
Теоретические основы химической технологии (ответы на билеты)
.pdf
2. Показатели эффективности инвестиционных проектов. Инвестиции, инвестиционный проект, денежные потоки проекта и их соотношение. Дисконтирование разновременных затрат, коэффициент дисконтирования, норма дисконта. Показатели эффективности, инвестиционный " климат" России.
Инвестиционный проект - долгосрочное вложение средств в создание новых или реконструкцию и модернизацию действующих производств с целью получения дохода. Инвестиция начинает приносить прибыль не сразу на старте проекта, а спустя некоторое, как правило, весьма продолжительное время, после организации производства (модификации производства) и освоения новых производственных мощностей.
Пример инвестиционных проектов по уровню риска:
А) (наибольший риск) В создание новых производственных мощностей Б) В увеличении производственных мощностей В) В повышении эффективности производства или качества продукции
Г) (наименьший риск) ради удовлетворения требований государственных органов Аксиома финансовых операций: рубль, потраченный сегодня, стоит дороже рубля,
полученного завтра.
Расчёт сложных процентов: Р = Р ∙ ( + К) Дисконтирование - определение стоимости денежного потока путём приведения стоимости
всех выплат к определённому моменту времени:
Р Р = ( + )
Инвестор вкладывает в проект деньги как в банк, и ожидает получение некоторой прибыли, определяемой нормой дисконта Е (стоимость вложенных денег) , которую согласовывают инвестор и производитель. Норма дисконта показывает, на сколько деньги, вложенные инвестором на старте проекта, будут дороже денег, которые принесет предприятие в виде прибыли. Норма дисконта выше процентной ставки ЦБ, поскольку инвестор планирует извлечь выгоду (иначе он мог бы просто положить деньги в банк). В проекте норма дисконта должна быть низкой для привлечения инвесторов, но для большей прибыли нужно стараться норму дисконта повышать.
Чистый дисконтированный доход - разница между доходами и затратами, приведенные к текущему моменту времени с учетом нормы дисконта:
ЧДД = ∑ − З
( + )
=
Для простоты будем считать, что инвестиция была однократной в самом начале срока жизни проекта и их не будем дисконтировать. Тогда размер исходного капиталовложения равен К. В реальных проектах это не так, поскольку, инвестиции обычно вносят периодично и их тоже нужно дисконтировать:
− З,
ЧДД = −К + ∑ ( + )
=
Рассмотрим для лучшего объяснения пример:
Пусть инвестор вложил в проект 1 млн. рублей. Норма дисконта установлена в 12%. В первый год проект заработал 200 тыс. руб., во второй год проект заработал 300 тыс. руб., а в третий
– 700 тыс. рублей, тогда:
|
|
|
|
|
|
|
|
|
|
|
|
|||
ЧДД = − + |
|
+ |
|
+ |
|
|
|
|
|
< |
||||
+, |
(+, ) |
(+, ) |
||||||||||||
Если ЧДД < 0, то инвестор понесет потери. Если ЧДД > 0 , то инвестиция целесообразна. |
||||||||||||||
Индекс доходности инвестиций – это отношение дисконтированной прибыли к величине |
||||||||||||||
исходного капиталовложения: |
|
|
|
|
|
|
− З, |
|||||||
|
|
|
|
|
|
∑Т |
||||||||
|
|
|
|
|
|
|
|
|||||||
|
|
|
ИД = |
= |
( + ) |
|
|
|
||||||
|
|
|
|
|
К |
|
|
|
|
|||||
|
|
|
|
|
|
|
|
|
|
|
|
|
||
Если ИД > 1, то проект можно принять; если же ИД < 0, то проект убыточный. |
||||||||||||||
Внутренняя норма доходности – это такая норма дисконта при которой дисконтированная |
||||||||||||||
прибыль равна величине исходного капиталовложения. |
||||||||||||||
|
|
|
|
Т |
− З, |
|||||||||
|
|
|
К = ∑ |
|
|
|
|
|||||||
|
|
|
|
|
|
|
|
|
|
|||||
|
|
|
|
= ( + (вн)) |
Чем выше внутренняя норма доходности, тем больше вероятность, что инвестор примет
проект.

