
Учебное пособие 800597
.pdf
мых элементов органическими веществами типа смолы и т. п. Эксперименты по термообработке сварных контактов Al
– Аu, в вакууме не показали явных отличий в росте интерметаллических фаз в сравнении с газовыми средами.
При оценке надежности микросварных соединений необходимо учитывать существенные различия физикомеханических свойств интерметаллических соединений Al – Аu от свойств чистых металлов (табл. 4.1).
Схема образования фаз в соединении алюминий – золото представлена на рис. 4.5.
При изготовлении, испытаниях и эксплуатации полупроводниковые изделия подвергаются различным температурным обработкам, влияющем на структуру, механические и электрические свойства контактов Al – Au.
Таблица 4.1
Параметры |
Аu |
Аu4A1 |
Аu5A12 |
Аu2Al |
АuA1 |
AuA12 |
Al |
|
|
|
|
|
|
|
|
|
|
Постоянная |
4,08 |
6,92 |
– |
6,05 |
6,05 |
6,0 |
4,05 |
|
решетки, Å |
||||||||
|
|
|
|
|
|
|
||
Удельное со- |
|
|
|
|
|
|
|
|
противление, |
2,3 |
37,5 |
25,5 |
13,1 |
12,4 |
7,9 |
3,2 |
|
106 Ом·см |
|
|
|
|
|
|
|
|
Линейное рас- |
|
|
|
|
|
|
|
|
ширение, |
1,42 |
1,2 |
1,4 |
1,3 |
1,2 |
0,94 |
2,3 |
|
105 °С–1 |
|
|
|
|
|
|
|
Металлографическим анализом поперечных сечений соединений Al – Au было установлено, что непосредственно после ТКС в соединениях между алюминиевой проволокой и золотой пленкой имеется ровная по толщине прослойка интерметаллида толщиной 1 – 3 мкм (рис. 4.6, а). В соединениях, полученных УЗС, интерметаллидов оптическим способом обнаружить не удалось (рис. 4.6, б). После термотренировки, предусмотренной технологией производства полупроводниковых изделий, интерметаллиды примерно одной и той же тол-
81
щины были выявлены в контактах, полученных ТКС и УЗС. Следует отметить, что в соединениях, образованных УЗС, они имели ярко выраженный островковый характер (рис. 4.б, в). Проведенные исследования показывают, что отказы в контактах Al – Au. в большей степени связаны с механическими напряжениями, возникающими в сварном соединении и в структурах AuxAly из-за различия в коэффициентах термического расширения. Особенно это наглядно видно на соединениях, полученных УЗС. Анализ поперечных сечений соединений Al – Au с помощью шлифов показал, что интерметаллиды, представляющие собой островки, при нагреве (или при эксплуатации приборов) увеличиваются в размерах, образуя зазор в сварном соединении, тем самым не только уменьшая прочность соединения, но и изменяя электрическое сопротивление контактов. Чем больше площадь взаимодействия соединяемых металлов, например при ТКС, тем в меньшей степени проявляется эффект роста сопротивления контактов (рис. 4.6, г).
