
3187
.pdf
благоприятна, так как процесс образования поковки в полости штампа протекает так, что волокна обтекают ее контур и не перерезаются.
Вследствие отсутствия облоя расход металла при штамповке в закрытых штампах сокращается, но поскольку закрытые штампы сложны в изготовлении, штамповка многих поковок сложной формы еще не освоена.
Штамповка в штампах для выдавливания — наиболее прогрессивный технологический процесс горячей штамповки. При использовании штампов для выдавливания значительно снижается расход металла (до 30 %), повышается коэффициент весовой точности, поковки получаются точные, максимально приближающиеся по форме и размерам к готовым деталям, производительность труда увеличивается в 1,5…2,0 раза.
Рис. 3.17. Схемы штамповки выдавливанием:
а — прямое; б — обратное: 1 — пуансон; 2 — матрица; 3 — поковка; 4 — выталкиватель
Для выдавливания наиболее целесообразны следующие типы поковок: стержень с фланцем, клапаны двигателей, полые детали типа стаканов и т.п. Схемы штамповки в штампах для выдавливания приведены на рис. 38, где стрелками указа-
121
но течение металла. Этим способом можно получать детали из углеродистых и легированных сталей, алюминиевых, медных и титановых сплавов. Поковки, изготовленные выдавливанием, имеют высокое качество поверхности, плотную микроструктуру. Точность поковок может соответствовать 12-му
квалитету, пределы допусков на размеры |
1,0 |
. Это достигает- |
|
0,5 |
|
ся в результате тщательной подготовки исходных заготовок под штамповку, а также высокой точности изготовления и наладки штампов использованием специальных смазок.
Основное преимущество процесса выдавливания перед штамповкой в открытых штампах — получение поковок с точными размерами и чистой поверхностью. Основные недостатки — высокие удельные усилия деформирования, большие энергозатраты на реализацию процесса и низкая стойкость штамповой оснастки.
Выбор штампа — открытый, закрытый или для выдавливания — определяется конфигурацией и сложностью детали, ее массой и материалом, характером производства. Следует учитывать также и существенные различия в макроструктуре материала поковок, полученных в различных штампах, т.к. макроструктура материала детали определяет ее прочность и долговечность.
3.8.2.Конструкции штампов
Взависимости от сложности поковки штампы бывают одноручьевыми и многоручьевыми.
Чем сложнее поковка по форме и чем больше она отличается от формы заготовки, тем большее число ручьев в штампах требуется для ее изготовления и тем более трудоемкой становится штамповка.
Ручьи в многоручьевых штампах разделяют на заготовительные и штамповочные. Ручьи, предназначенные для получения предварительной формы заготовки, называются заготовительными. Штамповочные ручьи делят на ручьи предвари-
122
тельной и окончательной штамповки. Ручей окончательной штамповки, который называют также чистовым ручьем, точно соответствует размерам горячей поковки. При штамповке заготовка последовательно переносится из ручья в ручей. Однако следует иметь в виду, что в многоручьевых штампах обязательным является ручей окончательной штамповки, остальные ручьи делают по мере необходимости, т. е. в зависимости от конфигурации поковки и серийности. Одноручьевые штампы имеют один окончательный ручей. Штамповка простых по форме поковок выполняется из проката, а сложных — из фасонных заготовок, предварительно откованных свободной ковкой.
В качестве примера рассмотрим молотовой многоручьевой штамп (рис. 3.18) и схему штамповки поковки шатуна по переходам в каждом ручье, начиная от заготовки. Назначение и роль ручьев этого и других штампов указаны ниже.
Заготовительные ручьи. Протяжной ручей (рис. 3.18, 4) выполняется в виде бойков и предназначен для увеличения длины отдельных участков заготовки за счет уменьшения площади ее поперечного сечения.
Подкатной ручей (рис. 3.18, 1, 3) предназначен для местного увеличения сечения заготовки за счет уменьшения сечения других участков. Подкатка выполняется за несколько ударов молота с кантовкой заготовки вокруг продольной оси на 90° после каждого удара.
