
Аэрокосмическая техника высокие технологии и инновации – 2015
..pdf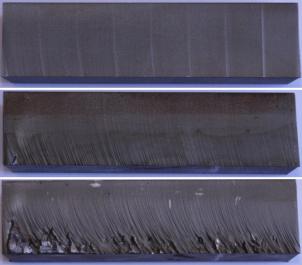
Гидроабразивная резка является сложным технологическим процессом, на качество которого влияет множество технологических параметров. При резе толстолистовых материалов наблюдается явное разделение раза на две характерные зоны: зона гладкого и волнистого реза.
Получены экспериментальные образцы из стали 30ХГСА толщиной 30 мм, на которых исследовалось влияние подачи режущей струи на шероховатость поверхности реза, величину волнистости, ширину зоны гладкого и волнистого реза. По данным образцам планируется определить зависимость отставания режущей струи по направлению подачи.
Рис. 1. Влияние подачи режущей струи на шероховатость и волнистость поверхности. Увеличение подачи справа налево
При эксперименте менялась подача от 5 до 120 мм/мин с шагом 5 мм/мин. При этом получены образцы, на которых отчетливо видно образование ступеней на маленькой скорости резания, а также определена скорость, при которой прекращается сквозное прорезание металла.
61
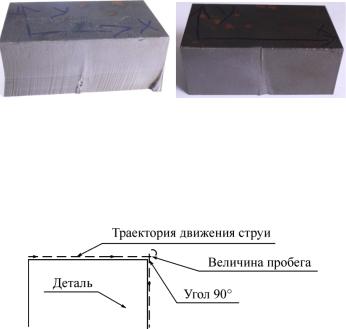
Явление недореза на внешних углах происходит вследствие отставания струи по ходу движения подачи. При разделительной резке этот параметр не столь критичен, но если выполняется качественный или тонкий рез, то это явление может привести к возникновению брака детали. Как и отставание струи, величина недореза зависит от технологических параметров: давления струи, твердости обрабатываемого материала, расхода и зернистости абразива, подачи режущей головки. Как правило, оборудование не позволяет менять большинство технологических параметров, поэтому был проведен эксперимент на стали 30ХГСА толщиной 30 мм по влиянию скорости подачи на величину заусенца.
При уменьшении подачи можно достичь почти идеально гладкой кромки реза. Эксперимент показал, что при скорости реза 42,3 м/мин величина заусенца составила 2,77 мм, а при ско-
рости 14,1 м/мин – 0,13 мм (рис. 2).
Рис. 2. Возникновение недореза на острых углах детали (справа)
Существует еще один способ уменьшения влияния этого эффекта, изменения траектории инструмента – головки. Суть метода заключается в расширении траектории движения инструмента на острых углах (рис. 3).
Рис. 3. Траектория движения струи
62
При данной траектории струя, проходя дополнительное расстояние – величину перебега, успевает дорезать материал в нижней части реза, тем самым исключая возможность появления брака детали. Величина перебега зависит от всех параметров технологического процесса.
Библиографический список
1.Барсуков Г.В. Повышение эффективности гидроабразивного резания на основе дискретного регулирования технологической системы: дис. … д-ра техн. наук. – Орел, 2006. – 411 с.
2.Zeng J., Munoz J.P. Intelligent Automation of AWJ Cutting for Efficient Prodaction // Proc. Of the 12th Int. Symp on jet Cutting Technology, BHRA. Rouen. – France, 1994. – P. 401–408.
3.Гидрорезание судостроительных материалов / Р.А. Тихомиров, В.Ф. Бабнин, Е.Н. Петухов, И.Д. Стариков, В.А. Ковалев. – Л.: Судостроение, 1987. – 164 с.