82
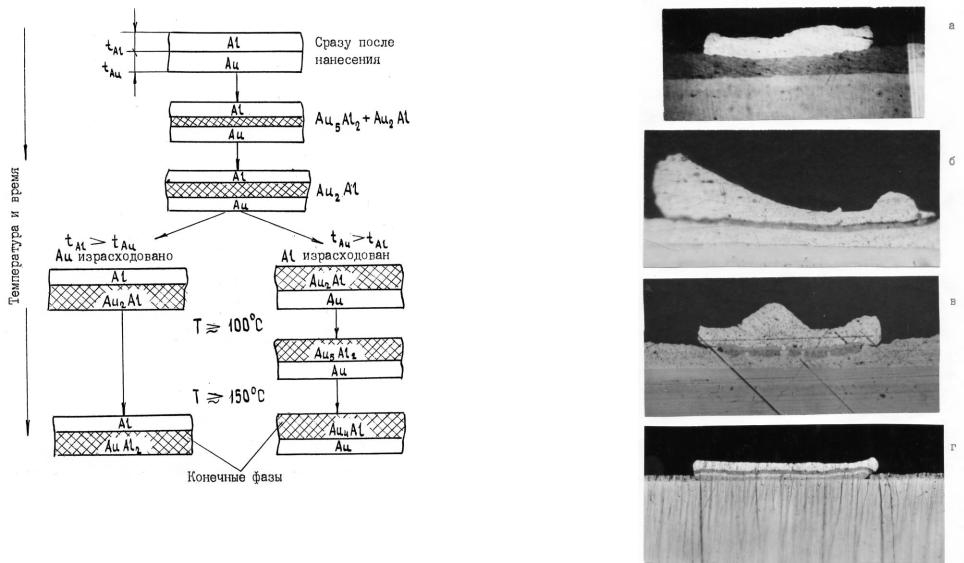
Рис. 4.5. Схема образования фаз в тонкопленочных парах
золото – алюминий |
|
|
Рис. 4.6. Поперечные сечения микросоединений |
|
алюминиевая проволока – пленка золота: ультразвуковое |
|
(а) и термокомпрессионное (б) соединения после сварки; |
|
ультразвуковое (в) и термокомпрессионное (г) соедине- |
|
ния после термотренировки при 125 °С в течение 96 ч. |
|
Увеличение1200Х (а, б, в) и 800Х (г) |
83 |
84 |
Для оценки качества микросоединений в технологии производства ИЭТ разработан экспресс-метод контроля испытаниями на коррозию. Установлена взаимосвязь между конст- руктивно-технологическими факторами образования микросоединений и их коррозионной стойкостью. Коррозионная стойкость соединений At – Au в 3 – 5 раз снижается из-за невоспроизводимое™ оптимальных параметров конструкции микросоединений (например, различия в натяжении проволоки, в ее деформации при сварке и др.). Доказано, что обработка микросоединений Al – Au летучими ингибиторами в 25 раз повышает коррозионную стойкость контактов.
С целью определения минимальной толщины золотого покрытия в контактных соединениях ИЭТ проведены исследования микросварных соединений, выполненных УЗС и ТКС, алюминиевой проволоки марки АКО, 9ПМ35 с гальваническим пленками золота толщиной от 0,5 до 5 мкм. Рассмотрены прочность и электросопротивление контактов после монтажа и после испытаний при температуре 300 °С в течение 10 ч. Лучше значения показателей прочности и электросопротивления получены для соединений с пленками золота толщиной 3 – 4 мкм.
Соединения с пленками золота толщиной менее 2 мкм имеют сравнительно низкие исходные значения по прочности сварных соединений из-за малого объемного взаимодействия контактирующих материалов. Поэтому в первые два часа термообработки происходит некоторое увеличение прочности соединений, а при дальнейшей термообработке прочность соединений и стабильность качества уменьшаются. Это связано с окислением металла подслоя в порах соединения, образованием дефектов по периферии контакта и отжигом алюминиевой проволоки.
4.2.3. Микросварные соединения алюминиевой проволоки с пленками никеля и его сплавами
На нужды электронной промышленности в конце 70-х годов расходовалось около 80 % золота, используемого в мире для технических целей. Из этого количества золота 90 % приходилось на технологическое покрытие корпусов или их участков. Поэтому изыскание путей замены золота, его экономии является важнейшей задачей полупроводниковой микроэлектроники. Вместе с тем, разработка конструкций и технологии монтажа микросоединений в ИЭТ без золота должны приниматься с учетом максимального использования существующих технологий и оборудования, применяемых в полупроводниковой микроэлектронике.
В последние годы велись работы по изучению возможности применения металлизации корпусов никелем и его сплавами, алюминированию, использованию медной рамки и металлизации на основе медных паст, а также комбинированным покрытиям корпусов. Для получения никелевой металлизации корпусов, отвечающей требованиям микросварки, необходимо внедрение новых электролитов никелирования с добавками, повышающими температурную стойкость покрытия, например, сплав никель – бор. Никелировать можно и некоторые типы серийно выпускаемых корпусов, но только после соответствующей доработки их в направлении снижения шероховатости поверхности контактных площадок.
