
576
.pdfможно в трещины, образовавшиеся в результате напряжений в слое покрытия.
При заполнении формы на ее поверхностные слои оказывают эрозионное влияние потоки жидкого металла. Наиболее заметно это воздействие на участке, где скорость течения металла максимальна (вблизи литниковой системы). Смытые жидким металлом частицы поверхностного слоя разносятся потоком по всему объему отливки и являются источником таких дефектов, как засоры. Если потоком металла смывается противопригарная краска, то на оголенном участке обязательно образуется металлизированный пригар. Именно этим чаще всего объясняется широко известный из практики факт образования пригара в зоне подвода металла.
Приведенные примеры наглядно показывают важность изучения таких механических свойств противопригарных покрытий и смесей, как прочность при разрыве и изгибе, пластичность и деформируемость, эрозионная стойкость покрытия. Именно эти свойства в значительной степени определяют противопригарные характеристики литейной формы.
Поверхность литейной формы еще до контакта с жидким металлом нагревается за счет излучения и конвекции. Чем больше масса отливки и продолжительность заливки, тем выше температура поверхности. Продолжительность заливки крупных форм составляет несколько минут, в течение которых температура поверхности формы может достичь 1000 ºС и более. Определение этой температуры расчетным путем затруднено из-за отсутствия необходимых данных, например об отражательной способности формовочных смесей и покрытий, и неопределенности условий нагрева. В табл. 7 (по данным О.М. Жудро) приведены некоторые данные о нагреве поверхности формы стальных отливок, полученные в реальных производственных условиях.
31
ELIB.PSTU.RU

|
|
|
|
|
|
Таблица |
7 |
|
|
Нагрев поверхности форм стальных отливок |
|
|
|||||
|
|
|
|
|
|
|
|
|
Отливка |
отливкиМасса, кг |
Продолжительность заливки, с |
Массоваяскорость заливки, кг/с |
скоростьСредняяподъема металлауровня, мм/с |
Температура заливаемогометалла, ºС |
точкиВысотазамера температурыповерхности плоскостинижнейот , мм |
Температураповерхности контактамоментук металла |
формойс , ºС |
|
|
|
|
|
|
|
|
|
|
|
|
|
|
|
|
|
|
Боковина: |
|
|
|
|
|
|
|
|
левая |
13 000 |
300 |
43,3 |
4,1 |
1540 |
125 |
790* |
|
правая |
|
|
|
|
|
225 |
900* |
|
11 100 |
240 |
46,2 |
3,2 |
1565 |
390** |
600* |
||
Стол |
16 000 |
480 |
31,0 |
5 |
1585 |
1200 |
1180 |
|
копра |
|
|
|
|
|
|
|
|
Станина |
21 200 |
520 |
78,0 |
7,5 |
1540 |
1000 |
1220* |
|
Корпус |
22 000 |
360 |
81,3 |
9,3 |
1565 |
1450 |
1270 |
|
|
|
|
|
|
|
|
(850) * |
|
Опора |
7400 |
180 |
41,1 |
5,1 |
1555 |
180 |
600* |
|
|
|
|
|
|
|
690 |
1040* |
Примечание: * температура формыподслоемпротивопригарнойкраски, ** участок формы защищен стержнем от прямого излучения.
Приведенные данные показывают, что степень нагрева поверхности формы зависит от расположения точки замера, конфигурации отливки и других факторов. Важными для оценки условий работы покрытия являются высокая температура на некоторых участках формы (до 1270 ºС) и значительный перепад температуры в слое покрытия (до 420 ºС). При заливке нагреваются не только горизонтальные, но и вертикальные стенки форм, причем перепад температуры вдоль поверхности составляет > 1 ºС/мм. Все это свидетельствует о сложных условиях, в которых находится поверхностный слой формы, поэтому для
32
ELIB.PSTU.RU
предотвращения металлизированного пригара смеси и покрытия должны сохранять высокий уровень механических свойств в широком диапазоне температур.
3.3. Эрозионная стойкость
Способность формы противостоять размывающему действию потока расплавленного металла называется эрози-
онной стойкостью. Стандартными методами испытаний формовочных материалов определение этого свойства не предусмотрено. Применительно к смесям эрозионную стойкость можно косвенно характеризовать осыпаемостью. Последняя определяется поверхностной прочностью, которую тоже косвенно характеризуют твердостью. Поверхностная прочность в значительной степени зависит от общей прочности смеси, однако эти свойства не идентичны. С повышением температуры исходные характеристики смесей заметно изменяются. Например, прочность жидкостекольных смесей при температуре > 800 ºС близка к нулю; осыпаемость жидкостекольных и песчано-масляных смесей при 20 ºС практически одинакова (~ 0,2 %), при повышении температуры до 1100 ºС осыпаемость первых возрастает до 1 %, вторых – до 12 %.
