
новая папка 2 / 45290
.pdf
Кафедра целлюлозно-бумажного производства
МАТЕРИАЛЬНЫЙ БАЛАНС ПРОИЗВОДСТВА БУМАГИ
Методические указания для студентов специальности 240406 «Технология
химической переработки древесины» специализации «Технология целлюлозно-бумажного производства»
Санкт-Петербург
2009
Рассмотрены и рекомендованы к изданию учебно-методической комиссией факультета биотехнологии и химической технологии
Санкт-Петербургской государственной лесотехнической академии
25 ноября 2009 г.
Составители:
кандидат технических наук, доцент О. П. Ковалева, кандидат технических наук, доцент Ю. А. Бобров
Материальный баланс производства бумаги: методические ука-
зания / О. П. Ковалева, Ю. А. Бобров. – СПб.: СПбГЛТА, 2009. – 28 с.
Методические указания по расчету материального баланса производства бумаги и картона, необходимому для выполнения курсового и дипломного проектов, предназначены для студентов, обучающихся по специальности 240406 «Технология химической переработки древесины» специализации «Технология целлюлозно-бумажного производства», а также слушателей факультета повышения квалификации.
Даны основные технологические расчеты производства бумаги и картона, приведен пример расчета баланса воды и волокна размольноподготовительного отдела и бумагоделательной машины. Приведен расчет оборудования размольно-подготовительного отдела и мокрой части бумагоделательной машины.
Темплан 2009 г. Изд. № 14.
2
Введение
Основной задачей курсового и дипломного проектирования является систематизация, закрепление и расширение теоретических и практических знаний по технологии бумаги и картона; овладение методикой выполнения расчетов, развитие и закрепление навыков самостоятельной работы.
Методические указания для студентов специальности «Технология химической переработки древесины» содержат описание методики расчета материального баланса бумажного производства и примеры расчетов по размольно-подготовительному отделу и мокрой части бумагоделательной машины. При проектировании студент должен учитывать все особенности производства заданного вида бумаги или картона и производить расчеты согласно приведенной методике.
1. Методические указания
Проектирование бумажной фабрики следует начинать с выбора принципиальной технологической схемы производства. Расчетно-пояснительная записка (РПЗ) по курсовому проектированию или технологическая часть РПЗ по дипломному проектированию должна включать цель и задачи проектирования; характеристику выпускаемой продукции, а также сырья и материалов, используемых для производства данной продукции [1].
Технологическая часть РПЗ должна содержать последовательное описание всех стадий технологического процесса производства бумаги или картона с системами водопользования, обработки и переработки отходов. При этом следует указать назначение технологических операций, сущность процесса, технологический режим и его аппаратурное оформление [2–5].
Выбор типа бумагоделательной (БДМ) машины определяется видом вырабатываемой бумаги. При выборе типа машины должны быть учтены качественные показатели бумаги в соответствии с требованием ГОСТа или ТУ, способ формования бумажного полотна, основные габариты и скорость БДМ [6].
Описание размольно-подготовительного отдела (РПО) должно включать: прием, разволокнение и размол волокнистых полуфабрикатов; очистку, деаэрацию и сортирование бумажной массы; составление композиции бумажной или картонной массы и использование вспомогательных химических реагентов.
3
В описании мокрой части БДМ или картоноделательной машины (КДМ) приводится конструкция напорного ящика и условия его работы; вид, количество и последовательность расположения обезвоживающих элементов; тип гауч-вала; способ передачи бумажного полотна из сеточной в прессовую часть бумагоделательной машины; вид и количество прессов; условия прессования полотна; величина давления и разрежения.
Материальный баланс воды и волокна бумажного производства составляется в соответствии с разработанной принципиальной схемой технологического процесса и использования оборотной воды и оборотного брака, с учетом потерь сырья и материалов на каждой стадии процесса.
По данным материального баланса производят расчет и подбор оборудования для осуществления каждой технологической операции, а также рассчитывают количество аппаратов и приводят их техническую характеристику. В заключение РПЗ приводят краткие выводы по выполненной работе.
Графическая часть курсового проекта включает технологическую схему размольно-подготовительного отдела или мокрой части бумагоделательной машины, а дипломного проекта – всего бумажного производства [4, 5].
