
Учебное пособие 800417
.pdf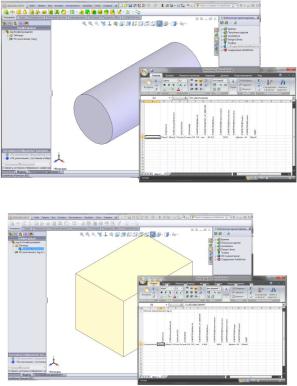
Для открытия предварительно созданных файлов, содержащих геометрическую информацию и заготовке и связь с таблицей параметров так же потребуется создать два *.bat файла со строкой типа
start "" "D:\STM\zag.sldprt"
Таким образом, для создания заготовки теперь достаточно знать объем поковки, выбрать величину соотношения размера основания к высоте, щелчком по кнопке «Вычислить» рассчитать значения размера основания и высоты заготовки и сгенерировать ее модель щелчком по кнопке «Генерация модели заготовки».
Результат работы программы показан на рис. 2.
а) круглая в плане заготовка
б) квадратная в плане заготовка
Рис. 2. Результаты работы программы
11

Литература
1. Алямовский А. А. и др. SolidWorks. Компьютерное моделирование в инженерной практике /Авторы: Алямовский А. А., Собачкин А. А., Одинцов Е. В., Харитонович А. И., Пономарев Н. Б. — СПб.: БХВ-Петербург, 2005. — 800 с.: ил.
Воронежский государственный технический университет
УДК 621.73
С.Л. Новокщенов
МОДЕЛИРОВАНИЕ МНОГОПЕРЕХОДНЫХ ПРОЦЕССОВ ОБРАБОТКИ МЕТАЛЛОВ ДАВЛЕНИЕМ ПРИ ПОМОЩИ САПР ТП
В статье рассматриваются вопросы реализации многопереходных технологических процессов на основе специализированного модуля Forming САПР ТП ОМД Deform-3D
Как правило, процессы обработки металлов давлением реализуются за несколько последовательно осуществляемых технологических операций. При моделировании таких процессов желательно иметь предварительное напряженно-деформированное состояние заготовки перед каждой технологической операцией. В случае реализации процессов полугорячей и горячей объемной штамповки первым этапом является нагрев заранее подготовленной заготовки, который осуществляется в индукционных нагревателях.
Рассматриваемая система Deform-3D позволяет решить эту задачу двумя способами. Первый заключается в простом учете нагрева непосредственным заданием температуры заготовки в препроцессоре (рис. 1),
Рис. 1. Главное окно пре-процессора Deform-3D
12
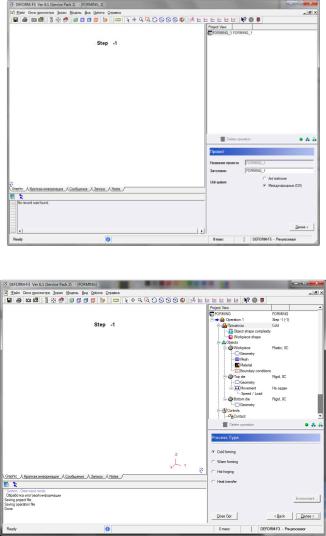
а)
б)
Рис. 2. Окна модуля «Forming»: а) начальное окно пре-процессора б) диалог выбора типа операции
13
Второй способ предполагает вместо стандартного препроцессора использовать модуль Forming, который позволяет последовательно реализовывать многопереходные процессы с автоматизированной передачей данных по технологическим переходам. В этом случае первой операцией в дереве как раз и будет операция нагрева заготовки (рис. 2 б).
Здесь так же следует иметь ввиду что с помощью этого же инструмента можно учитывать межоперационное остывания заготовки, связанное с прохождением времени, необходимого для ее выталкивания из матрицы, перемещения по воздуху в рабочей зоне, укладывание на следующую позицию штамповки. Каждый из перечисленных этапов моделируется как отдельная операция остывания заготовки за известный период времени.
Значение этого периода определяется, прежде всего, используемыми средствами механизации и автоматизации технологического процесса и, как правило, его определяют при составлении циклограммы работы кузнечно-прессовой машины или автоматической линии.