Чаще всего эрозионную стойкость смесей определяют на небольших по массе технологических пробах. Нужно иметь в виду, что характеристика эрозионной стойкости является относительной, зависящей от массы отливки, объемной и линейной скоростей заливки, места расположения в форме исследуемого участка, температуры заливки и т.д. Оценивают эрозионную стойкость по массе смеси, смытой потоком металла, отнесенной к единице поверхности формы. Эрозионная стойкость зависит от плотности набивки, пористости, точнее, размера пор, прочности смеси и типа используемого связующего. Так, увеличение плотности песчано-бентонитовой смеси от 1,5 до 1,8 г/см3 уменьшает эрозию формы от 0,7–0,75 до 0,05 г/см2.
33
ELIB.PSTU.RU
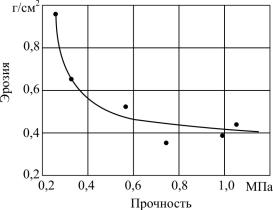
Применение мелкозернистых песков или введение в смесь дисперсионных добавок (маршалита) снижает эрозию. На рис. 4 приведена зависимость эрозии формы от сухой прочности смеси. Эрозия неокрашенной формы вызывает образование в отливках засоров, но непосредственно на возникновение пригара не влияет, если не считать, что смываемый поверхностный слой всегда более плотный, чем внутренние слои формы или стержня; последнее обстоятельство в некоторой степени снижает критическое давление проникновения и повышает опасность образования пригара.
Рис. 4. Влияние прочности смеси в сухом состоянии на эрозию формы
Эрозия противопригарного покрытия влияет на образование пригара, так как при удалении покрытия с поверхности резко уменьшается критическое давление проникновения литейной формы в целом. Определение эрозионной стойкости с целью обеспечения условий, максимально приближающихся к реальным, проводили следующим образом. Из противопригарных красок повышенной плотности изготовляли кольца толщиной 8–10 мм с внутренним диаметром 40±0,2 мм. Кольца заформовывали в смесь таким образом, что вместе с прослойкой смеси
34
ELIB.PSTU.RU
они выполняли вертикальный литниковый ход (стояк). Через стояк проливалось 200 кг жидкого металла при разных температурах. После этого кольца извлекали из формы, очищали от остатков смеси и мелких скрапин металла и замеряли внутренний диаметр кольца. Эрозия краски характеризовалась объемом смытой металлом за единицу времени заливки части кольца, отнесенным к единице рабочей поверхности образца.
Исследования наиболее распространенных противопригарных покрытий свидетельствуют о том, что характер изменения эрозионной стойкости водных красок на бентоните в интервале 20–120 ºС одинаков. Чем большее количество органических связующих приходится на единицу объема наполнителя, тем выше исходная эрозионная стойкость красок и стойкость в интервале 20–200 ºС. Падение эрозионной стойкости красок в интервале температур 200–400 ºС связано с выгоранием органических связующих. По данным Д.М. Колотило, температура деструкции СДБ, декстрина и патоки также находится в интервале
200–400 ºС.
Потери массы жидкого стекла при нагреве незначительны. В высушенном жидком стекле (силикате натрия) при нагреве до 800 ºС не происходит никаких агрегатных или полиморфных превращений. Согласно диаграмме состояния при 793 ºС силикат натрия расплавляется, однако вязкость расплава остается очень высокой вплоть до 1200 ºС. Эти обстоятельства, а также наличие бентонита объясняют высокую эрозионную стойкость жидкостекольных красок, практически не зависящую от температуры в интервале 20–1200 ºС.
3.4. Прочность противопригарных покрытий
При повышении температуры исходная прочность смеси существенно изменяется, однако принятые методы определения не характеризуют фактическое поведение смеси при нагреве.
35
ELIB.PSTU.RU
Прочность жидкостекольных смесей, например, практически равна нулю при температуре > 800 ºС, тем не менее в формах из таких смесей изготавливают довольно крупные и массивные отливки без каких-либо дефектов, возникших вследствие малой прочности. Прочность смесей на органических связующих резко уменьшается в результате деструкции последних; температура начала деструкции большинства органических материалов находится в пределах 350–550 ºС, однако такие смеси успешно применяют в производстве стального и чугунного литья, как правило, в качестве стержневых, подвергаемых большему нагреву, чем формовочные.
Условия реальной литейной формы далеки от условий определения прочности смесей при высокой температуре. В литейной форме каждый элемент объема смеси находится в условиях всестороннего сжатия. Если температура этого элемента достигнет критической tк, когда прочность смеси близка к нулю, разрушения смеси не произойдет, а под действием металлостатического давления будет наблюдаться доуплотнение смеси за счет сближения зерен песка, но форма или стержень в целом своей конструктивной жесткости не теряют, так как tк в большинстве случаев распространяется на небольшую глубину.
В противопригарном слое и в прилегающем слое смеси происходят различные физико-химические процессы, которые могут быть причинами возникновения напряжений. В процессе высыхания противопригарного слоя, нанесенного на жесткую, недеформированную форму, возникают напряжения, вызванные уменьшением объема краски. Объем материала линейно зависит от содержания влаги, а величина усадки пропорциональна изменению влажности ∆W в процессе сушки. При высыхании в слое краски могут возникнуть только растягивающие напряжения
(рис. 5, а).