Время окупаемости – это то время, за которое дисконтированная прибыль станет равной
величине исходного капиталовложения:
К = ∑Ток − З, = ( + )
Чем меньше время окупаемости, тем больше вероятность, что инвестор примет проект.
Факторы неблагоприятного инвестиционного климата:
Высокая инфляция
Значительные инвестиционные риски
Увеличение нормы дисконта
Увеличенные сроки окупаемости
Снижение реальных инвестиций
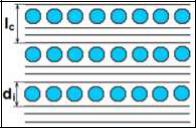
3. Физико-химические основы интеркалирования графита. Технологическая схема получения окисленного графита.
Благодаря слоистой структуре графита, различные атомы, молекулы и ионы способны внедриться в межслоевое пространство графитовой матрицы с образованием интеркалированных соединений графита (ИСГ). Несмотря на огромное многообразие ИСГ только три соединения нашли практическое применение: ИСГ с литием, с серной кислотой и азотной кислотой.
ИСГ с кислотами образуется при протекании двух параллельных реакций:
Образование макрокатиона: рС + [ОХ] → С+р + [ ] Интеркалирование макроаниона: С+р + ( + ) → + − ∙ + +
Природа связи графитовой матрицы – интеркалят электростатическая, но энергия взаимодействия на уровне Ван-дер-Ваальсовых взаимодействий.
Вкачестве окислителей могут выступать: бихромат калия, перманганат калия, азотная кислота, пероксид водорода.
Вкачестве интеркалатов: 75-98% азотная кислота, 70-96% серная кислота, 100% фосфорная кислота, 70% хлорная кислота.
Примечание: интеркалирующая способность убывает в ряду: 2 4 > 3 > 4. Строение интеркалированного графита:
ИСГ с постепенным ростом заряда и заполнением графитовой матрицы образует стехиометрические соединения, отличающиеся степенью заполнения графитовой матрицы. Такие соединения принято называть ступенями, n – номер ступени, который равен числу графитовых слое между ближайшими
слоями внедрённого вещества. Ic - период идентичности; di – толщина заполненного слоя. Тогда:
= + ( − ) ∙ ,
Но помимо этого, при окислении графита, протекает побочная реакция образования поверхностных функциональных групп (ПФГ). Эти группы
преимущественно образуются на торцах графитовых частиц и кристаллитов, а также на поверхности частиц, где есть атомы углерода с некомпенсированными связями. Наличие ПФГ влияет на способность материала к расширению, но не так значительно, как номер ступени, и на прочность графитовой фольги. При разложении ПФГ образуется аморфный углерод, который выступает как связующее и способствует повышению прочности графитовой фольги.
Несмотря на то, что сильные химические окислителисоли позволяют получать наиболее насыщенные ступени, высоко окисленную и диспергированную графитовую матрицу, все же существенным недостатком является их низкая растворимость в кислотах-интеркалатах и трудность очистки конечного продукта от избытка солей и продуктов их взаимодействия. Очистка конечных продуктов от окислителя подразумевает его отмывку водой, используя многократный избыток. Из-за чего образуется большое количество жидких отходов, содержащее какое-то количество кислоты и окислителя, которое требует утилизации.
Теперь рассмотрим свойства ИСГ с кислотами:
1)Обменные реакции: в обменные реакции вступают все ИСГ с кислотами, причем в зависимости от природы внедренной кислоты и кислоты, с которой предполагается провести обменную реакцию, продукт реакции может представлять собой бинарное или тройное ИСГ той же ступени, что и исходное соединение или с другим номером ступени.
2)Способность к вспениванию (многократному расширению): вспенивание – способность материала многократно увеличивать объём при резком нагревании. Считается, что вспенивание происходит за счет нагревания диспергирующего давления, возникающего при кипении, парообразовании и разложении интеркалата, в межкристаллитных областях. Факторы влияющие на степень расширения: скорость нагрева (чем быстрее подвод тепла, тем меньше времени на миграцию кислоты из межслоевого пространства и вскипание кислоты, т.е. больше интеркалята и из-за этого выше давление и степень расширения), размер частиц (чем меньше частицы, тем больше газопарной фазы выходит вдоль плоскости и не участвуют в процессе вспенивания) и номер ступени (чем выше номер ступени (I –III), тем больше интеркалята содержится в частице, а значит сильнее вспенивание).
