
3565
.pdf
ния, так как нельзя провести отрыв проволоки одновременно по всей площади контакта даже при симметричной схеме (рис. 6.3, е). Такие испытания являются очень жесткими, поэтому соединения могут показать низкие значения усилия отрыва, особенно при сварке проволоки из малопластичных материалов. В этом случае оптимальной схемой испытания может служить отрыв под углом 45 °С (рис. 6.3, в).
При разрушающем испытании микросварных соединений проволоки с контактной площадкой на кристалле или корпусе ИС возможны различные виды разрушений (рис. 6.4), наиболее характерными из которых являются: отслоение деформированного участка проволоки от контактной площадки (рис. 6.4, а); вырыв части пленки вместе с деформированной проволокой (рис. 6.4, б); частичный отрыв деформированной проволоки от поверхности контактной площадки (рис. 6.4, в); обрыв по утоньшению в месте максимальной деформации проволоки (рис. 6.4, г); обрыв по проволоке (рис. 6.4, д).
Испытания на прочность путем разрушения микросоединений под углом 90 °С к поверхности подложки выявили два, чаще всего встречающихся вида разрушений; обрыв по утоньшению проволоки в месте контакта с пленкой и частичное или отслаивание проволоки от пленки. При разрушениях с отслаиванием проволоки на поверхности пленок алюминия видны характерные линии сдвига, а на поверхности золотого покрытия – зоны объемного взаимодействия проволоки с пленкой. Данные виды разрушений характерны и для некоторых соединений при контроле
183
дозированным усилием, т. е. соединений, не выдержавших испытание.
Сварное соединение, выполненное при оптимальных режимах сварки, может разрушаться, как показано на рис. 6.4, в, г, д или реже по схеме рис. 6.4, а. Оптимальным критерием качества контактов является не характер разрушения микросоединений с максимальной прочностью по сравнению с привариваемой проволокой, а стабильность прочности для всех соединений.
Рис. 6.4. Виды разрушений сварных соединений проволоки с пленочной контактной площадкой: а – отслоение деформированного участка проволоки от контактной площадки; б – вырыв части пленки вместе с деформированной проволокой; в – частичный отрыв деформированной проволоки от поверхности контактной
184
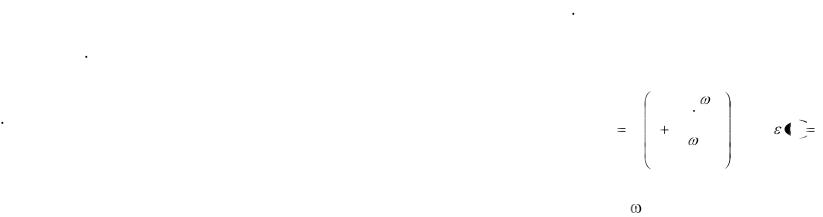
площадки; г – обрыв по утоньшению в месте максимальной деформации проволоки; д – обрыв по проволоке
6.4.2. Контроль обдувом струей газа
Данный метод применяется, в основном, для проведения 100 %-ного контроля сформированных проволочных перемычек. При испытаниях методом обдува испытываемый прибор зажимают в оправке и, регулируя параметры потока газа, изменяют силовое воздействие на его соединительные проводники (перемычки). Метод используют последовательно с формированием перемычек или параллельно с визуальным контролем сформированных микросоединений. В процессе контроля оправку с закрепленным прибором вращают и, например, обдувают струей воздуха при давлении 3 104 Па из сопла диаметром 1,6 мм, установленного на расстоянии 20 мм от оправки. Усилие, действующее на выводы, приблизительно равно 4 10-3 Н на вывод.
Одним из основных недостатков данного метода является снижение прочности соединений после проведения контроля. Следует также иметь в виду, что усилия, действующие на выводы, не поддаются точному контролю из-за специфики аэродинамики испытываемых микросоединений.