Вакуумное алюминирование и алюминиевая плакировка пригодны только для пластмассовых и металлостеклянных корпусов, поэтому не решают проблему замены золота на корпусах приборов повышенной надежности. Внедрение гальванического алюминирования сдерживает сложность техпроцесса покрытий из расплава солей, а также отсутствие соответствующего серийного оборудования для этих целей.
85
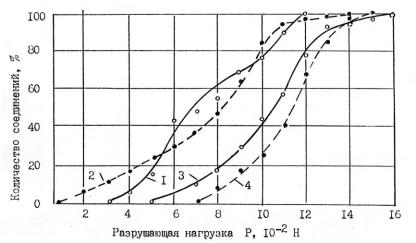
Применение медных рамок и медных покрытий сильно усложняет технологический процесс сборки и может снижать надежность приборов из-за быстрого окисления меди, роста сульфидов и низкой коррозионной стойкости, особенно в контакте с алюминиевым выводом.
Анализ пленочной металлизации показал, что пленки никеля и его сплавов, а также алюминия являются наиболее перспективными технологическими покрытиями корпусов ИЭТ. Следует отметить, что соединения алюминиевой проволоки с алюминиевым покрытием корпусов ИЭТ характеризуются нестабильностью, как при сварке, так и при технологических испытаниях по причине низкого качества алюминиевых покрытий. Технологический процесс гальванического алюминирования корпусов является достаточно сложным, структура покрытий отличается у различных партий корпусов, полученных на одних и тех же режимах, что недопустимо в условиях массового производства ИЭТ.
Из вышеприведенного следует, что в настоящее время наиболее технологичными покрытиями корпусов ИЭТ являются никель и его сплавы. Установлено, что качественные соединения Al – Ni, формируются, в основном, УЗС при отсутствии на никеле оксидных пленок толщиной более 0,005 – 0,007 мкм и значительной площади взаимодействия контактируемых материалов, т. е. при малой шероховатости поверхности пленочной металлизации (Ra = 0,32 – 0,16 мкм). Это связано с большой микротвердостью никеля в сравнении с алюминием, что практически исключает пластическую деформацию покрытия при сварке.
Установлено, что УЗС алюминиевой проволокой по покрытиям, полученным электрохимическим никелированием с предварительной электрохимической полировкой поверхности, повышает прочность микросварных соединений Al – Ni в среднем на (2 – 4)·10–2 H по сравнению с покрытиями, полученными химическим и электрохимическим никелированием без предварительной подготовки поверхности (рис. 4.7).
86
Рис. 4.7. Интегральное распределение прочности микросварных соединений, выполненных УЗС, алюминиевой проволоки с различными никелевыми покрытиями: 1 – химическое никелирование; 2 – электрохимическое никелирование; 3 – химическое полирование с последующим электрохимическим никелированием; 4 – электрохимическое полирование с последующим электрохимическим никелированием
Существенным недостатком пленок из чистого никеля является их низкая теплостойкость, поэтому данные покрытия применимы только при низкотемпературном монтаже элементов или при использовании защитной среды. В процессе напайки кристаллов к корпусу происходит окисление никелевого покрытия, что резко ухудшает свариваемость алюминиевой микропроволоки с пленочными площадками.
Легирование никеля бором значительно повышает температурную стойкость сплава даже при малой концентрации бора, а микротвердость и хрупкость покрытия можно уменьшать путем отжига.
