
Технология органического и нефтехимического синтеза
..pdf
МСО + МН → МСН2ОМ; |
(9.9) |
МСН2ОН + МН → МСН2ОН + 2М; |
(9.10) |
(I) |
|
МСН2ОН + МН → СН3ОН + 2М; |
(9.11) |
МСНО + МН → СН2О + 2М; |
(9.12) |
СН2О + МН → CH3OM; |
(9.13) |
(II) |
|
СН3ОМ + МН → СН3ОН + 2М |
(9.14) |
Справедливость этих схем подтверждалась многочисленными прямыми и косвенными факторами.
Исследования механизма синтеза метанола, проведенные в нашей стране в 1970–80-х гг., показали, что на оксидных катализаторах, в частности на медьсодержащих, возможно образование метанола также из диоксида углерода, присутствующего в исходной смеси или образующегося по реакции конверсии оксида углерода водой:
СО + Н2О ↔ СО2 + Н2; |
(9.15) |
СО2 + 3Н2 ↔ СН3ОН + Н2О |
(9.16) |
Главными особенностями данной схемы являются окислитель- но-восстановительный характер синтеза метанола и его цикличность.
Полагают, что образование метанола может происходить через стадию образования карбонатных и формиатных комплексов на поверхности медьсодержащего катализатора, обнаруженных спектральными методами:
(9.17)
Карбонатные комплексы при гидрировании превращаются в метанол и формиатные комплексы. Формиатные комплексы склонны к распаду и гидрированию в метанол.
201
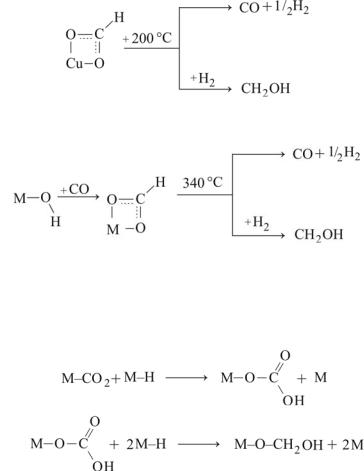
1. Формиаты, адсорбированные на атомах Сu:
(9.18)
2. Формиаты, адсорбированные на атомах Zn и Аl с участием ОН-группы:
(9.19)
Схему механизма превращения СО2 в СН3ОН с участием Н2 на катализаторе Cu–ZnO/Al2О3 можно представить следующим образом:
СО2 + М ↔ М–СО2; |
(9.20) |
Н2 + 2М ↔ 2М–Н; |
(9.21) |
|
(9.22) |
|
(9.23) |
M–O–CH2OH + M–H → CH3OH + M–O–M |
(9.24) |
На поверхности катализатора формиаты находятся в монодентатной и бидентатной формах, а реакция образования метанола протекает через лимитирующую стадию гидрирования формиата на меди.
Образование формиатов, возможно, также происходит по реакциям с участием оксида углерода:
202

М + СО ↔ М–СО; |
(9.25) |
|
(9.26) |
Формиатные комплексы, по-видимому, могут образовываться с различными скоростями из смеси СО2 + Н2 и СО + Н2. Возможно, этими различиями и объясняются разные скорости синтеза СН3ОН из этих смесей на разных катализаторах и в разных условиях.
Возможны и другие схемы механизма образования метанола, так как на поверхности катализатора были обнаружены группы Cu–Н, Сu–ОН, Сu–СО, Сu–СНО. Дальнейшие исследования, по-видимому, дадут однозначный ответ на вопрос о механизме образования метанола из синтез-газа.
9.2. ОСНОВНЫЕ ЗАКОНОМЕРНОСТИ ПРОЦЕССА
Влияние температуры и давления. Цинкхромовые катализаторы работают при температуре 330–400 °С и давлении 20–40 МПа; мед- но-цинковые – при температуре 220–270 °С и давлении 5–10 МПа.
Выбор рабочего давления в указанных диапазонах определяется кроме температуры составом синтез-газа, заданной производительностью и скоростью побочных реакций (в частности, метанообразования); выбор температуры – активностью катализатора и конструкцией реактора.
Влияние объемной скорости синтез-газа. С увеличением объемной скорости синтез-газа, особенно в интервале 10 000–40 000 ч–1, выход метанола и производительность катализатора сначала растут, а затем проходят через максимум.
Влияние рециркуляции газа. Степень превращения синтез-газа за проход через реактор составляет 15–50 %, что определяется положением равновесия реакции образования метанола в выбранных условиях синтеза, продолжительностью контакта и допустимым перепадом температуры по слою катализатора при адиабатическом
203
режиме процесса. Поэтому все промышленные установки работают с рециркуляцией газа после отделения от него воды и метанола. Для определения коэффициента рециркуляции предложена формула
UG UE |
1 Ф |
|
|
, |
(9.27) |
||
|
|
Са |
|
||||
|
|
|
|||||
|
1 Ф 1 |
|
|
|
|||
|
|
|
С |
|
|
|
|
|
|
0 |
|
|
где UG – общая степень превращения СО; UE – степень превращения СО за проход; Ф – коэффициент рециркуляции;
С0 – концентрация СО во входящем газе, мол. %; Са – концентрация СО в отходящем газе после конденсации воды
и метанола, мол. %.