Пережимной ручей аналогичен по форме подкатному и предназначен для осуществления местного уширения заготовки в плоскости, перпендикулярной к деформирующей силе. В пережимном ручье металл заготовки в осевом направлении почти не перемещается. Заготовка обрабатывается в нем без кантовки за один-два удара и без перемены положения переносится в следующий окончательный ручей.
Формовочный ручей предназначен для придания заготовке формы, соответствующей форме поковки в плоскости разъема. В этом ручье поперечные сечения заготовки изменяются по площади незначительно, а перемещение металла
123
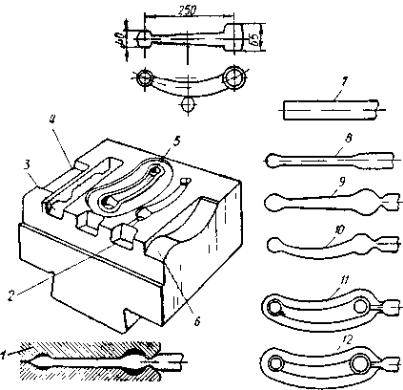
вдоль оси невелико. Из формовочного ручья заготовку переносят в предварительный или окончательный ручей с поворотом вокруг оси на 90°.
Рис. 3.18. Молотовой многоручьевой штамп и схема штамповки поковки по переходам:
1 — профиль подкатного ручья; 2 — предварительный ручей; 3 — подкаткой ручей; 4 — протяжной ручей;
5 — окончательный ручей; 6 — гибочный ручей; 7 — исходная заготовка; 8 — заготовка после протяжки;
9 — заготовка после подкатки. 10 — заготовка после гибки; 11 — поковка после предварительной штамповки;
12 — поковка после окончательной штамповки
124
Гибочный ручей (рис. 3.18, 6) предназначен для изгиба заготовки в соответствии с формой поковки в плане.
Площадка для осадки или для расплющивания предназначена главным образом для осадки заготовок в торец до требуемых размеров по высоте и диаметру. Применяется при штамповке поковок, имеющих в плане форму круга или близкую к нему. Осадка выполняется за один или несколько ударов.
Штамповочные ручьи. Предварительный (черновой) ручей (рис. 3.18, 2) предназначен для максимального приближения формы поковки к окончательной с целью увеличения стойкости окончательного (чистового) ручья (рис. 3.18, 5). Обычно он не имеет облойной канавки, несколько глубже и уже, чем чистовой ручей, и имеет большие радиусы скруглений. Поковка из предварительного ручья свободно укладывается в чистовом ручье и при штамповке обеспечивает его хорошее заполнение.
Чистовой ручей полностью соответствует размерам поковки в горячем состоянии. Этот ручей в отличие от всех остальных имеет облойную канавку. В случае штамповки прутка для отделения от него поковки применяют отрезной нож.
При проектировании технологического процесса, например штамповки под молотом, необходимо учитывать следующие особенности. При штамповке под молотами металл заготовки более легко заполняет полость верхней половины штампа. Для поверхности разъема штампов необходимо определить такую плоскость, при которой глубина ручьев является наименьшей. Слож-
ную поверхность разъема штампов назначать не рекомендуется. Разъем штампов назначают в таких участках поковки, по которым легко обнаружить возможный сдвиг половин штампов.
Мелкие поковки штампуют по 2…6 шт. с общим облоем из заготовки в виде прутка длиной не более 1200 мм и массой до 4,5 кг. Готовые поковки отделяют от прутка отрубными ножами штампа. Поковки средней массы штампуют последовательно из заготовки, рассчитанной на изготовление двух
125
поковок с одного нагрева. Штампуя первую поковку, заготовку удерживают клещами за второй конец. Штампуя вторую поковку, в клещах зажимают готовую первую поковку. Крупные поковки штампуют по одной из штучной заготовки. Для удержания заготовки и манипулирования ею при штамповке предусматривают дополнительный отход металла, называемый клещевиной.
