
4895
.pdf
21
допустимые диаметры отверстий; dmax и dmin – наиболее и наименее допустимые диаметры вала.
Поле допуска – совокупность всех возможных отклонений в пределах допуска.
Зазор – разность действительных размеров отверстия и вала, если размер отверстия больше размера вала.
Натяг – разность размеров вала и отверстия до сборки, если размер вала больше размера отверстия.
Различают посадки в системе отверстия – это такие посадки, при которых наименьший предельный размер отверстия равен номинальному (нижнее отклонение равно нулю), и посадки в системе вала у которых наибольший предельный размер вала равен номинальному (верхнее отклонение равно нулю). Например, в системе отверстия: отверстие 50+0,5, вал 50+−00,,0301 ; в сис-
теме вала: отверстие 50+−00,,0502 , вал 50-0,02. Всегда верхнее отклонение запи-
сывается выше, нижнее – ниже номинального размера, справа от него. В нашей стране в основном принята система отверстия.
Для краткости на чертежах размеры и положенные поля допуска, определяющие характер соединения, обозначают буквой латинского алфавита – прописной (заглавной) А, В, С…Z для отверстий и строчной (малой) а, в, с…z для валов (табл. 4.1).
|
|
|
Таблица 4.1 |
|
Характер соединения деталей |
||
Основное |
Посадки с зазором |
Переходные |
Посадки с натягом |
отклоне- |
|
посадки |
|
ние |
|
|
|
Отверстие |
A, B, C, D, E, F, G, H |
Js, K, M, N |
P, R, S, T, U, V, X, Y, Z |
|
|
|
|
Вал |
a, b, c, d, e, f, g, h |
Js, k, m, n |
p, r, t, u, v, x, y, z |
|
|
|
|
На чертежах предельное отклонение указывается следующим образом:
-условными обозначениями, например, отверстие 50Н7, вал 55q6;
-числовыми значениями в мм, например, отверстие 50+0,05, вал50−−0,0320,059;
-комбинированным способом, например, отверстие 18Н7+0,018, вал
12е8 −− 00,,032059 .
На сборочных чертежах посадки указывают в виде дроби, в числителе
– для отверстия, в знаменателе для валов. Например, 50 Н7 . g6
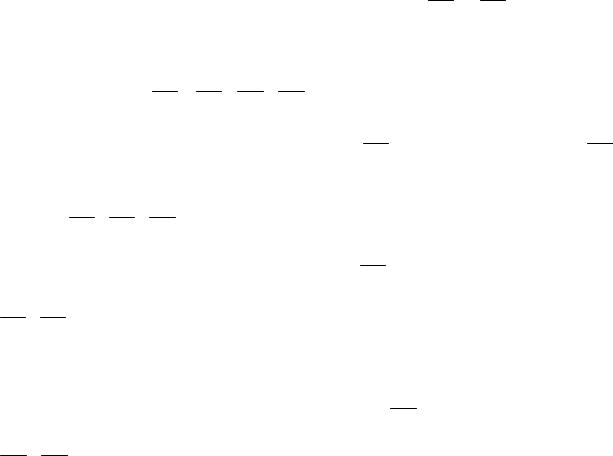
22
Цифра справа от буквенного обозначения посадки характеризует степень точности (степень качества) соединения, или квалитет (табл. 4.2)
Таблица 4.2
Квалитеты (степени точности)
|
|
Точные |
|
|
|
|
|
Средние |
|
|
|
Грубые |
|
|||||||
01 |
0 |
|
1 |
2 |
|
3 |
4 |
5 |
6 |
7 |
|
8 |
9 |
10 |
11 |
13 |
14 |
15 |
16 |
17 |
В машинах и механизмах общего назначения обычно применяют средние квалитеты.
3.Рекомендации по выбору посадок 3.1. Посадки зубчатых и червячных колес
Посадка зубчатых и червячных колес на вал, как правило, выполняется в системе отверстия. При выборе типа посадки учитывают условия работы и величину передаваемой нагрузки.