36
ELIB.PSTU.RU
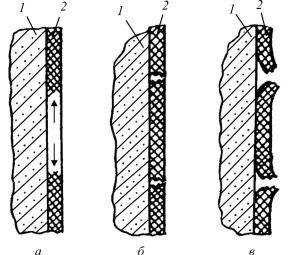
Рис. 5. Схема напряжений и разрушения слоя краски (2), нанесенного на форму (1)
По отношению к форме в целом эти напряжения будут проявляться как напряжения сдвига в плоскости соприкосновения смеси и краски. Если напряжения превысят предел прочности красок при растяжении, то в покрытии возникнут трещины (рис. 5, б), однако его деформация на этом не закончится. Поскольку высыхание краски начинается с поверхности, то по толщине слоя краски всегда будет некоторый градиент влагосодержания и, следовательно, разный уровень напряжений. Неуравновешенность напряжений создает изгибающий момент, действующий в пределах ограниченного трещинами участка покрытия и стремящийся оторвать его от смеси. Появление вида разрушения краски, изображенного на рис. 5, в, тем более вероятно, чем больше усадка краски при высыхании.
37
ELIB.PSTU.RU
3.5. Пути повышения механических свойств покрытий
Как показано выше, все механические свойства покрытий – эрозионная стойкость, прочность – в значительной степени зависят от свойств связующих материалов. Свойства последних предопределяют уровень напряжений, возникающих в слое краски при отверждении. Природа огнеупорного наполнителя, в свою очередь, незначительно влияет на перечисленные свойства, но определяет величину и характер деформации при нагреве и трещиноустойчивость покрытий.
Хотя строго обоснованных критериев выбора противопригарных покрытий в настоящее время нет, основные требования к противопригарным покрытиям можно сформулировать следующим образом. Поскольку содержание влаги во всех красках достаточно велико, избежать возникновения растягивающих напряжений при высыхании слоя покрытия не удается. Наиболее рациональным представляется выбор такого связующего материала, который обеспечивал бы минимальную усадку краски при высыхании и релаксацию начальных напряжений при нагреве до невысоких температур, пока прочность покрытия достаточно велика, а термическая деформация смеси еще не началась (релаксация напряжений должна происходить при температуре ≤ 200 ºС). Связующее должно обеспечивать максимальную прочность краски и максимальную прочность связи последней со смесью в широком диапазоне температур, что позволит повысить трещиноустойчивость противопригарного слоя при данном уровне напряжений и эрозийную стойкость покрытия. Характер термической деформации краски и смеси должен быть максимально близким.
Анализ применяемых в настоящее время связующих материалов для красок показывает, что большинство из них полностью не удовлетворяет всем указанным выше требованиям. Органические связующие (поливинилбутираль, бакелит и др.) обеспечивают высокие исходные свойства красок – большую
38
ELIB.PSTU.RU
прочность, хорошую эластичность и низкий уровень напряжений при отверждении, – однако прочность и эрозионная стойкость красок с этими связующими при высокой температуре близки к нулю. Неорганические связующие (жидкое стекло, бентонит и т.д.) способствуют возникновению больших напряжений при высыхании и нагреве красок. Оптимальными связующими для противопригарных красок следует считать органоминеральные вещества, например кремнийорганическое соединение – полиорганосилоксан [6, с. 66].
39
ELIB.PSTU.RU
4.ХИМИЧЕСКОЕ ВЗАИМОДЕЙСТВИЕ
4.1.Образование химического пригара
Химический пригар возникает в результате химического взаимодействия материала литейной формы с металлом отливки или образующимися на поверхности последней окислами компонентов сплава. Появляющиеся при этом продукты взаимодействия проникают в поверхностные слои формы и при охлаждении цементируют зерна песка, образуя химический пригар, в той или иной степени прочно связанный с отливкой.
Необходимо подчеркнуть, что под материалом формы следует понимать не только огнеупорный наполнитель формовочной смеси, связующий материал и различные добавки к смеси, но и газы, например пары воды, выделяющиеся при ее нагреве. Нужно иметь в виду, что проникать в поры формы могут не только жидкие, но и твердые продукты взаимодействия. Например, при взаимодействии металла только с окислительными газами, выделяющимися из смеси, т.е. при окислении поверхности отливки, рост окисной пленки в сторону литейной формы происходит в большей степени, нежели в сторону металла, так как объем продуктов окисления существенно превышает объем окисленного металла. Образующиеся окислы заполняют поры и окружают зерна формовочной смеси в поверхностном слое. Толщина слоя собственно химического пригара при пористости смеси 35–40 % равна толщине окислившегося слоя металла или даже несколько больше ее (рис. 6). Такое проникновение окислов в поверхностный слой формы на глубину, равную 5–6 зернам песка, при температуре, исключающей существование жидких фаз, неоднократно наблюдалось во время экспериментов.
40
ELIB.PSTU.RU