
Справочник по пайке
..pdf
0 |
1 |
2 |
3 |
4 |
5 |
|
6 |
|
7 |
8 |
19 |
10 11 |
|
12 Е 14 |
7s” |
16 К |
|||||
ттттт |
н |
|
|
|
|
|
|
|
|
|
|
|
|
|
|
|
|
|
|
|
|
т Ш Ш 1 1 ш |
|
|
|
|
|
|
j |
|
|
|
|
|
|
||||||||
|
|
|
|
|
|
|
|
|
|
|
|
|
|||||||||
|
|
|
|
|
|
|
|
|
|
|
|
|
|
||||||||
ш |
|
|
□ |
|
|
ш |
|
|
|
|
|
|
|
|
|
|
|
|
|
||
|
в № |
X L щ |
|
|
|
|
|
|
|
|
|
|
|
|
|
|
|||||
|
|
|
|
££ |
|
|
|
|
|
|
|
|
|
|
|
|
|||||
IIHl |
|
|
шш |
|
|
|
|
ото |
'Со* |
|
|
|
ш1 |
7^Г, |
|
|
|||||
ттттг в |
|
|
|
|
|
щ |
|
|
|
|
С е : |
|
|
||||||||
|
|
|
|
|
(м л■ |
|
|
|
|
|
|
||||||||||
Кп |
|
|
ш |
|
|
|
/w\ |
Ж 1 |
|
|
|
шЦd |
|
||||||||
1тттт 0 |
|
|
ggш |
|
|
|
|
||||||||||||||
Хе |
|
|
ш ш |
|
|
|
|
|
|
___ j |
|
|
|
|
|
|
|||||
|
|
|
|
|
|
|
|
|
|
|
и |
|
|
|
|
|
|||||
|
0 |
ш |
|
|
|
Nb Рт |
5т Ей |
|
Cd_ I L |
НО |
|
Е г |
I m |
|
|||||||
|
|
|
|
|
|
|
|
|
|
|
|||||||||||
ш |
|
XL Lu ш |
[та: |
|
|
g 2 L Тг_ ш щ |
Шв s |
Ро At_ |
|||||||||||||
Rn |
|
|
|
|
Т а шNp 7й_ |
|
|
|
|
|
I 1 |
|
|
|
|||||||
, 11111 |
|
|
|
|
|
|
|
|
|
|
|
|
|||||||||
|
7г_ X I А с |
|
|
Cm 1н_ T f j 7 7 Ет Md |
|
||||||||||||||||
|
|
|
|
|
|
|
|
|
|
|
|
___ 1 |
|
_ _ I |
d |
|
|
— iV |
|||
|
|
Nо Lr |
|
|
|
|
|
|
|
|
□ ___ □ |
|
|
||||||||
|
|
|
|
|
|
|
|
|
|
|
|
|
|
|
■ |
|
|
□ |
|
||
|
|
|
|
|
|
|
|
|
|
|
|
|
|
|
|
5 |
|
|
|
S |
|
0 |
11 |
2 |
3 |
4 |
5 |
|
6 |
|
7 |
8 |
9 |
|
10 |
и |
|
12 |
13 |
|
14 |
i s |
16 17 |
|
$ |
|
|
|
|
|
|
|
|
|
|
|
ШMШ Ш$$1 Ш |
||||||||
ГДО1 $ № . шС г шnf u n |
|
|
|||||||||||||||||||
н е |
1 |
|
|
ь |
ш5$ |
|
|
|
|
|
|
|
|
|
|
|
|
|
|||
Те |
ш |
|
|
|
|
|
|
|
|
|
|
|
|
|
|
||||||
ш и |
|
|
|
|
|
|
|
|
|
|
|
|
|
|
|
|
|
|
|
|
|
*******гр |
|
|
|
|
|
|
|
|
|
|
|
|
|
|
|
|
|
|
|
|
|
|
А Ш Mq Ш ; |
|
|
|
|
|
|
|
|
|
|
|
|
|
|
|
|
|
|
||
|
|
|
|
>>>> |
|
Ш |
Тс |
|
|
|
|
|
|
|
|
|
|
Ш Ш |
|||
|
h |
|
|
:1гу |
|
R u |
R h |
|
|
|
|
|
|
|
|
||||||
'ТТТТ |
|
|
щ |
|
|
f f i 1 |
|
is s |
|
|
|
1 |
|||||||||
|
|
ш , |
У S/ |
|
|
|
|
|
|
|