3)Взаимодействие с водой (гидролиз): при взаимодействии с водой ИСГ способна восстановить графитовую матрицу. Восстановление возможно из-за того, что потенциал образования макрокатиона выше потенциала разложения воды. При окислении воды на границе раздела фаз ИСГ-вода выделяется кислород, который взаимодействует с атомами углерода на
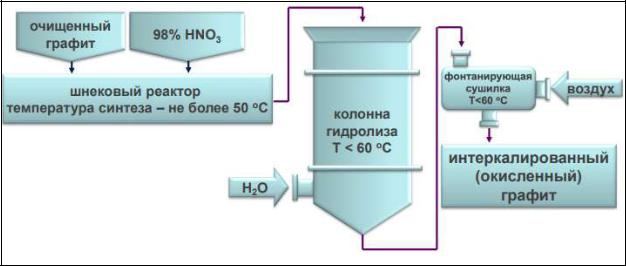
поверхности слоев и приводит к образованию кислородосодержащих поверхностных функциональных групп.
Теперь рассмотрим:
Технология получение интеркалированного (окисленного) графита:
Получение интеркалированного (окисленного) графита с азотной кислотой. В реактор смешения периодического действия с помощью дозаторов помещают графит и азотную кислоту. Реакция интеркалирования является экзотермической, поэтому важно не допустить перегрева. Для поддержания нужной температуры используют охлаждающий контур реактора, по которому циркулирует холодная вода. По истечении время синтеза, реакционную смесь отфильтровывают и помещают в следующий реактор для получения интеркалированного графита. Реактор, как правило, представляет собой колонну, куда сверху поступает ИСГ с азотной кислотой, а снизу вода. Такой способ подачи позволяет провести реакцию взаимодействия с водой наиболее эффективно. Затем продукт отфильтровывают и сушат в потоке воздуха при температуре не выше 60 0С до сыпучего состояния. Далее фасуют в тару.
С серной кислотой аналогично, только ещё зачастую добавляют окислители; при реакции интеркалирования поддерживают не выше 80 0С, такую же температуру поддерживают в колонне гидролиза и сушильной камере.

4. Физико-химические основы терморасширения окисленного графита. Технологическая схема получения пенографита. Материалы на основе пенографита.
Терморасширенный графит (пенографит, ТРГ) – низкоплотный углеродный материал, который представляет собой набор хаотично расположенных относительно друг друга червеобразных частиц. ТРГ получают путем термолиза интеркалированного графита (ИСГ). Химический состав ТРГ определяется на стадии выбора графита, т.к. содержание углерода в материале практически не меняется при интеркалировании и вспенивании. ТРГ обладает структурой графита, при этом является пористым материалом. Пористая структура терморасширенного графита представлена макропорами и мезопорами. Терморасширенный графит является промежуточным продуктом в цепочке получения графитовой фольги: сразу после получения его перерабатывают в рулоны или листы графитовой фольги (ГФ).
Рассмотрим физико-химические основы терморасширения окисленного графита
(интеркалированного графита):
Под термином «терморасширения ИСГ» понимается вспенивание – способность материала многократно увеличивать свой объём при резком нагревании. Считается, что вспенивание происходит за счет нагревания диспергирующего давления, возникающего при кипении, парообразовании и разложении интеркалата, в межкристаллитных областях. При терморасширении окисленного графита с кислотой происходит три процесса: 1) миграция кислоты из межслоевых пространств в межкристаллитные области и на дефекты матрицы; 2) кипение кислоты; 3) вспенивание.
Миграция кислоты не оказывает влияния на расширение окисленного графита, поскольку расширение происходит именно в них. Дальнейшая миграция интеркалята на дефекты нежелательна, так как интеркалат не принимает участия в процессе вспенивания.
Кипение кислоты протекает с испарением и разложением, при этом образуется газопаровая фаза, которая, находясь в замкнутом пространстве приводит к возникновению диспергирующего давления. Когда его значение достигает критического значения происходит увеличение расстояния между кристаллитами и формируется пористая структура.
Вспенивание является следствием предыдущего процесса, а степень расширения зависит от полноты протекания процессов 1 и 2. Чтобы вспенивание протекало максимально эффективно, необходимо минимизировать миграцию интеркалата на дефекты и газопаровой фазы за пределы межкристаллитных областей.