2. Методика составления баланса воды и волокна
Для организации производства бумаги или картона необходимо установить расход исходного сырья, химикатов, энергии и воды на единицу продукции. Расчет баланса воды и волокна позволяет определить расход волокнистого полуфабриката и воды на 1 т бумаги, получить точные данные о технологических потоках на различных стадиях процесса, выявить безвозвратные потери волокна и расход свежей воды.
Для определения количества вещества и воды, поступающих на данную стадию производства, при известном количестве вещества, выходящего с этой стадии, традиционно используют формулу И. И. Богоявленского [7]:
|
100 - Tн |
|
100 - Тк |
|
|
|
|
|
|
|
|
|
|||
Х = G + К |
|
× Х - |
|
G |
, |
(1) |
|
Тн |
Тк |
||||||
|
|
|
|
|
где Х – количество сухого вещества, поступающих на данную стадию производства, кг; G – количество сухого вещества, выходящего с данной стадии производства, кг; К – концентрация отходящей воды, кг/л; Тн и Тк – начальная и конечная сухость бумаги или соответственно начальная и конечная концентрация вещества в бумажной массе, %.
В более сложных случаях для определения количества сухого вещества в потоках на различных стадиях производства составляют систему уравнений с двумя неизвестными величинами: одно уравнение относится к
4
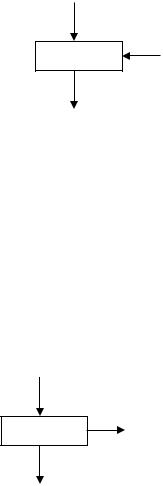
балансу потоков волокнистой массы, а другое – к балансу сухого вещества (волокна). При этом сумма потоков волокна и воды, поступающих на данную стадию производства, должна быть равна сумме уходящих потоков. Возможны два варианта:
1. Разбавление массы водой. Введем условные обозначения:
Q1 и K1 – соответственно количество и концентрация массы, поступающей на стадию производства;
Q2 и K2 – количество и концентрация массы, уходящей с данной стадии производства;
Q3 и K3 – количество и концентрация оборотной воды, поступающей на разбавление массы или отходящей при обезвоживании массы.
Q2 = Q1 + Q3 ;
Q2 K2 = Q1 K1 + Q3 K3 .
Q = Q |
К1 |
− К3 |
, |
(2) |
|
К1 |
− К3 |
||||
1 2 |
|
|
|||
Q1К1 |
|
|
|
|
Q3К3
Q2К2
тогда |
Q = Q |
К2 − К1 |
, |
(3) |
||||
|
3 |
2 К |
3 |
− К |
|
|
||
|
|
|
|
|
1 |
|
|
|
2. Обезвоживание массы. |
|
|
|
|
|
|
|
|
Q2 = Q1 – Q3 ; |
|
|
|
|
|
|
|
|
Q2 К2 = Q1 K1 – Q3 K3 . |
|
|
|
|
|
|
|
|
|
Q = Q |
К3 − К2 |
, |
(4) |
||||
|
1 |
2 К |
3 |
− К |
|
|
||
|
|
|
|
|
1 |
|
|
|
тогда |
Q = Q |
К1 − К2 |
, |
(5) |
||||
|
3 |
2 К − К |
3 |
|
|
|||
|
|
|
1 |
|
|
|
||
Q1К1 |
|
|
|
|
|
|
|
|
Q3К3
Q2К2
5

Расчет баланса производят на 1 т продукции в соответствии с параметрами готовой бумаги или картона, поэтому его начинают в порядке, противоположном ходу технологического процесса. По окончании расчета баланса определяют расход свежей воды на 1 т бумаги и безвозвратные потери волокна со сточными водами. Полученные при расчете данные сводят в таблицу прихода и расхода волокна и воды по каждой стадии процесса.
3. Расчет расхода сырья и химикатов
Для расчета расхода сырья и химикатов необходимо определить композиционный состав бумаги или картона, содержание проклеивающих веществ, красителя и различных вспомогательных веществ, а также произвести подбор расчетных коэффициентов, таких как, концентрация волокна в массе по стадиям технологического процесса, концентрация волокна в оборотной воде и оборотном браке. Подбор коэффициентов осуществляется на основании данных справочных материалов бумажного производства, учебных пособий и книг по технологии бумаги и ее свойствам, а также данных предприятий, специализирующихся по выпуску конкретного вида бумаги или картона.