i |
|
|||||||||
Хе |
|
|
|
|
|
|
|
|
|
|
|
|
|
|
|
|
|||||
|
|
1 8 &Nb |
|
|
|
|
|
|
|
|
|
|
|
|
|
|
|||||
|
С |
|
|
Рт Sm |
EU |
|
D d |
Tb |
B y Ho |
E r Tm |
|||||||||||
|
|
|
|
|
|
|
|
|
|
|
Л 44 |
|
|
|
|
^Али! |
|
|
|||
|
|
УЬ |
L u |
НЕ |
Та m l |
|
R e |
OS |
$ |
5Si |
И |
|
$3ШPo A t |
||||||||
|
|
|
|
|
|
|
W |
|
|
|
|
|
|
|
|
|
|
|
|
|
|
№ |
|
|
|
Е |
|
|
|
|
|
|
|
|
|
|
|
|
|
|
|
|
|
l u l l |
|
|
Ас |
Ра |
|
|
|
|
|
|
|
|
|
|
|
|
|
|
|
|
|
|
F г |
На |
|
V |
|
N p |
P u |
Am Cm |
8 k |
C f |
E s |
Fm Md |
|||||||||
|
|
|
|
|
.in . |
|
|
|
|
|
|
|
|
|
|
|
|
|
|
||
|
|
АЮ |
L r |
|
|
|
|
|
|
|
|
|
|
|
|
|
|
|
|
|
£7 |
|
|
|
|
|
|
|
|
|
|
|
|
|
|
|
|
|
|
|
|
Продолжение рис. 1 (расшифровку обозначений 1-6 см. на с. 9)
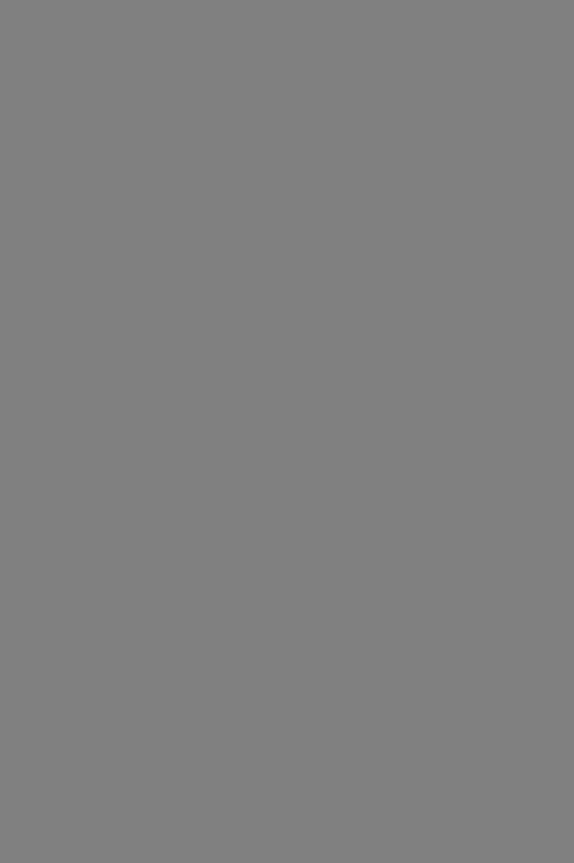

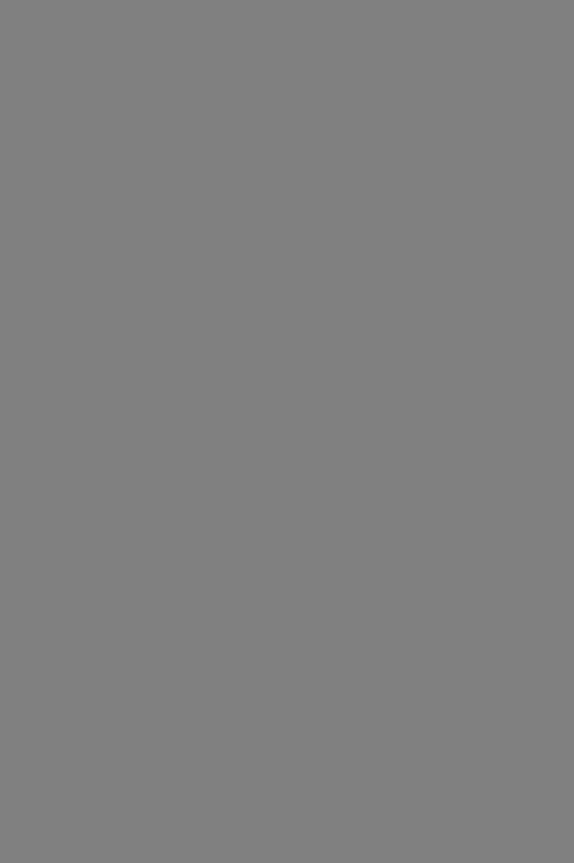
рой из указанных фаз обусловлено ее выделе нием на поверхности паяемого металла в виде прикристаллизованных слоев, что и подтвер ждается микрорентгеноспектральным анализом образцов, паянных при температуре 1350 °С (рис. 7). На кривой распределения отчетливо видна остановка, соответствующая слою твер дого раствора на основе железа (11 % меди).
В соответствии с диаграммой состояния уменьшение растворимости железа в жидкой меди при охлаждении приводит к выделению фазы, богатой железом. Последняя в условиях образования растворно-диффузионного спая выделяется в виде эпитаксиального слоя на границе с паяемым металлом.
При пайке железа медью с разными зазо рами структура, формирующаяся при затверде вании расплава, оказывается при прочих рав ных условиях различной в малых и больших зазорах. В широких зазорах (0,5 2 мм) кри сталлизация происходит с образованием разви той дендритной структуры и имеет характер объемного затвердевания. Содержание железа в осях дендритов достигает 4 %, а на перифе рии падает до 2 2,5 % (массовые доли). Смена форм затвердевания с изменением раз мера зазора вызывается изменением условий кристаллизации. Согласно существующим