
Механика композитных материалов 2 1980
..pdfПри Et>>Uo получаем: |
|
|
R = - |
(со2 — a2)2tg2 q> |
а = 1(-0)/Ги\ |
4со2а2+ (w2+ a 2)2tg ^ |
||
|
|
(5.3) |
ф= 4 - |
I(t) = {2n[Et- U t(t)]}'l>. |
|
nt п |
fit |
|
Как следует из (5.2), вероятность прохождения импульса через барьер сильно зависит от длительности последнего и от его превышения
над энергией импульса £*. Если при какой-то |
длительности барьера |
D ~ 0,01, то при увеличении длительности в два |
раза D уменьшается в |
100 раз. Такой же результат получился бы при возрастании в четыре раза величины Uo— E t или интенсивности сопротивления волны р. Пре одоление барьера при Et<iUo является туннельным эффектом для мощ ных импульс-поверхностей.
Из (5.3) следует, что если </>* — среднее значение по времени в об ласти барьера потока заторможенности импульса удовлетворяет соот ношению </*> = tinfit/to (п= 1, 2, ...) , то барьер для импульса является полностью прозрачным. Отсюда с учетом (3.7) и равенства 2я/Г = о) по-
Т |
|
лучим ^о = « 2". т. е. на длительности барьера тогда укладывается целое |
|
Число половин периода 1 Ф о р м у л а |
(5.3) дает R и при отражении от |
ямы (Ut(t) < 0). |
Рассмотрим две волны, движу |
6. О структуре мощных импульсов. |
щиеся в направлении е° оси х. Пусть накачка второй волны со стороны
первой имеет вид: |
(6.1) |
Ut= V.e0a(t), |
где V* — характерный объем импульс-поверхности; ео — деформация сжатия второго импульса; a(t) — релаксирующее напряжение растяже ния после прохождения первого импульса с деформацией —ZEQ. Для o(t) примем:
Г —EZeо; т<СТо; т=//,0;
I — EZEOAT? - 1exp ( —(3Tv); то= ^о/0»
где Е — модуль упругости; А, а, р, у — параметры ядра Колтунова [3];
0 = ^ 2/(xp2; p2=V*Eo2Eto; t0 — |
длительность первого импульса; А = |
= та1~°7ехр( — fJTav) ; та=то(1 —а) |
Пусть ео — минимально возможная |
деформация сжатия в импульс-поверхности. Такую импульс-поверхность назовем пресс-элементом. Тогда Z — целое. В случае волн, отталкиваю щихся при сильном сближении, Чг* (0 )= 0 . Отсюда следует, что в (6.2) интервалом малых времен т<До можно в первом приближении прене бречь. При рассмотрении состояния волн при конечном промежутке можно положить 4я/(оо) = 0 . Так как история накачки (6 .1), (6.2) в точке х выбрана так, что она равна нулю при t = оо, то связанным в среднем по времени состояниям волн соответствует отрицательная энергия вто рой волны Et<i 0.