Эксперименты показали, что свариваемость покрытий Ni + 1 % B практически не изменяется после вы-
88
87
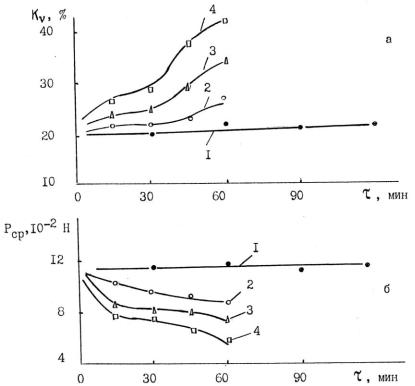
держки при температуре 300 °С в течение 90 мин. После на- |
Внедрение покрытия Ni + 1 % B на рамках стекло- |
грева при температуре 400 °С происходит медленное ухудше- |
керамических корпусов типа 401.14 позволило на 40 – |
ние свариваемости, а при 450 – 500 °С – сначала ухудшение |
50 % повысить стабильность микросоединений по проч- |
свариваемости (после термообработки покрытий в течение |
ности. |
15 мин), затем стабилизация ее на этом уровне (в течение 15 – |
|
30 мин), после чего происходит резкое ухудшение свариваемо- |
|
сти. На образцах, прошедших температурную обработку при |
|
450 – 500 °С в течение более 30 мин, наблюдались случаи раз- |
|
рушения сварных соединений по зоне контакта («отслоение») |
|
как в процессе сварки, так и при контроле прочности сварных |
|
соединений. Количество таких разрушений изменяется про- |
|
порционально времени обработки и колеблется от б до 20 %. |
|
Подбор режимов сварки (увеличение амплитуды и мощности |
|
колебаний, времени сварки, а также изменение давления инст- |
|
румента) не позволяет значительно улучшить свариваемость и |
|
исключить «отслоения». |
|
Методом Оже-спектроскопии поверхностного слоя тол- |
|
щиной 250 – 300 Å никель – бор покрытия установлено, что |
|
при нагреве выше 300 °С происходит диффузия бора на по- |
|
верхность покрытия, содержание которого достигает 5,5 % при |
|
500 °С, что ухудшает пластичность покрытия, необходимую |
|
для формирования сварных соединений. Термообработка в те- |
|
чение 45 – 60 мин при температуре 500 °С приводит к растрес- |
|
киванию покрытия, т. е. начинает окисляться никель, что под- |
|
тверждается быстрым увеличением содержания кислорода в |
|
поверхностном слое покрытия. Это приводит к резкому сни- |
|
жению прочности сварных соединений и их воспроизводимо- |
Рис. 4.8. Воспроизводимость качества Кν (а) и рас- |
сти (рис. 4.8). |
пределение прочности (б) микросоединений алюминие- |
Таким образом, нанесенное электрохимическим спосо- |
вая проволока – никель-бор покрытие в зависимости от |
бом покрытие сплавом Ni + 1 % B имеет удовлетворительную |
времени отжига покрытий перед сваркой при различных |
свариваемость методом УЗС с алюминиевой проволокой после |
температурах, °С: 1 – 300; 2 – 400; 3 – 450; 4 – 500 |
нагрева в течение 60 мин при температуре 400 °С и 30 мин при |
|
температуре 450 – 500 °С. Указанные время и температура пе- |
4.2.4. Микросварные соединения золотой проволо- |
рекрывают реальные режимы, применяемые при монтаже кри- |
ки |
сталлов в корпуса. |
с контактными площадками ГИС и микросборок |
89
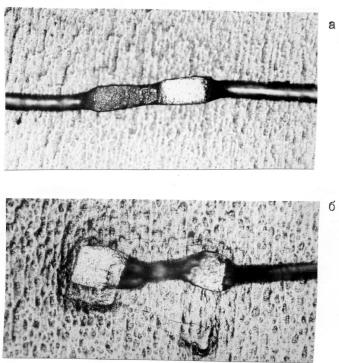
В ГИС и микросборках широко используется монтаж золотой проволоки к контактным площадкам из сплавов оловосвинец (OC61) и олово – никель. Основная сложность получения качественных соединений золотой проволоки с покрытием OC61 обусловлена растворением золота в жидких оловянносвинцовых припоях.
Рис. 4.9. Внешний вид микросоединений золотой проволоки с оловоникелевым покрытием, сформированными различными способами микросварки: а – на установке ЭМ-429; б – термокарандашом (односторонняя контактная сварка). Увеличение 150Х
При изготовлении некоторых типов микросборок используют однослойные платы, представляющие собой фольгированный медью диэлектрик. Для контактных площадок на фольгированный диэлектрик гальваническим методом наносят
90
оловоникелевое покрытие. В технологии производства микросборок толщина данных покрытий составляет от нескольких мкм до десяти и более мкм. Поэтому выбор оптимальной толщины оловоникелевого покрытия является актуальным вопросом для получения качественных микросоединений при монтаже микросборок.