Рециркуляция позволяет регулировать тепловой режим реактора и состав синтез-газа.
Состав синтез-газа. В процессах высокого давления используют синтез-газ, обогащенный водородом (Н2 : СО= (10–12) : 1). Отимальный состав синтез-газа для процессов низкого давленияН2 : СО≈ 3,5 : 1.
Избыток водорода по отношению к стехиометрическому позволяет повысить скорость реакции, улучшить качество метанола-сырца и ограничить содержание инертных компонентов.
Концентрация СО в синтез-газе составляет 5–25 об. %. Это объясняется тем, что с повышением концентрации СО увеличивается тепловыделение. Содержание СО2 поддерживается в пределах
2–5 об. %.
В промышленности применяется следующий оптимальный режим синтеза метанола на цинкхромовом катализаторе [(2,5–3,3) ZnO × × ZnCr2О4]: температура 360–380 °С, давление 30 МПа, объемное соотношение Н2 : СО = 6, объемная скорость газа (35–40) · 103 ч–1; на низкотемпературных медьсодержащих катализаторах (СuО– 52–54; ZnO – 24–28; А12О3 – 5–6 мас. %) температура 260–280 °С, давление
5–10 МПа, объемная скорость газа (5–35) · 103 ч–1, объемное соотно-
шение (Н2 + СО2) : (СО + СО2) = 0,5–5,0.
204
9.3. ТЕХНОЛОГИЧЕСКИЕ СХЕМЫ ПРОЦЕССА
Промышленные установки синтеза метанола представляют собой крупные агрегаты мощностью 600–900 т/сут. Строятся установки мощностью 1500–2000 т/сут с использованием энерготехнологического принципа максимально возможного использования теплоты химической реакции.
Основным аппаратом блока синтеза является реактор, обычно полочного или трубчатого типа. Подробно реакторы и другая аппаратура установок синтеза метанола описаны в работе 7 .
Принципиальная энерготехнологическая схема агрегата синтеза метанола мощностью 900 т/сут показана на рис. 9.1.
Природный газ под давлением 1,2 МПа разделяется на два потока. Первый поток смешивают с продувочными газами синтеза метанола в отношении 8 : 1 и через сепаратор и компрессор направляют в огневой подогреватель и далее в блок очистки от сернистых соединений. Очищенный газ (содержание соединений серы менее 0,5 мг/м3) смешивают с СО2 в соотношении СО2 : СН4 = 0,3–0,35 и с водяным паром в соотношении Н2О : СН4 = 3,0–3,5 и через подогреватель направляют в конвертер. Влажный конвертированный газ поступает в котел-ути- лизатор, где охлаждается до 280 °С, проходит последовательно подогреватели воды, охлаждается и отделяется от конденсата, дожимается компрессором до 5,5 МПа, смешивается с циркуляционным газом и через теплообменник и огневой подогреватель направляется в реактор синтеза метанола. Продукты синтеза через теплообменник и воздушный холодильник поступают в сепаратор метанола-сырца. Газ направляют на циркуляцию, а метанол-сырец на дистилляцию.
На рис. 9.2 представлены три типа реакторов синтеза метанола при пониженном давлении (5–10 МПа), различающиеся способами расположения катализатора и охлаждения.
В реакторе с закалочными устройствами используется конструкция с несколькими слоями катализатора. Предварительно нагретая смесь рециркулируемого и свежего газа (СО + Н2) подается в различные слои катализатора, разделенные закалочными устройствами для предотвращения перегревов. В большинстве случаев после
205

реактора стоит котел-утилизатор, в котором используется основное количество теплоты реакций.
Рис. 9.1. Принципиальная технологическая схема агрегата синтеза метанола мощностью 900 т/сут: 1 – сепаратор; 2 – паровая турбина; 3 – турбокомпрессор природного газа; 4 – огневые подогреватели; 5 – реактор сероочистки; 6 – адсорбер; 7 – паровые турбины; 8 – компрессор СО2; 9 – дымовая труба; 10 – паросборник; 11 – трубчатая печь; 12 – котел-утилизатор; 13 – подогреватель; 14 – экономайзер; 15 – установка деаэрации; 16 – водоподготовка; 17 – воздушный конденсатор; 18 – сепаратор синтез-газа; 19 – сепаратор; 20 – воздушный холодильник колонны синтеза; 21 – колонна синтеза метанола. Потоки: I – природный газ; II – продувочный газ синтеза; III – СО2; IV – пар, 4 МПа; V – пар, 0,4 МПа; VI – пар, 10,4 МПа; VII – вода; VIII – конвертированный газ на синтез;
IX – метанол-сырец
206

207
Втрубчатом реакторе (см. рис. 9.2, б) катализатор, находящийся в трубках, охлаждается водой, поступающей в межтрубное пространство.
