
Металлургия цветных металлов
..pdfжение высших сульфидов на простые сульфиды и серу по реакциям:
2FeS2->- 2FeS + S2; 4FeS + 702-^2Fe20 3 + 4S02; Cu2S ”f" 202—>- 2CuO -j- S02; 2ZnS + 302 + 2ZnO + 2S02;
S2 -j- 202-> 2S02.
Подобно высшим сульфидам диссоциирует арсено пирит:
FeAsS-^FeS + As.
Мышьяк легко летуч, он испаряется и окисляется в га зах до As20 3:
4As -j- 302 —>- 2AS20 3.
При большом избытке воздуха наблюдается дальней шее окисление:
As20 3 -f- 0 2 — AS20 5 .
Возможно и непосредственное окисление арсенопирита, однако оно приводит к тем же результатам:
2FeAsS + 502-^ Fe20 3 + As20 3 + 2S02.
Давление паров As20 3 достигает 98,1 кн/м2 (1 ат*) уже при 460° С, поэтому мышьяк легко удаляется из печи с обжиговыми газами. Давление же паров As2Os сравни тельно невелико; кроме того, этот кислотный окисел вза имодействует с основными окислами, с FeO или СаО, образуя арсенаты, например Fe3(As04hЧем больше из быток воздуха при обжиге, тем больше мышьяка связы вается в арсенаты и остается в огарке.
Сернистый газ частично окисляется избыточным кис лородом до S03, который с окислами металлов может образовать сульфаты, стойкие при высоких температурах, например сульфаты свинца и кальция.
Твердые составляющие обжигаемого концентрата вза имодействуют между собой: кислотные окислы Si02, А120 3, Fe20 3 реагируют с основными окислами FeO, СаО,1*
* 1 техническая |
атмосфера |
(1 ат) |
равна 1 кГ/см2, т. е. 1 ат= |
= 1 кГ/см2. Выразив |
в правой |
части ^ равенства килограмм-силу |
|
в ньютонах и сантиметр в метрах, получим: |
|||
|
1 ат=9,81 • 104 |
н/м2. |
|
Следовательно, 1 аг = 9,81 • 104 н/м2= 9,81 |
кн/м2. |
Cu20 и др., образуя соединения типа солей: силикаты, алюминаты и ферриты.
Разложению карбонатов способствует присутствие Si02 и S03, образующих более прочные соли, поэтому
СаСОз -|- S0 3—*■CaS04 -I- CQj; 2СаС03 -}- Si02 —>- Ca2Si04 2 с0 2; 2MgC03 + Si02->- Mg2Si04 + 2C02.
Реакции между твердыми веществами часто не завер шаются из-за нарушения контакта между ними, поэтому в обожженном концентрате мы зачастую находим значи тельное количество исходных веществ и конечных про дуктов реакций.
Температура в обжиговых печах зависит от содержа ния серы в концентрате, количества концентрата, загру жаемого в единицу времени, и количества поступающего в печь воздуха. С повышением температуры производи тельность печей увеличивается. Выбор температурного режима зависит от состава обжигаемого сырья, главным образом от наличия в нем легкоплавких составляющих. Спекание медных концентратов может быть вызвано об разованием сплавов FeS—Cu2S, минимальные температу ры плавления которых находятся в пределах 960—1000° С. Температура в отдельных очагах горения, например около движущегося гребка, часто значительно превы шает среднюю в массе шихты. Учитывая все эти факто ры, температуру при обжиге медных концентратов обыч но поддерживают не выше 850° С.
Количество подаваемого в печь воздуха ограничено необходимостью получать отходящие газы с содержани ем не менее 4% SO2, чтобы они были пригодны для про изводства серной кислоты. Кроме того, повышенный рас ход воздуха приводит к усиленному пылеобразованию: отходящие газы уносят из печи в виде пыли 10—-12% об жигаемого материала. „
Многоподовые обжиговые печи громоздки и мало про изводительны. Одна печь указанного выше размера об жигает в сутки до 250 тшихты, снижая содержание серы в ней с 24—25 до 10—12%• Обжиговые газы содержат до 7% S02. Надо заметить, что и эти сравнительно невысо кие технико-экономические показатели достигаются толь ко благодаря постоянному контролю химического состава
и крупности шихты, состава огарка, температуры газов на подах и количества подаваемого воздуха. Для посто янного контроля режима обжига—температуры и тяги в печи — применяются самопишущие приборы.