63
УДК 621.7
ТЕОРЕТИКО-ВЕРОЯТНОСТНАЯ МОДЕЛЬ ВИБРОУДАРНОГО УПРОЧНЕНИЯ
Ю.П. Анкудимов, И.В. Садовая
Донской государственный технический университет, Ростов-на-Дону, Россия
e-mail: i_sagulenko@mail.ru
Представлена теоретико-вероятностная модель процесса виброударного упрочнения поверхностного слоя деталей летательных аппаратов. Предложены зависимости, позволяющие с требуемой вероятностью определять режимы виброударного упрочнения, обеспечивающие минимальные значения энергетического воздействия частиц ударной среды и минимальное количество ударов, приходящихся в каждую точку обрабатываемой поверхности, ответственных за требуемое технологическое действие: степень и глубину наклепа, смятие микронеровностей и т.д.
Ключевые слова: виброударное упрочнение, теоретиковероятностная модель, качество поверхности.
Виброударное упрочнение (виброударная отработка деталей) широко применяется для повышения ресурса работы деталей летательных аппаратов, работающих в условиях знакопеременных нагрузок. Эффект упрочнения достигается путем многократного упругопластического деформирования и передеформирования их поверхностного слоя частицами гранулированной обрабатывающей среды (чаще всего шариками из стали ШХ15), помещенными в рабочую камеру, совершающую низкочастотные колебания.
На основе модели «динамических столбиков» А.Е. Кобринского, с учетом последних работ А.П. Бабичева, Ю.Р. Копылова [1–3] предложена теоретико-вероятностная модель процесса виброударного упрочнения.
64
Модель описывает процесс виброударной обработки со следующими допущениями:
–систему обрабатывающей среды составляют сферические тела квадратной упаковки« одного размера;
–система совершает колебания в однородном гравитационном поле вдоль вертикальной оси;
–слои сферических тел взаимодействуют между собой посредством прямых центральных ударов;
–диссипативные свойства системы описываются коэффи-
циентом восстановления при ударе Ky ;
–внешнее воздействие передается нижнему слою сферических тел от дна рабочей камеры радиуса R→∞, совершающего гармонические колебания;
–частота колебаний системы обрабатывающей среды равна частоте колебаний дна рабочей камеры.
Используя основные положения работы [1] по динамике «столбиков», получим при соударении i и i + 1 слоя сферических тел соотношения:
Ui,1 Vi 1,1 Ky Vi 1,2 Ui,2 ,
Vi,1 Ui,2 g ti'' ,
Ui,1 Vi,2 g ti' ,
где ti'' – время безударного движения i слоя после соударения в i + 1 паре слоев; ti' – время безударного движения i слоя после
соударения в i паре слоев.
Уравнение удара первого слоя с дном рабочей камеры выразится соотношением
V1,2 Kyo V1,1 1 Kyo Ao cos t ,
где Kyo – коэффициент восстановления при ударе первого слоя с облицовкой дна рабочей камеры. Свойства материала обли-
65
цовки целесообразно выбирать таким образом, чтобы Kyo при-
ближался к единице.
Потеря энергии в i слое выразится соотношением
|
m Ui2,1 Ui2,2 |
|
m |
|
1 |
Ky |
|
1 |
|
|
||
Ei |
|
|
|
|
|
|
|
n i n |
|
i |
n 1 i , (1) |
|
2 |
3 |
1 |
K y |
2 |
||||||||
|
|
|
|
|
|
где m – масса частицы слоя; n – число слоев испытывающих периодические колебания.
Вследствие «динамической вялости», обусловленной большим числом элементов и их диссипативными свойствами, верхняя часть слоев включает элементы, движущиеся как один элемент с массой, равной массе всех составляющих ее элементов. От реальной картины поведения такую систему отличает пренебрежение диссипативными свойствами верхней части
и стохастическими флуктуациям скоростей, которые возникают
вней и распространяются по ее элементам сверху вниз, постепенно затухая [1].