Рассмотрим два частных случая функции (6.2). Во-первых, для экс поненты а = 1 , у=1 и, во-вторых [4], |3 = 0, а ~ 0 . Решение уравнения (3.2) при нулевых условиях для t = 0 и t = оо в первом случае будет иметь вид [5, с. 985]:
4я* = ехр [ - р т ( - ^ + а 2/&2 ) j |
Zv (2 [ ~ |
] exp [ — рх/2]) |
1 9 / 7 2 |
То |
(6.3) |
Zv(0)= 0; |
/ Г 9Z l'/я \ |
|
fl2= —2£*0/р2; v = - + — ; |
Zv[ 2 [ — \ ) = 0, |
где Zv(x) — функция Бесселя. Во втором случае'Ч** будет иметь вг
|
nt |
|
|
|
W< = exp ( —ат)т |
pVTv; т=//0, |
(6 |
||
|
v=0 |
|
|
|
где для величин pv, приближенно |
(при малом а) являющихся постоз |
|||
ными, справедливы рекуррентные соотношения |
|
|
||
|
|
|
l |
|
|
|
|
— l |
|
pv+i = 2 [a (v + 1) —Z(a)] Pv/ (v + 1) (v + 2) ; |
Z(a)= Z (1 — а )а (т/т0)а |
Z. |
||
|
|
|
|
(6 |
Можно показать [2, с. 178], что если ряд |
(6.4) |
не обрывается, то услсн |
||
при ^= оо не удовлетворяется. Поэтому в |
(6.5) |
p,z< = 0 при v = tit —1. |
(6.5) с учетом определения а в (6.3) получается дискретный спектр ис рии энергии E t при а = 0, |3 = 0:
Z2p2 |
Z2\LZQaV*2ЕЧо |
(6 |
2nt2d |
n t = 1, 2, |
|
2nt2nt2 |
|
Величину tit назовем квантовым числом истории энергии. |
С ростом |
(£ *< 0 ) величина энергии волны E t и средний интервал |
времени |
между волнами растут. Поэтому большие щ соответствуют возбужд ным в среднем по времени состояниям волны. Так как в результате кв тования полей появляются частицы [2], то, если волна в точке х облад значением Et, соответствующим большим значениям nt, это значит, до этого она была возбуждена частицами, поведение которых выде лось на фоне движения частиц однородной среды. Если в другой то1 х Et стало меньшим, то это означает, что волна потеряла энергию, воз див некоторые выделившиеся частицы. В этом смысле можно говор о появлении новых частиц. При больших мощностях волн рождение уничтожение частиц является реальным (деструкция, разрушение, с кание, полимеризация). Приведенные примеры говорят о наличии стр туры волн.
По принципу неопределенностей в (6.6) нельзя одновременно то1 знать V* и t0. Поэтому надо пользоваться параметрами р и 0.
СП И С О К Л И Т Е Р А Т У Р Ы
1.Колокольчиков В. В. О распространении импульс-поверхностей в наследствеь
неоднородных средах. — Механика композитных материалов, 1979, № 6 , с. 963— 2. Д авы дов А. С. Квантовая механика. М., 1973. 703 с.
3.Колтунов М. А. Функции влияния в теории оболочек с наследственными свс
вами. — В кн.: Исследования по теории пластин и оболочек, 1967, сб. 5, с. 3 (Казань).
4.Работное Ю. Н. Ползучесть элементов конструкций. М., 1966. 752 с.
5.Градштейн И. С., Рыжик И. М. Таблицы интегралов, сумм, рядов и произ!
ний. М., 1971. 1108 с.
Куйбышевский государственный университет |
Поступило в редакцию 24.. |
УДК 539.4:678.067.5:620.1
Т.Д. Каримбаев, Ю. А. Ножницкий, В. И. Гундаров, Л. С. Рысин,
В.Г Лютцау, И. А. Тарасов
РАЗРУШЕНИЕ И ИЗНОС КОМПОЗИТНЫХ МАТЕРИАЛОВ ПРИ ВЗАИМОДЕЙСТВИИ С ПОТОКОМ АБРАЗИВНЫХ ЧАСТИЦ
Абразивная эрозия является сложным процессом, на который влияют как физико-механические свойства изнашиваемого материала, так и усло вия взаимодействия с потоком абразивных частиц [1—4]. Механизм аб разивной эрозии изучен недостаточно даже для однородных материалов, а известные расчетные методы [1, 5— 11] не позволяют с требуемой точ ностью предсказывать величину эрозионного износа натурных конструк ций без проведения специальных испытаний. Особенности же эрозион ного разрушения и износа конструкционных композитных материалов и находящих все более широкое применение композитных покрытий [12, 13] до настоящего времени почти не были изучены.
