
Оборудование для физико-механической обработки материалов
..pdfВнизу башни часто устанавливают аэроохладитель псевдоожиженного слоя. При падении капля остывает снаружи и дает внутри усадку (пустоту). Причем эта пустота (каверна) смещена в тыльную часть гранулы, что уменьшает ее прочность.
Для повышения однородности размеров получаемых гранул в последнее время разработаны так называемые акустические грануляторы. Сущность работы их заключается в воздействии на расплав при разбрызгивании колебаний звуковой частоты. Это способствует более равномерному дроблению струй с получением капель близкого размера.
Недостатком гранулирования в потоке воздуха является громоздкость грануляционной башни. Этот недостаток исключается при разбрызгивании расплава в слой инертной жидкости (например, минеральное масло). Кроме уменьшения капитальных вложений это дает возможность покрывать гранулы масляной пленкой, которая уменьшает их слеживаемость и пылимость.
4.3.Гранулирование суспензий и плавов
впсевдоожиженном слое гранул
содновременной сушкой
Сущность данного процесса заключается в подаче распыленной суспензии или плава в псевдоожиженный слой с одновременной сушкой. При этом часть исходного жидкого материала в виде тонкой пленки наносится на поверхность горячих гранул и высыхает. Размеры гранул увеличиваются по так называемому «нормальному» механизму роста. Рост гранул по такому механизму тем вероятнее, чем больше силы адгезии капли жидкости с поверхностью частиц. Адгезионная способность капли зависит от ряда факторов: шероховатости поверхности частиц, свойств распыливаемой жидкости и др.
Другая часть жидкости высыхает, не соприкасаясь с готовыми гранулами, и образует зародыши новых гранул. Образование новых гранул возможно также за счет дробления сущест-
71
ELIB.PSTU.RU
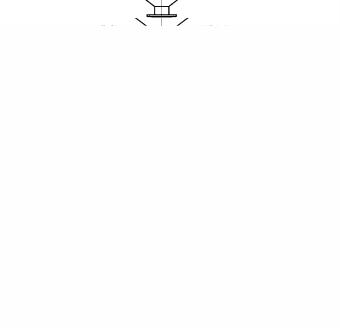
вующих. Часть мельчайших гранул выносится в систему пылегазоочистки и возвращается обратно в аппарат.
Часто из псевдоожиженного слоя производится селективная выгрузка за счет подачи в выгрузочный тракт небольшого количества встречного потока холодного воздуха (одновременное охлаждение готового продукта).
Аппарат для распыливания суспензии над псевдоожиженным слоем высокотемпературным теплоносителем называ-
ется РКСГ, т.е. распылительно-кипящая сушилка-гранулятор
(рис. 4.7).
Рис. 4.7. Схема РКСГ
72
ELIB.PSTU.RU
Достоинства:
высокая интенсивность процессов сушки и гранулирования (400…600 кг влаги/(м2 ч));
совмещение процессов сушки и гранулирования в одном аппарате;
высокая прочность и однородность получаемых гранул.
Недостатки:
ограниченная единичная мощность установки, связанная с ухудшением однородности псевдоожижения на решетках большой площади;
необходимость точного регулирования технологического процесса.
Для повышения интенсивности перемешивания гранул
впсевдоожиженном слое могут служить специальные газораспределительные решетки со струйным псевдоожижением и локальным фонтанированием, а также механические мешалки.
Этих недостатков в значительной степени лишены бара-
банные грануляторы-сушилки (БГС). Одна из конструкций БГС представлена на рис. 4.8.
Вбарабане создается падающий слой гранул в виде сплошной завесы при помощи Г-образных лопаток. Основной процесс протекает в так называемой зоне «факел-завеса». Крупные гранулы проходят через классифицирующий конус, а мелкие скапливаются в нижней части этого конуса, подхватываются обратным шнеком и транспортируются в виде внутреннего ретура
вначало барабана.
Внекоторых аппаратах внутреннего ретура нет, и все мелкие гранулы возвращаются обратно в аппарат в виде внешнего ретура (сферодайзеры) при помощи грохотов, конвейеров и элеваторов.
Расчет барабанного гранулятора-сушилки сводится к определению его основных габаритных размеров и расхода теплоносителя.