представлениям тип кристаллизации сплавов определяется градиентом температуры распла ва, а также величиной и протяженностью об ласти концентрационного переохлаждения вблизи фронта кристаллизации. При прочих равных условиях уменьшение зазора, а следо вательно, слоя кристаллизующейся жидкости, начиная с определенного момента, приводит к таким изменениям указанных факторов, что дендритная форма кристаллов постепенно ус тупает место ячеистой, а последняя - преобла дающему росту кристаллов с гладкой поверх ностью. Окончательная кристаллическая струк тура металла шва не соответствует первона чальным формам роста кристаллов. Новые границы зерен в шве пересекают в произволь ных направлениях дендритные и ячеистые кри сталлы. При больших зазорах имеются участ ки, где «вторичные» границы совпадают с по граничными зонами первичных дендритов. При малых зазорах структура шва по ширине представляет собой один слой зерен. Возник новение вторичной структуры в литых сплавах связывается с образованием при кристаллиза ции большого числа дефектов (дислокаций и вакансий), способных перемещаться и группи
роваться в определенных участках затверде вающего металла.
Уменьшение зазора и, следовательно, ко личества затвердевающего металла, в конеч ном счете, приводит к образованию плоских границ зерен при пайке как однокомпонентны ми, так и многокомпонентными припоями.
С уменьшением зазора под пайку от 2 до 0,3 мм предел прочности соединений встык при пайке железа медью возрастает с 255 МПа, что выше предела прочности припоя в исход ном состоянии, до 338 МПа, что соответствует пределу прочности железа. При зазоре 0,3 мм медная прослойка оказывается равнопрочной с паяемым металлом. Дальнейшее уменьшение зазора приводит к тому, что шов оказывается прочнее основного металла. При механических испытаниях разрушение образцов происходит по паяемому металлу и прочность стыковых соединений, выполненных с зазором 0,15 мм и менее, перестает зависеть от толщины медной прослойки.