С этой целью проведены исследования микросоединений золотой проволоки с оловоникелевым покрытием различной толщины. Покрытия состава 65 – 67 % Sn + 33 – 35 % Ni наносили гальваническим способом на фольгированный диэлектрик марки ФДМЭ-1 при плотности катодного тока 0,02 А/см2. Образцы для исследований имели толщину пленок от 1 до 13 мкм с интервалом через 2 мкм.
Для исследования влияния толщины оловоникелевого покрытия на качество микросоединений с золотой проволокой диаметром 40 мкм образцы разваривались термокарандашом (односторонняя контактная сварка) и на установке ЭМ-429 на оптимальных режимах. Анализировалась не только прочность микросварных соединений, но и фиксировалась величина деформации золотой проволоки. Внешний вид микросварных соединений золотая проволока – оловоникелевое покрытие показал (рис. 4.9), что сварные соединения, полученные на установке ЭМ-429, мало отличаются друг от друга как по прочности (около 0,15 Н), так и по величине относительной деформации проволоки после сварки (в среднем 62 мкм). Прочность микросоединений, выполненных термокарандашом, имеет разброс от 0,05 до 0,16 Н. Также наблюдаются значительные изменения деформации проволоки от 50 до 160 мкм (рис. 4.10). Это необходимо связывать с особенностями монтажа микросоединений термокарандашом.
Толщина оловоникелевого покрытия практически не влияет на прочность микросварных соединений, но при малых значениях (до 3 мкм) уменьшается деформа-
92
91

ция проволоки, что объясняется большей твердостью оловоникелевого покрытия по сравнению с медью. В процессе сварки при большей толщине гальванического покрытия меньшая часть механического воздействия сварочного инструмента идет на деформацию фольгированного диэлектрика и проволока при этом получает большую деформацию.
Рис. 4.10. Средние значения прочности микросоединений золотой проволоки с оловоникелевым покрытием (а) и величины деформации золотой проволоки (б) от толщины покрытия при монтаже различными методами: 1 – сварка термокарандашом; 2 – сварка на установке ЭМ-429 при напряжении 20
– 25 В, времени импульса 0,05 с и давлении электрода на проволоку 1,0 – 1,2 Н.
Для выяснения термостойкости исследуемых контактов они были подвергнуты термотренировке при температуре 125 °С в течение трех суток в воздушной среде. В процессе металлографического анализа поперечных сечений микросоединений проволока – оловоникелевое покрытие каких-либо существенных изменений, связанных с диффузионными процессами, не обнаружено
(рис. 4.11).
Рис. 4.11. Вид поперечного сечения микросварного соединения золотой проволоки диаметром 0,04 мм с оловоникелевым покрытием толщиной 5 мкм после термотренировки при температуре 125 °С в течение 72 часов. Увеличение 1200Х
Для исследований влияния толщины покрытия OC61 на структуру и прочность микросоединений при монтаже золотой проволокой в качестве подложки использовался диэлектрик, фольгированный медью толщиной 35 мкм. На медную поверхность наносили гальваническим методом слой покрытия толщиной 6 и 16 мкм. Внешний осмотр покрытий после их нанесения показал, что пленки толщиной 6 мкм крупнозернистые, тусклые, с белым налетом. Покрытия толщиной 16 мкм имеют бле-
93
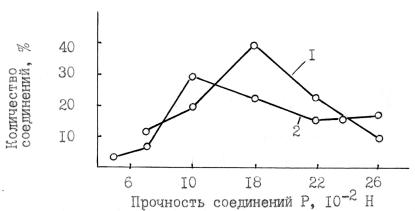
стящий внешний вид и достаточно высокую пластичность. Золотую проволоку диаметром 40 мкм присоединяли к оловянносвинцовым покрытиям OC6I на установке с расщепленным электродом
Прочность соединений проволоки с покрытием оценивалась с точностью до 0,01 Н (рис. 4.12). При оценке прочности во всех случаях микросоединения разрушались по проволоке без отслоения контакта от подложки. Кроме прочностных свойств контактов анализировался внешний вид соединений и исследовалась микроструктура сечений проволока – контактная площадка.
Рис. 4.12. Распределение прочности микросоединений золотой проволоки с покрытием OC61 различной толщины: 1 – толщина покрытия 6 мкм; 2 – толщина покрытия 16 мкм.