В данной работе экспериментально исследовалась абразивная эрозия ряда композитных материалов и покрытий на основе полимеров, угле рода, металлов, армированных стекло-, угле-, боро-, органоволокнами, лентами и тканями из этих волокон, нитевидными кристаллами, части цами, металлическими сетками. Для сопоставления были также испы таны некоторые широко применяемые в машиностроении металлические сплавы (1Х17Н2, ВТ8, Д16Т) и полученные различными методами твер дые керамические (SiC, Si3N4, AI2O3 и др.) и эластичные (на основе кау чука, полиэтилена, пленочных клеев и т. д.) покрытия.
Эрозионные испытания были проведены на специальном газоабразнвном стенде с достаточно длинным (1,7 м) участком для разгона частиц воздушным потоком. Уста новки такого типа [4, 10] по сравнению с распространенными струйными [14], центро бежными [15] и гравитационными [15] ускорителями частиц обладают более широкими возможностями для регулирования основных параметров потока, оказывающих влияние на процесс абразивной эрозии, и контроля за этими параметрами. Кроме того, конструк ция установки обеспечивает равномерный износ при заданном угле атаки всей рабочей поверхности образца, что позволяет использовать результаты лабораторных испытаний для оценки износа натурных конструкций. В качестве абразива использовались получен
ные помолом частицы кварцевого песка размером до 40 мкм (основная |
фракция |
15—20 мкм, удельная поверхность 286 м2/кг, твердость HV 1200 кгс/м2, |
плотность |
р= 2650 кг/м3). Для анализа влияния на эрозионный износ размеров, формы и свойств
материала абразивных частиц использовались также |
корунд (р = 4000 кг/м3, |
HV 2100 кгс/мм2, фракции с dr= 40 мкм, 50—70, 80— 100 мкм) |
и природная (подмосков |
ная дорожная) |
пыль (40—70 и 80— 100 мкм). |
Испытания проводились при концентра |
ции абразива в воздушном потоке около 1 0 _ 3 |
кг/м3, скорости потока на выходе из раз |
|
гонной трубы |
2 0 0 мус, близких к атмосферным условиям давлении и температуре. |
Износ образцов определяли по результатам их взвешивания до и после обдувки или по измерениям их линейных размеров с помощью микроскопа (по микрошлифам). Срав нительную оценку износа материалов проводили по коэффициенту е (м/кгс/м2) — отно шению изменения толщины образца в результате обдува к среднему расходу абразива, прошедшему за испытание через единичную площадку, перпендикулярную направлению потока. Для материалов, износостойкость которых изменяется в процессе обдувки, экс периментальное значение е является усредненным и характеризует унос материала при определенном расходе абразива. Продолжительность работы (Т, с) до допустимого
износа (h, м) в потоке с известной удельной запыленностью |
(К, кгс/м2 •с) определяется |
h |
соответствующих условиям |
по соотношению Т = —— , где е находится из испытаний, |
|
ел |
|
эксплуатации.
Характер разрушения материалов при абразивной эрозии исследовали с помощью светового, рентгеновского (МИР-2) и сканирующего электронного (Stereoskan S4) мик роскопов. Для идентификации продуктов износа и шаржировавших в изнашиваемую поверхность абразивных частиц использовали микроанализ.
Эрозионный износ материала увеличивается при повышении абсорби руемой им доли энергии абразивных частиц, а также при уменьшении удельной энергии изнашивания (энергии, необходимой для удаления единицы объема). В условиях испытаний износ металлических сплавов максимален при углах атаки а = 45—65° (рис. 1). Это можно объяснить тем, что теряемая при соударении с образцом из металлического сплава доля кинетической энергии абразивных частиц возрастает при увеличе нии угла атаки, а удельная энергия изнашивания этих материалов меньше при малых а, когда износ в основном обусловлен резанием — удалением массы изнашиваемого материала при единичном взаимодейст вии с абразивом [16]. При нормальных к изнашиваемой поверхности и близких к нормальным ударах удаление материала происходит после ряда циклов нагружения.