Часовая производительность БДМ (Qчас , кг/ч) определяется по формуле:
Qчас = 0,06 · В · V · g · К1 · К2 ,
где В – обрезная ширина машины, м; V – скорость БДМ, м/мин; g – масса 1 м2 бумаги, г; К1 – коэффициент холостого хода БДМ (обычно 0,95–0,98); К2 – коэффициент, учитывающий потери бумаги при отделке (в среднем
0,95–0,985).
Суточная производительность БДМ (Qсут , т/сут):
Qсут = Qчас × 23,5 .
1000
Годовая производительность, Qгод , тыс. т/год, рассчитывается на 345
рабочих дней в году:
Qгод = Qсут · 345.
Расход волокнистого сырья с учетом влажности бумаги и промоев волокна (безвозвратные потери волокна в процессе производства) определяется по формуле
Мчас = Qчас · К,
где Мчас – расход волокнистого сырья, кг/ч; К – коэффициент, учитывающий промои волокна и влажность бумаги, который рассчитывается по формуле
6

|
|
|
П |
|
|
|
З |
|
|
|
W |
|||
К = 1 |
+ |
|
|
|
× 1 |
- |
|
|
|
× 1 |
- |
|
|
, |
|
|
|
|
|||||||||||
|
|
100 |
|
|
100 |
|
|
100 |
здесь П – промои волокна, %; З – зольность бумаги, %; W – влажность бумаги, %.
Если в композиционный состав бумаги входит несколько волокнистых полуфабрикатов (различные виды целлюлозы, механической древесной массы, макулатурная масса), то их следует учитывать. При этом содержание отдельных компонентов композиции определяется по формуле
m = Мчас × G ,
100
где m – расход компонента, кг/ч; G – содержание компонента, %.
Удельный расход волокнистого сырья на 1 т продукции составит
Муд = К ×1000 , 0,88
где Муд – удельный расход полуфабриката, кг/т; К – коэффициент, учитывающий промои волокна и влажность полуфабриката; 0,88 – коэффициент, учитывающий влажность воздушно-сухого полуфабриката.
При использовании композиции бумаги, состоящей из различных полуфабрикатов, удельный расход каждого из них определяется в зависимости от его процентного содержания в массе.
Расход проклеивающих веществ П, кг/ч, определяется по формуле
П = Пуд · Qчас ,
где Пуд – удельный расход проклеивающих веществ для данного вида бумаги, кг/т; Qчас – часовая производительность БДМ.
Аналогично рассчитывают расходы других химикатов и добавок (как произведение удельного расхода вещества и часовой выработки бумаги). Расход проклеивающих веществ и других химикатов определяется в зависимости от их концентрации (г/л), применяемой в композиции бумаги (удельный расход химикатов разделить на концентрацию в г/л).
4. Пример расчета баланса воды и волокна
Расчет баланса воды и волокна на 1 т газетной бумаги нетто массой 45 г/м2 производится для машины необрезной шириной 8300 мм и скоростью 1200 м/мин. Для расчета примем брак в отделке 3 % и брак машинный 5 %, в том числе 2 % сухого и 3 % мокрого брака. Композиция бумаги: древесная масса (ДМ) – 80 %. макулатурная масса (ММ) – 20 %.
Расчет материального баланса производим согласно принципиальной технологической схеме (стр. 8).