Учет |
«вялой» части загрузки массой М при условии |
M m n , |
с использованием основных положений работы [1], |
приводит к значениям коэффициента потери скорости: |
|
|
|
|
l i 2 2 (l |
n)2 n i 1 |
1 Ky |
|
|
|
||||
K |
|
V |
|
1 |
Ky |
|
l i 1 |
, (2) |
|||||
|
|
|
|
||||||||||
i 1 |
|
|
|
|
|
|
|
||||||
|
|
|
|
1 |
Ky |
|
|||||||
Vi |
|
V |
|
l i 1 |
2 |
2 |
(l n)2 n i |
|
l i |
|
|||
|
|
|
|
|
|||||||||
|
|
i |
|
|
|
|
|
|
|
||||
|
|
|
1 |
Ky |
|
|
|
||||||
|
|
|
|
|
|
|
|
|
|
|
|||
где l |
H |
(Н – высота загрузки слоев, D – |
диаметр сфериче- |
||||||||||
|
D |
|
|
|
|
|
|
|
|
|
|
|
|
ских тел). |
|
|
|
|
|
|
|
|
|
|
|
Максимальные значения скорости первого слоя V1, 2 в зави-
симости от фазы соударения с дном камеры, материала частиц и облицовки камеры находятся в пределах A V1, 2 3 A .
66

Зная законы изменения скорости частиц рабочей среды (2) и потери энергии (1) по слоям от нижнего к верхнему, можно оценить вероятность того, что каждая точка поверхности детали получит не менее k ударов сферическим телом с энергией Eд Eд0 , достаточной для изменения ее параметров качества
при равновероятностном попадании детали в i слой и общем
числе колебаний слоев, равном |
f , |
|
где |
– продолжитель- |
|||||||||||||||
ность обработки. |
|
|
|
|
|
|
|
|
|
|
|||||||||
|
|
|
|
|
|
P k x f Ф0 t f |
Ф0 |
tk , |
|
(3) |
|||||||||
|
|
|
|
|
|
|
t |
2 |
|
|
|
|
|
|
|
|
|||
где Ф0 |
t |
1 |
|
e |
x |
dx представляет собой интеграл вероят- |
|||||||||||||
|
2 |
||||||||||||||||||
2 |
|||||||||||||||||||
|
|
|
|
0 |
|
|
|
|
|
|
|
|
|
|
|||||
ностей |
tk |
|
|
|
k f pВ3 |
и |
t f |
|
f 1 pВ3 |
|
. |
||||||||
|
|
f pВ3 1 pВ3 |
|
f pВ3 1 |
pВ3 |
||||||||||||||
|
|
|
|
|
|
|
|
||||||||||||
|
|
|
|
|
|
|
|
|
|
|
pВ3 pВ1 pВ2 , |
|
|
|
|||||
где p |
|
0,78 |
|
d |
2 |
|
|
|
|
|
|
|
|
|
|
|
|||
В1 |
|
|
0 |
|
– геометрическая вероятность покрытия квад- |
||||||||||||||
|
D2 |
||||||||||||||||||
|
|
|
|
|
|
|
|
|
|
|
|
|
|
|
рата упаковки D×D следами обработки (отпечатками диаметром d02 ) за одно колебание рабочей камеры; pВ2 1 F Eд0 – веро-
ятность удара о поверхность детали слоем частиц рабочей среды, обладающих энергией Eд Eд0 , зависящая в основном от амплитудно-частотных режимов вибрации и характеристик частиц рабочей среды, где F Eд – функция распределения энер-
гии по слоям частиц среды.
Представленные зависимости – (1)–(3) – позволяют использовать их для оценки энергетических возможностей виброударной обработки.
Предложенная модель апробирована при оптимизации ам- плитудно-частотных и временных режимов виброударной обра-
67
ботки деталей из стали 40ХГНМА и алюминиевого сплава АВТ1 на Ростовском вертолетном производственном объединении «Роствертол».