При повышении твердости изнашиваемого материала он поглощает меньшую долю кинетической энергии частицы [17]. Однако сопровождаю щее повышение твердости материала охрупчивание его приводит, осо бенно при высоких скоростях удара и больших углах атаки, к увеличе нию размеров продуктов хрупкого износа, что и наблюдалось при испы таниях керамических покрытий.
Эластичные покрытия, как правило, работоспособны при достаточно большой толщине и больших углах атаки. В этих условиях они легко «принимают» и легко «отдают» абразивные частицы, не погло щая энергии. Однако при высокой скорости удара эти покрытия те
ряют свою эластичность [7].
Рис. 1. Износ некоторых материалов при обдуве кварцевым песком (а) и корун дом (б, dr= 80— 100 мкм): 1 — 1Х17Н2; 2 — ВТ8 ; 3 — Д16Т;4—7'— боропластик ( 1/ о = 61 %) при обдуве в направлении ук
ладки армирующих элементов (4) и под углами 45° (5), 60° (6), 90° (7); 8—11 — различные композитные материалы при обдуве в направлении армирования (5 — углеалюмнннй, Ун = 60%, 9 ■— стекло пластики на различных связующих, 10 — углепластик, 11 — углерод-углерод).
При разработке методики рас чета эрозионного износа в [1, 6] на основе анализа ряда экспери ментов с резинами и пластмас сами было высказано предполо жение, что абразивные частицы обычно не шаржируют в изнаши ваемый материал. В данных экс периментах также не наблюда лось шаржирования частиц в образцы из стали 1Х17Н2, твер дые керамические покрытия, ком позиционные электрохимические покрытия (КЭП) с никелевой связкой, а также в бороволокна. В то же время частицы интен сивно шаржировали в поверх ность образцов из менее твердых материалов, причем количество шаржировавших частиц увеличи валось при уменьшении отноше ния твердости изнашиваемого
материала к твердости абразива. Шаржирование частиц в образцы из легких эластичных материалов при малых удельных расходах пыли вызывало привес этих образцов. Шаржировавшие абразивные частицы, обладая более высокой по сравнению с изнашиваемым материалом твер достью, могут, вообще говоря, способствовать повышению его износо стойкости [18]. Однако, одновременно являясь концентраторами напря жений, они способствуют хрупкому разрушению материала и снижают его прочность при переменных нагрузках, что и наблюдалось в испыта ниях. При увеличении удельного расхода абразивных частиц интенсив ность изнашивания этих покрытий резко возрастала. Разрушение их при упругом контакте с абразивными частицами происходило путем среза при малых и отрыва при больших углах атаки.
Проведенные исследования показали, что армированные пластмассы (стекло-, угле-, органо-, боропластики), углерод-углеродные материалы (карбонизованный углепластик), углеалюминий, армированные борными волокнами материалы на алюминиевой и магниевой матрицах значи тельно, особенно при больших углах атаки, уступают по стойкости к аб разивной эрозии испытанным металлическим сплавам (см. рис. 1). Так, например, при обдуве молотым кварцевым песком и а = 70° износостой кость бороалюминия примерно в 1,5, углеалюминия в 5, органопластика в 7, угле- и стеклопластиков более чем в 25, а карбонизованного угле пластика в 150 раз ниже, чем у сплава ВТ8. Износ армированных пласт масс и карбонизованных углепластиков максимален при углах атаки, близких к 90°.
Как показали испытания, износостойкость композитных материалов в большей степени, чем эрозионная стойкость металлических сплавов, за висит от кинетической энергии и твердости абразивных частиц. Так, при использовании в качестве абразива вместо кварцевого песка корунда с частицами, близкими по форме частицам кварцевого песка, но более крупными по размерам (80— 100 мкм) и более твердыми, износ металли ческих сплавов при угле атаки 70° повысился в 2,3—2,7 раза, стекло пластика на эпоксифенольном связующем — в 7, а боропластика при объемном содержании наполнителя 80% — более чем в 40 раз. Износ материалов природной пылью несколько ниже, чем частицами того же размера, полученными помолом и имеющими более острые грани, однако инверсий в ряду относительной износостойкости не наблюдалось.