Поскольку состав зоны сплавления зави сит от зазора под пайку и с уменьшением зазо ра содержание паяемого металла в зоне сплав ления возрастает, то наблюдаемая зависимость прочности паяного соединения от размера за зора может быть объяснена различной прочно стью образующегося в шве сплава, изменением структуры шва с уменьшением зазора и «кон тактным упрочнением».
Эффективность «контактного упрочне ния» в случае стыкового соединения стержней возрастает с уменьшением отношения ширины шва (толщины мягкой прослойки) к диаметру стержня. В результате нормальные напряжения в прослойке могут значительно превысить пре дел прочности ее материала, определенный при свободной деформации. Для вязкого разруше ния соединения по мягкой прослойке получена
Си (массовые доли), %
1¥
\
20 4\
16 31
11
8
<ь
оW го зо м 50 бомкн
Рис. 7. Распределение меди в зоне спая при пайке стали 03-ВД
зависимость прочности соединения от механи ческих свойств материала прослойки и ее раз меров:
О, =о” |и-[зл/Зае (1 + е„)3/2]"‘},
где оЦ*, ев - соответственно предел прочности
и относительное удлинение материала про слойки в исходном состоянии; as - отношение ширины шва (толщины прослойки) к диаметру стержня.
При образовании спаев взаимодействие на границе паяемый металл - расплав припоя может приводить к возникновению общих зе рен. Такой тип кристаллизации связан с проис ходящим при пайке оплавлением зерен паяемо го металла в диффузионной зоне, насыщенной компонентами припоя. Такой вид спая харак терен для пайки железа бериллием (рис. 8).
Замер микротвердости в этом случае по казал, что, если с увеличением выдержки при температуре пайки твердость паяемого металла снижается, твердость в шве возрастает, причем наибольшая твердость наблюдается в цен тральной его части (рис. 9). Последнее связано с образованием интерметаллидов в зоне шва, более богатых бериллием.
Согласно исследованиям поверхностных слоев стали 03-ВД и сталей, насыщаемых при температурах 1000 1150 °С бериллием, диффузия бериллия в сталь начинает заметно идти при 800 .°С; при 1150 °С происходит оп лавление зерен. На границе низкоуглеродистая сталь - бериллий при 1000 °С одновременно идут два процесса:
- диффузия бериллия в сталь, что вызы вает у - а-перекристаллизацию и появление кристаллов a -фазы, ориентированных в на правлении диффузии;
Рис. 8. Микроструктура шва при пайке стали 03-ВД бериллием (температура пайки 1350 °С, выдержка 1 мин; увеличение х 125)
Рис. 9. Распределение микротвердости по ширине шва при пайке стали 03-ВД бериллием:
/ - выдержка при пайке 1 мин; 2 - выдержка
после пайки при 1250 °С 1 ч
- диффузия углерода из стали в бериллий, что вызывает обеднение поверхностных слоев стали углеродом.
Взаимодействие бериллия с углеродом приводит к образованию карбида бериллия, имеющего высокую твердость.
При охлаждении насыщенных бериллием слоев происходит выпадение из перенасыщен ного раствора бериллия в a -железе интерме таллических соединений - бериллидов, что сопровождатся повышением твердости.
Формирование галтелей паяных со единений. Свойства паяных соединений в зна чительной мере определяются характером гал телей, которые в зависимости от типа соедине ний могут воспринимать до 75 % внешней на грузки. Процессы образования галтелей паяно го соединения зависят от природы взаимодей ствующих металлов, зазора, режима пайки, характера флюсования и других факторов. При прочих равных условиях образование галтелей определяется количеством жидкой фазы в шве. Гаптель паяного соединения можно рассматри вать как своеобразную емкость, которая в про цессе пайки заполняется расплавом припоя. При оптимальном количестве припоя в шве и необходимых условиях формирования спая образуются полномерные галтели. Избыток жидкой фазы, неравномерность зазора ведут к искажению формы галтелей, к образованию наплывов.
В основу расчета равновесной формы галтели положена зависимость, описывающая форму поверхности жидкости, граничащей с плоским вертикальным элементом детали.