6.4.3. Контроль воздействием линейных ускоре-
ний
Данный метод основан на воздействии сил инерции на проволочную перемычку, обладающую определенной массой, обусловленных поступательным движением или центробежной силой, возникающими при вращении изделий. Существует несколько способов осуществления рассматриваемого метода: воздействие центробежной силы, одиночных ударов, многократных ударов и вибрации.
Испытания образцов на воздействие линейных ускорений приложением к выводу центробежной силы проводятся на центрифуге, например, при ускорении 20000 g, что для алюминиевой проволоки диаметром 0,04 мм при длине 2 мм соответствует приложению распределенной силы 3,4 10-3 Н. Спектр линейного ускорения трапецеидальной формы приведен на рис. 6.5.
Максимальное ускорение массы (вывода) Хmax определяем по формуле
|
sin |
|
|
t1 |
|
|
|
|
X max jo 1 |
2 |
|
при t1 |
jo , |
||||
|
|
|
||||||
|
|
t1 |
|
|||||
|
|
|
|
|
|
|||
|
|
|
2 |
|
|
|
|
где jo – максимальное значение ускорения опорного основания; - круговая частота колебаний; t1 – время разгона центрифуги.

Рис. 6.5. Спектр линейного ускорения трапецеидальной формы
Для испытаний на воздействие линейного ускорения применяется специальное оборудование: центрифуги типа Ц-5/300, Ц20000, G-385 или стенды испытания на ударные нагрузки.
Недостатками данных способов является низкая производительность. Сила, прикладываемая к проволочным проводникам из алюминия незначительна, так как величина прилагаемого ускорения ограничена техническими возможностями.
6.4.4. Электромагнитный метод контроля
Этот метод основан на том, что на проводник длиной l с током I, помещенный в магнитное поле напряженностью Н, действует сила Лоренца F = I [l, H], которая и используется в качестве контрольного воздействия.
Сила контрольного воздействия аэкв при электромагнитном методе эквивалента воздействию некоторого ускорения:
аэкв |
4IH |
, |
|
d 2 |
|||
|
|
где - плотность материала проволоки; d – диаметр проволоки.
При этом направление тока и силовые линии магнитного поля должны быть взаимно перпендикулярны. Величина эквивалентного ускорения тем больше, чем тоньше проволока и меньше плотность материала.
Существуют различные способы контроля
прочности электромагнитным методом:
1. Импульсное пропускание через выводы приборов электрического тока с одновременным импульсным возбуждением магнитного поля в соленоиде. Например, для получения силового воздействия F = 12 10-3 Н на алюминиевую проволоку диаметром 0,025 мм и длиной 2 мм при плотности тока I = 0,5 А необходима величина магнитной индукции 15 Тл. Такую напряженность получают за счет импульсного магнитного поля (так как при постоянном поле насыщение происходит уже при 2 Тл). Время измерения n = 1 мс. Импульсное поле получают в соленоидах, питаемых от генератора постоянного тока специальной конструкции или батареи конденсаторов.
Разработаны и внедрены установки контроля данным способом, совмещенные с измерителем электропараметров приборов, управляемым от ЭВМ. На рис. 6.6 изображена структурная схема установки электромагнитного контроля прочности сварных соединений внутренних выводов транзисторов.