Взаимодействие с запыленным потоком материалов на основе поли меров или углерода, армированных не стойкими к удару волокнами, со провождается интенсивным шаржированием абразивных частиц (рис. 2—а), пробивающих армирующие слои (рис. 2—б). Это объясняет причину низкой износостойкости таких материалов, так как при шаржи ровании абразивных частиц на деформирование и разрушение материала расходуется значительно большая часть их кинетической энергии, чем при отскоке. Вследствие низкой межслоевой прочности этих материалов трещины в дальнейшем распространяются между слоями, обусловливая износ путем послойного скалывания (рис. 2—г). При таком характере разрушения стойкость материала к абразивной эрозии практически не зависит от ориентации армирующих элементов в плоскости слоя, оказы вающей существенное влияние на его основные физико-механические свойства.
Если компоненты материала отличаются по эрозионной прочности, то при взаимодействии с потоком абразивных частиц происходят преиму щественные разрушения и износ менее стойкой к абразивной эрозии со ставляющей. В частности, в армированных борными волокнами мате риалах на полимерной, алюминиевой, магниевой матрице при обдуве кварцевым песком в первую очередь изнашивается связка (рис. 3—а, 4—а ) , в углеалюминии — наполнитель (рис. 3—б, 5—а, б ) .
В этих случаях износостойкость армированного волокнами материала повышается при увеличении содержания в изнашиваемом слое более стойкого к эрозии компонента. Например, при обдуве молотым кварце вым песком боропластиков в направлении армирования коэффициент
эрозии составляет при объемном содержании |
наполнителя |
Ув = 80% |
||
0,111 •10—6 м/кгс/м2 (угол атаки а = 20°) |
и 0,303-10~6 |
м/кгс/м2 |
(а = 70°), |
|
при VB = 61%1 соответственно 0,17 - 10-6 |
и 0,41 |
- 10-6 |
м/кгс/м2, а при |
ув= 43% — 0,288 •10-6 и 0,896 •10—6 м/кгс/м2. Ориентация армирующих элементов в плоскости слоя и в этом случае относительно слабо сказы вается на износостойкости материала (см., например, результаты испы таний боропластиков — рис. 1—а). Так, при обдуве в направлении, пер пендикулярном ориентации армирующих элементов, износ менее стойкой к эрозии компоненты ниже, чем при обдуве в направлении армирования. Однако в этом случае становятся наименее благоприятными условия из нашивания бороволокон, а в углеалюминии облегчается разрушение об разующихся на поверхности алюминиевых гребешков (см. рис. 5—а, б). Таким образом, износ менее стойкой к абразивной эрозии компоненты может ухудшить условия износа второй составляющей.
Испытания показали, что абразивная эрозия армированных части цами А1г03 (размером 5 мкм) или TiC (2—3 мкм) КЭП на никелевой матрице обусловлена разрушением связки, после износа которой проис ходит унос армирующих частиц (см. рис. 3—в). Таким же был механизм износа армированных нитевидными кристаллами SiC покрытий на поли мерной или алюминиевой матрице. При увеличении размеров упрочняю щих элементов происходит не только их выкрашивание из связки, но и разрушение. Избирательный характер эрозионного износа ранее был от мечен при испытаниях спеченных твердых сплавов [19—21] и армирован ных частицами огнеупорных обмазок [22].
Таким образом, износостойкость армированных частицами материа лов существенно зависит от свойств связующего, и армирование не стой ких к эрозии матриц недостаточно эффективно. Износостойкость этих материалов повышается при увеличении содержания наполнителя. Од нако, как отмечено в [23], предельное упрочнение матрицы приводит ее в состояние весьма малой пластичности и способствует хрупкому разру шению. В этом случае армированный частицами материал будет обла дать наибольшей износостойкостью при оптимальном содержании упроч няющей фазы [19, 24].