3.8.3. Основные этапы технологического процесса горячей объемной штамповки
При разработке технологического процесса объемной штамповки отправным пунктом является проектирование чертежа поковки, который составляют на основании чертежа детали. От правильной разработки чертежа поковки зависит сложность, а иногда и возможность ее изготовления. Принята такая последовательность:
1)выбор плоскости разъема;
2)назначение припусков, допусков и напусков;
3)определение штамповочных уклонов;
4)определение радиусов закругления;
5)в поковках с отверстиями конструируют наметку под прошивку;
6)конструирование штампов с учетом расположения волокон в поковке, приемов и удобств штамповки, расположения баз последующей механической обработки и т. д.
Поверхностью разъема называется поверхность, по которой штампы соприкасаются между собой. При открытой штамповке поверхность разъема выбирают в виде плоскости или сочетания плоскостей так, чтобы поковка свободно вынималась из штампа. Желательно, чтобы плоскость разъема совпадала с двумя наибольшими габаритными размерами детали. Тогда третий наименьший габаритный размер будет высотой детали. При этом полость штампа будет иметь наименьшую глубину и наибольшую ширину и длину, что обеспечивает его прочность, легкость изготовления и легкий выем поковки. Для
126
возможности контроля сдвига между верхним и нижним штампами необходимо, чтобы плоскость разъема пересекала вертикальную поверхность поковки.
Установление припусков, допусков и напусков необходимо, так как штамповкой нельзя получить абсолютно точные поковки. Припуски включают дефектный слой металла, вмятины от окалины, искривление поковки, обезуглероженный слой и т. д. Этот дефектный слой удаляется при механической обработке.
Допуски учитывают недоштамповку поковки по высоте, износ ручья штампов, возможный сдвиг штампов и другие факторы.
Припуски и допуски при объемной штамповке назначают по ГОСТу. Величины их зависят от габаритов и массы поковки, от вида оборудования, требуемой шероховатости поверхности.
Иногда для упрощения формы поковки и технологии ее изготовления на поковку назначают напуски. В частности, устанавливают напуск на отверстия при диаметре менее 30 мм, так как стойкость выступов штампа для получения выемки в поковке диаметром менее 30 мм будет очень мала. К технологическим напускам относятся также штамповочные уклоны, шпоночные канавки и др.
Штамповочные уклоны необходимы для облегчения заполнения полости штампа металлом и извлечения из нее поковки. Штамповочные уклоны устанавливаются сверх припуска и назначаются на все вертикальные поверхности поковки, перпендикулярные плоскости разъема. Различают наружные и внутренние штамповочные уклоны. Наружные штамповочные уклоны в большинстве случаев составляют 5…7°, внутренние 7…10°. Их величина зависит от отношения глубины полости к ее ширине, материала поковки, смазки штампов, наличия выталкивателей и других факторов.
Все пересекающиеся поверхности поковки сопрягаются по радиусам, которые необходимы для лучшего заполнения полости штампа и предохранения его от преждевременной
127
поломки, уменьшения концентрации напряжений в штампе. Радиусы закруглений выбирают по таблицам в зависимости от отношения глубины прилегающей полости к ее ширине. Внутренние радиусы примерно в три раза больше соответствующих наружных.
При штамповке в штампах с одной плоскостью разъема нельзя получить сквозное отверстие в поковке. Поэтому для экономии металла и облегчения последующей прошивки в поковке делают наметку с перемычкой — пленкой небольшой толщины. Обычно толщина пленки составляет 0,1 диаметра отверстия, но не менее 4 мм.
Определив все размеры спроектированной поковки с учетом температурной усадки, получают чертеж горячей поковки, по которому изготовляется полость штампа. Чертеж поковки при штамповке в закрытых штампах составляется по тем же принципам, но имеются некоторые особенности. Плоскость разъема обычно выбирают по верхней или нижней торцевой поверхности детали в той части, которая имеет наибольшую площадь поперечного сечения и вертикальные прилегающие к ней стенки. При штамповке на молоте более целесообразно выбирать нижнюю торцевую поверхность, с тем, чтобы поковка оставалась на выступе нижнего штампа и ее легко можно было удалить после штамповки. Штамповочные уклоны целесообразно выбирать несколько уменьшенными по сравнению с обычной штамповкой. Наружные радиусы закруглений выбирают в зависимости от глубины прилегающей полости, но не менее 1,5 мм; внутренние обычно в 2,5…3 раза больше, чем наружные.