73
ELIB.PSTU.RU
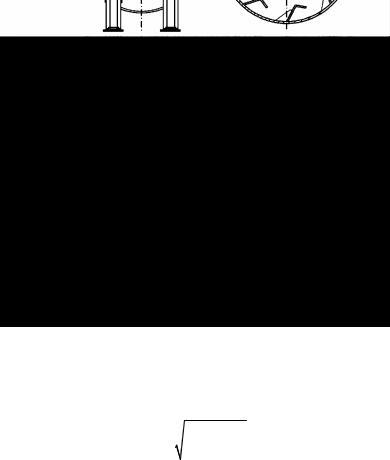
Рис. 4.8. Устройство БГС: 1 – корпус барабана; 2 – обратный шнек; 3 – привод; 4 – ролик опорный; 5 – загрузочная камера; 6 – разгрузочная камера; 7 – классифицирующий конус
Диаметр аппарата
D = |
Q0 |
, |
(4.1) |
0,785 A |
|||
|
F |
|
|
где Q0 – общее количество испаренной влаги, т/ч; AF – влагосъем поперечного сечения БГС, кг/(м2 ч).
Общее количество испаренной в БГС влаги
Q |
= G |
W1 − W2 |
, |
(4.2) |
0 |
пр |
100 − W |
|
|
|
|
1 |
|
|
где Gпр – производительность по готовому продукту, т/ч; W1 – влажность пульпы, подаваемой в аппарат, %; W2 – влажность готового продукта, %.
74
ELIB.PSTU.RU
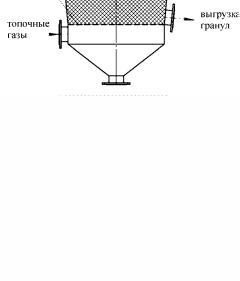
Влагосъем поперечного сечения БГС
AF = 0,49 ∆T + 200, |
(4.3) |
где ∆T – температурный напор теплоносителя, °С.
∆T = t1 – t2,
где t1 – температура теплоносителя на входе в аппарат, °С; t2 – температура теплоносителя на выходе из аппарата, °С.
Общая длина аппарата БГС определяется как сумма длин трех его зон: распыла пульпы, ссыпания порошка и досушки гранул.
4.4. Гранулирование методом формования (экструзии)
Сущность метода заключается в продавливании исходного материала через перфорированную решетку и последующей конвективной сушке гранул (рис. 4.9).
Рис. 4.9. Устройство гранулятора: 1 – вал; 2 – формующая решетка; 3 – корпус; 4 – газораспределительная решетка; 5 – валки
75
ELIB.PSTU.RU
Для повышения пластичности материал увлажняют и вводят специальные пластифицирующие добавки.
Достоинства:
компактность;
высокий выход гранул требуемого размера.
Недостатки:
неправильная форма гранул;
недостаточная прочность гранул.
4.5. Гранулирование методом прессования (вальцедробления)
Метод основан на свойстве сыпучих материалов под действием достаточно больших давлений достигать высокой степени уплотнения и агломерирования отдельных частиц за счет межмолекулярных сил притяжения. Возможно также спекание твердых частиц при высоких температурах и давлениях, а также химическом взаимодействии.
Процесс прессования можно разделить на несколько стадий. Сначала происходят структурные деформации, связанные с ликвидацией пустот и переходом частиц в плотную упаковку. С ростом нагрузки начинаются сдвиговые деформации, сопровождающиеся разрушением исходных частиц, изменением формы и пористости агломератов. В результате увеличивается число контактов и создаются благоприятные условия для межмолекулярного сцепления структурных элементов. При этом могут возникать также электростатические силы.
При дальнейшем повышении нагрузки происходит упругопластическое сжатие. Резко возрастает число контактов и их прочность. Необходимое для этого давление зависит от пластических свойств порошка.
На контактных поверхностях частиц при пластических деформациях возможно образование расплава и спекание частиц. Если пластические деформации у материалов проявляются слабо, то прочность спрессованных плиток незначительна. В этом
76
ELIB.PSTU.RU

случае повышают температуру порошка или вводят специальные пластичные добавки.
Чаще всего прессование проводится между вращающимися навстречу друг другу валками с гладкой или профилированной поверхностью (рис. 4.10).
Рис. 4.10. Кинематическая схема прокатки порошка между гладкими валками
Прессование может проводиться также в таблетирующих машинах в так называемых глухих матрицах.
Угол подачи αп определяет уровень сыпучего материала, ограниченный дозирующим устройством. При прессовании порошков минеральных удобрений αп ≈ 40…70°.
Угол прессования αпр – это угол, начиная с которого наблюдается заметное силовое воздействие. Угол прессования зависит от условий внешнего и внутреннего трения порошка, от уровня порошка, типа питателя и наличия подпрессовывателя, ширины и толщины плитки, частоты вращения, характера поверхности валков и др.