При равновесной форме жидкости гра-
du
ничные условия следующие: и = 0 и — = 0 dv
Рис. 10. Форма галтели паяного соединения:
а - в тавровом соединении; б - при различных краевых углах смачивания; 1 - 0°; 2 - 10°; 3 - 20°; 4 - 30°; 5 - 40°; 6 - 45°
при v -> оо, где и - ордината галтели; и - аб сцисса галтели.
Для расплава припоя в равновесном со стоянии граничные условия следующие: и = 0
du |
|
при v = v0 |
(рис. 10, а). Согласно |
||
и — = —tgP |
|||||
dv |
|
|
|
|
|
1л |
|
л |
и = и0 |
du |
|
рис. 10, |
а при о = 0 |
и — = -ctg а. |
dv
Значения параметров UQ, а, Р, а, получен ные экспериментально на меди с применением различных припоев и флюса № 209 при темпе ратуре (800 ± 10) °С и выдержке 5 мин, приве дены в табл. 2. Нулевое значение угла р связа но с условиями эксперимента.
Применение расчетных методов оценки галтелей при проектировании изделия позволя ет обеспечить формирование полных галтелей при минимальном расходе припоя.
2. Значения капиллярной константы а и
краевого угла смачивания различных припоев
Припой |
М», мм |
<х° |
р° |
а*, мм |
|
ПСр 40 |
|
4,7 |
21 |
0 |
5,9 |
МЦФЖ |
|
6,0 |
5 |
0 |
6,2 |
МФОЦ-7-3-2 |
4,5 |
9 |
0 |
4,9 |
|
ПМФС |
|
3,2 |
14 |
0 |
3,7 |
Сплав |
равных |
4,2 |
11 |
0 |
4,7 |
долей |
меди и |
|
|
|
|
олова |
|
|
|
|
|
*а - капиллярная константа, связанная с по
верхностным натяжением припоя ст и его плотно
стью зависимостью а =
Влияние состава припоя и газовой сре ды в камере пайки на свойства паяных со единений. Изменение свойств паяемого метал ла происходит не только под влиянием нагрева и взаимодействия с расплавом припоя, но и под действием газовой среды, находящейся в каме ре пайки. Влияние газовых сред особенно за метно проявляется, когда паяемый металл ак тивно взаимодействует с газовыми средами. Из конструкционных материалов, применяемых в паяных изделиях, таким свойством обладают титан и сплавы на его основе.
Взаимодействие титана с кислородом в ат мосферных условиях протекает уже при 20 °С. По мере повышения температуры интенсив ность окисления возрастает. При достижении 450 °С параллельно с окислением идет процесс проникновения кислорода в кристаллическую решетку титана и образование газонасыщенного слоя, представляющего собой твердый раствор газа в металле. При температуре выше 600 °С кислород активно диффундирует в титан.
Наличие газов в кристаллической решет ке титана приводит к ее искажению, являюще муся причиной уменьшения пластических свойств материала.
Высокотемпературный нагрев титана на воздухе, а также в среде кислорода приводит к появлению на его поверхности окалины, состоя щей главным образом из рутила. При окислении титана в парах воды при 800 1200 °С окисная пленка состоит только из фазы ТЮ2 в модифи кации рутила; фаз Ti20 3 и ТЮ не обнаружива ется. Таким образом, в образовании поверхно стных пленок на титане основная роль отво дится кислороду и водяному пару.
Из других атмосферных газов в образова нии поверхностных пленок на титане при вы соких температурах большое значение имеет
азот. При окислении титана на воздухе азот в составе окалины обнаруживается начиная с температуры 900 °С. Отмечается, что наличие азота в решетке рутила приводит к образова нию дырчатой структуры, облегчающей диф фузию кислорода в объеме окисной пленки. Значения толщин окисных пленок, образую щихся при окислении титана ВТ1 на воздухе, приведены в табл. 3.