2. Размещение прибора в постоянное магнитное поле и создание в проводниках тока, что имитирует воздействие на проволоку линейного
186

ускорения или воздействие ударов. В частности, |
же диодных и транзисторных матриц. К основ- |
можно осуществлять вибрацию проволоки на частоте |
ному недостатку метода следует отнести воз- |
собственного резонанса, при которой за счет корот- |
можность прибоев p-n-переходов при пропуска- |
ких импульсов тока развиваются максимальные на- |
нии токов больших значений, а также ограни- |
грузки на контакты. Если принять максимально до- |
ченность применения в связи с необходимостью |
пустимую плотность тока в алюминиевой проволоке |
наличия замкнутой электрической цепочки с ма- |
(в импульсе) 105 А/см2, то максимальное эквивалент- |
лым сопротивлением. |
ное ускорение будет равно ~ 3 105 g. Следует отме- |
Анализ существующих методов контроля |
тить, что получение столь больших ускорений, на- |
микросварных соединений показывает, что каж- |
пример, с помощью центрифуги весьма сложная за- |
дый отдельно взятый способ не позволяет ком- |
дача. Не менее трудно осуществить и эквивалентные |
плексно отбраковывать все возникающие дефек- |
механические удары с ускорением свыше 100 g. |
ты как на этапе формирования соединений, так и |
|
при контроле сформированных контактов. Это |
|
связано с наличием большого количества разно- |
|
плановых дефектов, влияющих на прочность |
|
сварного соединения. Поэтому необходимо про- |
|
водить дифференцированную отбраковку де- |
|
фектных соединений и на этапе формирования |
|
микросварных соединений, и при заключитель- |
|
ном контроле. |
Рис. 6.6. Структурная схема установки для контроля качества микросоединений транзисторов электромагнитным методом: 1 – сеть переменного тока; 2
– импульсный источник питания соленоида; 3 – соленоид; 4 – испытуемый транзистор; 5 – импульсный источник питания испытуемого транзистора; 6 – устройство синхронизации; 7 – схема запуска
Метод может быть использован для контроля внутренних соединений диодов, транзисторов, а так-
188

7. Герметизация полупроводниковых приборов, ИС и микросборок в корпуса
Главной задачей герметизации является предотвращение проникновения внутрь корпуса газов из окружающей среды, всегда содержащих влагу. Влага, проникающая в корпус, растворяет газы и загрязнения, образуя в условиях электрических напряжений электролитические пары.
Под герметичностью понимают способность ка- кой-либо замкнутой конструкции не пропускать через свои элементы жидкость или газ. Абсолютно непроницаемых конструкций не существует, поэтому герметичность характеризуется допустимой утечкой (течью) в единицах потока жидкости или газа. Поток жидкости или газа через микроотверстия выражают в единицах объема при определенном давлении, отнесенных к определенному времени (м3 Па/с).
Герметизация является одной из важнейших операций технологического процесса производства ИЭТ и от ее качества зависит выход годных изделий.
Решающим фактором, определяющим срок безотказной работы ГИС (15 – 20 лет), является остаточная влага внутри их корпусов. В большей степени воздействию влаги подвержены бескорпусные компоненты, проволочные соединения компонентов с контактными площадками платы и пленочные резисторы. Именно влага является причиной и ускорителем многочисленных деградационных процессов, в конечном итоге приводящих к разрушению и отказам элементов ГИС. При этом отказы возникают тем бы-
189
стрее, чем толще слой конденсированной влаги на поверхности компонентов и платы, больше разность потенциалов и меньше расстояние между смежными пленочными элементами схемы, чем выше уровень загрязнения влаги. Непосредственное воздействие на элементы ГИС оказывает слой влаги на поверхности и влага, находящаяся в парообразном состоянии в составе газовой среды в корпусе. Известно, что при понижении температуры окружающей среды ниже точки росы влага конденсируется на поверхности элементов схемы. Температура точки росы зависит от количества влаги в герметизированном пространстве. Задача герметизации сводится к смещению этой температуры за нижний предел температуры эксплуатации ГИС. Значительную опасность для надежности ГИС представляют частые переходы температуры через точку росы, создающие условия конденсации влаги в процессе эксплуатации.
Эффективным методом снижения влажности в герметизированном пространстве является герметизация ГИС в сухой атмосфере. Для этого используют вакуум или сухой азот с точкой росы ниже минус 40 °С. Следует отметить, что этот способ не является достаточным, так как не устраняет влагу, адсорбированную поверхностью деталей конструкции и компонентов ГИС. При этом количество адсорбированной влаги может в сотни раз превышать влажность сухого азота. Десорбция влаги может быть достигнута прока-
190
ливанием элементов конструкции перед герметизацией. На количество остаточной влаги решающее воздействие оказывают время и температура прокаливания (табл. 7.1).