Для неподвижных соединений колес с валом, которые требуют перио- Нn67 и Hk67
небольших нагрузок, вторая – для средних, при мощности двигателя до 5кВт). Для зубчатых и червячных редукторов общего назначения обычно ис-
пользуют посадки Нr67 , Hs67 , Hp67 , mH76 . Для цилиндрических зубчатых и чер-
вячных колес наиболее употребима посадка Hp67 , для конических колес mH76 . Для подвижных блоков шестерен коробок передач по шпонкам применяют посадки Нh67 , Hf 67 , He87 . Посадку зубчатого вала на ступицу червячного колеса
осуществляют : при сплошной нагрузке по Hp67 , при умеренных толчках по
Hr67 , Нn67 .
3.2. Посадка шкивов и звездочек Рекомендуемые посадки шкивов ременных передач и звездочек цепных
передач – переходные: при спокойной нагрузке Нк67 , при умеренных толчках
mН76 , Hn67 (если шкивы и звездочки установлены на шпонках). 3.3. Посадки подшипников качения
Посадки подшипников качения в корпус и на вал производится в зависимости от режима работы в табл. 4.3.
23
|
|
|
Таблица 4.3 |
|
Посадки подшипников качения |
|
|
Посадка |
|
Режим работы |
Рекомендуемая по- |
|
|
|
садка |
В корпус |
|
Легкий или нормальный |
Js7 |
На вал |
|
Легкий или нормальный |
js6, k6 |
В корпус |
|
Нормальный или тяжелый |
H7, K6 |
|
|
|
|
На вал |
|
Нормальный или тяжелый |
k6, m6 |
|
|
|
|
4.Соединения с натягом (прессовые соединения)
Впоследнее время для передачи момента со ступицы детали на вал все чаще стали применять соединения с натягом (без шпонок и шлицевых соединений).
Исходными данными являются: вращающий момент на ступице Т, Нмм: диаметр соединения d, мм; диаметр отверстия пустотелого вала d1, мм (для сплошного вала d1=0); диаметр (условный) ступицы d2, мм, длина сопряже-
ния l, мм.
Выбор посадок осуществляют в следующем порядке: Определяют среднее контактное давление, МПа
|
р = |
|
2Тk |
|
, |
|
|
(4.1) |
|||
|
|
|
|
|
|
|
|
||||
|
|
|
|
πd2lf |
|
|
|
||||
где |
k – коэффициент запаса сцепления (муфты соединительные k=3, штиф- |
||||||||||
|
ты ременных передач k=4, звездочки цепных передач k=3,5, зубчатые |
||||||||||
|
колеса k=4,5); |
|
|
|
|
|
|
|
|
|
|
|
f – коэффициент трения (табл.4.4). |
|
|
|
|
|
|||||
|
|
|
|
|
|
|
|
|
|
|
Таблица 4.4 |
|
Коэффициенты трения |
|
|||||||||
Материал соединительных дета- |
|
|
|
|
|
|
|
Сборка |
|
||
|
лей |
|
|
|
|
прессованием |
|
Нагревом |
|||
Сталь-чугун |
|
|
|
|
|
|
|
0,08 |
|
0,14 |
|
Сталь-сталь |
|
|
|
|
|
|
|
0,08 |
|
0,14 |
|
Сталь-бронза, латунь |
|
|
|
|
|
|
|
0,05 |
|
0,07 |
|
Чугун-бронза, латунь |
|
|
|
|
|
|
|
0,05 |
|
0,07 |
|
|
Находят деформацию деталей, мм |
|
|
|
|
|
|
||||
|
|
|
C1 |
|
|
C2 |
|
|
|||
|
|
|
+ |
|
(4.2) |
||||||
|
|
|
|
||||||||
|
δ = рd |
|
E1 |
E2 |
, |
||||||
|
|
|
|
|
|
||||||
где |
С1 и С2 – коэффициенты жесткости соединяемых деталей |
|
|
|
24 |
|
|
|
C1 = |
1+ (d1 /d)2 |
− µ ; |
C2 = |
1+ (d/d2 )2 |
+ µ2 , |
(4.3) |
1− (d1 /d)2 |
1− (d/d2 )2 |
|||||
В приведенных формулах |
Е – модуль упругости: для |
стали – |
2,1.105МПа, для чугуна – 0,5.105МПа, для бронзы и латуни – 105МПа; µ - коэффициент Пуассона: для стали – 0,3, чугуна – 0,25, бронзы и латуни – 0,35.