Факторы влияющие на степень расширения: скорость нагрева (чем быстрее подвод тепла, тем меньше времени на миграцию кислоты из межслоевого пространства и вскипание кислоты, т.е. больше интеркалята и из-за этого выше давление и степень расширения), размер частиц (чем меньше частицы, тем больше газопарной фазы выходит вдоль плоскости и не участвуют в процессе вспенивания) и номер ступени (чем выше номер ступени (I –III), тем больше интеркалята содержится в частице, а значит сильнее вспенивание).
Технология получения пенографита:
Так как терморасширенный графит является промежуточным продуктом в цепочке получения графитовой фольги, то их часто осуществляют в одном производственном цикле. Потому рассмотрим получение технологию получения графитовой фольги:
Принципиальная схема установки получения графитовой фольги состоит из дозатора интеркалированного графита – устройства, обеспечивающего равномерную скорость подачи материала во времени; блока подготовки и подачи
газа-носителя, который обеспечивает равномерное движение интеркалированного и терморасширенного графита; реактора вспенивания; бункера-
газоотделителя, в котором происходит разделение газовой и твердой фазы после вспенивания; системы очистки газов перед сбросом в атмосферу; клети
прокатки, обеспечивающей постепенное прессование терморасширенного графита за счет расположенных под углом лент; серии прокатных вальцов, обеспечивающих постепенное уплотнение материала и получения графитовой фольги заданной толщины и плотности; намотчика для графитовой фольги или гильотины для получения листов.
Материалы на основе пенографита: сальниковая набивка (уплотнитель), листовые уплотнения, фланцевые уплотнения и плетеная набивка. Помимо этого, из пенографита делают компоненты огнезащитных покрытий, эффективные сорбенты (превосходно впитывают жидкости), катализаторы, компоненты в электродах химических источников тока, антифрикционные материалы.
5. Основные технологии материалов на основе углерода. Преимущества и недостатки материалов на основе углерода.
Основные технологии на основе углерода:
Сырьё (кокс, графит, антрацит) => затем они подвергаются размолу, измельчению, промывке => фракционирование (просев) => смешение с добавлением пека (углеродное связующее) => прессование => карбонизация, спекание (800 0С), введение добавок => графитизация (3000 0С) => механическая обработка => готовое изделие.
После дробления часто проводят прокаливание для удаления летучих соединений. Кокс берут обычно из каменного угля, а пек из нефти.
Графитация в основном проводится при температурах выше 1800 0С. Улучшается преимущественная ориентация кристаллов. Происходит пересублимация углерода.
Получение углеродного волокна из пека:
Процесс производства углеродных волокон из мезофазных (часть пека, характеризующаяся твердой и жидкой фазой) пеков следующий:
1)Нагревание при 400-450 0С в среде инертного газа в течение длительного времени для получения мезофазного состояния
2)Формирование волокон из жидкокристаллических пеков
3)Отверждение и стабилизация волокон
4)Карбонизация волокон
5)Графитация волокон
Если время получения жидкокристаллического состояния уменьшить или ускорить процесс, то механические свойства будут плохие. Карбонизация (нагрев без доступа кислорода) и графитация последовательно при 950 0С происходит быстрое выделение летучих веществ (Н2, Н2О, СНп, НСN…). Быстрое газовыделение нежелательно, так как образуются дефекты в виде пузырей и трещин; карбонизация при 1400-1700 0С; графитация при 3000 0С. Чем больше ориентация расположения связей С-С-С, тем прочнее кристалл и тем выше его удельная электропроводность и теплопроводность.
Преимущества материалов на основе углерода:
Они зачастую легкие и представляют собой материалы низкой плотности с очень высоким соотношением плотности к весу
Высокая прочность на растяжение (армирующие, углеродные волокна, которые трудно растянуть)
Имеют низкое тепловое расширение (исключение материалы на основе пенографита для огнезащиты)
Коррозионная стойкость – материалы на основе углерода являются одними из наиболее коррозионно-стойких материалов
Электропроводность – композиты из углеродного волокна являются отличным проводником электричества
Недостатки материалов на основе углерода:
Наличие дефектов сильно снижают прочность материалов
Высокая стоимость из-за сложности производства
Малопригодны для вторичной переработки (так как требуются для этого большие финансовые затраты).