7

Принципиальная схема для расчета баланса воды и волокна
|
|
Древесная масса |
Макулатурная масса |
||||||||||||
|
|
|
|
|
|
|
|
|
|
|
|
|
|
|
|
|
|
Бассейн нере- |
|
|
|
|
|
|
|
|
|
Бассейн нерегу- |
|||
|
|
|
|
|
|
|
|
|
лируемой ММ |
||||||
|
гулируемой ДМ |
|
|
|
|
|
|
|
|
|
|||||
|
|
|
|
|
|
|
|
|
|
||||||
|
|
|
|
|
|
|
|
|
|
|
|
|
|
|
|
|
|
|
|
|
|
|
|
|
|
|
|
|
|
|
|
|
|
Бассейн регу- |
|
|
|
|
|
|
|
|
|
Бассейн регули- |
|||
|
|
|
|
|
|
|
|
|
Композиционный |
|
|||||
|
|
|
|
|
|
|
|
|
|
руемой ММ |
|||||
|
|
лируемой ДМ |
|
|
|
|
|
|
|
|
|||||
|
|
|
|
|
|
|
|
|
бассейн |
|
|
|
|||
|
|
|
|
|
|
|
|
|
|
|
|
|
|
|
|
|
|
|
|
|
|
|
|
|
|
|
|
|
|
||
|
|
|
|
|
|
|
|
|
|
|
|
|
|
|
|
|
|
|
|
|
|
|
|
|
|
|
|
|
|||
|
|
Бассейн брака |
|
Машинный бассейн |
|
|
|
||||||||
|
|
|
|
|
|
|
|
|
|
|
|
|
|
|
|
|
|
|
|
|
|
|
|
|
|
|
|
|
|
|
|
|
|
|
|
|
|
|
|
|
|
|
|
Смесительный насос |
|
|
|
|
|
|
|
|
|
|
|
|
|
|
|
|
|
|
|
|
|
|
|
|
|
|
|
|
|
|
|
|
|
|
|
|
|
|
|
|
|
|
|
|
|
|
|
Очистка |
|
|
В сток |
|
|
|
|
|
|
|
|
|
|
|
|
и сортирование |
|
|
|
|
|
|
|
|
|
|
|
|
|
|
|
|
|
|
|
|
|
|
|
|
|
|
|
|
|
|
|
|
|
|
|
|
|
|
|
|
|
|
|
|
|
|
|
|
|
|
|
|
|
|
|
|
|
|
|
|
|
|
|
Напорный ящик |
|
|
|
|
|
|
|
|
|
|
|
|
|
|
|
|
|
|
|
|
|
|
Сборник |
|
|
|
|
|
|
||||||
|
|
|
|
|
Формующий вал |
|
|
|
|||||||
|
|
|
оборотной воды 1 |
|
|
|
|
|
|||||||
|
|
|
|
|
|
|
|
Вода |
|||||||
|
|
|
|
|
|
|
|
|
|
|
|
|
|
|
|
|
|
|
|
|
|
|
|
|
|
|
|
|
|
||
|
|
|
|
|
|
|
|
|
|
|
|
|
|
|
|
|
|
|
|
|
|
|
|
|
|
|
|
Отсасывающие |
|
|
|
|
|
Сгуститель |
|
|
|
|
|
|
|
|
|
|
|||
|
|
|
|
|
|
|
ящики |
|
|
|
|||||
|
|
|
|
|
|
|
|
|
Вода |
|
|
|
|
||
|
|
|
|
|
|
|
|
|
|
|
|
|
|
||
|
|
|
|
|
|
|
|
|
|||||||
|
|
|
|
|
|
|
|
|
|
|
|
|
|
|
|
|
|
|
|
|
|
|
|
|
|
|
|
Гауч-вал |
|
|
|
|
|
|
Гауч-мешалка |
|
|
|
|
|
|
||||||
|
|
|
|
|
|
|
|
|
|||||||
|
|
|
|
|
|
|
|
|
|
|
|
|
|
|
|
|
|
|
|
|
|
|
|
|
|
|
|
Прессовая часть |
|
|
|
|
|
|
|
|
|
|
|
|
|
|
|
|
|
||
|
|
Сборник избыточной |
|
|
|
|
|
|
|||||||
|
Сушильная часть |
|
|
|
|||||||||||
|
|
оборотной воды 2 |
|
|
|
|
|
|
|||||||
|
|
|
|
|
|
|
|
||||||||
|
|
|
|
|
|
|
|
|
|
|
|
|
|
||
|
|
|
|
|
|
|
|
|
|
|
|
|
|||
Осветленная вода |
|
|
|
|
|
|
Накат |
|
|
|
|||||
|
|
|
|
|
|
|
|
|
|
|
|
|
|
|
|
Ловушка
Отделка
Гидроразбиватель
брака
Вода
Примечание: ----- |
вода, |
|
масса |
|
8
Вданном примере приведен расчет материального баланса для расчета высокоскоростной бумагоделательной машины с двухсеточным формованием бумажного полотна. С целью учета всех потерь волокна при обезвоживании бумажного полотна процесс формования разбит на несколько стадий по аналогии с расчетом материального баланса плоскосеточной бумагоделательной машины. Для расчета баланса плоскосеточной бумагоделательной машины следует заменить название стадии расчета «формующий вал» на название «регистровая часть».
