
Учебное пособие 1422
.pdf
|
51 |
|
3). Легкая узкая |
200. |
|
4). Легкая широкая |
500. |
|
Типы применяемых подшипников (4) обозначаются следующим образом: |
||
1). Радиальный однорядный шариковый 0. |
|
|
2). Радиально-упорный шариковый |
6. |
|
Конструктивные особенности (5) и (6) применяемых подшипников |
||
имеют следующие обозначения: |
|
|
1). Обычные (открытые) |
|
00. |
2). С одной защитной шайбой |
06. |
|
3). С двумя защитными шайбами |
08. |
|
4). С разъемным внутренним кольцом |
12. |
|
5). С односторонним резиновым уплотнителем |
16. |
|
6). С двухсторонним резиновым уплотнителем |
18. |
|
Классы точности (а) имеют следующие обозначения: |
||
1). Высокий |
6. |
|
2). Особо высокий |
5. |
|
3). Сверхвысокий |
4. |
|
4). Прецизионный |
2. |
|
Радиальным зазором подшипника (б) называется зазор между телами качения и кольцами в радиальном направлении. Чем меньше зазор, тем более чувствителен подшипник к натягам при посадке внутреннего и наружнего кольца и тем меньшие натяги должны использоваться при этих посадках. Для консистентных смазок всегда применяется увеличенный зазор, так как малые зазоры вызывают повышенный расход смазки и изменение ее структуры. Увеличение радиального зазора необходимо для подшипников, работающих в широком диапазоне температур.
Радиальные зазоры обозначаются: основной - без обозначения; седьмой дополнительный: 7; восьмой дополнительный: 8. Значения радиальных зазоров определены ГОСТом.
Материал сепаратора (в) обозначается следующим образом:
1). Сталь |
- без обозначения. |
2). Бронза |
- Б. |
3). Текстолит |
- Е. |
4). Латунь |
- Л. |
При изготовлении деталей подшипника из нержавеющей стали ставится буква Ю, при использовании нагревостойких сталей - буква Р.
Температура отпуска колец (г) должна быть всегда выше рабочих температур. Обозначение температуры отпуска колец приведены в табл.2.1.
Таблица 2.1.
Температура |
200 |
225 |
250 |
300 |
350 |
400 |
450 |
|
|
отпуска колец, оС |
|
|
|||||||
Обозначение |
Т |
Т1 |
Т2 |
Т3 |
Т4 |
Т5 |
Т6 |
|
|

52
Тип применяемой в подшипнике смазки (д) ставится только в обозначении закрытых подшипников. Обозначения типов смазки даны в табл.2.2.
Примеры обозначений подшипников: 76-180506ЕТ2С4 - радиальный однорядный с двусторонним резиновым уплотнителем, легкой широкой серии, внутренний диаметр 30 мм, с текстолитовым сепаратором, класс точности 6, радиальный зазор седьмого дополнительного ряда, температура отпуска колец 250 оС, смазка ЦИАТИМ-221С.
|
|
Таблица 2.2. |
Тип смазки |
Обозначение |
Температура примениния, оС |
ОКБ-122-7 |
С1 |
от -60 до +100 |
ЦИАТИМ 221 |
С2 |
от -60 до +150 |
ЦИАТИМ 221С |
С4 |
от -60 до +200 |
ЦИАТИМ 202 |
С5 |
от -50 до +150 |
ВНИИНП 207 |
С15 |
от -60 до +180 |
Рассмотрим несколько подробнее особенности применяемых шарикоподшипников.
Открытые подшипники серий 7000100, 100 и 200 (рис.2.36 а)), как и все однорядные радиальные шарикоподшипники способны компенсировать радиальную и смешанную радиально-аксиальную нагрузку. Применяются штампованные (сталь, латунь),текстолитовые и бронзовые сепараторы.
При использовании открытых подшипников в конструкции машины должны обязательно предусматриваться уплотнительные устройства для удержания смазки и защиты подшипника.