За последние годы в металлургии меди начали при менять более производительный способ обжига — в ки пящем слое. От описанного выше он отличается не толь ко высокой производительностью, но и возможностью по лучать отходящие газы, более богатые SO2. Если в 1 м3 объема многоподовой печи выгорает в сутки около 140 кг серы, то в печи'кипящего слоя 750 /сг, а содержа ние SO2 в газах достигает 14%.
Печь для обжига в кипящем слое имеет форму цилин дра или призмы. Свод и стены, укрепленные стальным кожухом, футерованы внутри жаростойким бетоном. По дом служит стальная плита, также защищенная от дей ствия высокой температуры слоем жаростойкого бетона.
В подовой плите сделаны отверстия для воздушных |
|
сопел, |
расположенные в шахматном порядке. Снизу |
к поду |
плотно примыкают воздушные коробки (см. |
рис. 74).
Если на под с воздушными соплами загрузить мелкую шихту, а снизу через воздушную коробку подать сжатый воздух, шихта придет в состояние, называемое псевдо ожижением. Частицы ее будут подниматься струйками воздуха на некоторую высоту, а затем падать. Такой слой шихты называют псевдоожиженным: он способен пере текать с высшего уровня на низший, подобно жид кости.
По внешнему виду псевдоожиженный слой похож на кипящую жидкость, поэтому его называют также кипя щим слоем. В кипящем слое каждая „частица окружена потоками воздуха, поэтому обжиг сульфидов протека ет быстро. Чтобы поддержать температуру на нужном уровне, приходится отводить тепло. Для этого -в зоне кипящего слоя устанавливают водяные холодильники.
Шихту в печь загружают непрерывно через загру зочную воронку, а в противоположном конце печи ога рок «стекает» в желоб. Степень десульфуризации зави сит от времени пребывания материала в печи — от ско рости загрузки. До 60—70% всей шихты уносится газа ми в виде пыли, которую улавливают и вместе с огарком направляют на плавку.
Расчет выхода и состава огарка
Методика этого расчета не зависит от способа обжи га и конструкции применяемой печи. Исходя из требуе мой степени десульфуризации, вычисляют количество выгорающей серы. Остаток серы распределяют между медью, цинком, свинцом и железом в порядке убывания сродства металлов к сере. Полученный таким образом вещественный состав несколько отличается от действие тельного, однако он приблизительно правильно отража ет последующее поведение огарка при плавке.
Для примера рассчитаем выход.огарка при десульфу ризации 65% из концентрата следующего состава, %: 14 Си; 32 Fe; 38 S; 4 Si02; ICaO; 4Zn; 6 прочих; 3 влаги.
Сначала выразим содержания элементов, участвую щих в реакциях обжига, в килограмм-атомах (кг-атом) на 100 кг концентрата. Разделив соответствующие про центы на атомные массы, получим количества килог рамм-атомов в 100 кг концентрата:
Си |
Fc |
S |
Zn |
0,22 |
0,57 |
1,19 |
0,03 |
После обжига останется серы
1,19— 1,19-0,65 = 0,42 кг-атом.
Сера в огарке будет связана в C112S — 0,11, в ZnS — 0,03, т. е. 0,11+0,03=0,14 кг-атом.
На образование FeS остается 0,42—0,14 = 0,28 кг-атом серы. Получится FeS 0,28 кмоль.
Железа в виде окислов будет 0,57 — 0,28 = 0,29 кг-атом.