Воднослойном реакторе с радиальным потоком (см. рис. 9.2, в) катализатор расположен в виде вертикального кольцевого слоя. Радиальный поток газов, создаваемый в реакторе, обеспечивает незначительное падение давления и позволяет экономить энергию при работе компрессора рециркуляции.
Производство метанола в мире в начале XXI в. составило около 30 млн т в год.
Основной областью применения метанола является получение формальдегида (свыше 40 %). Метанол также используется в синтезе уксусной кислоты, сложных эфиров (в частности, диметилфталата), простых эфиров (МТБЭ, МТАЭ и др.), метилгалогенидов, аминов, ионообменных смол, в качестве растворителя, экстрагента и добавки
кмоторным бензинам. В дополнение к традиционным областям потребления значительными могут стать в будущем потребности в метаноле в новых областях, таких как энергетика, синтез белка, продуцируемого одноклеточными организмами.
208
Глава 10 РАЗРАБОТКА МАЛОСТАДИЙНОЙ ТЕХНОЛОГИИ
ПЕРЕРАБОТКИ ПРИРОДНОГО ГАЗА В СИНТЕТИЧЕСКИЕ ДИЗЕЛЬНЫЕ И РЕАКТИВНЫЕ
ТОПЛИВА НА МАЛОГАБАРИТНЫХ УСТАНОВКАХ НИЗКОГО ДАВЛЕНИЯ
10.1.ЦЕЛЬ РАЗРАБОТКИ И ОСНОВАНИЕ ТРЕБОВАНИЙ
КТЕХНОЛОГИИ. ОБЗОР ПРОБЛЕМЫ
Как показывает анализ состояния топливно-энергетического комплекса России, проблема получения моторных топлив из природного газа и из других источников газообразного углеводородного сырья (как альтернатива падающей и дорожающей нефтедобыче) должна рассматриваться в качестве локальной со сравнительно небольшими единичными масштабами соответствующих производств. Это позволит при ограниченных капиталовложениях, которые под силу потенциальным потребителям, за относительно короткие сроки решить проблему автономного обеспечения их моторными топливами.
В то же время существует большое количество удаленных и рассредоточенных потребителей в местах добычи, транспортировки и производства углеводородных газов, куда доставка жидкого моторного топлива автотранспортом и по продуктопроводам неэкономична, и, следовательно, крайне остро стоит проблема обеспечения моторным топливом таких потребителей. Поэтому весьма целесообразным является автономное производство жидкого моторного топлива путем углубленной переработки имеющегося местного газообразного углеводородного сырья, что крайне важно для значительной части регионов России.
При этом принципиально важным является тот факт, что существенная часть этого сырья (13–17 % от общих запасов газа) прихо-
209
дится на долю низконапорных скважин и забалансовых месторождений, которые не эксплуатируются ввиду неэкономичности транспортировки газа из этих месторождений в магистральный трубопровод высокого давления, что требовало бы предварительного компримирования, являющегося весьма энерго- и капиталоемким процессом. Следует подчеркнуть, что из 1195 месторождений 880 являются мелкими, в том числе 187 законсервированы, 110 подготовлены к промышленной эксплуатации, но не разрабатываются. Таким образом, если технология переработки могла бы базироваться на низком исходном давлении газа (без его предварительного компримирования), то применение этой технологии даст огромное дополнительное преимущество в виде значительного расширения ресурсной базы природного газа за счет появляющейся возможности автономного использования низконапорных и забалансовых месторождений.
Что касается целевого продукта технологии, то с учетом протяженности дорог России и трудности создания в ряде отдаленных регионов плотной сети автозаправочных станций задачей технологии должно являться получение топлива, обладающего максимальной калорийностью (чтобы обеспечить наибольшую длину независимого пробега) и возможностью полностью использовать существующую инфраструктуру заправочной сети, хранения топлива и моторостроения. Этим обоим требованиям одновременно отвечают синтетические жидкие топлива (СЖТ), причем углеводородного типа (УСЖТ). Синтетические топлива неуглеводородного типа, т.е. оксигенаты (метанол, диметиловый эфир и др.), имеют теплотворную способность примерно вдвое меньшую, чем у углеводородных. Непосредственное применение природного газа, сжатого до максимального давления 20 МПа, в качестве топлива (КПГ – компримированный природный газ) обеспечивает объемную теплотворную способность Q = 7,2 МДж/л, что примерно в 5 раз ниже, чем у стандартного (в том числе и синтетического) жидкого моторного топлива. Ограничивающим фактором является также значительный балластный вес баллонов даже в случае применения новейших металлопластиковых материалов. Сжиженный метан в качестве моторного топлива (СПГ –
210