|
|
|
Отверстие |
|
|
Вал |
|
|
Интервалы разме- |
|
|
|
Квалитет |
|
|
||
|
ров, мм |
6, 7 |
|
8 |
9 |
6, 7 |
8 |
9 |
|
|
|
|
|
Ra, мкм |
|
|
|
Св. 18 |
до 50 |
0,8 |
|
1.6 |
3,2 |
0,8 |
0,8 |
1,6 |
Св. 50 |
до 120 |
1,6 |
|
1,6 |
3,2 |
0,8 |
1,6 |
1,6 |
Св. 120 до 500 |
1,6 |
|
3,2 |
3,2 |
1,6 |
3,2 |
3,2 |
Проводят проверку на температурную деформацию (обычно при подборе посадки зубчатых венцов червячных передач, которые нагреваются при работе передачи до высоких температур).
δt = d106 [(t2 − 200 )α2 − (t1 − 200 )α2 ], |
(4.5) |
где α - коэффициенты: для стали – 12.10-6, для чугуна – 10.10-6, для бронзы, латуни – 19.10-6;
t1 и t2 – средние объемные температуры соответственно обода центра и венца колеса.
Находят минимальный натяг (мм), который для передачи вращающего
момента должен быть |
|
[N]min ≥ δ + u + δt . |
(4.6) |
Определяют максимальный натяг (мм), допускаемый прочностью охва- |
|
тывающей детали |
|
[N]max ≤ [δ]+ u , |
(4.7) |
где [δ]=[p]max δ/p, мм – максимальная деформация, допускаемая прочностью охватывающей детали ([p]max = 0,5σT2 [1− (d/d2 )2 ], МПа –максимальное давление, допускаемое прочностью охватывающей детали, где σT2 - предел текучести материала охватывающей детали ,МПа).
25
Производят выбор посадки. По значениям [N]min и [N]max , переведя их размерности в мкм, выбирают из табл.4.6 одну из посадок.
5.Порядок выполнения работы
5.1.Ознакомиться с терминологией единой системы допусков и поса-
док.
5.2.Изучить систему обозначения посадок.
5.3.Ознакомиться с рекомендациями по выбору посадок зубчатых и червячных колес.
5.4.Ознакомиться с рекомендациями по выбору посадок шкивов и
звездочек.
5.5.Ознакомиться с рекомендациями по выбору посадок подшипников
качения.
5.6.Изучить методику расчета и выбора посадок для прессовых соеди-
нений.
6.Оформление отчета
6.1.Привести наиболее употребимые посадки зубчатых и червячных колес, шкивов ременных передач, звездочек цепных передач и подшипников качения.
6.2.Представить расчет по выбору посадки прессового соединения зубчатого колеса с валом по данным: передаваемый вращающий момент Т=200000 Нмм; диаметр соединения d=35 мм; вал сплошной, то есть d1=0;
диаметр ступицы колеса d2=50 мм; длина ступицы l=35 мм; материал вала – Сталь 45, материал колеса и его ступицы - Сталь 45. Предел текучести взять разным σT2 =500 МПа.
7.Контрольные вопросы
7.1.Как понимать термин «посадка в системе отверстия»?
7.2.Как понимать термин «посадка в системе вала»?
7.3.Как обозначается посадка на сборочных чертежах и на чертежах деталей машин ?
7.4.В чем суть методики расчета посадок прессовых соединений ?