Таблица 7.1
Количество остаточной влаги при различных режимах прокаливания
Время прока- |
Содержание влаги, ррт, при тем- |
|||
ливания, ч |
|
пературе |
|
|
|
150 °С |
200 °С |
|
250 °С |
1 |
2 |
3 |
|
4 |
1 |
15000 |
14000 |
|
10000 |
10 |
5000 |
1000 |
|
50 |
100 |
500 |
200 |
|
10 |
При использовании прокачки осушенным азотом для снижения влажности в герметизированном пространстве изготовленная ГИС с отверстиями в крышке корпуса выдерживается в течение нескольких часов на нагревателе при температуре 80 – 100 °С, после чего на этом же нагревателе производится прокачка осушенным азотом с последующей запайкой отверстий. Необходимый для безотказного функционирования ГИС (15 – 20 лет) уровень влажности (температура точки росы составляет минус 32 °С) достигается при использовании прокачки осушенного азота в течение 30 мин. Естественно, эти параметры должны обеспечиваться высоким качеством гермети-
191
зации.
Наибольшее распространение в полупроводниковой промышленности, особенно в серийном производстве, получили методы герметизации холодной и электроконтактной сваркой и пайкой. Герметизация полупроводниковых приборов и ИС заливкой пластмассой, склеиванием специальными клеями, стеклоцементами, глазурями и лаками, заварка стеклом пригодна для массового производства полупроводниковых приборов и ИС широкого назначения. Приборы в пластмассовой оболочке характеризуются низкой стоимостью, хорошим внешним видом, групповой технологией производства.
7.1. Холодная сварка
Метод герметизации полупроводниковых приборов холодной сваркой в настоящее время часто применяется в электронной промышленности. Он, в основном, используется для герметизации транзисторов и диодов малой, средней и большой мощности. Для образования качественного соединения двух металлических деталей необходимо выполнять следующие условия: обеспечить чистоту соединяемых деталей, достаточную их деформацию и пластичность.
Герметизация корпусов полупроводниковых приборов холодной сваркой обеспечивает получение вакуум-плотного сварочного шва. Применение этого метода требует соответствующей
192
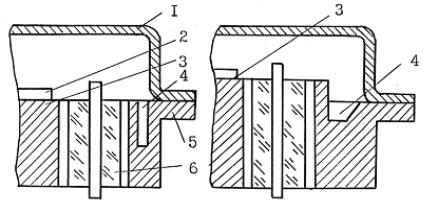
конструкции корпуса, ограничивает выбор металлов как по толщине (сварка металлов менее 0,3 мм не освоена), так и по свойствам (хотя бы один из металлов должен быть пластичным). В полупроводниковом производстве холодной сваркой герметизируют корпуса, изготовленные из следующих пар металлов: медь – медь, медь – сталь, ковар – медь. В конструкциях холодносварных корпусов полупроводниковых приборов предусматривают специальные разгрузочные (компенсационные) элементы, которые при деформации снижают механические напряжения. Конструктивные решения компенсаций напряжений в корпусах различных типов полупроводниковых приборов показаны на рис. 7.1.
а) |
б) |
Рис. 7.1. |
Компенсация напряжений во фланцах |
ножек приборов кольцевыми разгрузочными канавками: а – получаемой резанием; б – получаемой штамповкой; 1 – баллон; 2 – кристалл; 3 – плоскость монтажа кристалла; 4 – разгрузочная канавка; 5 – фланец; 6 – стеклоизолятор
Надежность герметизации во многом зависит от качества рабочего инструмента – пуансонов, которые изготовляют из высокостойких инструментальных сталей, закаливая, тщательно обрабатывая и полируя их рабочий профиль. Верхний и нижний пуансоны должны быть соосны между собой и обеспечивать передачу усилия от пресса точно по центру. Смещение пуансонов относительно друг друга и внецентровое приложение усилия приводит к браку при герметизации полупроводниковых приборов.