При штамповке в разъемных матрицах наличие двух плоскостей разъема позволяет не предусматривать напусков там, где потребовалось бы делать их в штампах с одной плоскостью разъема. Штамповочные уклоны назначают значительно меньше (0,5…1,5) или совсем не предусматривают.
128
3.8.4. Оборудование для горячей объемной штамповки
Для горячей объемной штамповки применяют молоты, кривошипные горячештамповочные прессы, горизонтальноковочные машины, гидравлические прессы, винтовые прессы и машины для специализированных процессов штамповки. Процессы штамповки на этих машинах имеют свои особенности, обусловленные устройством и принципом их действия.
Основным видом штамповочных молотов являются паровоздушные штамповочные молоты. У штамповочных молотов стойки станины устанавливают непосредственно на шаботе. Масса шабота у штамповочных молотов в 20…30 раз больше массы падающих частей. Паровоздушные штамповочные молоты строят с массой падающих частей 630…25 000 кг.
На молотах штампуют поковки разнообразных форм преимущественно в многоручьевых открытых штампах.
У бесшаботных паровоздушных молотов шабот заменен подвижной бабой, соединенной с верхней бабой механической или гидравлической связью. При соударении верхней и нижней баб развивается значительная энергия, что позволяет штамповать на этих молотах крупные поковки преимущественно в одноручьевых штампах (ввиду подвижности обоих штампов многоручьевая штамповка на них затруднена).
Кривошипные горячештамповочные прессы имеют постоянный ход, равный удвоенному радиусу кривошипа. Поэтому в каждом ручье штампуют за один ход пресса, и производительность штамповки на прессах выше, чем на молотах. При штамповке на кривошипных прессах имеются большие возможности для механизации и автоматизации процесса, чем при штамповке на молотах.
Заготовка перед штамповкой на прессе должна быть полностью очищена от окалины, так как деформация происходит за один ход пресса; при наличии окалины она заштамповывается в поверхность поковки. Стоимость кривошипного
129
горячештамповочного пресса в 3…4 раза выше стоимости эквивалентного по мощности молота.
На кривошипных прессах возможна штамповка всех видов поковок, штампуемых на молотах. Однако при штамповке поковок с удлиненной осью и большой разностью площадей поперечных сечений по длине требуется применение предварительно профилированных заготовок.
Ввиду худшего заполнения полостей при штамповке сложных поковок на прессах применяют большее число ручьев, чем в молотовых штампах. Штампы на прессах не должны смыкаться на величину, равную толщине заусенца, поэтому полость для него делается открытой, в отличие от молотовых штампов.
Благодаря наличию выталкивателей на прессах удобно штамповать в закрытых штампах выдавливанием и прошивкой. Кривошипные горячештамповочные прессы имеют усилие 6,3…100 МН; такие прессы успешно заменяют штамповочные молоты с массой падающих частей 0,63…10 т.
Широкое применение для горячей объемной штамповки, особенно для операций высадки, получили горизонтально-ко- вочные машины (ГКМ), представляющие собой механический пресс, расположенный в горизонтальной плоскости. Кроме главного деформирующего ползуна имеется ползун, движение которого перпендикулярно движению главного ползуна, осуществляющего смыкание и размыкание блока матриц. В отличие от штампов молотовых и прессовых штампы для ГКМ имеют два взаимно перпендикулярных разъема и могут быть открытыми и закрытыми. Наличие двух разъемов в штампе создает лучшие условия для выполнения высадочных работ и позволяет получать поковки, как правило, без штамповочных уклонов. Горизонтально-ковочные машины создают усилие на главном ползуне до 31,5 МН.
Поковки, получаемые на горизонтально-ковочных машинах, обычно имеют форму тел вращения. Типичные представители поковок, штампуемых на ГКМ, приведены на рис. 3.19. Эти машины позволяют производить высадку конусов на
130