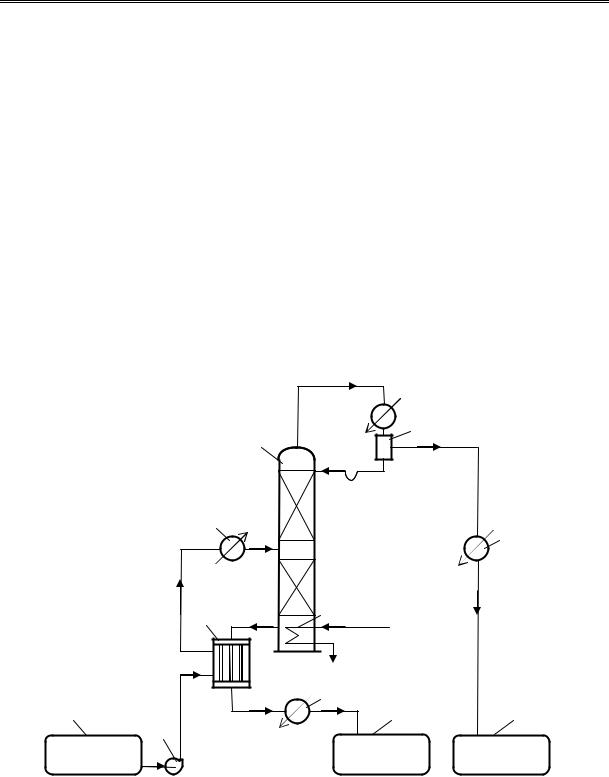
Схема непрерывно действующей установки с горячим орошением показана на рис. 17.4. Исходная смесь забирается из сборника 1 насосом 2, предварительно нагревается в подогревателе 3 и направляется в кипятильник 4. Кипящая смесь с постоянным расходом поступает в эвапоратор ректификационной колонны 5, где она разделяется на паровую и жидкую фазы. С верхней части колонны пары отводятся в дефлегматор 6, где частично конденсируются. Образующаяся в дефлегматоре горячая флегма отделяется от пара в сепараторе 7 и направляется на орошение верхней части колонны. В конденсаторе-холодильнике 8 пары полностью конденсируются, образующийся конденсат охлаждается и поступает в сборник дистиллята 10. Для непрерывной генерации пара в нижней части колонны имеется кипятильник 9. Отсюда же отводится кубовой остаток, который предварительно охлаждается в теплообменнике 3, отдавая свое тепло холодной исходной смеси, затем окончательно охлаждается до необходимой температуры в холодильнике 12 и поступает в сборник остатка 11.
Вода
6
7
5
4 |
|
Вода |
|
|
8 |
Водяной |
|
|
пар |
|
|
3 |
9 Водяной |
|
|
пар |
|
Вода |
12 |
|
1 |
11 |
10 |
2 |
Остаток |
Дистиллят |
Исходная смесь |
||
(А + В) |
(В) |
(А) |
Рис. 17.4. Схема ректификационной установки непрерывного действия:
1, 10, 11 – сборники, соответственно, исходной смеси, дистиллята и остатка; 2 – насос; 3 – подогреватель; 4, 9 – кипятильник; 5 – ректификационная колонна;
6 – дефлегматор; 7 – сепаратор; 8 – конденсатор-холодильник; 12 – холодильник
230