Врасчете отсутствует стадия деаэрации, поскольку на ней не происходит потерь волокна, а также принят условный расчет очистки бумажной массы, объединяющий стадии очистки и сортирования.
С целью упрощения расчетов в данном примере предусматривается подача свежей воды на спрыски, которая может быть заменена осветленной оборотной водой.
Примем следующие показатели для расчета:
1. Концентрация массы на разных стадиях производства, %:
бассейн нерегулированной ДМ и ММ |
|
3,5 |
бассейн регулированной ДМ и ММ |
|
3,2 |
машинный бассейн |
|
3,0 |
напорный ящик |
|
0,6 |
после формующего вала |
|
5 |
после отсасывающих ящиков |
|
15 |
после гауч-вала |
|
25 |
после прессовой части |
|
42 |
после сушки |
|
93 |
2. Концентрация отходящих вод, % или г/л: |
|
|
регистровая вода |
0,25 |
0,0025 |
вода отсасывающих ящиков |
0,14 |
0,0014 |
вода от гауч-вала |
0,20 |
0,002 |
прессовая вода |
0,18 |
0,0018 |
вода от промывки сетки |
0,01 |
0,0001 |
вода от промывки прессовых сукон |
0,001 |
0,00001 |
Производительность БДМ
Минутная выработка бумаги нетто, кг/мин, составит
P = B · V · g · К1 · К2,
где В – необрезная ширина бумаги, м; V – скорость БДМ, м/мин; g – масса 1 м2 бумаги, кг; К1 – коэффициент холостого хода машины, 0,95; К2 – коэффициент потери бумаги при отделке, 0,97
9

P = 8,3 · 1200 · 0,045 · 0,95 · 0,97 = 413,02кг/мин
1 т бумаги нетто вырабатывается за 1000 = 2,42 мин. 413,02
Накат. Для выработки 1 т бумаги необходимо выработать на накате
при 3 % брака в отделке 1000 = 1030,93 кг , т. е. количество брака в отделке
0,97
составляет 30,93 кг на 1 т готовой бумаги.
Количество сухого машинного брака (2 %) от массы брутто составит:
1030,93 · 0,02 = 20,62 кг.
Тогда после сушильной части БДМ должно выходить
1030,93 + 20,62 = 1051,55 кг бумаги.
В соответствии с заданной влажностью готовой бумаги в ней со-
держится |
|
|
|
|
|
|
|
волокна |
1051,55 · 0,93 = 977,94 кг; |
|
|||||
воды |
1051,55 – 977,94 = 73,61 |
кг. |
|
||||
В сушильной части из бумажного полотна удаляется воды |
|||||||
|
977,94 × |
100 - 42 |
- |
100 - 93 |
|
= 1276,88 кг . |
|
|
42 |
|
|||||
|
|
|
|
93 |
|
|
|
Тогда в сушильную часть поступает массы |
|||||||
|
1051,55 + 1276,88 = 2328,43 кг, |
||||||
в том числе воды 2328,43 – 977,94 = 1350,49 кг. |
|||||||
Общее количество сухого брака, поступающего в гидроразбиватель, |
|||||||
составит |
|
30,93 + 20,62 = 51,55 кг. |
|||||
В нем содержится |
|
|
|
|
|
|
|
волокна |
51,55 · 0,93 = 47,94 кг; |
|
|
|
|||
воды |
51,55 – 47,94 = 3,61 кг. |
|
|
|
Представим схематическое изображение баланса. На схеме в виде дробного числа указано количество волокна (в числителе) и количество воды (в знаменателе). В виде целых чисел указаны количества волокнистой массы либо воды без содержания волокна.
10