Библиографический список
1.Кобринский А.Е., Кобринский А.А. Виброударные системы. Динамика и устойчивость. – М.: Наука, 1973. – 591 с.
2.Бабичев А.П., Бабичев И.А. Основы вибрационной технологии. – Ростов н/Д: Изд. центр ДГТУ, 1998. – 624 с.
3.Копылов Ю.Р. Динамика процессов виброударного упрочнения: моногр. – Воронеж: Научная книга, 2011. – 569 с.
68
УДК 621.77.539.37
НАНОСТРУКТУРИРОВАНИЕ ПОВЕРХНОСТЕЙ ДЕТАЛЕЙ С ГАЛЬВАНИЧЕСКИМИ ПОКРЫТИЯМИ ОТДЕЛОЧНОЙ ОБРАБОТКОЙ ПРЕЦИЗИОННЫМИ МЕТОДАМИ ППД
М.Е. Попов, А. Эль Дакдуки, М. Игбоануго
Донской государственный технический университет, Ростов-на-Дону, Россия
e-mail: mepop@yandex.ru
Представлены результаты исследования технологических возможностей повышения качества хромовых электролитических покрытий методами поверхностного пластического деформирования (ППД).
Ключевые слова: функциональные покрытия, нанесение электролитических покрытий, обработка покрытий методами ППД, наноструктурирование поверхностей.
Работа машин и агрегатов современной техники происходит с возрастающими скоростями и нагрузками, при высоких и низких температурах, в агрессивных средах и вакууме. В связи с этим повышаются требования к их надежности и долговечности, все большее применение находят упрочняющие методы обработки поверхностей деталей машин.
В зависимости от условий эксплуатации деталей машин методы упрочнения можно условно разделить на следующие группы (табл. 1).
Из трех указанных в табл. 1 групп методов упрочнения к первой относятся все методы поверхностного пластического деформирования (ППД), термической, химико-термической (ХТ) и термомеханической (ТМ) обработки. Применение этих методов вызывает деформационные, структурные, фазовые изменения или изменения по химическому составу поверхностного слоя однородного материала детали.
69
|
|
Таблица 1 |
|
Методы упрочнения |
|
|
|
|
№ |
Условия эксплуатации |
Методы технологического |
п/п |
|
воздействия (упрочнения) |
1 |
Циклические нагрузки, требующие |
Силовое и тепловое воздействие |
|
высокой усталостной прочности ма- |
на поверхностные слои деталей |
|
териалов |
машин для их упрочнения |
2 |
Износ различных видов, требующий |
Методы защиты поверхностного |
|
высокойизносостойкостиматериалов |
слоя, улучшающие триботехниче- |
|
|
ские свойства поверхности |
3 |
Сложные условия циклических на- |
Комбинированные методы техно- |
|
гружений с одновременным изнаши- |
логического воздействия |
|
ванием отдельных поверхностей |
|
Ко второй группе относятся методы, связанные с нанесением различных твердых покрытий из самых разнообразных материалов (металлов, сплавов, керамики, пластмасс), в результате чего физико-химическое состояние поверхностного слоя может значительно отличаться от основного материала детали. К ним относятся наплавка и напыление, электролитические и химические покрытия, покрытия полимерными материалами, плазменные покрытия и т.д.
К третьей группе относятся комбинированные методы, включающие одновременно два или более метода, принадлежащие к различным группам (например, нанесение покрытия наплавкой с последующим ППД).
В данной работе представлены результаты исследования технологических возможностей повышения качества хромовых электролитических покрытий методами поверхностного пластического деформирования (ППД).
Качество электролитического покрытия зависит от материала детали, материала покрытия, шероховатости исходной поверхности перед покрытием, толщины покрытия, режимов нанесения покрытия и других факторов.
Толщина хромовых электротехнических покрытий определяется служебным назначением покрытия поверхности детали. В соответствии с этим будет различной и толщина требуемого
70