Механизм разрушения и износа компонентов композитного материала в одних и тех же условиях может быть различен. Изменение условий взаимодействия с абразивом также по-разному сказывается на их изно состойкости.
Армирующие волокна, как и полимерные и углеродная матрицы, раз рушаются хрупко. Пробой углеродных жгутов (см. рис. 2—б, 5—в) вы зывает унос крупных, до 100 мкм, осколков моноволокон (рис. 2—в, 5— д, е). Бороволокна при обдуве кварцевым песком значительно превос ходят по прочности стекло-, угле- и органические наполнители и обла дают относительно высокой эрозионной стойкостью. В этом случае износ бороволокон незначителен и происходит путем откола небольших фраг ментов (рис. 3—а). При обдуве в направлении армирования поверхность волокна, имеющая первоначально форму «кукурузного початка», сгла живается, приближаясь к цилиндрической. При соударении с более круп ными (80— 100 мкм) и более твердыми частицами корунда волокна бора также начинают интенсивно разрушаться; имеются случаи пробоя воло кон и их продольного растрескивания.
Разрушение в тех же условиях металлических матриц и металличе ских сеток, как и неармированных металлических сплавов, обусловлено
Ь основном микрорезанием при малых углах атаки и малоцикловой уста лостью при пластическом деформировании (рис. 4—б, г; 5—в).
Взаимодействие с потоком абразивных частиц сопровождается ло кальными перегревами материала мишени. Об этом в частности свиде тельствует интенсивное сгорание продуктов износа при испытании образ цов из обладающих относительно низкой теплопроводностью титановых сплавов. На рис. 4—в хорошо заметно оплавление микрообъемов маг ниевой матрицы материала магний—бор при обдуве молотым кварце вым песком. Для оплавления одного такого микрообъема достаточно 3% кинетической энергии частицы основной фракции (20 мкм) при скорости ее 200 м/с. Микроанализ показал, что часть расплавленного металла при липает к абразивным частицам.
Таким образом, подтверждается высказанное в [9] предположение о том, что возможен унос части материала за счет разбрызгивания рас плава или вследствие его прилипания к отскакивающим, либо удаляе мым при последующих ударах частицам. По-видимому, локальные пере гревы при соударении с частицами могут оказывать влияние и на про цесс разрушения полимерных материалов, способствуя снижению их эластичности и деструкции.
Из изложенного следует, что проведенные исследования позволили выявить некоторые особенности эрозионного разрушения композитных материалов. В частности, показано, что армированную волокнами композицию при взаимодействии с потоком частиц нельзя рассматривать как однородный материал, как это было сделано в работах [25, 26].
Относительно низкая эрозионная стойкость испытанных композитных материалов обусловлена низкой износостойкостью связки, а также хруп костью армирующих элементов и низкой межслоевой прочностью. При использовании не стойких к абразивной эрозии связующих не удается су щественно повысить износостойкость материала изменением ориентации или типа армирующих элементов. Так, например, замена углепластика поливолокнистым материалом-стеклоуглепластиком или органоуглеплас тиком, обладающим более высокой ударной вязкостью [27], позволяет существенно повысить их стойкость к удару крупным предметом, но, как показали наши исследования, не обеспечивает требуемой стойкости к аб разивной эрозии. Для повышения эрозионной стойкости деталей из композитных материалов более эффективным представляется использо вание полиматричных материалов [28] или специальных защитных по крытий [28, 29].
СП И С О К Л И Т Е Р А Т У Р Ы
1.Крагельский И. В ., Добычин М. Н., Комбалов В. С. Основы расчетов на трение
иизнос. М., 1977. 526 с.
2.Уэтц Г. Наиболее важные результаты исследований абразивной эрозии, прове
денных в Штутгартском университете. — Тр. Таллин, политехи, ин-та. Сер. А, 1973,
вып. 347, с. 3— 21.