Максимальная прочность контактов золотой проволоки с покрытиями толщиной 6 и 16 мкм (0,22 Н) достигается за счет того, что проволока в месте соединения покрывается расплавом OC61 за счет натекания жидкой фазы. Прочность микросоединений в этих случаях находится в прямой зависимости от разрывных усилий самой проволоки. На покрытиях толщиной 16 мкм соединений с максимальной прочностью в два раза больше. Это можно объяснить наличием большего числа проволочных выводов, покрытых припоем не только в зоне кон-
94
такта, но и выше паяного соединения. Однако на покрытиях толщиной 16 мкм имеют место и соединения с минимальной прочностью 0,05 Н. Такой разброс прочности контактов, по-видимому, нужно связывать с хрупкой прослойкой припоя, обогащенной золотом.
В процессе формирования соединения с импульсным вводом энергии происходит локальное расплавление покрытия, которое смачивает золотую проволоку в месте контакта. В жидком объеме припоя идет растворение золота, а вместе с этим обогащение им этой области припоя. Известно, что легирование припоев на основе эвтектики олово – свинец 5 % золота приводит к охрупчиванию этих припоев. При формировании соединений на покрытии OC61 толщиной 16 мкм большая поверхность золотой проволоки находится в контакте с жидким припоем, чем на поверхности толщиной 6 мкм. Это определяет большую легированную область и наибольшее растворение золотой проволоки в первом случае. Чем толще хрупкие прослойки, тем легче они разрушаются при термоциклировании, что и приводит к понижению прочности микросоединений. Это хорошо согласуется с металлографическими исследованиями поперечных сечений соединений. Легированная прослойка в соединениях, полученных на покрытиях OC6I толщиной 16 мкм, значительно толще, чем в соединениях на покрытиях толщиной 6 мкм.
Следовательно, при монтаже соединений золотой проволоки с контактными площадками, покрытыми слоем OC61, импульсной сваркой предпочтительней покрытие толщиной около 6 мкм.
При изготовлении РЭА широко применяются микросборки на бескорпусных ИС в основном с проволочными золотыми выводами. Монтажной платой в таких микросборках может быть ситалловая, поликоровая платы, пассивная часть которых выполнена методом тонкопленочной технологии, керамическая плата из материала
95
22ХС с пассивной частью, выполненной методом толстопленочной технологии, и многослойные печатные платы с шагом координатной сетки 0,625 мм.
Впоследнее время все более широко применяются микросборки с алюминиевой коммутацией, выполненной методом тонкопленочной технологии. Использование алюминия в качестве токоведущих дорожек и контактных площадок обусловлено хорошей адгезией, высокой теплопроводностью, простотой проведения процессов фотолитографии.
Однако из-за преобладающего использования для выводов бескорпусных ИС и внутрисхемных соединений золотых проволочных проводников необходимо отрабатывать процесс сварки золотых проводников с алюминиевыми контактными площадками для получения надежных соединений.
Работы по присоединению выводов бескорпусных ИС на установке ультразвуковой сварки ЭМ-424 показали, что качество и стабильность сварного соединения зависят от ряда факторов: точности настройки магнитострикционного преобразователя и установки рабочего электрода, жесткости фиксации электрода и схемы, разнотолщинности выводов бескорпусных ИС, чистоты соединяемых поверхностей и др. Все факторы в совокупности выдержать невозможно и нельзя получить качественные по прочности и внешнему виду сварные соединения.
Всвязи с этим основные работы проводят на установках контактной сварки ЭМ-429 расщепленным электродом при косвенном нагреве и термокарандашом с V-образным электродом в импульсном режиме, где в процессе сварки металл в зоне контакта нагревается до температуры, достаточной для того, чтобы в момент приложения усилия осадки (сжатия) соединяемый металл пластически деформировался до состояния схватывания и образования прочного соединения.
Впроцессе экспериментальных работ определены оптимальные режимы сварки. Например, для сварки расщепленным электродом золотой проволоки диаметром 0,04 мм режимы следующие:
–время нарастания и спада сварочного импульса η:
250 – 350 нс;
–время сварочного импульса η´: 250 – 350 нс;
–давление сварочного инструмента Q: 1,0 – 1,1 Н;
–мощность W: 0,7 – 0,9 Вт.