77
ELIB.PSTU.RU
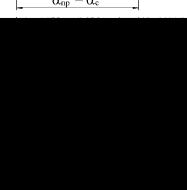
Нейтральный угол αн определяет сечение, где давление достигает максимальной величины.
Угол упругого сжатия валков αс – это угол, характеризую-
щий увеличение протяженности очага деформации материала вследствие упругой деформации валков; αс ≈ 1…1,5°.
В зоне подачи (αпр ≤ α ≤ αп) материал находится в сыпучем состоянии. В этой зоне отмечено значительное скольжение слоев материала порошка относительно поверхности валков и относительно друг друга. При этом ликвидируются арочные эффекты, происходит более плотная, чем при насыпке, укладка частиц порошка, и в зону уплотнения порошок попадает с плотностью, равной плотности порошка после утряски (ρ = ρнас).
В зоне уплотнения (αн < α < αпр), начиная с αпр, происходит изменение плотности сыпучего тела от насыпной плотности порошка до конечной плотности плитки (ρнас → ρплитки).
В зоне выдавливания (αс ≤ α ≤ αн) после прохождения нейтрального сечения плотность и толщина проката остаются неизменными. В этой зоне собственно процесса прессования не происходит, а осуществляется выдавливание материала в узкую
Рис. 4.11. Диаграмма прессования порошка
щель (ρ = ρплитки).
Основное силовое взаимодействие между материалом и валками происходит в зонах уплотнения и выдавливания (рис. 4.11). Кривая имеет плавный подъем давления от нуля во входном сечении зоны уплотнения, крутой подъем до максимума в нейтральном сечении и резкое падение давления к сечению выхода материала из валков.
78
ELIB.PSTU.RU
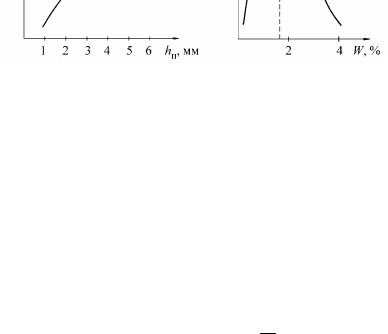
Параметры, влияющие на производительность вальцпрессов:
1. Сыпучесть порошка
g = |
M |
, |
(4.4) |
|
S t |
||||
|
|
|
где М – количество просыпающегося порошка через площадь S межцентрового зазора между валками за время t.
Сыпучесть порошка зависит от влажности порошка, размера частиц и величины зазора между валками.
С увеличением ширины щели сыпучесть порошка возраста-
ет (рис. 4.12).
|
|
|
|
|
|
|
|
|
Рис. 4.12. График зависимости |
Рис. 4.13. График зависимости |
|
сыпучести порошка от ширины |
сыпучести порошка от влажности |
|
щели |
|
|
Сувеличением влажности сыпучесть порошка сначала увеличивается, а затем резко снижается (рис. 4.13).
Сувеличением диаметра частиц сыпучесть сначала улучша-
ется, но при определенном соотношении h начинается сводооб- dч
разование |
h |
< 15 и сыпучесть резко ухудшается (рис. 4.14). |
|
||
dч |
|
|
|
|
79 |
ELIB.PSTU.RU
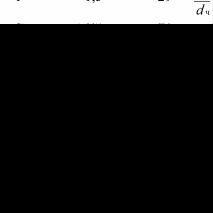
Рис. 4.14. График зависимости сыпучести порошка от диаметра частиц (h = 5,5 мм)
2.Условия воздухоудаления: при прессовании порошков наблюдается выдавливание воздуха и его фильтрация через слой материала навстречу его движению. В предельном случае, когда скорость сжатия достигнет определенной величины, поток выдавливаемого воздуха может препятствовать потоку материала, переводя его в псевдоожиженное состояние. Такая скорость называется критической скоростью прессования. Она зависит от большого числа факторов (размера и плотности частиц, наличия подпрессовывателя, высоты слоя материала над валками и др.)
3.Скорость прессования. Максимальная скорость прессования ограничивается, как было показано выше, переходом материала в псевдоожиженный слой.
Минимальная скорость определяется из условия
Gп ≥ Gпр,
где Gп – количество пересыпающегося материала через зазор между валками, кг/с; Gпр – расход материала на прессование.
Gп = L hп g, |
(4.5) |
где L – длина валков; hп – ширина щели (прессования); g – сыпучесть.
80
ELIB.PSTU.RU