27
|
|
|
|
|
|
|
|
|
|
|
|
|
|
|
|
|
|
|
|
|
|
|
|
|
|
|
|
|
|
Таблица 3.6 |
|||
|
|
|
|
|
|
|
|
|
|
|
Значение натягов Nmin/Nmax, мкм для посадок |
|
|
|
|
|
|
|
|
|
|||||||||||||
|
|
|
|
|
|
|
|
|
|
|
|
|
|||||||||||||||||||||
Интер- |
|
H7 |
H7 |
H8 |
H7 |
H7 |
H7 |
H8 |
H7 |
H8 |
H8 |
H8 |
|||||||||||||||||||||
валы |
|
|
|
|
|
|
|
|
|
|
|
|
|
|
|
|
|
|
|
|
|
|
|
|
|
|
|
|
|
|
|
|
|
p6 |
r6 |
s7 |
s6 |
S7 |
t6 |
n8 |
n7 |
x8 |
z8 |
za8 |
|||||||||||||||||||||||
диамет- |
|
|
|
|
|
|
|
|
|
|
|
|
|
|
|
|
|
|
|
|
|
|
|
|
|
|
|
|
|
|
|
|
|
ров, мм |
|
|
|
|
|
|
|
|
|
|
|
|
|
|
|
|
|
|
|
|
|
|
|
|
|
|
|
|
|
|
|
|
|
|
|
|
|
|
|
|
|
|
|
|
|
||||||||||||||||||||||
30…40 |
7/36 |
15/44 |
13/59 |
24/53 |
25/61 |
29/58 |
32/88 |
42/88 |
52/108 |
84/140 |
120/175 |
||||||||||||||||||||||
|
|
|
|
|
|
|
|
|
|
|
|
||||||||||||||||||||||
40…50 |
-//- |
-//- |
-//- |
-//- |
-//- |
35/64 |
42/98 |
52/88 |
69/125 |
108/164 |
152/207 |
||||||||||||||||||||||
|
|
|
|
|
|
|
|
|
|
|
|
||||||||||||||||||||||
50…65 |
9/44 |
18/53 |
18/72 |
30/65 |
32/74 |
43/78 |
55/119 |
66/109 |
90/154 |
140/204 |
193/258 |
||||||||||||||||||||||
|
|
|
|
|
|
|
|
|
|
|
|
||||||||||||||||||||||
65…80 |
-//- |
20/55 |
24/78 |
36/71 |
38/80 |
52/87 |
70/134 |
81/123 |
114/178 |
178/242 |
241/306 |
||||||||||||||||||||||
|
|
|
|
|
|
|
|
|
|
|
|
||||||||||||||||||||||
80…100 |
10/51 |
24/65 |
29/93 |
44/85 |
46/96 |
64/105 |
86/162 |
99/149 |
149/216 |
220/296 |
297/373 |
||||||||||||||||||||||
|
|
|
|
|
|
|
|
|
|
|
|
|
|
|
|
|
|
|
|
|
|
|
|
|
|
|
|
|
|
|
|
|
|
28
ЛАБОРАТОРНАЯ РАБОТА №5
ИЗУЧЕНИЕ ПОДШИПНИКОВ КАЧЕНИЯ И УПЛОТНЕНИЙ ПОДШИПНИКОВЫХ УЗЛОВ
1. Цель работы
Ознакомление с различными типами подшипников качения, системой их условных обозначений (маркировкой), а также с основными типами уплотнений подшипниковых узлов.
2. Общие сведения
Подшипники качения – это опоры вращающихся или касающихся деталей, использующие элементы качения (шарики или ролики) и работающие на основе трения качения. Они состоят из наружного кольца, внутреннего кольца, между которыми расположены тела качения. Для предохранения тел качения от соприкосновения между собой их отделяют друг от друга сепаратором, который существенно уменьшает потери на трение.
Преимущества подшипников качения (по сравнению с подшипниками скольжения):
-малый коэффициент трения (f=0,0015…0,006);
-незначительный расход смазки;
-малое сопротивление при разгоне, малый статический момент трения;
-меньшие габариты в длину;
-снижение стоимости производства за счет массового изготовления стандартных типов подшипников;
-простота монтажа, демонтажа и обслуживания;
-большая надёжность против заедания.
Недостатки подшипников качения:
-ограниченная способность восприятия ударных и динамических нагрузок
-ограничение срока службы подшипников усталостным выкрашиванием поверхностей качения
-большие габариты по диаметру при больших нагрузках. Подшипники качения классифицируют по следующим признакам.
По форме тел качения подразделяют на роликовые, которые в свою
очередь, делятся по форме роликов на подшипники с короткими цилиндрическими, коническими, бочкообразными, игольчатыми и витыми роликами.
По направлению действия воспринимаемых сил (нагрузок) разделяют на типы: радиальные, воспринимающие преимущественно радиальные нагрузки, действующие перпендикулярно оси вращения подшипника; радиаль- но-упорные, воспринимающие одновременно действующие радиальные и осевые нагрузки; упорные, воспринимающие только осевые силы.
29
По способности самоустановки – подразделяют на несамоустанавливающиеся и самоустанавливающиеся.
По числу рядов тел качения (расположенных по ширине) – делят на однорядные, двухрядные, четырехрядные и многорядные.