На рис. 4.13 приведен характер изменения прочности сварного соединения при изменении времени нарастания и спада сварочного импульса.
Качество сварки определяли визуально под микроскопом при увеличении 16Х. При этом деформация проводника составляла 1,5 – 2,5 его диаметра. Прочность сварных соединений контролировали на установке УКПМ-1. Сварное соединение выдерживает без механических повреждений воздействие растягивающей силы, направленной вдоль оси проводника, равной 0,09 – 0,14 Н.
В целях дополнительной проверки качества сварных соединений опытная партия образцов была подвергнута испытаниям, включающим в себя воздействия термоциклов, линейных центробежных нагрузок, вибрации, одиночных и многократных ударов. Кроме того, образцы были подвергнуты нагреву при температуре 250 °С в течение 5 ч. Дефектов сварных соединений и изменений по внешнему виду обнаружено не было.
96 |
97 |
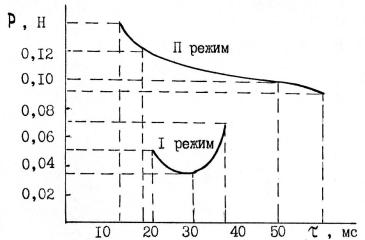
Рис. 4.13. Характер изменения прочности сварного соединения при изменении режимов сварки:
I режим – η´ = 400 мс; W = 0,8 Вт; Q = 1,1 Н;
II режим – η´ = 300 мс; W = 0,8 Вт; Q = 1,1 Н
Анализ прочности микросварных соединений золотых проводников диаметром 40 – 50 мкм выполненных различными видами сварки, показал, что применение расщепленного электрода и сдвоенного электрода с регулируемым зазором дает возможность использовать один и тот же инструмент как для сварки выводов с микросхемами, так и с печатными платами. Сварка с контактированием иглой нецелесообразна для присоединения выводов к контактным площадкам, имеющим толщину золотого покрытия менее 0,7 мкм.
На прочность термокомпрессионных межсоединений, выполненных на установках шариковой сварки, влияют диаметр сварного соединения и смещение его относительно края контактной площадки. Допустимое значение смещения сварной точки относительно края контактной площадки может быть до 0,5 размера площадки. Эти условия позволяют обеспечить прочность межсоединений золотой проволокой диаметром 0,03 мм не менее 0,03 Н с вероятностью более 99,87 %.
4.2.5. Пайка золотой микропроволоки с контактными площадками ГИС и микросборок низкотемпературными припоями
Вопросы формирования надежных контактов с использованием золотой проволоки и низкотемпературных припоев еще полностью не решены. Если и удалось, в частности, получить прочные паяные соединения с помощью индиевых припоев, то нельзя не учитывать то, что процессы старения протекают в этих соединениях с большей скоростью, чем при использовании оловянносвинцовых припоев. Поэтому при решении применять тот или иной припой необходимо учитывать конструкционные особенности ИЭТ и их условия эксплуатации. Знание процессов взаимодействия золотой проволоки с различными припоями, как при пайке, так и при эксплуатации ИЭТ в конечном итоге определяет долговечность и надежность контактных соединений.
В производстве ГИС и микросборок для монтажа золотой проволокой диаметром 0,04 мм широко применяются припои ПОС-61, ПОС-61М, ПСрОСЗ-58, ПОИ50 и ПОСК50-18. При пайке золотой проволоки к контактным площадкам ГИС вышеуказанными припоями наблюдались дефекты паяных контактов как на стадии производства, так и на этапе эксплуатации. Исследования показали, что отказы на стадии монтажа связаны с растворением золотой проволоки в жидкой фазе припоя (при пайке), а на этапе эксплуатации – в твердой фазе (при воздействии повышенных температур).
Для исследования процессов растворения золотой проволоки в жидкой фазе припоя использовалась специально разработанная установка, позволяющая изменять время контактирования проволоки с жидким припоем от 0,2 до 10 с. Скорость растворения золота определялась по уменьшению диаметра сердцевины проволоки, не затронутой реакцией. Растворение золотой проволоки оцени-
98 |
99 |