3. Значения толщин окисных пленок при окислении титана ВТ1 на воздухе, мм
Темпе- |
|
|
Время выдержки, ч |
|
|
||
|
|
|
|
|
|
|
|
ратура, |
|
1 |
2 |
4 |
8 |
16 |
32 |
°С |
0,5 |
||||||
800 |
_ |
- |
- |
- |
0,005 |
0,017 |
0,029 |
900 |
0,012 |
0,02 |
0,03 |
0,05 |
0,075 |
0,10 |
0,25 |
1000 |
0,035 |
0,06 |
0,10 |
0,19 |
0,25 |
0,30 |
- |
Пайку титановых сплавов производят при температуре около 1000 °С, поэтому при нали чии окислительной атмосферы взаимодействие кислорода с титаном в процессе пайки проте кает с большой интенсивностью.
Удаление окисных пленок при пайке ти тана фактически обеспечивается путем регули рования соотношения скоростей окисления и растворения окислов в паяемом металле и в конечном итоге достигается за счет примене ния среды с парциальным давлением кислоро да, при котором скорость растворения пленки больше, чем скорость ее роста.
Применение аргона или вакуума при пай ке титана не изменяет механические свойства соединений, выполненных припоями на основе серебра, а также припоями систем титан - никель, титан - никель - медь, титан - никель - кобальт и др. Однако в отдельных случаях применение вакуума приводит к лучшим ре зультатам по сравнению с аргоном. Например, при пайке титана припоем на основе алюминия в вакууме с остаточным давлением 0,133 Па растекание лучше, чем в атмосфере аргона. При пайке титана с повышенным содержанием водорода в вакууме достигается не только улучшение условий пайки, но и обезводороживание паяемого металла. В связи с этим утвер дилось мнение о предпочтительности вакуума перед нейтральными газами даже в тех случа ях, когда не удается создать высокой степени разрежения, как это имеет место, например,
при пайке крупногабаритных изделий в печах с использованием механических вакуумных на сосов. Применение низкого вакуума с повы шенным содержанием примесей приводит к уменьшению пластичности металла, что стано вится особенно опасным при пайке тонко листовых конструкций. В этом случае исполь зование вместо вакуума аргона может снизить содержание примесей. Поэтому, если необхо димо максимальное сохранение пластичности титана, то, несмотря на удовлетворительное протекание процесса пайки в вакууме, вопрос предпочтительности вакуума или аргона сле дует решать с учетом содержащихся в них вредных примесей.
В зависимости от характера взаимодейст вия металлов при образовании спая и, следова тельно, от направленности изменения свойств взаимодействующих металлов может резко изменяться прочность паяемого металла под действием расплавленного припоя. Наимень шие изменения наблюдаются в случае взаимо действия металлов, расположенных рядом в периодической системе элементов Д. И. Мен делеева и образующих непрерывные твердые растворы. Изменение механических свойств ограниченных твердых растворов примерно обратно пропорционально предельной раство римости.
Значения предельной растворимости компонентов припоев в титане приведены в табл. 4, там же указаны интерметаллиды, обра зующиеся в системах этих металлов с титаном, и их температуры плавления.
Ввиду того, что при 20 °С растворимость компонентов припоев в a-Ti значительно ниже предельной, указанной в табл. 4, после пайки припоями, содержащими никель, кобальт, мар ганец, получить структуру, состоящую из твердого раствора, можно лишь в случае при менения весьма продолжительных выдержек и при толщине паяемого материала, которая по зволяет рассматривать диффузию компонентов припоя в решетку титана как в бесконечное пространство.