Допустим, что вследствие малого избытка воздуха все железо связано в РезС>4, количество которого составит
|
|
0,29 |
„ , |
кмоль. |
|
|
|
|
|
|
—1— ^ 0 ,1 |
|
|
|
|||
|
|
3 |
|
|
|
|
|
|
Вещественный состав огарка: |
|
|
|
|
||||
|
Cu2S |
ZnS |
FeS |
Fe,04 |
SiO:; |
CaO |
Прочих |
Всего |
кмоль |
0,11 |
0,03 |
0,28 |
0 , 1 |
— |
— |
— |
— |
кг . |
17,6 |
0,3 |
24,6 |
23,2 |
4 |
1 |
6 |
76,7 |
Для получения элементарного состава огарка надо содержания элементов и окислов отнести к выходу огар
ка (содержание серы умножить на 0,35), тогда получим, %: 18,3 Си; 41,8 Fe; 17,3 S; 2,6 Zn; 5,2 Si02; 1,3 CaO; 13,5 прочих К
Пылеулавливание и очистка газов
Пыль, выносимая газами из обжиговых печей, состоит из мелких частиц шихты и летучих окислов, которые сконденсировались из газов при их охлаждении. С пылью
Рис. 28. Осадительные камеры для улавливания крупной пыли
уносится до 10% Си, представляющей большую цен ность, поэтому ее необходимо уловить и возвратить в производство. Кроме того, обжиговые газы направля ются на производство серной кислоты, аппаратура кото рого чувствительна даже к малой запыленности. Особен но недопустимо присутствие в газах мышьяка, отравля ющего катализаторы сернокислотного производства. Следовательно, помимо улавливания пыли, требуется и тщательная очистка от нее обжиговых газов.
Грубую пыль улавливают в осадительных камерах и циклонах, часть ее оседает в газоходах на пути к пыле уловителям. Для выпуска пыли газоходы снабжены бун керами и люками.
Осадительные камеры делают разной формы, но все они являются местным расширением газохода. В этих камерах скорость потока газа резко уменьшается и твер дые частицы выпадают из него под действием силы тя жести. Иногда для лучшего оседания пыли путь газа
вкамере удлиняют, устанавливая перегородки (рис. 28).
Вциклонах (рис. 29) используется центробежная си-1
1 Содержание прочих находится по разности от 100%; сюда же входит кислород Fe30 4.
ла, возникающая при вихревом, спиральном закручива нии потока газа. Газ поступает в циклон со скоростью 15—20 м/сек по касательной и от-этого движется сверху вниз по спиральной траектории. Центробежная сила прижимает пылинки к стенкам циклона, они теряют ско рость и падают в бункер.
Рис. 29. Схемы циклона |
(а) и группового циклона (б): |
/ — центральная |
труба; 2 —• сборник пыли |
Циклоны делают из листовой стали: высота этих ап паратов 3—4 м, диаметр 0,8—2,5 м. В циклонах осажда ется до 90% крупной (крупнее 5 мкм) и 30—40% мелкой пыли (тоньше 3 мкм).
Поперечник наиболее мелких частиц, улавливаемых в циклоне, зависит от диаметра циклона:
®min = £ D .
Постоянная с зависит от свойств пыли и формы цик лона. С уменьшением диаметра эффективность циклона повышается, поэтому делают также групповые (батарей ные) циклоны (см. рис. 29).
Мелкие пылинки — менее 0,5 мкм в поперечнике — не улавливаются в осадительных камерах и циклонах: наиболее тонкие из них способны долго витать даже в не
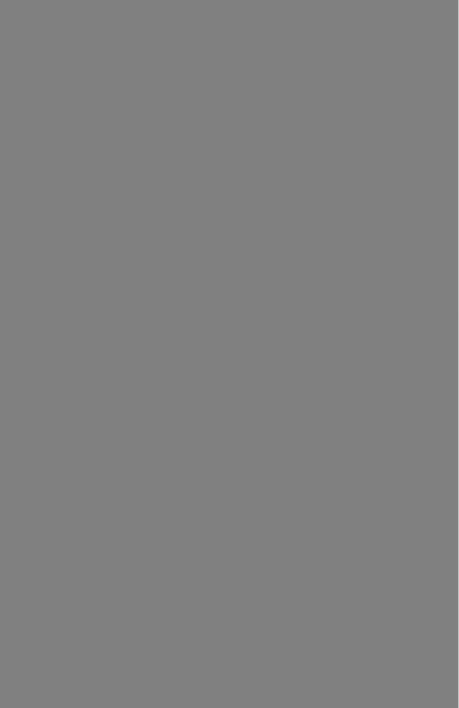
электрическое поле постоянного тока напряжением 50— 80 тыс. в. Газ между электродами ионизируется, поэтому вокруг проволок возникает свечение — «корона».