3.Клейс И. Р. О проблемах по определению эрозионного износа при соударении
спотоком твердых частиц. — В кн.: Теория трения, износа и проблемы стандартиза
ции. Брянск. 1978, с. 219—230.
4. Бирюков В. И., Виноградов В. Н., Мартиросян М. М., Михайлычев В. Н. Абра
зивное изнашивание газопромыслового оборудования. М., 1977. 207 с.
5. Черепанов Г |
П. Механика хрупкого разрушения. М., 1974. 640 с. |
6 . Стыллер Е. |
Е ., Ратнер С. Б. Износ косым потоком твердых частиц. — Тр. |
ВНИИПТУглемаш (Всесоюз. науч.-исслед. и проект.-технол. ин-т угольн. машинострое
ния), 1975, вып. 20, с. 32—53 |
(М.). |
с. 62— 108. |
|
7. |
Пенкин Н. С. Гуммированные детали машин. М., 1977, |
||
8 . |
Ш елдон. Сходство и |
различия в эрозионном поведении |
материалов. — Теорет. |
основы инж. расчетов, 1970, N° 3, с. 208—214.
9. Смелтзер, Гулден, Комптон. Механизмы эрозии металлов при ударном воздейст
вии частиц пыли. — Теорет. основы инж. расчетов, 1970, № 3, с. 225—238.
10. Grant G., Tabakoff W. Erosion prediction in turborflachinery due to ertvironme solid particles. — AIAA Pap., 1974, N 16, 16 p.
11. Jennings W. H„ H ead W. |
/., Manning |
C. |
R. A mechanistic model for the p |
diction of ductile erosion. — Wear, |
1976, vol. 40, |
N |
1, p. 93— 112. |
12.Сайфуллин P. С. Композиционные электрохимические покрытия и материа, М., 1977. 270 с.
13.Гуняев Г. М., Сорина Т. Г., Владимирский В. Н., Куприянова Р. М. Эрозион стойкие покрытия на основе нитевидных кристаллов. — В кн.: Авиационные материа. 1977, вып. 2, с. 40—45 (М.).
14.Антонов А. А. Методика и некоторые результаты испытаний на износ стале! чугуна воздушно-абразивной струей. — Тр. Московск. ин-та нефтехим. и газо] пром-сти, 1961, вып. 20, с. 79—95.
15.Клейс И. Р., Ууэмыйс X. X. Новые механические установки для исследова! "абразивной эрозии. — Вести, машиностроения, 1971, № 9, с. 13— 15.
16.Клейс И. Р., Паппель Т. А. Исследование энергобаланса удара абразив! струей. — В кн.: Износ материалов при ударном воздействии твердых частиц. М., 1S
с.11— 12.
17. |
Uetz Н., Fohl J. Wear as an energy transformation process. — Wear, |
19 |
||
vol. 49, N 2, p. 253—264. |
|
|
||
18. |
Кащ еев В. H. Закономерности абразивного изнашивания металлов и сплавов. |
|||
В кн.: |
Теория |
трения, износа и |
проблемы стандартизации. Брянск, 1978, с. 181— 1 |
|
19. |
К абрал |
X. И., М озберг Р. |
К О характере разрушения твердых сплавов при |
|
разивной эрозии. — Тр. Таллин, |
политехи, ин-та. Сер. А, 1970, вып. 294, с. |
17— |
20. Ууэмыйс X., Клейс И., Туманов В., Тийдиман Т. Исследование абразивной э зии спеченных вольфрамовых твердых сплавов. — Порошковая металлургия, 1974, JST с. 98— 101.
21. Вальдм а Л. Э., Кудрявцев В. А., Каллас П. К. Влияние структуры и механи ских свойств твердых сплавов TiC—Ni—Со—Сг на гидроабразивный износ. — В i Износ материалов при ударном воздействии твердых частиц. М., 1976, с. 46—48.