Далее опции модуля Forming позволяют реализовать:
1)холодную объемную штамповку;
2)полугорячую объемную штамповку;
3)горячую объемную штамповку.
Литература
1.В.С. Паршин, А.П. Карамышев, И.И. Некрасов, А.И. Пугин, А.А. Федулов. Практическое руководство к программному комплек-
су Deform. Б.— СПб.: БХВ-Петербург, 2010. — 267 с.: ил.
2.Алямовский А. А. и др. SolidWorks. Компьютерное моделирование в инженерной практике /Авторы: Алямовский А. А., Собачкин А. А., Одинцов Е. В., Харитонович А. И., Пономарев Н. Б. — СПб.: БХВ-Петербург, 2005. — 800 с.: ил.
Воронежский государственный технический университет
14
УДК 621.73
С.Л. Новокщенов
АНАЛИЗ РЕЗУЛЬТАТОВ МОДЕЛИРОВАНИЯ МНОГОПЕРЕХОДНЫХ ПРОЦЕССОВ
В статье дается сравнение результатов моделирования с применением модуля Forming и реализацией многопереходных процессов с применением препроцессора САПР ТП ОМД Deform-3D
Для выполнения сравнительного анализа результатов моделирования с применением САПР ТП рассмотрим пример моделирования технологического процесса изготовления изделия типа «Гайка» с помощью функций пре-процессора Deform-3D и модуля Forming.
Результаты расчёта
|
|
|
По пере- |
Рас- |
|
№ |
Наименование |
Forming |
ходный |
||
хожде- |
|||||
перехода |
операции |
|
анализ |
||
|
ние, % |
||||
|
|
Усилие, тс |
Усилие, тс |
||
|
|
300 се- |
задано |
|
|
1 |
Нагрев |
кунд до |
вручную |
- |
|
|
|
340 0С |
340 0С |
|
|
2 |
Предварительная |
362 |
328 |
10,3 |
|
штамповка |
|||||
|
|
|
|
||
3 |
Окончательная |
137 |
116 |
18,1 |
|
штамповка |
|||||
|
|
|
|
По результату анализа данных из таблицы можно сделать следующие выводы:
1) полученные при моделировании величины расхождения значений расчетного усилия позволяют судить об адекватности данных, небольшое превышение усилия при использовании модуля Forming связано с учетом реализации предварительного напряжен- но-деформированного состояния поковки на стадии нагрева;
15
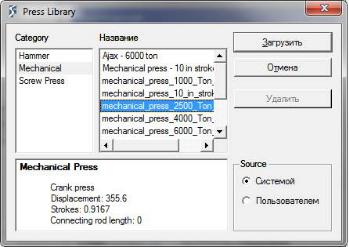
2)модуль Forming позволяет создавать, решать и хранить данные о штамповочном переходе в едином расчетном файле базы данных;
3)в модуле Forming проще реализовано задание граничных условий протекания процесса деформации – нет необходимости ручного вычисления шага перемещения инструмента;
4)в модуле Forming при задании движения деформирующего инструмента реализована база данных по кинематике основных видов кузнечно-прессовых машин (рисунок).
Выбор кузнечно-прессового оборудования
Литература
1.В.С. Паршин, А.П. Карамышев, И.И. Некрасов, А.И. Пугин, А.А. Федулов. Практическое руководство к программному комплексу Deform. Б.— СПб.: БХВ-Петербург, 2010. — 267 с.: ил.
2.Алямовский А. А. и др. SolidWorks. Компьютерное моделирование в инженерной практике /Авторы: Алямовский А. А., Собачкин А. А., Одинцов Е. В., Харитонович А. И., Пономарев Н. Б. — СПб.: БХВ-Петербург, 2005. — 800 с.: ил.