В большинстве встречающихся на прак тике случаев образующаяся при диффузионной пайке структура шва двухфазная: твердый рас твор a-Ti и интерметаллидные включения. Изменение механических свойств сплавов, имеющих в своем составе интерметаллиды, зависит от особенностей выделения второй фазы и характера дисперсионного механизма упрочнения. В результате дисперсных выделе-
4.Растворимость металлов в титане и
составы интерметаллидов, образующихся при их взаимодействии
|
|
Предельная растворимость |
|
||
Группа |
Металл |
a-Ti |
|
p-Ti |
|
периодической |
Содержание |
|
Содержание |
|
|
системы |
|
о |
о |
||
|
|
(массовые |
О |
(массовые |
о |
|
|
доли), % |
|
доли), % |
|
1 |
Ag |
14,6 |
855 |
30,5 |
1040 |
|
Си |
2,1 |
798 |
17,7 |
990 |
IV |
Sn |
22,5 |
885 |
35 |
1600 |
VII |
Мп |
0,5 |
530 |
33 |
1175 |
VIII |
Со |
- |
685 |
17 |
1020 |
VIII |
Ni |
0,1 |
770 |
13 |
955 |
Металлические соединения в системе
Состав |
Tnл, °C |
TiAg |
1040 |
Ti2Cu |
990 |
TiCu |
975 |
Ti2Cu3 |
920 |
TiCu3 |
885 |
Ti3Sn |
1663 |
Ti2Sn |
1552 |
Ti5Sn3 |
1505 |
Ti6Sn5 |
1495 |
TiMn |
950 |
TiMn2 |
1330 |
TiCo2 |
1250 |
TiCo |
1500 |
Ti2Co |
1050 |
Ti2Ni |
984 |
TiNi |
1310 |
TiNi3 |
1380 |
ний может иметь место как упрочненение, так и разупрочнение сплава. Выделение небольшо го количества второй фазы в мелкодисперсном состоянии сопровождается повышением проч ности и уменьшением пластичности. Вторая фаза в этом случае вносит искажения в кри сталлическую решетку металла. Увеличение количества выделяющейся избыточной фазы может послужить причиной резкого уменьше ния пластических и прочностных свойств, если эта фаза выделяется в виде сетчатого каркаса. Менее опасны интерметаллиды в случае их выделения в виде сосредоточенных включений.
Уменьшение количества выпадающих интерметаллических включений, а следова тельно, и снижение охрупчивания титана могут быть достигнуты за счет различных приемов. Из них для пайки представляют интерес два:
-выбор компонентов припоя, которые имеют увеличенную растворимость в a-Ti;
-использование в качестве припоя мно гокомпонентных композиций, позволяющих при таком же количестве припоя, вводимого в
зону пайки, как и в случае однокомпонентного
припоя, уменьшить степень пересыщения a-Ti.
При применении в качестве припоя мно гокомпонентных композиций, например при пай ке титанового сплава ОТ4 (ГОСТ 19807-91), наи большая прочность наблюдается при толщине медного слоя 8 мкм, а никелевого 2 мкм, т.е. при содержании в покрытии 80 % Си и 20 %Ni (рис. 11).
Толщина слоя Си, мкм
Рис. 11. Механические свойства образцов из сплава ОТ4 в зависимости от толщины медно-никелевого покрытия:
/- после выдержки 30 мин при 1000 °С; 2- после выдержки 2 ч при 1000 °С
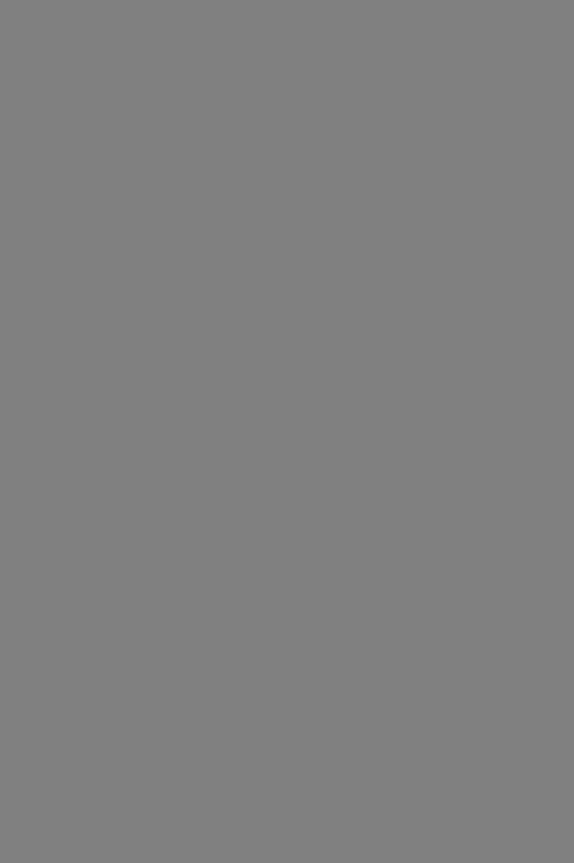