22.Видерхорн, Фуллерма, Буковский, Роббинс. Влияние гидротермических сред эрозию огнеупорных обмазок. — Теорет. основы инж. расчетов, 1977, № 2, с. 48—
23.Самсонов Г В., Данькин А. А., Марков А. А., Богомол И. В. Прочность и гг абразивная износостойкость керметов на основе карбита титана. — Машиноведе] 1978, № 1, с. 88—93.
24.П огодаев Л. И., Н екоз А. И., Овчаренко В. В. Износостойкость двухфаз] материалов при ударном воздействии твердых частиц и кавитационном изнашивании
Вкн.: Проблемы трения и изнашивания, 1975, вып. 8, с. 18—21 (Киев).
25.Спрингер, Янг. Модель дождевой эрозии композиционных материалов, арм!
ванных |
волокнами. |
— Ракет, техника и космонавтика, |
1973, т. 13, № |
7, |
с. 4 5 - |
26. |
Greszczuk |
L. В. Response of isotropic and composite materials to pari |
|||
impact. — In: ASTM STP 568, 1975, D. 183—214. |
Н., Машинская |
Г. |
П., I |
||
27. |
Гуняев Г |
M., Румянцев А. Ф., Ф едькова Н. |
дина Н. П., Степанычев Е. И., Махмутов И. М. Поливолокнистые композиционные териалы. ■— В кн.: Авиационные материалы, 1977, вып. 2, с. 40—45 (М.).
28. Гундаров В. И., Каримбаев Т. Д., Ножницкий IO. А., Рысин Л. С. Эксперт тальное исследование эрозионной стойкости композиционных материалов и эффен
ности |
некоторых |
способов защиты деталей из этих материалов от эрозионного |
носа. |
— В кн.: |
Износ материалов при ударном воздействии твердых частиц. |
1976, |
с. 76. |
|
29. Хасуй А. Техника напыления. М., 1975. 289 с. |
||
М осква |
Поступило в редакцию 02.С |

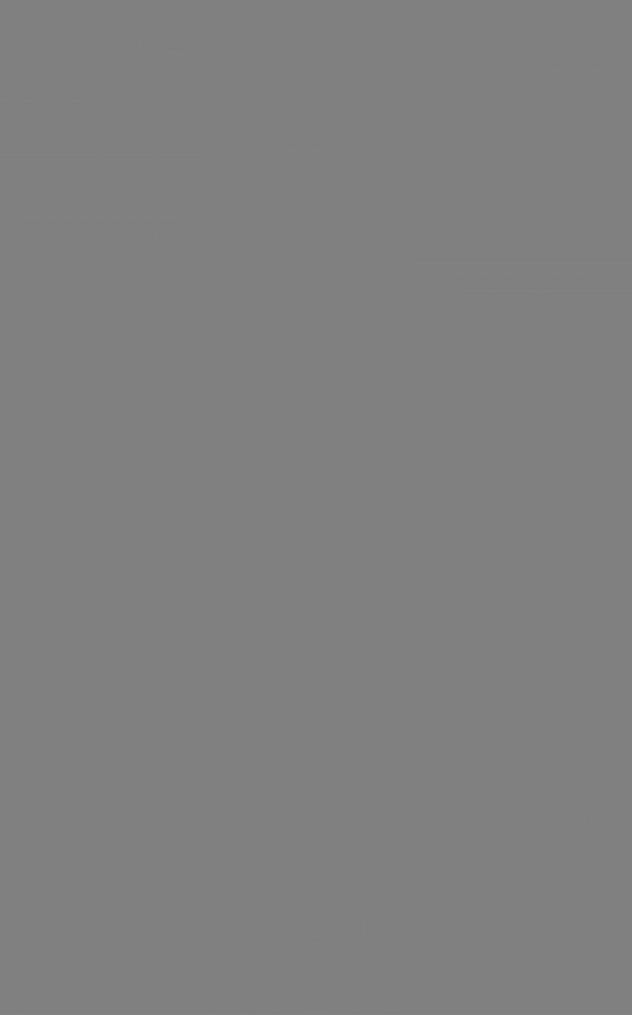