а) |
б) |
в) |
|
Рис. 2.36 |
|
Подшипники с защитными шайбами имеют как одностороннее, как в серии 60200 (рис. 2.36 б)), так и двухстороннее уплотнение - серия 160500 (рис. 2.36 в)). Штампованные шайбы не создают полного уплотнения, поэтому в большинстве случаев требуется дополнительная защита подшипника от

53
попадания в него грязи из окружающей среды. При одной защитной шайбе подшипники заполняются смазкой в машине, при двух - на заводеизготовителе.
Подшипники с резиновым уплотнителем имеют одностороннее, как в серии 80200 (рис. 2.37 а)), так и двухстороннее уплотнение - серия 180500 (рис.2.37 б)).
Рис. 2.37
Уплотнение осуществляется эластичными шайбами и прорезиненной тканью, зажатыми с двух сторон стальными шайбами. Такое уплотнение предотвращает вытекание консистентной смазки и защищает подшипник от попадания в него пыли, влаги и грязи из окружающей среды. Применяются текстолитовые сепараторы, состоящие из двух половин, скрепленных заклепками.
2.4.3. Схемы установки подшипников качения
Для обеспечения правильной нагрузки и нормальной работы шарикоподшипников в машине схема их установки должна соответствовать приведенной на рис.2.38.
Внутреннее и наружное кольца одного из подшипников (обычно со стороны выходного конца вала) закрепляются в аксиальном направлении. Этот подшипник будет компенсировать как радиальную, так и аксиальную нагрузки. Закрепление подшипника должно быть надежным, т.е. создаваемым при закреплении натягом необходимо исключить возможности проворота колец на валу и в корпусе машины.
У второго подшипника внутреннее кольцо также закрепляется на валу в аксиальном направлении, а наружнее кольцо свободно, подшипник воспринимает только радиальную нагрузку. Свободное перемещение наружнего кольца необходимо для компенсации как температурных расширений, так и всех допусков по осевым размерам ротора и статора.

54
Рис. 2.38
Вбольшинстве случаев внутренние кольца на валах закрепляются стандартными круглыми гайками со шлицами на наружней поверхности, контровка гаек производится стопорными шайбами с отгибными усиками. Между кольцом и стопорной шайбой рекомендуется устанавливать дистанционную шайбу, которая защищает подшипник при выполнении операции контровки.
Для машин с ограниченным ресурсом работы и при низких частотах вращения для закрепления колец в аксиальном направлении можно применять упрощенную конструкцию. В этом случае подшипник закрепляется разрезными пружинными кольцами. Защита от проворота колец на валу и в корпусе осуществляется только натягами при посадке.
Вмикромашинах (до (5 10) Вт) при достаточных посадочных натягах на внутренних кольцах шарикоподшипников иногда даже не фиксируют эти кольца в осевом направлении. Надежность такой схемы низкая: под влиянием осевой нагрузки может произойти "сползание" опорного подшипника с посадочной поверхности, а это повлечет за собой выход машины из строя. Опорный подшипник, который компенсирует осевую нагрузку на ротор от ударов, вибрации и линейных ускорений, должен обязательно закрепляться в осевом направлении со стороны внутреннего и наружного колец.
2.4.4.Уплотнительные устройства узлов подшипников
2.4.4.1. Неподвижные уплотнения

55
Для неподвижных уплотнений широко используются резиновые кольца круглого сечения с натягом по диаметру (рис.2.39).
Уплотнения с плоскими прокладками применяется редко и только для консистентных смазок. При высоких давлениях и жестких требованиях к герметичности и устанавливаются два круглых резиновых кольца последовательно, но габариты уплотнения при этом значительно возрастают. Обжатие резинового кольца должно составлять (15 30) % от его диаметра. Основные
Рис. 2.39 |
размеры таких уплотнений стандартизированы. |
|
Марка резины выбирается в соответствии с рабочими |
условиями узла (температура, вид смазки и др.).
2.4.4.2. Уплотнения вращающихся валов
Уплотнения должны удерживать смазку в подшипнике и защищать его от воздействия окружающей среды. По расположению относительно оси вала уплотнения бывают двух типов: радиальные и торцевые. Рассмотрим наиболее распространенные них.