7.2. Электроконтактная сварка
Этот метод широко используется для герметизации корпусов полупроводниковых приборов и ИС круглой и прямоугольной формы со штырьковыми выводами, а также СВЧ-приборов. Перед проведением процесса электроконтактной сварки все детали корпусов подвергают тщательной обработке: промывке, обезжириванию, травлению, зачистке и сушке.
Основными параметрами электроконтактной сварки являются величина сварочного тока, длительность его протекания, усилие сжатия электродов. К разновидностям данного способа сварки относятся стыковая, точечная и шовная (роликовая) сварка. Контактная точечная сварка может быть рельефный конденсаторный (по контуру). Конденсатную сварку по контуру по тепловому воздействию на корпус можно отнести к
193

разряду низкотемпературных. В этом процессе длительность сварочного импульса составляет порядка 20 – 80 мс, так что выделяемое тепло не успевает распространиться в глубь тела корпуса, а отводится в электроды, которые обычно выполняются из медных сплавов с высокой теплопроводностью.
Следует отметить, что при импульсной шовной сварке наблюдается большой нагрев элементов корпуса. Например, в течение одной секунды от начала сварки температура на крышке размером 10 10 мм достигает 110 °С, а к концу сварки (через 3 – 6 с) повышается до 220 –250 °С. При этом температура в центре керамического основания корпуса достигает 50 и 110 °С соответственно.
Для герметизации широко применяется машина модели ПГРС. Данная машина имеет невысокую скорость перемещения предметного стола, обусловленную применением источника тока промышленной частоты. Герметизацию можно проводить в контролируемой атмосфере любого газа. Визуальный контроль осуществляется с помощью микроскопа.
В табл. 7.2 приведены технические характеристики машин для контактной шовной сварки корпусов.
Таблица 7.2
Основные технические характеристики машин для сварки
Характеристики ма- |
Модели машин |
|
шин |
ПГРС- |
ПГРС- |
ПГРС- |
|
|
|
1 |
1М |
2 |
|
1. |
Производитель- |
90 – |
120 – |
60 – |
|
ность, сварок/ч |
120 |
150 |
90 |
||
2. |
Размеры сваривае- |
15 |
|
30 |
|
мых крышек корпу- |
20 20 |
||||
15 |
30 |
||||
сов, мм |
|
||||
|
|
|
|||
3. |
Частота сварочного |
50 |
50 |
50 |
|
тока, Гц |
|||||
|
|
|
|||
4. |
Потребляемая |
2,0 |
2,0 |
3,0 |
|
мощность, кВт |
|||||
|
|
|
7.3. Герметизация сваркой плавлением
К этим методам относятся аргонодуговая, микроплазменная, электроннолучевая и лазерная.
Аргонодуговая сварка является разновидностью электродуговой и выполняется в защитной атмосфере газа (аргона) плавящимся и неплавящимся электродом. Как правило, герметизацию корпусов выполняют неплавящимися электродом на постоянном токе прямой полярности (минус на электроде). Герметизируют корпуса со штырьковыми выводами, периметр сварки которых превышает 50 мм, а суммарная толщина кромок отбортовки составляет 0,2 – 0,6 мм. Контроль сварного соединения осуществляется внешним осмотром и проверкой герметичности. Сварные швы должны иметь гладкую или мелкочешуйчатую поверхность по всей длине шва
без видимых дефектов: непроваров, подрезов, пор, трещин, незаплавленных кратеров.
Микроплазменная сварка является разновидностью аргонодуговой и отличается от нее большей стабильностью и более высокой температурой столба дуги. Этот вид сварки не имеет тех недостатков, которые присущи аргонодуговой сварке.