Воронежский государственный технический университет
16
УДК 621.791.053
М.Н Краснова, В.А. Жиленко СРАВНЕНИЕ ДВУХ МЕТОДОВ: ЛУЖЕНИЕ И ЦИНКОВАНИЕ
Встатье рассматриваются технологические процессы методов лужевания
ицинкование металла. Далее рассматриваются способы, которые могут исполняться в двух методах. Затем приводятся их достоинства и недостатки
Во всём машиностроении главной проблемой всегда было долговечность металлических конструкций. Ученым почти сразу стало понятно, чтобы защитить металл от коррозии, его нужно обрабатывать 9мастик, мазут и т.д.), но с развитием человек понял, что такой вид обработки имеет очень большой минус при сырой погоде или при резких перепадах те ператур. И промышленному машиностроению нужно было более эффективный и менее затратный метод во всех смыслах.
На данное время существует много методов обработки металла. Этим мы обязаны ученым из области химии. Рассмотрим в примере два метода обработки металла – это лужение и цинкование. Лужениие – это технологический процесс нанесение на поверхности изделий тонким слоем припоя (образующийся на поверхности изделий слой принято называть полудой). В свою очередь припой представляет собой расплавленное олово или сплав олова со свинцом. Лужению могут подвергаться следующие металлы: сталь, чугун, медь, латунь, бронза, никель, алюминий, свинец, цинк, серебро, золото, платина, кобальт, кадмий. Так же данный метод широко применяется в производстве различных изделий, которые используются в радиотехнической, машиностроительной, авиационной и других отраслях промышленности.
Лужение металла выполняют двумя способами: горячим и гальваническим. Первый способ в свою очередь имеет два вида исполнение растиранием и погружением.
Технологический процесс растиранием.
Растирание начинается с подготовки изделия. Характер подготовки изделия зависит от требований и от метода нанесения полуды. Обработку выполняют последовательно : обработка щетками, шлифование и обезжиривание с последующим травлением. После изделия моют в чистой воде, так же можно применять венскую известь, бензин, керосин и др.(бензин и керосин не рекомендуется применять, так как они относятся к горючим веществам). Предвари-
17
тельно подготовленное и смазанное флюсом изделие нагревают до температуры плавления олова, чтобы оно плавилось и растекалось по поверхности. Флюсом служат хлорид цинка (ZnCl2) и нашатырь (NH4Cl). Поверхности смазывают раствором хлористого цинка и нагревают до его кипения. Далее вводят олово, которое плавится, соприкасаясь с нагретой поверхностью. Затем изделие посыпают порошкообразным нашатырем, а жидкое олово распределяют по поверхности равномерным слоем. Когда изделие остынет, его протирают смоченным песком, промывают водой и сушат.
Технологический процесс погружением.
Лужение начинают с подготовки изделий. Подготовленное к лужению изделие погружают в лудильную жидкость. Затем её вынимают и сразу погружают в оловянную ванну. Тольщина олова будет зависеть от времени пребывания изделия в ванне. Извлеченное из ванны изделие встряхивают, распределяя тем самым олово и удаляя излишки . чтобы нейтрализовать остатки хлористого цинка, остывшее изделие погружают в воду или водный раствор соды. После его вытирают и сушат в чистых опилках. Если изделие не помещается в ванну, то не поместившиеся части обливают оловом.
Второй метод обработки металла является цинкование. Цинкование- покрытие поверхности изделия цинком, который благодаря своей хрупкости и минимальному уровню твердости обеспечивает любому изделию надежную защиту. Цинк вступает в реакцию с окружающей средой раньше, чем она доходит до металла. Таким образом, цинковое покрытие выполняет роль протекторов. Оцинковку металла в основном проводят при помощи специального оборудования разными методами: холодное цинкование, горячее цинкование.
Технологический процесс холодного цинкования. Нанесение цинка начинается с подготовки изделия. Подготовка поверхности начинается с тщательной очистки. Очистку выполняют последовательно механически, термически и химически. После этого поверхность промывается , сушится и флюсуется. Далее наносят покрытие. Процесс нанесения покрытия очень схож с нанесением ЛКМ, т.е. обычное окрашивание металла, проводимое несколько необычными составами. После изделие сушат в соответсвии с инструкцией к цинконаполненной краске.