Уплотнение фетровыми кольцами использовалось в машинах старых разработок для консистентных смазок при температуре окружающего воздуха не выше +60 оС и окружных скоростях шейки вала до 8 м/с. При более высоких температурах и окружных скоростях происходит затвердевание и разрушение фетра. Шейка вала под кольцом полируется, твердость поверхности берется в пределах 48 60. Канавки во фланце (рис. 2.40 а)) выполняются конусными для обеспечения поджима фетрового кольца к валу, а само кольцо пропитывается той же смазкой, которая закладывается в подшипник.
а) |
б) |
в) |
Рис. 2.40

56
Монтажные уплотнения или уплотнения резиновой манжетой со спиальной пружиной (рис. 2.40 б)) применялись в машинах старых разработок при окружных скоростях шейки вала не выше 10 м/с. Вследствие неизбежного износа резины при вращении вала обеспечить значительный ресурс работы при этих уплотнениях не удается. Тип резины определяется как рабочими температурами, так и видом уплотняемой среды.
Лабиринтные уплотнения являются бесконтактными и могут применяться для любых окружных скоростей. Уплотняющее действие лабиринта основано на создании между неподвижной и вращающейся деталями большого гидравлического сопротивления малыми зазорами сложной извилистой формы с промежуточными расширениями. Простые лабиринтные уплотнения с одним кольцевым зазором не нашли применения. Уплотнения гребенчатого типа с несколькими зазорами (рис. 2.40 в)) более надежны и широко применяются для подшипников с консистентными смазками. Радиальный зазор между гребнями выбираются от 0,05 до 0,2 мм в зависимости от диаметра, посадки подшипника и радиального зазора в нем. Для автоматической компенсации температурных расширений внешний и внутренний гребни уплотнения изготавливаются из одинакового материала или из материалов с близкими коэффициентами линейного расширения. Лабиринтные уплотнения обычно используются в комбинации с другими видами уплотнений, что повышает их надежность. Научно обоснованной методики расчета лабиринтных уплотнений нет, обычно используется опыт, полученный при изготовлении и эксплуатации. В [7] предложена методика сравнительных оценок уплотняющих свойств для уплотнений с различными геометрическими размерами.
Резьбовые маслоотгонные уплотнения или уплотнения с маслоотгонной резьбой (рис.2.41)) также относятся к бесконтактным уплотнениям. Их применение не ограничено окружными скоростями на цапфе вала. Более того, эффективность действия этого уплотнения увеличивается с ростом окружных скоростей. В уплотнении сочетаются лабиринтный эффект и действие винтового насоса. Применяются как для консистентных, так и для жидких смазок. Одним из недостатков этого уплотнения
является возможность захвата из внешней среды и затягивания в подшипниковый узел пыли и влаги из окружающей среды. При использовании такого уплотнения радиальный зазор между неподвижной и вращающейся частями должен быть весьма малым. Так как уменьшение этого зазора ограничено наличием допусков на изготовление деталей, радиальным зазором в подшипнике, допусками на посадку подшипников, температурными и другими факторами, то иногда прибегают к нанесению слоя мягкого металла
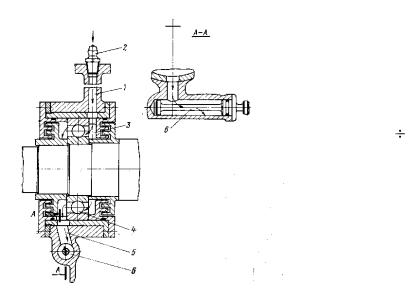
57
(олова, баббита и др.) на неподвижную втулку. В этом случае во время приработки уплотнения на собранной машине мягкий материал в местах касания удаляется и зазор восстанавливается по всему периметру.
Профиль резьбы может быть как прямоугольный, так и трапецеидальный. Могут быть использованы и профили метричных резьб. Направление нарезки резьбы (правая или левая) согласуется с направлением вращения вала машины, так чтобы винтовой насос уплотнения перемещал смазку в сторону подшипника.