Электроннолучевая сварка характеризуется точным регулированием и управлением тепловой энергии, локальным нагревом, высокой чистотой при сварке благодаря наличию вакуума, что позволяет успешно применять ее для герметизации микроэлектронных устройств. Герметизацию данным способом можно проводить в непрерывном и импульсном режимах.
Лазерная сварка представляет собой совместное оплавление соединяемых материалов под действием интенсивного светового потока с образованием шва. Для герметизации корпусов применяют шовную лазерную сварку, выполняемую как в непрерывном, так и в импульсном режимах работы лазера. Свариваемые кромки корпуса не должны иметь заусенцев, раковин, царапин, трещин, следов припоя, жировых пятен и других загрязнений, препятствующих получению качественного соединения.
Внешний вид сварных соединений проверяют осмотром с помощью лупы. Прожоги, непровары, выплески, свищи и поры не допускаются.
7.4. Пайка
195
Для герметизации корпусов полупроводниковых приборов и ИС широко используют процесс пайки. Пайкой герметично соединяют между собой однородные и разнородные металлы, металлы с керамикой или со стеклом. В последнем случае в качестве припоя используются расплавленные стекла.
Сущность процесса герметизации пайкой заключается в соединении металлических или металлизированных поверхностей деталей корпусов с помощью припоя, который при температуре пайки смачивает паяемые поверхности, заполняет капиллярный зазор между ними и, кристаллизуясь, образует монолитный герметичный шов. Прочность паяного соединения зависит от чистоты исходных деталей, применяемого припоя и флюса, а также от технологического режима пайки (температуры, времени выдержки, скорости нагрева и охлаждения и др.). Прочность соединения, как правило, равна прочности припоя.
Основными преимуществами пайки являются: относительная ее простота и возможность герметично соединять детали корпусов полупроводниковых приборов и ИС сложной конфигурации, отсутствие расплавления деталей, что обеспечивает сохранение их исходной формы, структуры и механических свойств.
В полупроводниковой промышленности применяют, в основном, два вида низкотемпературной пайки: пайка в печах при нагреве конвек-
196

цией и пайка струей горячего газа. Припои наносят предварительно на соединяемые поверхности или в виде закладных деталей. Закладная деталь представляет собой выпускаемую в больших количествах заготовку постоянной массы. В зависимости от способа пайки она может быть офлюсована, т.е. предварительно покрыта слоем флюса.
Достоинством пайки является групповая герметизация ИЭТ, предварительно собранных в специальных кассетах.
7.4.1. Герметизация корпусов микросборок пай-
кой
По конструкционно-технологическому исполнению возможны следующие варианты общей герметизации микросборок: заливка объема неремонтопригодных микроблоков с общей герметизацией (МБОГ) эпоксидной смолой с предварительной технологической защитой микроплат и навесного монтажа с помощью кремнийорганических компаундов или герметизация опрессовкой. Для вакуумных микросхем, реализуемых в виде микроблока (вакуумные СБИС), герметизирующей средой является вакуум в полости конструкции.
Опыт разработки герметичных блоков РЭС и МБОГ показал, что наиболее технологичной является вакуумплотная герметизация корпусов паяным швом, которая является основным вариантом для микроблоков. При этом полость МБОГ заполняется сухим азотом или аргоном при избыточном давлении до
197
12·104 Па.
Герметичность микросборок обеспечивается соединением деталей корпуса и внешних соединений. На рис. 7.2 показаны варианты конструкций узлов герметизации соединений крышки и кожуха.
Рис. 7.2. Типы узлов герметизации микросборок:
а – с резиновой прокладкой; б – д – паяные соединения с проволокой; е – паяное соединение с лентой: 1
– корпус; 2 – крышка; 3 – уплотнительная прокладка; 4 – изоляционная прокладка; 5 – проволока; 6 – лента
На рис. 7.3 показаны сечения паяных соеди-
198