Основными характеристиками подшипников являются грузоподъемность, быстроходность, масса, габариты, потери энергии.
Для маркировки, указаний на чертежах и в спецификациях, применения в технической литературе и т.п. стандартные подшипники имеют условные обозначения. Условные обозначения подшипников составляются из цифр, значения которых определяются местом, занимаемым ими в обозначении. Две первые цифры, считая справа, обозначают внутренний диаметр подшипника (для подшипников с внутренним диаметром от 20 до 495 мм эти цифры соответствуют внутреннему диаметру, деленному на 5). Третья цифра справа совместно с седьмой обозначает серию подшипников всех диаметров, кроме малых, до 9 мм. Основная из особо легких серий обозначается цифрой 1, легкая – 2, средняя – 3, тяжелая – 4, легкая широкая – 5, средняя широкая – 6 и т.д. Четвертая цифра – тип подшипника:
0 – радиальный шариковый;
1 – радиальный шариковый сферический;
2 – радиальный с короткими цилиндрическими роликами;
3 – радиальный роликовый двухрядный сферический;
4 – радиальный роликовый с длинными игольчатыми роликами;
5 – радиальный роликовый с витыми роликами;
6 – радиально-упорный шариковый;
7 – радиально-упорный роликовый конический;
8 – упорный шариковый;
9 – упорный роликовый.
Пятая или пятая и шестая цифры, вводимые не для всех подшипников, обозначают конструктивные особенности подшипников, например наличие стопорной канавки на наружном кольце, наличие встроенных уплотнений и т.п.
Промышленность изготовляет подшипники качения пяти классов точности: 0; 6; 5; 4 и 2. Обозначения даны в порядке повышения точности, определяемой допусками на изготовление элементов, а также нормами плавности вращения. Класс точности указывается слева от условного обозначения подшипников через тире (например, 6-207).
Примеры обозначения подшипников: шариковые радиальные однорядные с внутренним диаметром 50 мм, легкой серии – 210, средне – 310, тяжелой – 410. Радиально-упорные роликовые конические подшипники с внутренним диаметром 80 мм легкой серии 7216, легкой широкой – 7516, средней
– 7916, средней широкой – 7616.
Уплотнения подшипниковых узлов делятся на следующие основные
типы.
30
Контактные (манжетные, войлочные и т.п.), применяемые при низких и средних скоростях. Основное достоинство уплотнений этого типа – простота и дешевизна изготовления. Недостаток – трение на поверхности контакта.
Щелевые и лабиринтные, применяемые в неограниченном диапазоне скоростей, осуществляющие защиту благодаря сопротивлению протекания жидкости или газа через узкие щели. Они практически не имеют изнашивающихся деталей и не требовательны в эксплуатации.
Центробежные, применяемые при средних и высоких скоростях и основанные на отбрасывании центробежными силами смазки и загрязняющих веществ, попадающих на вращающиеся защитные диски.
Комбинированные, сочетающие уплотнения, основанные на двух или более из указанных типов.
3.Порядок выполнения работы
3.1.Ознакомиться с устройством и характеристиками основных типов подшипников качения (у.п. Проектирование механических передач под редакцией С.А. Чернавского-М.,1984г.)
3.2.Изучить систему условных обозначений подшипников качения.
3.3.Выполнить эскизы основных типов подшипников качения.
3.4.Выбрать из партии подшипников по одному подшипнику каждого типа (или по указанию преподавателя), записать номера подшипников и расшифровать полное их наименование.
3.5.Выбрать три подшипника без обозначений, сделать необходимые замеры и восстановить их маркировку, сравнив затем с ГОСТом
3.6.Ознакомиться с основными типами уплотнений подшипниковых
узлов
2.Оформление отчета
4.1.Эскизы основных типов подшипников качения.
4.2.Расшифровка обозначения подшипника
Обозначение подшип- |
d, мм |
D, мм |
B, мм |
Серия |
Тип подшипни- |
ника |
|
|
|
|
ка |
|
|
|
|
|
|
4.3. Составление обозначения подшипника
|
d, мм |
D, мм |
B, мм |
Предпола- |
Обозна- |
Тип подшипника |
|
|
|
гаемое обо- |
чение по |
|
|
|
|
значение |
ГОСТу |
|
|
|
|
|
|
4.4. Эскизы основных типов уплотнений подшипниковых узлов