Для реверсивных машин это уплотнение непригодно, оно не применяется
ипри наличии избыточного давления в полости подшипника.
2.4.5.Способы подведения смазки к подшипнику
От способа подведения смазки к подшипнику во многом зависят срок службы и надежность работы подшипника. Бесперебойный подвод новых, чистых порций смазки к поверхности трения тел качения обеспечивает устойчивую работу и отсутствие износа. Далее рассматриваются способы подвода смазок к подшипникам, которые нашли применение в машинах общепромышленного назначения.
Заполнение внутренней полости подшипника консистентной смазкой как способ подвода смазок используется в закрытых подшипниках с двухсторонним уплотнением.
Смазка вносится в них на заводе-изготовителе при сборке подшипника и при эксплуатации не заменяется. Количество смазки невелико из-за ограниченного внутреннего объема подшипника, поэтому обеспечить длительный срок службы невозможно. При ограниченном сроке службы применение закрытых подшипников позволяет наиболее просто выполнить подшипниковый узел при наименьших габаритах и массе.
Заполнение внутренней полости подшипникового узла консистентной смазкой является вторым широко распространенным способом ее внесения. Для увеличения количества смазки прибегают к искусственному увеличению того объема, который может быть заполнен смазкой. Такой способ пригоден для подшипников с односторонним уплотнением. Смазка вносится в узел при установке крышки в процессе сборки машины. Количество заполняемой смазки обычно 1/4 1/3 свободного объема. Это количество в несколько раз превышает то, которое закладывается в закрытый
подшипник.
Пополнение смазки при эксплуатации без разборки машины осуществляется для
Рис. 2.42

58
ресурсов работы до 10000 часов, применяются узлы с пополнением и частичной заменой смазки. Конструктивная схема такого узла показана на рис. 2.42. Канал 1 для подачи смазки выводится на корпус машины, где устанавливается шариковая пресс-масленка 2, через которую специальным шприцем производится пополнение смазки при регламентных работах. Пройдя по каналу, новая порция смазки попадает в кольцевую камеру 3 узла справа от подшипника 4. При работе машины смазка непрерывно подпитывает подшипник. Периодичность и доза пополнения смазки зависят от конструкции узла и условий эксплуатации.
Циркуляционная смазка подшипников жидкими маслами также имеет широкое распространение. Жидкая смазка в подшипниковом узле является не только смазывающей, но и охлаждающей средой,
|
она выносит из подшипника все его внутренние |
||||||
|
потери. На рис.2.43 показана конструктивная |
||||||
|
схема узла подшипника с подачей масла через |
||||||
|
жиклер. Струя масла направляется в зазор между |
||||||
|
внутренним |
|
кольцом |
и |
сепаратором. |
||
|
Отличительной особенностью узла подшипника в |
||||||
|
машинах интегральной конструкции является то, |
||||||
|
что подшипник открыт со стороны полости |
||||||
|
машины и в эту полость сбрасывается масло из |
||||||
Рис. 2.43 |
подшипника. |
|
Отпадает |
необходимость |
в |
||
уплотнениях, |
что |
является |
|
очень |
важным |
||
|
|
преимуществом.
В закрытых узлах (с уплотнениями) одной из важнейших задач при конструировании становится правильная организация отвода смазки. При вращении подшипника и вала в полости узла образуется масловоздушная пена, затрудняющая выход масла в сливное отверстие. Поэтому, кроме того, что сливное отверстие должно находиться в самой нижней точке узла, его диаметр необходимо принимать максимально возможным. Всегда желательно, чтобы в узле имелся хотя бы минимальный объем, где масловоздушная смесь могла частично оставаться перед тем как попасть в сливное отверстие.
2.5. Корпуса и щиты
2.5.1. Задачи проектирования корпусов и подшипниковых щитов
Корпуса и щиты являются неподвижными частями электрической машины. В коллекторных машинах постоянного тока и щеточных машинах переменного тока с индуктором на статоре, корпуса выполняют одновременно функцию магнитопровода и поэтому выполняются из стали. В остальных случаях корпуса служат для размещения в них пакетов электротехнической

59
стали статора с обмотками. В этом случае они изготавливаются из легких сплавов.