Встречаясь с ионами, частицы пыли заряжаются од новременно с коронирующим электродом и отталкивают ся от него. Притягиваясь к осадительному электроду, они теряют свой заряд и оседают на электроде. Периодиче скими ударами механических молотков пыль сбрасыва ется в бункер.
Обычные электрофильтры могут работать при темпе ратурах до 450° С и скоростях газа до 1 м/сек с коэффи циентом полезного действия до 98—99% (полнота улав ливания пыли). Схема пластинчатого электрофильтра показана на рис. 30.
Для очистки газов многоподовых обжиговых печей применяют электрофильтры, а для газов печей кипящего слоя — циклоны и электрофильтры. Пыль из газоходов и электрофильтров идет на плавку вместе с огарком.
§ 15. Выплавка штейна из концентратов
Плавка в отражательных печах
У с т р о й с т в о о т р а ж а т е л ь н о й печи
Отражательная печь для плавки медных концентра тов, показанная на рис. 31, имеет длину 35—40 м, шири ну 7—10 м и высоту 3,5—4,5 м. В зависимости от преоб ладания в шихте кислотных или основных окислов для сооружения печей применяют кислые или основные огне упорные материалы. Основные огнеупоры более стойки при основных шлаках, кислые — при кислых. Правиль ный подбор огнеупорных материалов для определенной шихты удлиняет срок службы кладки.
Стены и свод печи делают из динасового или магне зитового кирпича. Динасовые своды делают арочными: кирпичная кладка в виде арки опирается на балки, ле жащие вдоль стен. Такие своды хороши при плавке шихт с высоким содержанием ЭЮг. Для плавки железистых шихт лучше подвесной (рис. 31) или распорно-подвес ной (рис. 32) свод из магнезита или хромомагнезита.
Для образования плотной лещади под печи покрыва ют слоем кварцевого песка, который при прогреве до 1500—1600°С уплотняется благодаря переходу кварца
Рис. 31. Отражательная печь для плавки медных концен тратов:4*21
1 — загрузочные отверстия:
2 — шлаковое окно; 3 — летки
для |
выпуска |
штейна; |
4 — фундамент; |
5 — лещадь: |
|
6 — форсуночные |
окна; |
7 — подвесной свод; 8 — бо ров; 9' — температурные швы
(плотность 2650 кг/м3) в тридимит1 (плотность 2240 кг/м3), оплавлению зерен и шлакованию.
Для крепления печи вдоль стен ее устанавливают по парно двутавровые балки или клепаные колонны с ин тервалом 0,9—4,2 м. Противостоящие пары балок стягивают проходящими над сводом тягами. При разо греве печи гайки тяг постепенно отпускает (рис. 32).
Рис. 32. Распорно-подвесной свод отражательной печи
(по В. II. Смирнову): |
|
|
/ — стены печн; 2 — арочный свод: |
3 — стойки крепления; |
4 — тяга; 5 — подвес |
|
ки свода |
|
Тепловое расширение кладки компенсируется темпе |
||
ратурными швами — |
промежутками |
в кладке (см. |
рис. 31). |
|
|
Отражательные печи отапливают мазутом, угольной пылью или природным газом.
Угольную пыль вдувают в печь горелками, а мазут — форсунками через отверстия в передней торцовой стенке. Обычно горелки или форсунки (4—10 шт.) располагают в один ряд. Воздух для вдувания и распыления топлива подается вентилятором под давлением 1,96 — 2,45 кн/м2 (200—250 мм вод. ст.) — это первичное дутье; дополни
тельное количество вторичного |
воздуха, подогретого |
до 200—250° С, вдувается через |
кольцевое пространство |
горелки и подсасывается в отверстия возле форсунок. Теплотворная способность угольной пыли меньше, чем
мазута: кроме того, уголь имеет сравнительно высокую зольность. Нагревание материалов в отражательных пе чах происходит открытым факелом; зола падает на по верхность расплавленной ванны и может повлиять на со-
1 Кристаллическая модификация S i0 2.