Технологический процесс горячее цинкование. Горячее цинкование начинается с подготовки изделия. Подготовка начина-
18
ется с обезжиривания поверхности изделия. После промывка изделия. Далее травление, путем опускания в ванну с соляной кислотой. Удаление остатков кислоты. Затем флюсование для получение защитной пленки. После сушат изделие, и потом изделие погружают в расплав цинка, где держат его в зависимости от требований. И в конце охлаждают готовое изделие.
Наименование ме- |
|
|
|
|
|
Цена, |
|
|
тодов |
Плюсы |
Минусы |
|
|||
|
|
руб/кг |
|||||
|
|
|
|
|
|
|
|
|
|
|
|
|
|
|
|
|
|
1.возможность |
само- |
1.тольщина |
по- |
|
|
|
|
востонавления |
|
крытия. |
|
|
|
|
|
2.сохранение |
тепло- |
2.трудность |
по- |
|
|
|
Горячее |
проводности |
3.срок |
лучения равно- |
45 |
||
|
лужение |
службы |
|
|
мерного слоя. |
|
|
Лу- |
|
|
|
|
3.устойчивость к |
|
|
же- |
|
|
|
|
температуре. |
|
|
ние |
|
1равномерность |
1.трудность |
са- |
|
||
|
Гальвани- |
нанесения слоя |
мого процесса |
|
|||
|
ческое лу- |
2.качество |
поверхно- |
2.габариты изде- |
20 |
||
|
жение |
сти |
|
|
лий |
|
|
|
|
1.Высокие |
|
протек- |
1.механическое |
|
|
|
Холодное |
торные |
свойства. |
воздействие |
|
|
|
Цин- |
цинкование |
2.Легкость нанесения. |
|
|
20 |
||
кова- |
|
3.габариты изделий |
|
|
|
||
ва- |
Горячее |
1.механическое воз- |
1.габариты изде- |
|
|||
ние |
цинкование |
действие |
|
|
лия. |
|
36 |
|
|
2.равномерно |
покры- |
|
|
|
|
|
|
тие |
|
|
|
|
|
Таким образом по таблице видно, что каждый метод уникален по своему. Каждый имеет и плюсы и минусы. Таким образом каждый метод хорош в своих условиях и сферах применения.
Литература
1.Окулов В.В. «Гальванотехника и обработка поверхности»
2008г.
2.Ильин В.А. 1977 г. «Цинкование, адмирование, лужение и свинцевание».
Воронежский государственный технический университет
19
УДК 539.37
В.А. Нилов, О.К. Битюцких, А.В. Демидов
ВЫЯВЛЕНИЕ ВЛИЯНИЯ ДЕФЕКТОВ РАБОЧЕГО КОЛЕСА ТУРБОДЕТАНДЕРА ПРИ МОДЕЛИРОВАНИИ ДИНАМИЧЕСКИХ СОСТОЯНИЙ
С статье приводится анализ методом конечных элементов рабочего колеса турбодетандера
Важным этапом проектирования конструкции турбодетандера является исследование динамических состояний его подвижных элементов.
При разгоне турбодетандера частота вращения вала увеличивается и при совпадении с частотой собственных колебаний рабочего колеса может произойти явление резонанса, поэтому выявление низших частот и форм собственных колебаний рабочего колеса представляется весьма важным для качественного проектирования конструкции. В данной статье рассматривается наиболее важный и широко распространенный случай динамического анализа - исследование собственных колебаний конструкций без диссипации энергии.
При вычислении наименьших собственных значений и соответствующих собственных векторов систем высокой размерности с большой шириной ленты весьма эффективен метод итераций в подпространстве (метод одновременных итераций). Использование компактных форм представления матриц жесткости и инертности обеспечивает возможность решения систем уравнений высоких порядков в оперативной памяти компьютера. Достоинством этого метода является и возможность определить на сравнительно ранней стадии решения обусловленность матриц жесткости и инертности. Ошибки в исходных данных могут привести к тому, что матрица жесткости не будет положительно определенной, что выявляется при факторизации матрицы, доначала проведения итераций.
Основной целью метода итераций в подпространстве является одновременное вычисление р наименьших собственных значений и соответствующих собственных векторов.
При моделировании методом конечных элементов [1] рабочего колеса турбодетандера использованы наиболее простые плоские тре-
20