Щиты предназначены для размещения в них узлов подшипников, на которые опирается вал ротора. В щеточных машинах постоянного и переменного тока на щитах размещаются щеткодержатели. В бесконтактных машинах постоянного тока на щитах крепятся блоки статических выпрямителей и их радиаторы.
Рассмотрим наиболее распространенные схемы стыковки подшипниковых щитов и корпусов электрической машины, которые представлены на рис. 2.44 а) - г)):
Рис. 2.44
Двухщитовая конструкция (рис. 2.44 а)) используется для машин средней и большой мощности. Эта конструкция требует точной обработки посадочных мест в корпусе и на обоих щитах, так как она определяет соосность ротора и статора.
Однощитовая конструкция (рис. 2.44 б)). В ней щит со стороны стыковки объединен с корпусом, число обрабатываемых стыковочных мест становится вдвое меньше, что снижает стоимость и увеличивает точность. Эта схема наиболее широко используется для электрических машин специального назначения, в том числе машин, предназначенных для авиации.
Конструкция с неразъемным щитом (рис. 2.44 в)) используется для некоторых типов высокоскоростных электрических машин. Задний подшипниковый щит укрепляется на корпусе до начала окончательной обработки посадочных мест под подшипники и внутреннего диаметра статора. Обязательным условием такой конструкции является совпадение размеров посадочных гнезд под подшипники и внутреннего диаметра статора. Достоинством такой схемы является высокая точность соосности ротора, статора и обоих подшипников. Ни одна из рассмотренных ранее схем не обеспечивает такой точности.
Бесщитовая конструкция (рис.2. 44 г)) применяется для электрических машин (чаще генераторов) интегрального типа т.е. электрическая машина является частью конструкции рабочего механизма. Второй подшипник для вала ротора непосредственно встраивается в привод рабочего механизма.
Назначение корпусов и щитов, представляет общие задачи при их проектировании:
60
1). Обеспечение стабильной работы подшипников во всем диапазоне рабочих температур.
2). Надежная центровка и фиксация всей машины на месте ее установки, а также взаимная центровка корпусов и щитов.
3). Надежное закрепление и центровка пакетов стали и полюсов.
4). Минимальная масса и габариты при достаточной механической прочности и жесткости.
5). Удобство размещения элементов, требующих периодического осмотра и эксплуатации.
6). Возможность применения прогрессивных способов изготовления (штамповка, литье под давлением и т.д.).
Крепление подшипниковых щитов и корпусов на практике осуществляется одним из следующих способов: резьбовые соединения, клеевые соединения, пайка.
При резьбовом соединении, прочность стыковки достигается выбором достаточного количества крепящих шпилек или болтов. Применение шпилек для легких сплавов (алюминий, магний и т.д.) предпочтительней. Это объясняется тем, что использование стального болта приводит к выработке резьбы. При эксплуатации для сильных вибрационных или ударных нагрузок наблюдались случаи вырыва болта из ослабленных резьбовых отверстий.
При выборе конструкции фланцевого соединения следует руководствоваться следующими общими правилами:
1). Следует использовать большее число шпилек (болтов) меньшего сечения. Это обеспечивает высокую надежность крепления, делает затяжку более равномерной и уменьшает массу, т.к. требует меньшей жесткости фланца.
2). Для силовых креплений следует избегать применение резьб менее М5 (для средних и крупных машин), т.к. возможны срывы резьбы при эксплуатации.
3). Для легких сплавов следует применять шпильки.
4). Для ответственных стыков на сборочных чертежах следует указывать момент закручивания, что обеспечивает равномерную и гарантированную затяжку.
5). Контровку гаек и болтов следует производить стандартными шайбами с отгибными усами.
6). Не рекомендуется применять для контровки пружинные шайбы т.к. они подвержены разрушению при вибрационных и ударных нагрузках.
2.5.2. Конструкции корпусов
На рис.2.45 показан корпус машины постоянного тока относительно небольшой мощности с полюсами 2 и катушками 3.